Welding with aluminum differs significantly from welding with steel. Aluminum and steel have unique properties that require different techniques.
Aluminum and steel are among the most commonly welded metals. While both are essential in various industries, they present distinct challenges. Aluminum is softer, melts at a lower temperature, and is more prone to warping. Steel, on the other hand, is stronger, melts at a higher temperature, and is less likely to distort.
These differences affect the welding process, from preparation to execution. Understanding these distinctions is crucial for achieving strong, durable welds. In this blog post, we will explore the key differences in welding techniques, equipment, and considerations for aluminum and steel. This guide will help you navigate the unique challenges each metal presents.
Material Properties
Understanding the material properties of aluminum and steel is vital for successful welding. Each metal has unique characteristics that affect the welding process. Let’s delve into the specifics of each material.
Aluminum Characteristics
Aluminum is lightweight and corrosion-resistant. This makes it ideal for many applications. It has a high thermal conductivity, which means it heats up quickly. This can be challenging for welders. Aluminum also has a lower melting point compared to steel. This requires careful control of heat input. Aluminum’s oxide layer needs to be removed before welding. This layer can prevent proper weld penetration. Proper cleaning is crucial for strong welds.
Steel Characteristics
Steel is heavier and stronger than aluminum. It’s widely used in construction and manufacturing. Steel has a higher melting point, making it more heat-resistant. This allows for more flexibility in welding techniques. Steel’s thermal conductivity is lower than aluminum’s. This means it retains heat better. Steel is less prone to warping during welding. It also doesn’t form an oxide layer like aluminum. This simplifies the welding process.
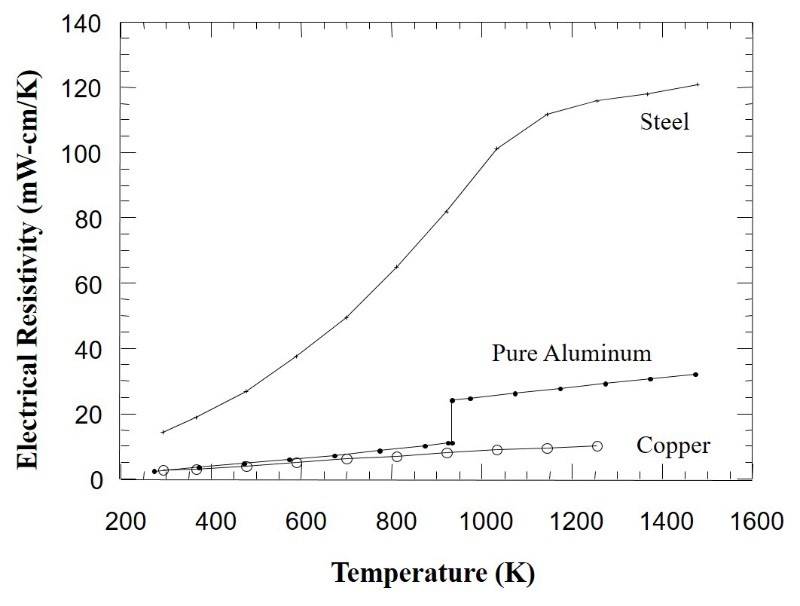
Credit: ahssinsights.org
Thermal Conductivity
Thermal conductivity plays a crucial role in welding. It determines how heat moves through a material. Aluminum and steel have different thermal properties. This affects how they are welded. Understanding these differences can improve welding results.
Heat Distribution In Aluminum
Aluminum has high thermal conductivity. It absorbs and spreads heat quickly. This can cause challenges during welding. The heat spreads away from the weld area. This makes it hard to maintain a stable weld pool. Aluminum also has a low melting point. This increases the risk of burn-through.
Proper heat management is essential. Use higher travel speeds and lower heat inputs. Preheating the material can help. It reduces the temperature difference between the weld and the base metal. This ensures better weld quality and reduces distortion.
Heat Distribution In Steel
Steel has lower thermal conductivity. It does not spread heat as quickly as aluminum. This makes it easier to control the weld pool. Steel has a higher melting point than aluminum. It is less prone to burn-through.
Welding steel requires different techniques. Slow travel speeds and higher heat inputs are common. This helps penetrate the thicker material. Preheating is not always necessary. However, it can help with thicker sections. This reduces the risk of cracking.
Melting Points
When it comes to welding, understanding the melting points of materials is key. Aluminum and steel are common metals in welding, but they behave quite differently under heat. Let’s dive into the melting points of these two metals and see how that affects the welding process.
