Mig welding is a popular welding method. It stands for Metal Inert Gas welding.
Many industries use it due to its efficiency and ease. But like any technique, it has its ups and downs. Understanding Mig welding’s pros and cons is essential for anyone in welding. This method offers many benefits, like faster welds and ease of learning.
Yet, it also has some drawbacks, such as the need for a clean work surface and potential safety risks. This post will explore both sides, helping you decide if Mig welding is right for your needs. Whether you are a hobbyist or a professional, knowing these details will enhance your welding projects. Let’s dive into the specifics of Mig welding’s advantages and challenges.
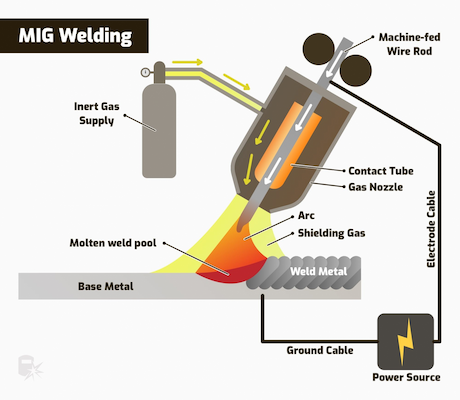
Credit: americantorchtip.com
Introduction To Mig Welding
Welcome to the world of MIG welding! If you are just starting out or looking to improve your welding skills, understanding the basics is essential. In this section, we will delve into what MIG welding is, and explore its historical roots. Ready to spark some interest? Let’s dive in!
What Is Mig Welding?
MIG welding, or Metal Inert Gas welding, is a popular welding technique that uses an electric arc to join metals. Here’s how it works: a continuous wire electrode is fed through a welding gun, creating a strong, precise weld. The process is shielded by an inert gas (often argon or a mix of gases) to protect the weld from contaminants in the air.
Why choose MIG welding? It’s a go-to method for many due to its ease of use and versatility. Whether you’re welding thin sheets of metal or thick structural components, MIG welding can handle the job. Plus, it’s faster than many other welding methods, making it perfect for both hobbyists and professionals.
Brief History
Now, let’s take a trip back in time. MIG welding was first developed during World War II. The need for quick, reliable welding techniques was at an all-time high. Engineers and scientists worked tirelessly to create a method that could keep up with the demands of the war effort.
Here’s a fun fact: the initial use of MIG welding was for welding non-ferrous metals like aluminum. It wasn’t until later that it became popular for welding steel. Over the years, advances in technology have refined the process, making it more efficient and accessible.
So, next time you strike an arc, remember you’re part of a rich history of innovation and craftsmanship. Pretty cool, right?
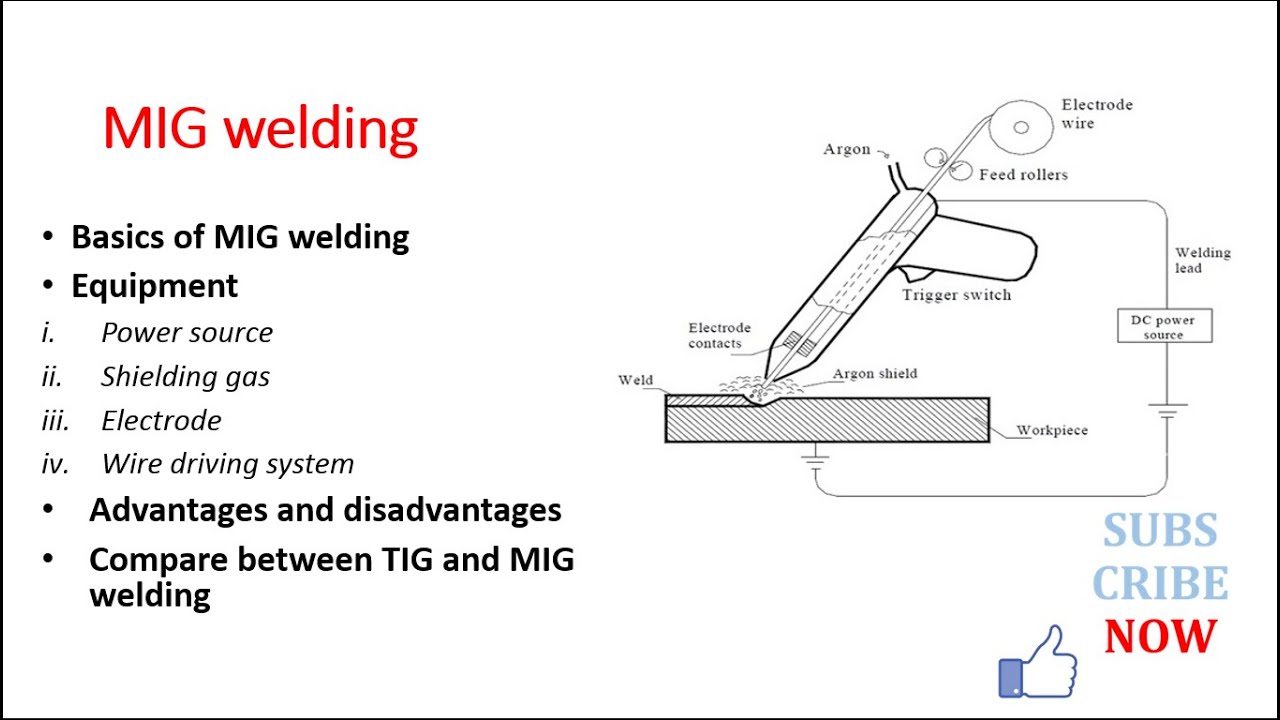
Credit: www.youtube.com
Advantages Of Mig Welding
MIG welding is a popular welding method for its many advantages. It is often chosen for its ease of use, speed, efficiency, and versatility. These benefits make it a favorite among welders, both beginners and professionals.
