Resistance welding is one of the most widely used and efficient welding processes in the manufacturing and fabrication industries. If you’re assembling automotive parts, crafting electrical components, or working on structural steel, resistance welding provides a fast, consistent, and cost-effective solution. But not all resistance welding techniques are created equal—each type comes with unique advantages and is suited for specific applications.
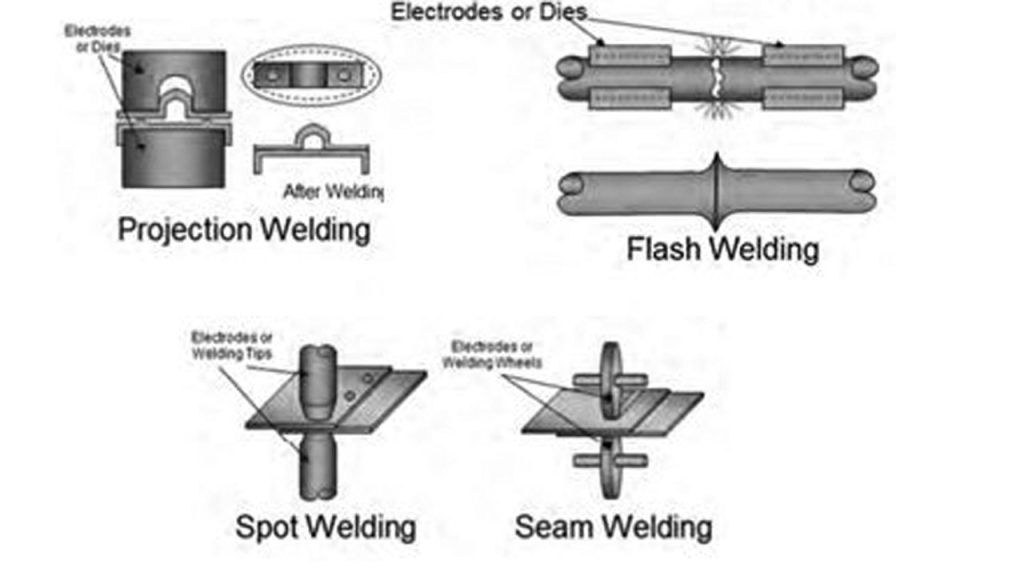
Image by greatspecials
In this article, I’ll take you through the major types of resistance welding, their principles, and where they are typically applied. Whether you’re a beginner in the field or looking to refine your knowledge, this guide will help you understand how resistance welding works and its practical uses.
What is Resistance Welding?
Resistance welding is a process that joins metals by applying heat generated from electrical resistance. In simpler terms, it uses electrical current and pressure to fuse two metal surfaces together without any filler material. This makes it a clean, efficient, and eco-friendly process.
What’s fascinating about resistance welding is its versatility—it can weld thin sheets of metal just as easily as thicker ones, all while delivering consistent results. Industries like automotive, aerospace, electronics, and construction rely heavily on resistance welding because of its precision, speed, and ability to automate the process.
Let’s dive into the different types of resistance welding and where they shine.
Spot Welding
What Is Spot Welding?
Spot welding is perhaps the most recognizable type of resistance welding. It involves creating welds at specific points (or “spots”) by clamping the metal parts between two electrodes. The electrodes pass electrical current through the metal, generating heat that fuses the pieces together.
Key Features
- Ideal for joining overlapping sheets of metal.
- Produces minimal distortion.
- Typically used for thin materials.
Applications of Spot Welding
Spot welding is widely used in the automotive industry, where it’s essential for assembling car bodies and frames. It’s also common in appliances, furniture manufacturing, and electronic enclosures.
Seam Welding
What Is Seam Welding?
Seam welding is similar to spot welding but involves creating a continuous weld along a seam instead of individual spots. This is achieved by using rolling electrodes, which maintain constant pressure and deliver a steady electrical current as the material moves through them.
Key Features
- Produces an airtight, watertight seal.
- Ideal for overlapping joints.
- Requires a consistent, uniform motion.
Applications of Seam Welding
Seam welding is commonly used in fabricating fuel tanks, pipelines, and aircraft components, where leak-proof joints are critical. It’s also used in creating cans and containers for food and beverages.
Projection Welding
What Is Projection Welding?
Projection welding uses raised projections or embossments on one or both of the workpieces. When current and pressure are applied, the projections concentrate the heat at specific points, creating strong welds.
Key Features
- Allows for multiple welds in one operation.
- Efficient and precise for small, localized areas.
- Reduces electrode wear.