Aluminum Melting Temperature
Aluminum has a melting point of about 660 degrees Celsius (1,220 degrees Fahrenheit). That’s relatively low compared to many other metals. This means aluminum heats up and melts quickly. Here’s a fun fact: it’s so quick to heat that you might miss it if you blink!
Because of its low melting point, welding aluminum requires a delicate touch. If you apply too much heat, you can easily burn through the metal. It’s like walking on eggshells—one wrong step, and you’ve got a mess.
Another thing to note is that aluminum doesn’t change color much when it’s heated. Unlike steel, which glows red-hot, aluminum stays its shiny self until it suddenly melts. This can be tricky because you don’t get visual clues that it’s getting too hot.
Steel Melting Temperature
Steel, on the other hand, melts at a much higher temperature—about 1,370 degrees Celsius (2,500 degrees Fahrenheit). That’s more than twice the temperature required for aluminum. So, you need more heat to weld steel, and it takes longer to reach its melting point.
When welding steel, it’s easier to see when the metal is getting hot. It glows red, then orange, and finally white as it reaches higher temperatures. This gradual color change acts like a built-in thermometer, helping you judge when the metal is ready to weld.
However, higher temperatures also mean more energy is required, and with that comes the risk of warping or distorting the metal if not handled properly. But at least you won’t find yourself melting through steel as quickly as you might with aluminum.
Metal | Melting Point (Celsius) | Melting Point (Fahrenheit) |
---|---|---|
Aluminum | 660 | 1,220 |
Steel | 1,370 | 2,500 |
In summary, aluminum’s low melting point means it heats up and melts quickly, requiring careful control to avoid burning through. Steel’s higher melting point allows for more visible cues but demands more energy and brings its own challenges. Understanding these differences can make a world of difference in your welding projects.

Credit: www.fvmt.com
Oxidation And Contamination
Oxidation and contamination are critical factors in welding. Both aluminum and steel are prone to these issues. However, their reactions differ significantly. Understanding these differences is key for successful welding.
Aluminum Oxidation
Aluminum oxidizes quickly when exposed to air. This oxidation forms a thin, hard layer of aluminum oxide. This layer can impede welding. It has a much higher melting point than aluminum itself. Removing this layer is essential before welding. Using a stainless steel brush can help clean aluminum surfaces. Some welders also use chemical cleaners to remove the oxide layer.
Steel Oxidation
Steel also oxidizes but in a different manner. The rust on steel forms more slowly compared to aluminum oxide. Rust is porous and flaky, unlike aluminum oxide. This makes steel easier to clean before welding. A grinder or wire brush is often used to remove rust from steel. Proper cleaning ensures a strong weld. Contamination from dirt or oil can also affect the weld quality in steel. Always clean the surface thoroughly.
Welding Techniques
Welding techniques vary greatly based on the type of metal. Aluminum and steel require different methods due to their unique properties. Understanding these differences is essential for achieving strong, durable welds.
Methods For Aluminum
Aluminum welding needs special care. It is softer than steel and melts at lower temperatures. The oxide layer on aluminum melts at a higher temperature than the metal itself. This can lead to contamination if not handled properly.
TIG (Tungsten Inert Gas) welding is popular for aluminum. It offers precise control and clean welds. The welder must use a dedicated AC (Alternating Current) power source. AC helps remove the oxide layer effectively.
MIG (Metal Inert Gas) welding is also used. It is faster than TIG and suitable for thicker aluminum pieces. A spool gun or push-pull gun is necessary to prevent wire feeding issues.
Pre-cleaning aluminum is crucial. Remove any oil, dirt, or oxide layers before welding. Use a stainless steel brush or a chemical cleaner for best results.
Methods For Steel
Steel welding is more forgiving than aluminum. It has higher tensile strength and melts at higher temperatures. This makes it easier to work with and less prone to warping.
MIG welding is common for steel. It is efficient and works well with various thicknesses. MIG welding uses a continuous wire feed for consistent welds.
TIG welding is also used for steel, especially for precise and clean welds. It offers greater control and is ideal for thinner materials.
Stick welding (Shielded Metal Arc Welding) is another method for steel. It is versatile and works well in outdoor conditions. Stick welding is effective for thicker materials and provides strong welds.
Pre-cleaning steel is important but less critical than aluminum. Remove rust, paint, and dirt before welding. Use a wire brush or grinder for cleaning.
Equipment And Tools
Welding with aluminum differs from welding with steel in several ways. The equipment and tools used play a crucial role in achieving successful welds. Different materials need specific tools to ensure strong, clean welds.