Ease Of Use
MIG welding is user-friendly. Even beginners can learn it quickly. The process involves using a welding gun that feeds wire automatically. This reduces the need for constant adjustments. The welder can focus on guiding the gun and maintaining a steady hand.
The automatic feed system helps maintain a consistent weld. This consistency is key for producing strong, reliable welds. The method is also less messy, with fewer sparks and less smoke compared to other welding types.
Speed And Efficiency
MIG welding is fast. The continuous wire feed speeds up the welding process. This allows for longer welds without stopping. The efficiency of this method is one reason it is used in many industries. It saves time and increases productivity.
The speed and efficiency translate into cost savings. Less time is spent on each weld, which means more work can be completed in a day. This makes MIG welding a cost-effective choice for many projects.
Versatility
MIG welding is versatile. It can weld various metals. This includes stainless steel, aluminum, and mild steel. The ability to work with different metals makes it useful in many applications.
Different thicknesses of metal can be welded with MIG welding. This flexibility allows for a wide range of projects. From thin sheets to thicker plates, MIG welding handles it all. This versatility makes it a valuable skill for any welder.
High Quality Welds
MIG welding, also known as Metal Inert Gas welding, is celebrated for producing high-quality welds. It’s a favorite among both professional welders and hobbyists. But why is it so highly regarded? Let’s delve into the specifics of consistent weld quality and reduced welding defects to understand the true benefits of MIG welding.
Consistent Weld Quality
One of the standout features of MIG welding is its ability to deliver consistent weld quality. This means that you can achieve uniform welds every time you work on a project. Why is this important? Consistency ensures that the structural integrity of the weld is maintained, which is crucial for safety and durability.
Imagine baking a cake. You want each slice to taste just as good as the last. Similarly, in welding, consistency ensures that each joint is strong and reliable.
- Ease of Use: MIG welding is relatively easy to learn and use, which makes it accessible to beginners.
- Speed: The process is faster compared to other welding methods, which can save time and increase productivity.
In my experience, once you get the hang of it, MIG welding can feel almost like second nature. It’s like riding a bike; you never really forget how to do it.
Reduced Welding Defects
Another significant advantage of MIG welding is the reduction of welding defects. Defects in welding can lead to weak spots, which can compromise the entire project. With MIG welding, the chances of such defects are minimized.
Here’s a quick comparison of common welding defects and how MIG welding addresses them:
Defect | MIG Welding Solution |
---|---|
Porosity | Inert gas shields the weld, reducing contamination. |
Undercutting | Better control over the welding process minimizes this risk. |
Cracks | Consistent heat distribution prevents cracks. |
Think of welding defects as potholes on a road. They can make the journey bumpy and unsafe. MIG welding smooths out these potholes, ensuring a smoother and safer path.
So, if you’re aiming for high-quality welds, MIG welding is a reliable choice. It offers consistent results and reduces the likelihood of defects, making your projects sturdier and more professional-looking. Ready to give it a try?

Credit: primeweld.com
Cost-effectiveness
MIG welding, or Metal Inert Gas welding, is a popular welding process. One of its biggest advantages is cost-effectiveness. MIG welding can save both time and money. This makes it a preferred choice for many projects. Let’s explore why it’s cost-effective.
Lower Labor Costs
MIG welding is simple to learn and perform. This reduces training costs for workers. The welding process is also fast. Welders can complete jobs quickly. This lowers labor costs significantly.
The ease of use means fewer mistakes. Fewer mistakes mean less rework. Rework can be costly and time-consuming. By reducing rework, MIG welding saves money.
Minimal Post-weld Cleanup
MIG welding produces clean welds with little spatter. This means less time spent on cleaning after welding. Minimal cleanup translates to lower labor costs.
Clean welds also mean fewer defects. Fewer defects lead to higher quality products. High-quality products reduce costs associated with returns or repairs.
The reduced need for cleaning supplies is another cost-saving factor. Less spatter means less use of grinding tools and cleaning agents. This further reduces overall expenses.
Safety Considerations
Using MIG welding involves several safety considerations. Proper eye protection is essential to prevent damage from the bright welding arc. Wearing fire-resistant clothing and gloves can protect the skin from burns and sparks.
