Welding stainless steel can be tricky. Choosing the right process matters.
Stainless steel is valued for its strength and resistance to corrosion. But welding it requires special techniques. The best welding process ensures quality, durability, and safety. Understanding the best methods can save time and money. It helps avoid common issues like warping and rust.
This blog explores the top welding processes for stainless steel. Each process has unique benefits and challenges. Whether you’re a novice or an expert, this guide will help you choose the right method. Dive in to discover the best practices for welding stainless steel.
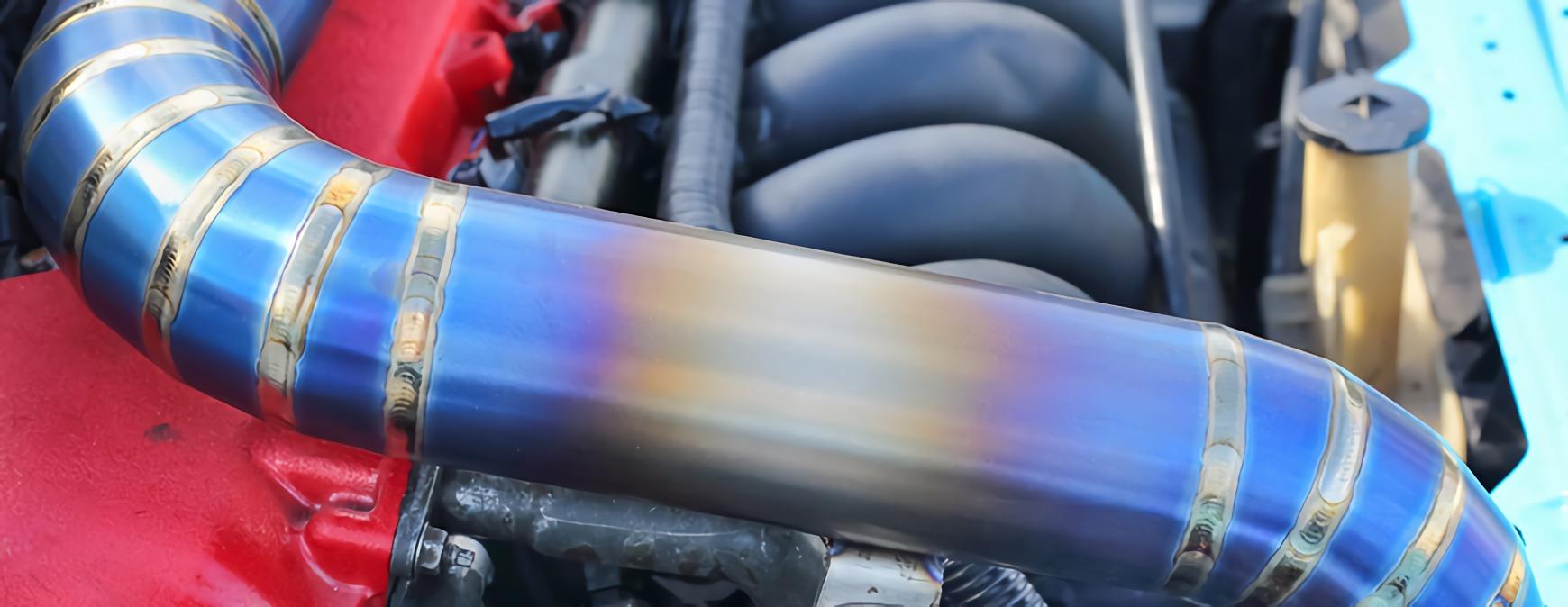
Credit: www.tws.edu
Tig Welding
When it comes to welding stainless steel, TIG Welding, or Tungsten Inert Gas welding, often takes the top spot. This process is renowned for its precision and ability to produce high-quality welds. But what makes TIG welding so special? Let’s dive into the details.
Advantages Of Tig Welding
TIG welding offers several advantages, especially when working with stainless steel. Here are some key benefits:
- Precision and Control: TIG welding allows for precise control over the heat and the weld, ensuring clean and accurate results.
- High-Quality Welds: It produces welds that are both strong and aesthetically pleasing, with minimal spatter and clean finishes.
- Versatility: Suitable for welding thin materials and capable of welding a variety of metals, including stainless steel, aluminum, and more.
- Low Distortion: The focused heat input reduces the risk of warping and distortion, which is crucial when working with thin stainless steel sheets.
