Ultrasonic welding is a fascinating and innovative process that has transformed the way materials, particularly plastics and metals, are joined together. Unlike traditional welding techniques, ultrasonic welding doesn’t rely on heat or adhesives to bond materials. Instead, it uses high-frequency sound waves to create friction, which generates the energy needed to form a strong, reliable bond.
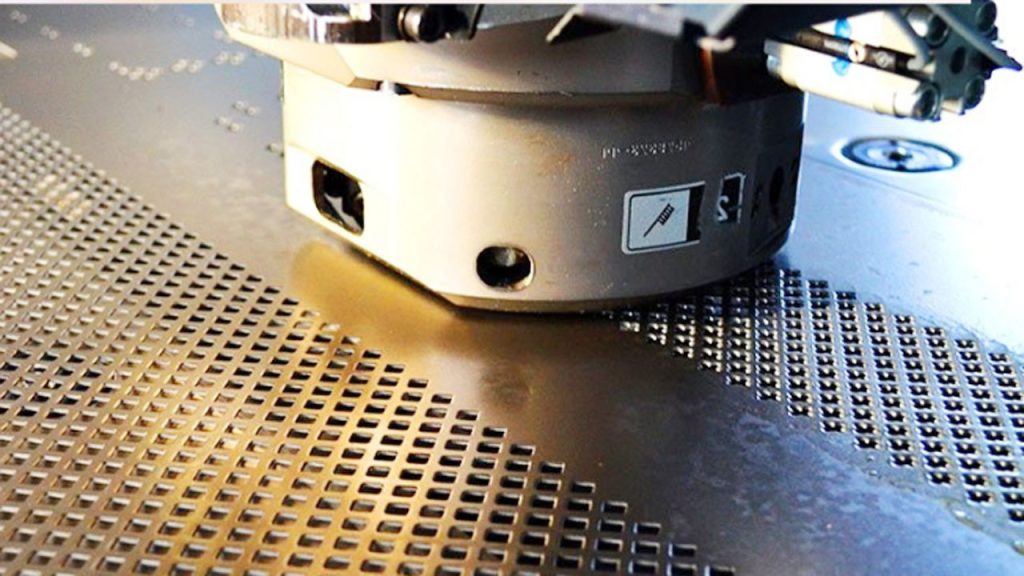
If you’ve been curious about ultrasonic welding and its different types, you’ve come to the right place. I’ve spent time exploring this process and its many applications, and I’m excited to share everything I’ve learned with you.
If you’re a professional in the manufacturing industry or just someone looking to understand more about this technology, this guide is here to break it all down in a simple and engaging way.
What Is Ultrasonic Welding?
Before we dive into the types, let’s quickly define what ultrasonic welding is. Ultrasonic welding is a technique that uses high-frequency ultrasonic vibrations to join two materials, typically plastics or thin metals. The vibrations generate localized heat through friction, allowing the materials to bond without needing additional adhesives, screws, or fasteners.
This process is widely used in industries like automotive, electronics, packaging, and even medical device manufacturing. It’s efficient, clean, and capable of producing precise welds, which makes it an ideal choice for delicate or high-volume production tasks.
Why Understanding the Types of Ultrasonic Welding Matters
The term “ultrasonic welding” might sound like a one-size-fits-all process, but in reality, there are several types, each suited for specific materials and applications. Choosing the right type of ultrasonic welding for your project is critical to achieving the best results. Let’s explore the most common types and what makes each one unique.
Ultrasonic Spot Welding
Ultrasonic spot welding is a versatile method often used for joining thin sheets of plastic or metal. This process focuses the ultrasonic energy on small, localized points to create a series of “spots” where the materials are bonded.
Applications:
- Automotive parts like dashboards and interior panels
- Packaging materials like plastic films
- Electronic enclosures
Advantages:
- Quick and efficient for small weld areas
- No additional fasteners or adhesives needed
- Minimal deformation of the material
Challenges:
- Limited to smaller surfaces
- Not suitable for high-strength structural applications
Ultrasonic Seam Welding
Ultrasonic seam welding involves continuous welding along a joint or seam. Unlike spot welding, this method uses a rolling motion to create a strong and consistent weld along the length of the material.
Applications:
- Packaging, such as sealing food containers and blister packs
- Medical devices requiring airtight seals
- Textiles, like protective clothing or filters
Advantages:
- Produces airtight and watertight seals
- Excellent for high-speed production
- Clean and precise finish
Challenges:
- Requires more complex equipment
- Limited to linear or slightly curved seams
Ultrasonic Insert Welding
This type of welding is specifically designed for embedding metal components, such as threaded inserts, into plastic materials. It’s widely used in applications where durability and the ability to disassemble parts are essential.