Applications of Projection Welding
Projection welding is perfect for applications where multiple welds need to be made simultaneously, such as nut and bolt attachment, fastener welding, and electrical contact assembly. It’s often used in automotive parts, construction materials, and electrical appliances.
Flash Welding
What Is Flash Welding?
Flash welding involves clamping two metal pieces together and passing a high electrical current through them until their edges heat up and begin to melt. The pieces are then pressed together, forming a solid joint.
Key Features
- Joins thick materials.
- Produces a strong, durable weld.
- Requires minimal edge preparation.
Applications of Flash Welding
Flash welding is commonly used in railroad track construction, pipe fabrication, and structural steelwork. It’s also effective for joining circular or irregular shapes, such as gears or rings.
Upset Welding
What Is Upset Welding?
Upset welding is similar to flash welding but doesn’t involve the molten “flashing” process. Instead, it applies consistent pressure and heat to the entire area being welded, creating a strong joint.
Key Features
- Ensures uniform heating and bonding.
- Best suited for symmetrical parts.
- Produces minimal material waste.
Applications of Upset Welding
Upset welding is widely used in axle manufacturing, steel rod connections, and wire joining. It’s especially effective for creating continuous welds in chain links and rings.
Resistance Butt Welding
What Is Resistance Butt Welding?
Resistance butt welding joins two metal pieces by heating and pressing their ends together. It’s a straightforward process often used for materials with a smaller cross-section.
Key Features
- Efficient for simple joint designs.
- Works well for round or tubular parts.
- Ideal for non-overlapping connections.
Applications of Resistance Butt Welding
This method is commonly used in welding pipes, rods, and wire ends. It’s particularly valuable in construction, electrical applications, and furniture manufacturing.
High-Frequency Resistance Welding (HFRW)
What Is High-Frequency Resistance Welding?
HFRW utilizes high-frequency electrical current to generate heat. It’s especially effective for joining conductive materials quickly and efficiently, often in automated systems.
Key Features
- Delivers rapid, precise welds.
- Works for both ferrous and non-ferrous metals.
- Requires less heat input compared to traditional methods.
Applications of High-Frequency Resistance Welding
HFRW is widely used in tube and pipe manufacturing, automotive radiator fabrication, and heat exchanger construction. Its ability to produce consistent, high-quality welds makes it indispensable in mass production.
Choosing the Right Type of Resistance Welding
With so many options available, selecting the right type of resistance welding depends on the following factors:
- Material Thickness: Spot welding works best for thin sheets, while flash welding handles thicker materials.
- Joint Design: Seam welding is perfect for continuous seams, while projection welding focuses on multiple spots.
- Application Requirements: For airtight seals, go with seam welding. For heavy-duty connections, flash welding is ideal.
- Production Volume: HFRW is highly efficient for high-volume production.
Here’s a quick comparison table for better clarity:
Type of Welding | Key Features | Applications |
---|---|---|
Spot Welding | Welds specific points | Automotive, appliances, electronics |
Seam Welding | Creates airtight seams | Fuel tanks, pipelines, food containers |
Projection Welding | Localized welds on projections | Fasteners, automotive parts, electrical items |
Flash Welding | Strong, durable joints | Railroad tracks, structural steel, gears |
Upset Welding | Uniform heating and bonding | Axles, rods, chains |
Resistance Butt Welding | Simple joint connections | Pipes, rods, wire ends |
HFRW | Rapid, precise welds | Tubes, radiators, heat exchangers |
Conclusion
Resistance welding offers a wide range of techniques, each tailored to specific applications. Whether you’re creating strong joints for structural steel or precise welds for electronic components, there’s a resistance welding method to suit your needs. The efficiency, speed, and cleanliness of this process make it a go-to choice for industries around the world.
If you’re new to resistance welding, start by understanding the material and application requirements of your project. With the right tools, techniques, and a bit of practice, you’ll be able to achieve professional-grade results every time.
FAQs
What is the most common type of resistance welding?
Spot welding is the most commonly used type, especially in the automotive and appliance industries.
Can resistance welding be automated?
Yes, many resistance welding processes, such as spot welding and seam welding, are easily automated for mass production.
What materials can be welded using resistance welding?
Resistance welding works well with conductive metals like steel, stainless steel, aluminum, and copper.
Is resistance welding environmentally friendly?
Yes, it doesn’t require filler materials or produce harmful emissions, making it an eco-friendly welding option.
How do I choose the right resistance welding method?
Consider factors like material thickness, joint design, production volume, and application requirements to select the appropriate method.
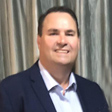
Endow Russel the owner chief editor of giftendow.com . I am a mechanical engineer and assign to an local firm with much experience in welding and industrial equipment.