When performing MIG welding, safety should be a top priority. Ensuring proper safety measures can protect you from serious injuries. Let’s dive into the essential safety considerations.Protective Gear Requirements
Wearing the right protective gear is crucial. Always wear a welding helmet to shield your eyes and face from sparks and bright light. Gloves are necessary to protect your hands from burns and hot metal. A flame-resistant jacket or apron can protect your upper body. Ensure you also wear safety glasses under the helmet for extra eye protection. Use ear protection to guard against loud noises. Don’t forget sturdy, closed-toe shoes to protect your feet from falling objects and hot sparks.Common Safety Hazards
Be aware of common safety hazards. Electric shock is a risk if you touch live electrical parts. Always check your equipment and cables for damage before starting. Exposure to toxic fumes is another hazard. Ensure proper ventilation in your workspace. Use a fume extractor if necessary. Fire hazards are also present. Keep flammable materials away from the welding area. Always have a fire extinguisher nearby. Burns from hot metal and sparks are common. Wear your protective gear at all times. Be mindful of your surroundings to avoid tripping over cables and tools. By following these safety considerations, you can ensure a safer welding experience. “`Disadvantages Of Mig Welding
MIG welding, while popular, comes with its own set of challenges. Understanding these disadvantages can help you decide if it’s the right method for your welding needs.
Equipment Costs
Investing in MIG welding equipment can be expensive. The machines and accessories are often pricier compared to other welding types. You need a welding machine, gas cylinders, and consumables like wire. These costs can add up quickly. For hobbyists or small shops, this can be a significant investment.
Sensitivity To Contaminants
MIG welding is sensitive to contaminants. Dirt, rust, and oil on the metal can cause problems. Clean surfaces are crucial for a strong weld. Contaminants can lead to weak welds or defects. This means extra time spent on surface preparation. Not ideal for projects with tight deadlines.
Limitations In Outdoor Use
MIG welding, also known as Gas Metal Arc Welding (GMAW), is quite popular due to its versatility and ease of use. However, like any other welding method, it has its limitations. One significant drawback is its performance in outdoor settings. Let’s dive into why MIG welding might not be the best choice for outdoor projects.
Wind Sensitivity
One of the primary concerns with MIG welding outdoors is wind sensitivity. The process relies on a shielding gas to protect the weld pool from contaminants. Even a slight breeze can blow this gas away, leading to oxidation and a weak weld.
I once tried to weld a fence on a windy day. Let me tell you, it was a disaster! The wind kept disrupting the shielding gas, causing the welds to be full of porosity. It was a classic case of “live and learn”.
Shielding Gas Issues
Another limitation is related to the shielding gas itself. When you’re welding outdoors, maintaining a consistent gas flow can be challenging. This inconsistency can result in poor weld quality and even safety concerns.
Imagine trying to make a perfect cake while someone keeps turning the oven off and on. Frustrating, right? The same goes for MIG welding without stable shielding gas coverage.
Here’s a quick summary:
- Wind can disrupt the shielding gas.
- Inconsistent gas flow leads to poor weld quality.
- Outdoor conditions can make it hard to control the welding environment.
So, while MIG welding is fantastic in controlled environments, you might want to think twice before taking your setup outside on a blustery day. Stay tuned for more tips and tricks to make your welding projects a success, no matter where you are!
Comparing Mig Welding To Other Methods
MIG welding is popular for many welding projects. It offers several advantages compared to other methods. Understanding these differences helps you choose the best technique for your needs.
Mig Vs. Tig Welding
MIG welding is faster than TIG welding. It uses a continuous wire feed. This makes it ideal for large projects. TIG welding, on the other hand, uses a tungsten electrode. This process is slower but provides more precise welds. TIG welding is often used for delicate and detailed work. MIG welding is easier to learn. It is more forgiving for beginners. TIG welding requires more skill and practice.
Mig Vs. Stick Welding
MIG welding is more efficient than stick welding. The continuous wire feed reduces downtime. Stick welding uses a consumable electrode. This means frequent stops to replace the stick. MIG welding produces cleaner welds. It generates less spatter. Stick welding can handle dirtier surfaces better. It is more versatile for outdoor work. MIG welding needs a shielding gas. This makes it less suitable for windy conditions.
Frequently Asked Questions
What Is A Disadvantage Of Mig Welding?
A disadvantage of MIG welding is its sensitivity to wind and drafts. This can lead to poor weld quality.
What Is The Problem With Mig Welder?
MIG welders can face issues like poor wire feed, inconsistent arc, or excessive spatter. These problems often arise from incorrect settings, dirty nozzles, or worn-out parts. Regular maintenance and proper setup can help avoid these common issues.
What Is The Biggest Mistake In Mig Welding?
The biggest mistake in MIG welding is improper machine setup. This includes incorrect voltage, wire feed speed, and gas flow.
Should I Buy A Mig Or Stick Welder?
Choose a MIG welder for ease of use and cleaner welds, ideal for beginners. Pick a stick welder for heavy-duty, outdoor, and rusty metal tasks. Assess your project’s needs to decide.
Conclusion
Mig welding offers both advantages and disadvantages. It’s efficient and easy to learn. Yet, it may struggle with thick materials. Its equipment can also be expensive. Always weigh these pros and cons. Choose the right welding method for your project needs.
Happy welding!