You can find the tolerance for weld size or length in welding standards. These standards provide the necessary guidelines for precise welding practices.
They ensure safety and quality in manufacturing and construction projects. Understanding weld tolerances is crucial for anyone involved in welding. These tolerances dictate the acceptable limits for deviations in weld size or length. Adhering to these standards helps avoid structural issues and ensures the longevity of the weld.
Whether you’re a welder, engineer, or inspector, knowing where to find these tolerances is essential. This knowledge aids in achieving the desired strength and appearance of welds. It also ensures compliance with industry regulations. In this blog post, we will explore the sources where you can find these important guidelines. Stay tuned to learn more about maintaining quality and safety in your welding projects.
Introduction To Weld Tolerance
You can find the tolerance for weld size or length in welding codes and standards. These documents provide specific guidelines.
Weld tolerance refers to the permissible limits of variation in the weld size or length. These variations can affect the quality and strength of a welded joint. Understanding weld tolerance is crucial for maintaining the integrity of the structure. It ensures that the welds meet the required specifications.Importance Of Weld Tolerance
Weld tolerance helps in maintaining safety standards. It ensures that the welded joints are strong and durable. Accurate weld tolerance prevents structural failures. It also helps in avoiding costly repairs. Proper weld tolerance contributes to the overall quality of the construction. It ensures that the final product is reliable and safe.Common Welding Standards
Several standards define weld tolerances. The American Welding Society (AWS) provides guidelines. The International Organization for Standardization (ISO) also sets standards. These standards help in achieving consistency. They ensure that the welds are within acceptable limits. Adhering to these standards is essential for quality control. It helps in producing high-quality welds. “`Types Of Weld Tolerances
When it comes to welding, precision is key. Weld tolerances refer to the acceptable limits within which weld size and length can vary. These tolerances ensure the strength and safety of the weld. Understanding these can make the difference between a successful project and a structural failure. Let’s dive into the two main types: size tolerance and length tolerance.
Size Tolerance
Size tolerance is all about the thickness and width of the weld. It’s like baking a cake; you need the right amount of ingredients. If the weld is too small, it might not hold. Too big, and you’re wasting material. Size tolerance ensures that the weld is just right. For instance, if the specified weld size is 5 mm, the size tolerance might allow for a weld between 4.8 mm and 5.2 mm.
Specified Size | Size Tolerance Range |
---|---|
5 mm | 4.8 mm – 5.2 mm |
10 mm | 9.8 mm – 10.2 mm |
Length Tolerance
Length tolerance is about how long the weld runs. Imagine drawing a straight line; it’s hard to make it perfect. Length tolerance allows for small variations in the weld’s length. For example, if the weld should be 50 cm long, a length tolerance might let it be anywhere from 49.5 cm to 50.5 cm.
- Short Welds: For short welds, the tolerance might be tighter.
- Long Welds: For longer welds, there’s usually a bit more leeway.
Remember, just like in cooking, following the recipe (or in this case, the tolerance limits) can lead to a perfect result. Too much deviation, and you might end up with a weld that’s not up to snuff. So, always check the specified tolerances and stick to them.
Now, next time someone asks, “Where can you find the tolerance for weld size or length?” you can confidently explain the types of weld tolerances and their importance. Happy welding!
Industry Standards For Weld Tolerance
When it comes to welding, precision is everything. Whether you’re working on a massive construction project or a simple home repair, knowing the tolerance for weld size or length is crucial. But where do you find these tolerances? Industry standards, of course! These standards ensure that welds are safe, strong, and up to code. Let’s dive into the specifics of some key organizations that set these benchmarks.
American Welding Society (aws)
The American Welding Society (AWS) is like the big brother of welding standards in the United States. They have a bunch of guidelines that help welders achieve perfection in their craft. These guidelines cover various aspects, including weld size, length, and even the appearance of the weld. The AWS D1.1 Structural Welding Code is particularly important for those involved in structural steel welding.
For example, AWS D1.1 provides detailed tables that specify acceptable tolerances for different types of welds. Imagine you’re welding a beam for a bridge. The AWS standard will tell you the exact range of weld sizes that are acceptable. It’s like having a rulebook to make sure everything fits perfectly!
International Organization For Standardization (iso)
Now, let’s take a trip across the pond to the International Organization for Standardization, better known as ISO. This organization sets global standards, making sure welders from Tokyo to Toronto are on the same page. ISO 5817 is the standard you’ll want to get familiar with. It specifies the quality levels for imperfections in welded joints.
