To calculate weld strength, you need to consider the type of weld, material, and load. It’s not just about the numbers; it’s understanding the basics.
Weld strength calculation is essential in ensuring structural integrity and safety. Whether you’re a seasoned welder or a beginner, knowing how to determine this strength can save time and prevent costly mistakes. This process involves understanding the properties of the materials you’re working with and the type of weld used.
By following a systematic approach, you can ensure your welds are strong and reliable. In this post, we will break down the steps to help you accurately calculate weld strength, providing you with the knowledge you need to carry out your projects with confidence.
Introduction To Weld Strength
Have you ever wondered what keeps a skyscraper standing tall or a car frame sturdy? The answer often lies in weld strength. Understanding weld strength is crucial for ensuring safety and durability in various structures. But what exactly is weld strength, and why is it so important?
Importance Of Weld Strength
Weld strength isn’t just a fancy term engineers throw around. It’s a critical factor that determines how much load a welded joint can handle before it breaks. Imagine a chain; each link needs to be strong enough to support the whole chain. Similarly, weld strength ensures each joint in a structure can withstand stress and pressure.
Without proper weld strength, buildings could collapse, vehicles might fail, and machinery could break down. That’s why understanding and calculating weld strength is essential for anyone involved in construction, manufacturing, or any industry that relies on welded joints.
Applications In Various Industries
Weld strength plays a pivotal role in many industries. Let’s take a closer look:
- Construction: From bridges to buildings, weld strength ensures the integrity and safety of structures.
- Automotive: Weld strength affects the durability and safety of cars, trucks, and even bicycles.
- Aerospace: Airplanes and spacecraft require impeccable weld strength to handle extreme conditions.
- Manufacturing: Many products, from household appliances to industrial machines, rely on strong welds for reliability.
Each industry has its own standards and requirements for weld strength, reflecting the specific demands and safety considerations of that field.
In a nutshell, weld strength is a fundamental concept that ensures the safety and durability of countless structures and products we rely on daily. Whether you’re building a skyscraper, designing a car, or crafting the next big thing in manufacturing, understanding and calculating weld strength is key to success. Ready to dive deeper into the calculations? Let’s get started!
Types Of Welds
Understanding the types of welds is essential for calculating weld strength. Different welds suit different projects and materials. The two most common types are butt welds and fillet welds.
Butt Welds
Butt welds join two pieces of metal end-to-end. This type of weld is strong and often used in construction. The weld can be applied with different techniques. Each technique affects the weld’s strength. A well-done butt weld can handle high stress.
Fillet Welds
Fillet welds join two pieces at a right angle. This type of weld is common in structural applications. The weld forms a triangle shape at the joint. Fillet welds are versatile and easy to apply. They distribute stress over a larger area. This makes them reliable for many uses.
Factors Affecting Weld Strength
When it comes to welding, understanding the strength of your weld is crucial. Why? Because the strength of a weld determines how well it will hold up under pressure. But what exactly affects weld strength? Let’s dive into some key factors.
Material Properties
Not all materials are created equal. Some metals are naturally stronger than others. For example, steel is much stronger than aluminum. But strength isn’t the only property to consider. Here are a few material properties that can affect weld strength:
- Composition: Different metals and alloys have different strengths and weaknesses.
- Thickness: Thicker materials generally create stronger welds.
- Hardness: Harder materials may be more difficult to weld properly.
- Corrosion Resistance: Materials that resist corrosion tend to hold up better over time.
Imagine trying to glue two pieces of paper together. It’s easy, right? Now, think about gluing two pieces of metal. That’s a whole different ball game!
Welding Techniques
The technique used in welding can make a huge difference. It’s not just about sticking two pieces of metal together. It’s about doing it in a way that ensures a strong, lasting bond. Some techniques are more effective than others. Let’s take a look:
- MIG Welding: This is great for beginners and works well with thin metals.
- TIG Welding: This offers precision and is ideal for thinner materials.
- Stick Welding: This is versatile and works well outdoors.
- Flux-Cored Welding: This is perfect for thick materials and can be used in any position.
Ever tried tying a knot? A simple knot might work for tying your shoes, but you’d need a different knot to secure a boat. Welding is similar. The technique you choose can make or break the strength of your weld.
In conclusion, if you want a strong weld, pay attention to both the material properties and the welding techniques. Choose the right material and technique, and you’ll have a weld that stands the test of time.