Best Practices For Tig Welding Stainless Steel
To achieve the best results with TIG welding on stainless steel, here are some best practices to follow:
- Clean the Surface: Ensure the stainless steel surface is clean and free from contaminants like oil, dirt, and rust. Use a stainless steel brush or acetone for cleaning.
- Use the Right Electrode: A tungsten electrode with a pointed tip is ideal for stainless steel. A 2% thoriated or ceriated tungsten is often recommended.
- Choose the Correct Filler Rod: Select a filler rod that matches the stainless steel grade you are welding. ER308L is a common choice for 304 stainless steel.
- Set Proper Amperage: Adjust the amperage based on the thickness of the stainless steel. Too much heat can cause warping, while too little can result in weak welds.
- Maintain a Steady Hand: Keep a steady hand and a consistent arc length. A short arc length ensures better control and less contamination.
- Use Argon Gas: Shield the weld with pure argon gas to prevent oxidation and ensure a clean weld pool.
Remember, practice makes perfect. If you’re new to TIG welding, take your time to practice on scrap pieces before tackling your main project. And don’t forget to have fun with it – after all, there’s something quite satisfying about creating a flawless weld, isn’t there?
In conclusion, TIG welding is an excellent choice for welding stainless steel due to its precision, quality, and versatility. By following best practices, you can achieve professional-grade results and make your welding projects stand out.
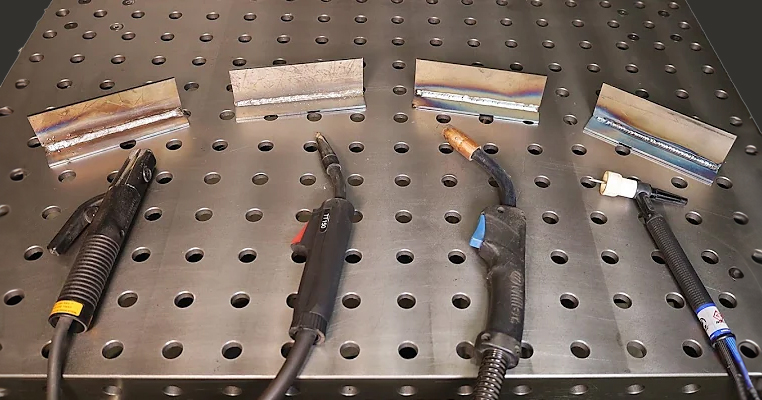
Credit: blog.red-d-arc.com
Mig Welding
When it comes to joining stainless steel, there are several welding processes to consider. One of the most popular and effective methods is MIG welding. MIG stands for Metal Inert Gas, and this technique is prized for its efficiency and ease of use. But what makes MIG welding so special for stainless steel? Let’s dive into the details.
Benefits Of Mig Welding
MIG welding offers numerous advantages for those working with stainless steel. Here are some key benefits:
- Ease of Use: MIG welding is beginner-friendly. With some practice, even novices can achieve strong welds.
- Speed: This process is faster compared to other welding methods, making it ideal for larger projects.
- Clean Welds: MIG welding produces neat and clean welds, which is crucial when working with stainless steel.
- Versatility: It is suitable for various thicknesses of stainless steel, from thin sheets to thicker plates.
- Minimal Post-Weld Cleanup: The process generates less spatter, reducing the time spent on post-weld cleaning.
Now, with these benefits in mind, let’s explore some effective techniques for MIG welding stainless steel.
Techniques For Mig Welding Stainless Steel
Getting the best results from MIG welding requires using the right techniques. Here are some tips to help you master the process:
- Choose the Right Shielding Gas: Use a mixture of Argon and CO2. A common blend is 90% Argon and 10% CO2.
- Select the Correct Wire: Use stainless steel wire that matches the type of stainless steel you are welding. For example, use ER308L wire for 304 stainless steel.
- Maintain Proper Polarity: Ensure the machine is set to DCEP (Direct Current Electrode Positive) for MIG welding.
- Control Your Speed: Maintain a steady travel speed. Too fast or too slow can affect the quality of the weld.
- Use the Right Technique: Employ a push technique rather than a pull. This helps with better gas coverage and cleaner welds.
- Practice Proper Joint Preparation: Clean the metal thoroughly to remove any contaminants that could affect the weld quality.
Mastering these techniques will not only improve the strength and appearance of your welds but also enhance your overall welding skills.