One interesting thing about ISO standards is that they categorize weld quality into three levels: B (stringent), C (intermediate), and D (moderate). Think of it as grading welds based on their quality. So, whether you are working on a high-stress component that needs top-notch welds or a less critical part, ISO has you covered.
Aspect | AWS | ISO |
---|---|---|
Scope | Primarily U.S. | Global |
Key Standard | D1.1 | ISO 5817 |
Quality Levels | Single standard | Three levels (B, C, D) |
So, whether you’re working in the U.S. or abroad, knowing these standards will help you produce high-quality welds that are up to snuff. And remember, a good weld is not just about strength; it’s about safety and reliability too. So, keep these standards handy and weld away with confidence!
Engineering Drawings And Weld Tolerance
Engineering drawings are essential in welding projects. They show the details and measurements needed. Understanding these drawings helps ensure accuracy and quality. Weld tolerance is a key part. It specifies the acceptable limits for weld size or length.
Reading Engineering Drawings
Reading engineering drawings is a crucial skill. Start with the title block. It contains important information about the drawing. Next, focus on the views. There are usually three views: top, front, and side.
Each view provides different details. Pay attention to dimensions and notes. These often include weld size and length. Always cross-check these details with the title block.
Key Symbols And Notations
Engineering drawings use specific symbols for welds. Understanding these symbols is important. The most common is the fillet weld symbol. It looks like a triangle. Another common symbol is the groove weld. It appears as a rectangle or V shape.
Notations on the drawings are also key. They provide additional instructions. For example, ‘all around’ means the weld goes around the entire joint. ‘Intermittent’ indicates the weld is not continuous.
Recognizing these symbols and notations ensures proper welds. It also helps in meeting the specified tolerances. Accurate welds lead to stronger and safer structures.
Software Tools For Weld Tolerance
Software tools help you find the tolerance for weld size or length. These tools make the job easier and more accurate. Let’s explore two main types of software tools that can help: CAD programs and simulation software.
Cad Programs
CAD programs are essential for weld tolerance. These programs let you design and model welds. You can set specific tolerances for weld size and length. CAD programs provide precise measurements. This ensures your welds meet quality standards. Popular CAD programs include AutoCAD and SolidWorks. These tools are user-friendly. They offer a range of features. These features help you visualize and adjust your welds. You can easily modify your designs. This saves time and reduces errors.
Simulation Software
Simulation software is another tool for weld tolerance. These programs simulate the welding process. They show how welds will behave under different conditions. This helps you understand potential issues. You can see how welds will react to stress and heat. Simulation software provides detailed analysis. This includes data on weld size and length tolerances. Examples of popular simulation software are ANSYS and Simufact Welding. These tools are powerful. They offer in-depth insights. This helps you create better welds. You can ensure your welds are strong and reliable. Simulation software is a valuable addition to your toolkit.