Tools For Aluminum Welding
Welding aluminum requires a spool gun or push-pull gun. These tools feed the soft aluminum wire smoothly. A TIG welder with an AC setting is also essential. It provides the necessary heat control for aluminum. An argon gas cylinder ensures proper shielding for clean welds. A dedicated aluminum wire brush is needed to clean the workpiece. This avoids contamination from other metals.
Tools For Steel Welding
Welding steel often uses a MIG welder or stick welder. These tools provide the necessary power for steel. A CO2 or a mix of CO2 and argon gas cylinder is used. This helps in achieving optimal shielding. A steel wire brush or grinder cleans the surface before welding. This ensures strong welds by removing rust and debris. A chipping hammer is also useful for removing slag from the weld.
Joint Preparation
When it comes to welding, joint preparation is a crucial step that can make or break the success of your project. Whether you’re working with aluminum or steel, getting your joints ready involves careful attention to detail. But, how do these two metals differ in their preparation? Let’s dive into the specifics of preparing aluminum and steel joints.
Preparing Aluminum Joints
Welding aluminum requires a bit more finesse compared to steel. The first thing to note is that aluminum forms a thin oxide layer when exposed to air. This layer has a much higher melting point than the aluminum itself, so removing it is essential.
- Cleaning: Use a stainless steel brush or a chemical cleaner to remove the oxide layer.
- Degreasing: Ensure all oils and contaminants are wiped off with a solvent like acetone.
- Fit-Up: Aluminum expands more than steel when heated, so a tight fit-up is crucial to avoid gaps.
Aluminum is also softer than steel, so be gentle during the preparation to avoid any warping or damage. Have you ever tried to cut a cake with a dull knife? It’s a mess! The same goes for working with aluminum—sharp tools are your best friend.
Preparing Steel Joints
Steel, on the other hand, is a bit more forgiving but still requires proper preparation. Unlike aluminum, steel doesn’t form an oxide layer that affects welding. However, it can rust, and any rust must be removed before you start.
- Cleaning: A wire brush or grinder works well to remove any rust or mill scale.
- Degreasing: Like aluminum, steel should also be free of oils and contaminants. Use a simple degreaser.
- Fit-Up: Steel doesn’t expand as much as aluminum, but a good fit-up is still important for a strong weld.
One thing to keep in mind is that steel is heavier and harder. It’s like the difference between cutting through butter and cutting through a loaf of bread. Ensure your tools are up to the task to make the job easier.
In summary, joint preparation for aluminum and steel varies significantly. Aluminum needs a gentle touch and thorough cleaning, while steel requires rust removal and a sturdy approach. By understanding these differences, you can ensure your welding projects are strong and durable.
Common Challenges
Welding aluminum and steel presents different challenges. Each metal has unique properties. Understanding these differences can help you weld more effectively. Let’s explore the common challenges of welding with aluminum and steel.
Issues With Aluminum
Aluminum is softer than steel. This makes it more prone to damage. It also has a lower melting point. This means it can overheat easily. Aluminum conducts heat well. This can lead to heat distortion. Contamination is another issue. Aluminum can be easily contaminated with dirt or oil. Clean the surface thoroughly before welding.
Issues With Steel
Steel is harder and denser than aluminum. This makes it more durable but harder to weld. Steel requires higher temperatures to weld. This can make it more energy-intensive. Steel can also rust. This means you must clean it before welding. Warping can occur with steel, especially in thin sheets. This happens because of uneven cooling.

Credit: ahssinsights.org
Frequently Asked Questions
What Is The Difference Between Aluminium And Steel Welding?
Aluminium welding requires lower temperatures and specific techniques due to its high thermal conductivity. Steel welding needs higher temperatures and can use more common methods.
What Are The Disadvantages Of Aluminium Welding?
Aluminium welding can be challenging due to its high thermal conductivity. It requires precise control to avoid warping. Oxide layer removal is necessary for clean welds. Special equipment and skilled welders are often needed.
Can You Use A Steel Welder For Aluminum?
You can’t use a steel welder for aluminum. Aluminum requires a welder specifically designed for it, like TIG or MIG welders.
Why Is Aluminum Welding Hard?
Aluminum welding is challenging due to its high thermal conductivity and low melting point. It requires precise temperature control. The oxide layer on aluminum can contaminate welds, and specialized equipment and techniques are essential.
Conclusion
Welding with aluminum differs significantly from steel. Aluminum welds at lower temperatures. Steel requires higher heat. Aluminum conducts heat quickly. Steel retains heat longer. Different techniques are needed for each. Filler materials vary too. Understanding these differences is crucial. This ensures strong, durable welds.
Practice and experience help improve skills. Choose the right materials. Use proper equipment. Safety should always be a priority. Happy welding!