In conclusion, MIG welding is an excellent choice for working with stainless steel, offering benefits such as ease of use, speed, and clean welds. By following the right techniques, you can achieve high-quality welds that meet the demands of any project.
Stick Welding
Stick welding, also known as Shielded Metal Arc Welding (SMAW), is a popular method for welding stainless steel. This process uses an electric current to form an arc between the metal and the stick, or electrode. The electrode is coated with flux, which melts during welding, creating a protective gas shield and slag. This helps prevent contamination of the weld area.
Pros And Cons Of Stick Welding
Stick welding offers several advantages. It is versatile and can be used in various positions. It works well outdoors and in windy conditions. The equipment is simple and portable, making it suitable for fieldwork.
But there are drawbacks too. Stick welding can produce more spatter. It requires frequent rod changes and can be slower than other methods. Beginners may find it challenging to master.
Tips For Stick Welding Stainless Steel
Use the right electrode for stainless steel. E308L and E309L are common choices. Clean the metal surface before welding to ensure a strong weld. Adjust the amperage based on the thickness of the metal and the electrode used.
Maintain a short arc length to minimize spatter. Practice proper rod angle and travel speed. Avoid overheating the metal to prevent warping. Use a back-and-forth motion to create a smooth weld bead.
Flux-cored Arc Welding
Flux-Cored Arc Welding (FCAW) is a versatile welding process. It is especially useful for welding stainless steel. FCAW uses a wire electrode with a flux core. This core produces a shielding gas when heated. This gas protects the weld pool from contamination. FCAW is popular in construction and heavy manufacturing.
Why Choose Flux-cored Arc Welding?
FCAW offers many benefits. It provides high deposition rates. This means more metal is deposited in less time. It is also suitable for outdoor work. The shielding gas from the flux core reduces the need for external gas. This makes FCAW less sensitive to wind.
FCAW can weld thicker materials. It is ideal for structural applications. The process is also less complex. Operators can learn FCAW quickly. It works well on dirty or rusty metals. This reduces the need for extensive surface cleaning.
Steps For Flux-cored Arc Welding Stainless Steel
First, prepare your workspace. Ensure good ventilation. Clean the stainless steel surface. Remove dirt, oil, and rust. Choose the right wire for stainless steel. Use a wire with a flux core designed for stainless steel.
Second, set up your welding machine. Adjust the voltage and wire feed speed. Follow the manufacturer’s recommendations. Attach the ground clamp to your workpiece. Ensure a secure connection.
Third, begin welding. Hold the torch at a 10-15 degree angle. Maintain a steady travel speed. Keep a consistent arc length. Watch the weld pool. Adjust your speed as needed. Ensure even and smooth welds.
Finally, inspect your welds. Look for any defects. Clean the welded area. Remove any slag or spatter. Ensure strong and clean welds. Practice improves your skills. Keep welding to perfect your technique.
Laser Welding
Laser welding is a modern technique for joining stainless steel. It uses a laser beam to fuse materials. The process is precise and efficient. It creates strong, clean welds with minimal distortion. This method is popular in various industries for its accuracy and speed.
Advantages Of Laser Welding
Laser welding offers many benefits for stainless steel. It ensures high precision and control. This results in cleaner and stronger welds. The heat-affected zone is smaller. Thus, there is less distortion in the material. Laser welding is also fast. It can weld thin and thick materials easily.
The process is versatile. It can weld complex shapes and hard-to-reach areas. This makes it ideal for intricate designs. Laser welding is also automated. This reduces the need for manual labor. It increases productivity and consistency.
Applications Of Laser Welding In Stainless Steel
Laser welding is used in various industries. In the automotive industry, it joins car parts and frames. It ensures strong and durable joints. In the medical field, it welds surgical instruments. The precision is vital for these tools.
The aerospace industry also uses laser welding. It welds engine parts and structural components. This ensures safety and reliability. In electronics, it joins small and delicate parts. The low heat input prevents damage to sensitive components.
The food and beverage industry benefits too. Laser welding creates smooth, clean joints. This is important for hygiene and safety. Stainless steel containers and pipelines are often welded using this method.
Choosing The Right Filler Material
When it comes to welding stainless steel, selecting the appropriate filler material is crucial. The right filler material ensures strong welds, corrosion resistance, and overall durability. However, choosing the right one can seem daunting with so many options available. This guide will walk you through the types of filler materials and the factors to consider for making the best choice.