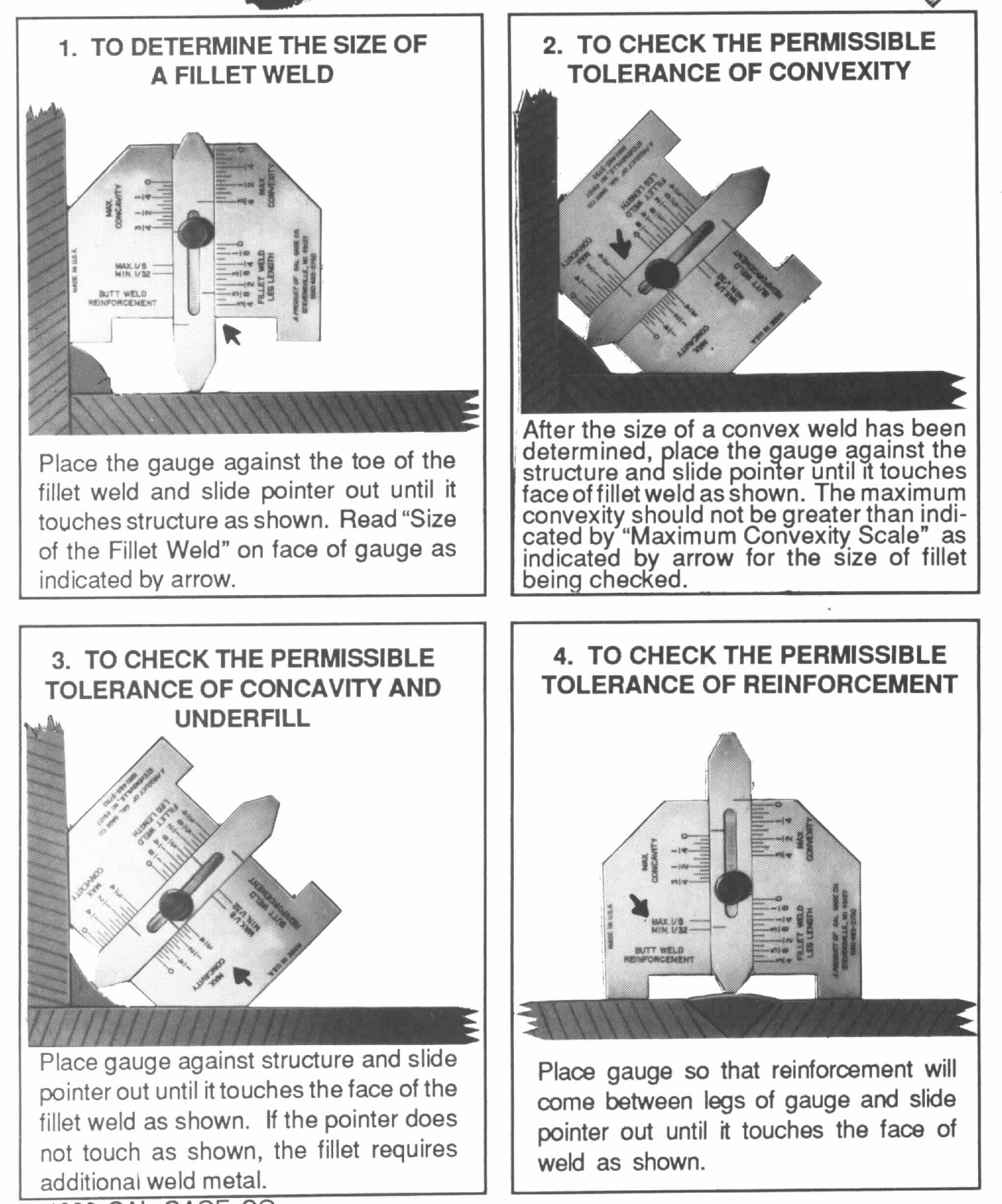
Credit: www.newmantools.com
Practical Applications In Welding
Welding is a critical process in many industries. It involves joining materials, usually metals, by melting and fusing them. But, did you know that the size and length of the welds are crucial too? Yes, these factors can affect the strength and durability of the weld. So, where can you find the tolerance for weld size or length? Let’s dive into some practical applications in welding to understand better.
Automotive Industry
The automotive industry relies heavily on welding. Cars are made up of many metal parts that need to be joined together securely. The tolerance for weld size and length is vital here. Why? Because even a small error can lead to big problems. Imagine driving a car with weak welds. Scary, right?
In the automotive industry:
- Welds must be precise to ensure safety.
- Too small welds might break under stress.
- Too large welds can add unnecessary weight and cost.
Manufacturers follow strict guidelines to maintain the right balance. They use advanced tools to measure the welds accurately. This ensures that every car is safe and reliable.
Construction And Infrastructure
When it comes to construction, welding is like the backbone of a building. Skyscrapers, bridges, and even your home rely on strong welds. Here, the tolerance for weld size and length is equally important.
Consider these points:
- Buildings need to withstand various forces like wind, earthquakes, and weight.
- Welds must be strong enough to hold the structure together.
- Incorrect welds can lead to structural failures.
Engineers and welders work together to ensure every weld meets the required standards. They use detailed blueprints and follow codes like the AWS D1.1 Structural Welding Code. This helps in maintaining the integrity of the construction.
So, whether it’s the car you drive or the building you live in, weld size and length matter a lot. The tolerance for these factors is not just a technical detail; it’s a matter of safety and reliability. Next time you see a welder at work, you’ll know how important their job is. They are not just joining metals; they are building our world.
Challenges In Maintaining Weld Tolerance
Welding is a precise art and science. It’s essential to get it right, especially when it comes to weld size or length. But, achieving consistent weld tolerance can sometimes feel like trying to catch lightning in a bottle. Let’s explore some of the biggest challenges welders face in this quest.
Material Properties
Every piece of metal has its own personality. Some are easy-going, like aluminum, while others, like stainless steel, can be stubborn. The properties of the material being welded play a huge role in maintaining weld tolerance. Different metals expand and contract differently when heated. This can make keeping a consistent weld size or length quite tricky.
- Expansion and Contraction: Metals like steel expand when heated and contract upon cooling. This can distort the weld if not managed properly.
- Heat Resistance: Some metals can handle more heat than others without warping. For instance, titanium is strong but reacts very differently to heat than aluminum.