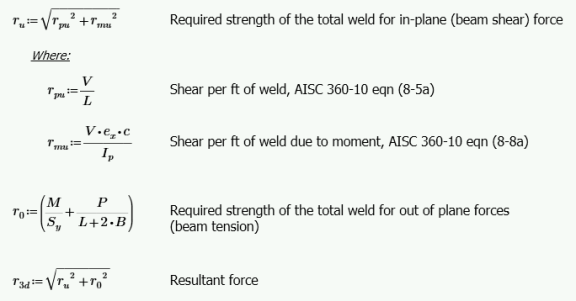
Credit: risa.com
Preparation For Calculation
Calculating weld strength is essential for ensuring the safety and reliability of welded structures. Proper preparation is the first step in this process. It requires gathering all necessary data and understanding the load requirements. Let’s dive into these preparatory steps.
Gathering Necessary Data
Before you start calculating weld strength, gather all relevant data. This includes material properties, weld dimensions, and joint configurations. Material properties involve tensile strength, yield strength, and ductility. Weld dimensions include length, width, and depth of the weld. Joint configurations refer to the type of weld joint used, like butt, lap, or fillet joints. Accurate data collection is crucial for reliable calculations.
Understanding Load Requirements
Understanding load requirements is vital for accurate weld strength calculations. Determine the types of loads the weld will face. These can be static, dynamic, or cyclic loads. Static loads are constant and unchanging. Dynamic loads vary over time. Cyclic loads repeat over a cycle. Each type of load affects the weld differently. Know the magnitude and direction of these loads. This helps in selecting appropriate weld sizes and materials. Ensure your calculations consider all possible load scenarios.
Calculating Weld Strength
Calculating weld strength is crucial in ensuring the safety and durability of welded structures. Understanding the strength of welds helps in designing structures that can withstand the applied loads without failure. Let’s explore the basic formulas and step-by-step calculations used to determine weld strength.
Basic Formulas
To calculate weld strength, you need to know a few basic formulas. The main formula involves the weld’s throat area and the allowable stress. The throat area is the minimum cross-sectional area of the weld. It’s calculated based on the type of weld and its dimensions.
The formula for the throat area of a fillet weld is:
For a groove weld, the throat area is usually the weld size itself. The next key formula is:
Weld Strength = Throat Area × Allowable Stress
Allowable stress depends on the material and welding process. It’s usually provided in welding standards or specifications.
Step-by-step Calculation
Follow these steps to calculate the weld strength:
Step 1: Determine the type of weld (fillet or groove).
Step 2: Measure the weld dimensions. For a fillet weld, measure the leg size. For a groove weld, measure the weld size.
Step 3: Calculate the throat area. Use the basic formula for the weld type.
Step 4: Find the allowable stress. Refer to welding standards or material specifications.
Step 5: Calculate the weld strength. Multiply the throat area by the allowable stress.
By following these steps, you can accurately determine weld strength. This ensures the welded structure can handle the expected loads.

Credit: www.youtube.com
Using Welding Codes And Standards
Using welding codes and standards is essential for calculating weld strength. These guidelines ensure the safety and reliability of welded structures. Weld strength calculations must follow specific standards set by recognized organizations. This ensures consistency and compliance in the welding industry.
Common Standards
Several organizations provide welding standards. The American Welding Society (AWS) is one of the most well-known. They offer guidelines for different types of welding. The American Society of Mechanical Engineers (ASME) is another major organization. They focus on pressure vessels and piping. The International Organization for Standardization (ISO) also provides global standards. These organizations ensure welds meet safety and performance criteria.
Adapting Calculations To Codes
Each welding code has specific requirements. Calculations must align with these requirements. Understanding the code’s criteria is essential. For example, AWS D1.1 focuses on structural welding. It outlines specific formulas for weld strength. ASME codes may include different factors. These could be material properties or environmental conditions. Adapting calculations to each code ensures accuracy. It also guarantees compliance with industry standards.
Tools And Software
Welding is both an art and a science. For those diving into the technical side of welding, understanding how to calculate weld strength is crucial. Whether you’re working on a small DIY project or a large industrial structure, having the right tools and software can make the task much easier. In this section, we’ll explore both manual calculation tools and software solutions that can help you determine weld strength accurately and efficiently.
Manual Calculation Tools
Sometimes, the best way to learn is to do things by hand. Manual calculation tools are great for those who want to understand the fundamentals of weld strength. These tools include:
- Calculator: A basic calculator can help you perform the essential arithmetic needed for weld strength calculations.
- Weld Strength Charts: These are reference materials that provide values for various types of welds and materials.
- Formulas: Familiarize yourself with the key formulas for calculating weld strength, such as the Weld Strength Formula:
Strength = Area x Shear Strength
.
Let’s not forget, using manual tools can also be a valuable skill when technology fails you. Remember the saying, “Better safe than sorry”?