Types Of Filler Materials
Various filler materials suit different types of stainless steel. Here are the most common:
- ER308L – Ideal for 304 and 308 stainless steel types. It provides good corrosion resistance.
- ER309L – Used for welding dissimilar metals, like joining stainless steel to mild steel.
- ER316L – Best for 316 stainless steel, especially in marine environments due to its superior corrosion resistance.
- ER347 – Suitable for high-temperature applications, often used in the aerospace industry.
Factors To Consider
Choosing the right filler material involves more than just knowing the types available. Here are key factors to consider:
- Base Material Compatibility: Ensure the filler material matches or exceeds the properties of the base metal. For example, ER316L is used for 316 stainless steel due to its similar composition.
- Corrosion Resistance: Depending on the environment, like marine or acidic conditions, select a filler that offers the necessary resistance. ER316L is preferred in marine settings.
- Mechanical Properties: Consider the strength and ductility required for the application. Some fillers offer higher tensile strength, which is essential for structural welds.
- Application Specifics: Different applications may demand specific properties. For instance, ER347 is ideal for high-temperature conditions, making it suitable for aerospace components.
When in doubt, consult with a welding professional or refer to manufacturer guidelines to ensure the best match. Remember, the right filler material makes all the difference in the quality and longevity of your welds.
Common Welding Challenges
Choosing the best welding process for stainless steel can be challenging. TIG welding offers precision and clean welds. MIG welding provides speed and ease for beginners.
Welding stainless steel presents unique challenges. The material’s properties can complicate the welding process. Understanding these challenges is vital for achieving strong, durable welds.Avoiding Distortion
Stainless steel warps easily from heat. This can distort the welded parts. To avoid this, control the heat input. Use clamps and fixtures to hold the pieces in place. Applying too much heat too fast can cause major issues. It’s essential to balance the heat to avoid deformation.Preventing Corrosion
Stainless steel is known for its corrosion resistance. But welding can affect this property. Using the wrong filler material can lead to rust. Clean the weld area thoroughly before and after welding. Contamination can cause corrosion. Also, pickling and passivation can help restore the steel’s protective layer. “`
Credit: americantorchtip.com
Safety Tips
Welding stainless steel requires special attention to safety. Proper precautions prevent injuries and ensure a smooth welding process. Following these tips can help create a safer working environment.
Protective Gear
Always wear the right gear when welding stainless steel. A welding helmet with a dark lens protects your eyes from bright light and sparks. Fire-resistant clothing shields your skin from burns and hot metal splashes. Leather gloves provide hand protection and improve grip. Steel-toed boots keep your feet safe from falling objects.
Safe Welding Practices
Ensure your workspace is well-ventilated. Welding stainless steel releases fumes that can be harmful. Use a fume extractor or work in an open area. Keep your work area clean and free of flammable materials. Sparks can easily ignite nearby objects, causing fires. Maintain a safe distance from others to avoid accidents.
Always inspect your equipment before starting. Check for damaged cables, loose connections, and other potential hazards. Use the correct welding settings for stainless steel to prevent material damage and ensure a strong weld. Follow the manufacturer’s guidelines to ensure safe and effective welding.
Frequently Asked Questions
Is Mig Or Tig Better For Stainless Steel?
TIG welding is better for stainless steel. It provides more precision and cleaner welds. MIG welding is faster but less accurate.
What Is The Best Way To Weld Stainless Steel?
The best way to weld stainless steel is using the TIG welding process. This method ensures precision and clean welds. Use a tungsten electrode and argon gas for shielding. Maintain a clean work area and control heat input to prevent warping.
Always wear appropriate safety gear.
Is It Better To Weld 304 Or 316 Stainless Steel?
316 stainless steel is better for welding. It offers improved corrosion resistance, especially in chloride environments, compared to 304 stainless steel.
What Type Of Welding Is Used For Stainless Steel?
TIG welding, also known as Gas Tungsten Arc Welding (GTAW), is commonly used for stainless steel. MIG welding, or Gas Metal Arc Welding (GMAW), is also suitable. Both methods provide strong, clean welds.
Conclusion
Choosing the best welding process for stainless steel ensures strong and durable joints. TIG welding offers precision and a clean finish. MIG welding provides speed and versatility. Stick welding is cost-effective and great for outdoor jobs. Each method has its benefits.
Consider your project needs and skill level. Always prioritize safety and quality. With the right process, your stainless steel projects will be successful. Explore, practice, and perfect your welding skills. Happy welding!