Applications:
- Automotive components with embedded fasteners
- Consumer electronics like laptops and smartphones
- Toys and household appliances
Advantages:
- Creates strong, permanent bonds between metal and plastic
- Reduces stress on surrounding materials
- Fast and repeatable process
Challenges:
- Limited to materials with specific melting points
- Requires careful alignment to avoid defects
Ultrasonic Tube Sealing
Ultrasonic tube sealing is a specialized type of ultrasonic welding used primarily in packaging applications. This process seals the ends of tubes made from flexible plastic materials.
Applications:
- Sealing toothpaste, cosmetic, or food tubes
- Industrial packaging for chemicals or adhesives
Advantages:
- Provides a strong, leak-proof seal
- Ideal for mass production in the packaging industry
- No heat damage to the contents inside the tube
Challenges:
- Only suitable for flexible plastic materials
- Requires precise control of the ultrasonic energy
Ultrasonic Metal Welding
While ultrasonic welding is most commonly associated with plastics, it’s also effective for joining thin sheets of metal. Ultrasonic metal welding uses vibrations to create a solid-state weld without melting the materials.
Applications:
- Battery assembly, such as lithium-ion batteries
- Electrical connections in automotive and aerospace industries
- Solar panels and other renewable energy components
Advantages:
- No need for flux, fillers, or solder
- Produces strong, conductive joints
- Minimal thermal distortion
Challenges:
- Limited to thin materials
- Requires precise alignment and high-quality equipment
Ultrasonic Plastic Welding
Ultrasonic plastic welding is the most widely used type of ultrasonic welding. It’s perfect for joining thermoplastic materials and is highly customizable based on the application.
Applications:
- Medical devices like syringes and IV bags
- Consumer goods such as plastic toys and containers
- Automotive parts like bumpers and instrument panels
Advantages:
- Fast and efficient for high-volume production
- Produces clean, strong welds with no adhesives required
- Eco-friendly, as it eliminates the need for additional materials
Challenges:
- Not suitable for all plastics (e.g., thermosetting plastics)
- Requires consistent material quality for optimal results
How to Choose the Right Type of Ultrasonic Welding
Choosing the right type of ultrasonic welding depends on several factors, including:
- Material Type: Are you working with plastics, metals, or a combination of both?
- Weld Area: Is the weld localized, continuous, or requires embedding?
- Application: Consider the specific requirements of your project, such as strength, appearance, or environmental resistance.
To simplify the decision-making process, here’s a quick comparison table:
Type of Welding | Best For | Common Materials | Key Advantage |
---|---|---|---|
Spot Welding | Small, localized welds | Plastics, thin metals | Quick and precise bonding |
Seam Welding | Continuous, watertight seams | Plastics, textiles | Airtight and clean welds |
Insert Welding | Embedding metal into plastic | Plastics with metal inserts | Strong, durable joints |
Tube Sealing | Packaging applications | Flexible plastics | Leak-proof and consistent seals |
Metal Welding | Electrical or structural metals | Thin metals | Strong, conductive connections |
Plastic Welding | Thermoplastic assembly | Thermoplastics | Fast and eco-friendly production |
Conclusion
Ultrasonic welding is a versatile and efficient technology that plays a vital role in modern manufacturing. By understanding the different types of ultrasonic welding, you can choose the best method for your specific needs, ensuring strong, reliable, and aesthetically pleasing bonds.
If you’re sealing a tube of toothpaste, assembling a lithium-ion battery, or creating a medical device, there’s a type of ultrasonic welding tailored to your application. Take the time to evaluate your materials, design requirements, and production goals, and you’ll be well on your way to mastering this innovative process.
FAQs
What materials can be welded using ultrasonic welding?
Ultrasonic welding works best with thermoplastics and thin metals, but it’s also effective for joining dissimilar materials like metal and plastic.
Is ultrasonic welding eco-friendly?
Yes, ultrasonic welding eliminates the need for adhesives, fasteners, or additional materials, making it an environmentally friendly process.
Can ultrasonic welding create airtight seals?
Absolutely. Techniques like ultrasonic seam welding are specifically designed to produce airtight and watertight seals.
How does ultrasonic welding compare to traditional welding?
Ultrasonic welding is faster, cleaner, and more precise, especially for plastics and thin materials, whereas traditional welding is better suited for heavy-duty metalwork.
What industries benefit most from ultrasonic welding?
Industries like automotive, electronics, packaging, medical devices, and renewable energy heavily rely on ultrasonic welding for its efficiency and precision.
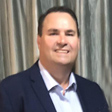
Endow Russel the owner chief editor of giftendow.com . I am a mechanical engineer and assign to an local firm with much experience in welding and industrial equipment.