Welding is one of those skills where the tools you choose can make or break your project. If you’ve ever dabbled in welding or are looking to start, you’ve probably heard about flux-cored wire. It’s a game-changer in many ways, and once I started using it, I quickly saw why so many professionals swear by it.
Flux-cored wire isn’t just a tool; it’s a solution to many challenges welders face, especially when working outdoors or with thicker materials. In this guide, I’ll walk you through what flux-cored wire is, where it shines, and how you can get the most out of it.
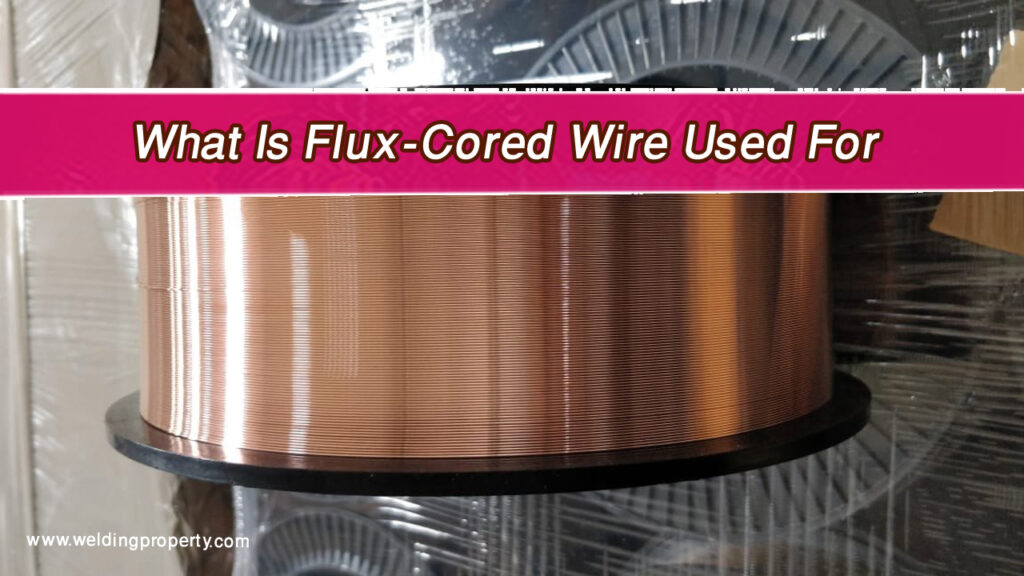
What Is Flux-Cored Wire?
Flux-cored wire is a type of welding wire that’s used in flux-cored arc welding (FCAW). Unlike solid wire, this wire is hollow and filled with a flux material. The flux acts as a shielding agent, protecting the weld pool from contamination by the surrounding air.
There are two types of flux-cored wire:
Self-Shielded Flux-Cored Wire: This type doesn’t require an external shielding gas. The flux inside the wire does all the work, making it perfect for outdoor welding.
Gas-Shielded Flux-Cored Wire: This type is used with an external shielding gas, offering cleaner and more controlled welds.
Why Is Flux-Cored Wire Popular Among Welders?
Flux-cored wire is popular because it offers versatility and convenience that other welding methods can’t always match. Here’s why it’s a go-to for many welders:
- Outdoor Compatibility: It handles windy conditions better than MIG welding since it doesn’t always rely on external gas.
- High Deposition Rate: Flux-cored wire allows you to weld faster, which is a significant advantage for large projects.
- Ease of Use: It’s beginner-friendly and doesn’t require an elaborate setup, especially if you’re using self-shielded wire.
- Strong Welds: The penetration it provides is excellent, making it ideal for structural and heavy-duty applications.
Common Applications of Flux-Cored Wire
Construction and Structural Welding
One of the most common uses for flux-cored wire is in construction. When you’re welding thick steel beams or structural components, you need a method that offers strong penetration and reliable welds. Flux-cored wire excels in these situations, even in outdoor environments.
Shipbuilding
In shipyards, the ability to weld in various conditions is crucial. The wind-resistant properties of self-shielded flux-cored wire make it invaluable for shipbuilding, where precision and durability are critical.
Pipeline Welding
Pipelines often run through challenging environments, from open fields to extreme weather conditions. Flux-cored wire ensures high-quality welds that can withstand pressure and environmental factors.
Automotive Repairs
While flux-cored wire isn’t the first choice for thin car sheet metal, it’s excellent for heavier components like chassis repair or welding exhaust systems.