Imagine trying to keep a consistent weld on a piece of metal that behaves like a hot-headed teenager! It’s challenging but not impossible with the right techniques and understanding of material properties.
Human Factors
Let’s be honest, we are all human, and humans make mistakes. Even the best welders can have an off day. Human factors are a significant challenge in maintaining weld tolerance. Here are some common issues:
- Fatigue: Welding can be exhausting. A tired welder might not hold the torch as steadily, leading to variations in the weld.
- Experience: New welders might not have the same level of skill as seasoned professionals, which can affect the consistency of their work.
- Concentration: Welding requires intense focus. Distractions or lapses in concentration can lead to errors in weld size or length.
Let’s not forget that even the most seasoned welders are not immune to these factors. It’s like driving a car; no matter how experienced you are, there are days when you might just miss a turn or two.
So, whether it’s the unpredictable nature of metal or the human element, maintaining weld tolerance is a challenge that requires skill, patience, and a bit of understanding. But with practice and the right knowledge, it’s a challenge that can be met head-on.
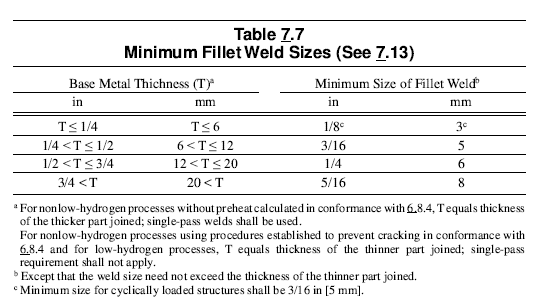
Credit: aqcinspection.com
Best Practices For Ensuring Weld Tolerance
Ensuring weld tolerance is essential for the safety and durability of any construction project. Without proper weld tolerance, structures can fail, leading to costly repairs or even hazardous situations. Fortunately, by following some best practices, you can ensure that your welds meet the necessary standards. Let’s dive into some proven methods to keep your welds in check.
Regular Inspections
One of the most important practices is conducting regular inspections. Think of it like going to the doctor for a check-up. Just as you need to ensure your health, welds need to be inspected to ensure their integrity. Regular inspections help identify any issues early before they become significant problems.
- Use visual inspections to spot visible defects.
- Employ non-destructive testing (NDT) methods like ultrasonic testing for internal flaws.
- Schedule inspections at consistent intervals, depending on the project’s requirements.
In my experience, scheduling inspections every few weeks can save you from future headaches. It’s like catching a cold before it turns into the flu!
Proper Training And Certification
Another crucial aspect is ensuring that all welders have proper training and certification. It’s like hiring a chef who knows their way around the kitchen. You wouldn’t trust just anyone to handle a delicate recipe, would you?
- Ensure welders receive training from accredited institutions.
- Verify that they hold certifications relevant to the type of welding they’re performing.
- Encourage continuous education and skills updates to keep up with industry standards.
For instance, I once worked with a team that had a mix of certified and uncertified welders. The difference in the quality of work was night and day. It’s not just about getting the job done; it’s about doing it right!
Practice | Benefits |
---|---|
Regular Inspections | Identifies defects early, ensures safety and quality |
Proper Training and Certification | Guarantees skilled workmanship, compliance with standards |
By following these best practices, you can be confident that your welds will hold up under pressure. After all, nobody wants to deal with a weld gone wrong. So, invest in regular inspections and ensure your team is properly trained and certified. Your projects—and peace of mind—will thank you!

Credit: www.amazon.com
Frequently Asked Questions
What Is The Tolerance On Weld Size?
The tolerance on weld size typically depends on the welding code or standards used. Common tolerances range from ±1/16 inch to ±1/8 inch. Always refer to specific welding standards for precise requirements.
Where Is The Weld Size Located?
The weld size is located on the welding symbol. It appears on the same side of the reference line as the weld symbol.
What Is The Tolerance For Welding Location?
The tolerance for welding location varies based on project specifications and standards. Typical tolerance ranges from ±1mm to ±3mm. Always consult the welding code or project guidelines for exact requirements.
How To Determine The Weld Size?
To determine weld size, consult design specifications and engineering drawings. Use welding codes and standards for guidance. Measure throat thickness and leg length accurately.
Conclusion
Finding weld size or length tolerance is essential for a successful project. Standards and guidelines provide the necessary specifications. Always double-check with the relevant codes. Consult with experienced professionals when in doubt. This ensures your welds meet safety and quality standards.
Proper adherence guarantees durability and integrity in your work. Remember, precision matters in welding. Stay informed and maintain accuracy. This approach leads to reliable and safe welds every time.