Software Solutions
In today’s digital age, software solutions have become indispensable in the welding industry. They save time, reduce errors, and offer more detailed analysis. Here are some popular software solutions:
- WeldCalc: This software allows you to input various parameters and get precise weld strength calculations.
- SolidWorks: Known for its 3D modeling capabilities, SolidWorks also has features for stress analysis and weld strength calculations.
- ANSYS: This is a powerful tool for finite element analysis, providing detailed insights into weld strength under different conditions.
Using these software solutions, you can simulate real-world conditions and ensure that your welds will hold up under stress. It’s like having a crystal ball for your welding projects!
Pro Tip: Always double-check your software results with manual calculations. It’s like having a safety net for your digital trapeze act.
Practical Tips
Calculating weld strength can feel like solving a complex puzzle. But with some practical tips, it becomes easier. Whether you’re a seasoned welder or a newbie, these tips can help you avoid common pitfalls and ensure accurate results. Let’s dive in!
Common Mistakes To Avoid
When calculating weld strength, it’s easy to make mistakes that can lead to weak joints or even safety hazards. Here are some common mistakes to watch out for:
- Ignoring Material Properties: Different materials have different strengths. Always check the properties of the materials you are using.
- Overlooking Weld Size: The size of the weld affects its strength. Ensure that the weld is neither too small nor too large for the job.
- Not Considering Load Types: Welds can be subjected to different types of loads – tensile, shear, or combined. Make sure to calculate for the specific load type.
- Skipping Safety Factors: Safety factors are crucial. They provide a margin for error. Never skip them in your calculations.
Best Practices For Accuracy
To ensure accurate calculations, follow these best practices:
- Use Reliable Formulas: Always use formulas that are widely accepted and verified in the welding industry.
- Double-Check Measurements: Accuracy in measurements is key. Double-check all your measurements before starting the calculation.
- Utilize Calculators: Many online calculators can assist in weld strength calculations. They can save time and reduce errors.
- Consult Experts: When in doubt, ask an expert. Experienced welders or engineers can provide valuable insights.
Remember, calculating weld strength is not just about numbers; it’s about ensuring the safety and integrity of your welds. So take your time, follow these tips, and you’ll be on your way to strong, reliable welds.
Have you ever miscalculated weld strength before? Share your experience in the comments below!
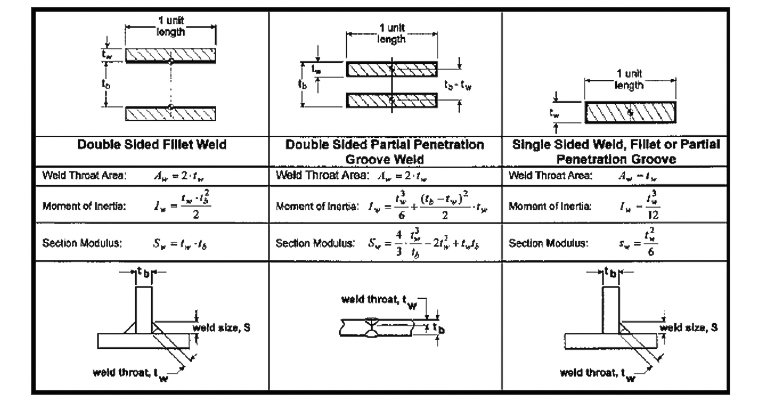
Credit: blog.red-d-arc.com
Frequently Asked Questions
How Is Weld Strength Calculated?
Weld strength is calculated using the formula: Strength = Area x Strength of Weld Material. Measure the throat thickness and weld length. Multiply by the material’s strength.
How To Check The Strength Of Welding?
To check welding strength, use visual inspection, ultrasonic testing, radiographic testing, and tensile strength tests. Ensure welds are free of cracks and defects.
What Is The Formula For Welding Calculation?
The formula for welding calculation is P = (I x V x 60) / (S x E). Here, P is power, I is current, V is voltage, S is weld speed, and E is efficiency.
What Is The Rule Of Thumb For Weld Strength?
A common rule of thumb for weld strength is to match the weld size to the thickness of the thinner material being joined. This ensures adequate strength and integrity in the weld joint. Always consult welding codes and standards for specific requirements.
Conclusion
Calculating weld strength ensures safety and reliability. Use the right formulas and methods. Understand the material’s properties. Consider factors like load type and weld size. Practice and experience improve accuracy. Review your calculations regularly. Keep learning and stay updated on industry standards.
This keeps your skills sharp. Strong welds create strong structures. This guide helps you understand the basics. Stay safe and weld confidently.