Industrial Fabrication
In factories and workshops, gas-shielded flux-cored wire is often used for fabricating heavy-duty machinery. It allows for clean, precise welds with minimal post-weld cleanup.
Benefits of Using Flux-Cored Wire
1. Better Performance in Challenging Conditions
One of the standout benefits of flux-cored wire is its ability to perform well in less-than-ideal conditions. Whether you’re dealing with wind, rain, or dirty metal surfaces, this wire gets the job done.
Reduced Equipment Needs
If you’re using self-shielded wire, you can skip the external shielding gas setup. This makes the process more straightforward and reduces costs for beginners or mobile welders.
Stronger Welds on Thicker Materials
Flux-cored wire provides deeper penetration, making it ideal for thick metals. This is especially useful in industries like construction and shipbuilding.
High Welding Speed
With a faster deposition rate, flux-cored wire allows you to complete projects quicker. This is a massive plus if you’re working on large-scale jobs.
Versatility
Whether you’re welding indoors or outdoors, on clean or dirty metal, flux-cored wire adapts to a wide range of situations.
Tips for Getting the Best Results with Flux-Cored Wire
Choose the Right Wire Type
Select self-shielded wire for outdoor projects and gas-shielded wire for indoor or controlled environments. Each has its strengths, so match the wire to your needs.
Dial in Your Settings
Flux-cored welding requires precise machine settings. Adjust your voltage, amperage, and wire feed speed based on the material thickness and wire type.
Keep Your Work Area Clean
While flux-cored wire is more forgiving than some methods, cleaning the metal surface before welding will still improve your results.
Mind Your Technique
Maintain a steady hand and a consistent travel angle. A dragging technique (pulling the weld) usually works best for flux-cored welding.
Be Prepared for Spatter
Flux-cored welding produces more spatter than MIG welding. Using anti-spatter spray and wearing appropriate protective gear will save you time and effort.
Is Flux-Cored Wire Right for You?
Flux-cored wire is an excellent choice if you’re tackling outdoor projects, welding thick materials, or need a versatile, user-friendly option. However, it might not be the best fit for thin materials or jobs requiring ultra-clean welds.
If you’re a hobbyist or DIYer looking for a reliable welding method without a steep learning curve, self-shielded flux-cored wire could be your best friend. On the other hand, if you’re working in a controlled indoor environment, gas-shielded flux-cored wire might offer the precision you need.
Common Mistakes to Avoid
Using the Wrong Wire Type
Choosing the wrong type of flux-cored wire can lead to poor weld quality or unnecessary complications. Always match the wire to your project requirements.
Skipping Maintenance
Regularly clean your welding equipment and inspect the wire for rust or damage. A well-maintained setup ensures consistent performance.
Ignoring Heat Settings
Too much heat can lead to burn-through, especially on thinner metals. Always test your settings on scrap material before starting the actual weld.
Conclusion
Flux-cored wire is a versatile and powerful tool that has carved out its place in the welding world. Whether you’re a seasoned professional or just starting, understanding its applications and benefits will help you use it effectively.
From construction sites to shipyards, automotive repairs, and industrial fabrication, flux-cored wire shines in challenging conditions where other methods might struggle. While it’s not perfect for every job, its reliability, cost-effectiveness, and ease of use make it a fantastic option for many welding tasks.
If you’re curious about whether flux-cored wire is right for your next project, give it a try. You’ll likely be impressed with what it can accomplish!
FAQs
What is the difference between self-shielded and gas-shielded flux-cored wire?
Self-shielded wire doesn’t require an external shielding gas, making it ideal for outdoor projects. Gas-shielded wire, on the other hand, provides cleaner welds but requires a gas setup.
Can flux-cored wire be used on thin materials?
While possible, it’s challenging to use flux-cored wire on thin materials due to the risk of burn-through. MIG welding with gas is often a better choice for thin metals.
Is flux-cored welding good for beginners?
Yes! Flux-cored welding is beginner-friendly, especially self-shielded wire, as it doesn’t require additional equipment like gas tanks.
How do I reduce spatter when using flux-cored wire?
To minimize spatter, ensure your machine settings are correct and clean the workpiece thoroughly. Anti-spatter spray can also help.
What metals can I weld with flux-cored wire?
Flux-cored wire is great for steel and stainless steel but isn’t suitable for non-ferrous metals like aluminum.
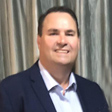
Endow Russel the owner chief editor of giftendow.com . I am a mechanical engineer and assign to an local firm with much experience in welding and industrial equipment.