If you’ve ever walked past massive pipelines, towering bridges, or seen a ship being built, you’ve already witnessed the incredible strength of Submerged Arc Welding (SAW). When I first explored welding techniques, SAW quickly stood out to me because of its efficiency and the unique way it produces flawless welds hidden beneath a protective layer of flux.
Like any process, SAW has its strengths and limitations. Whether you’re a professional welder, a manufacturing engineer, or someone curious about industrial welding, understanding the advantages and disadvantages of SAW will help you decide if it’s the right choice for your project. Let’s break it down together.
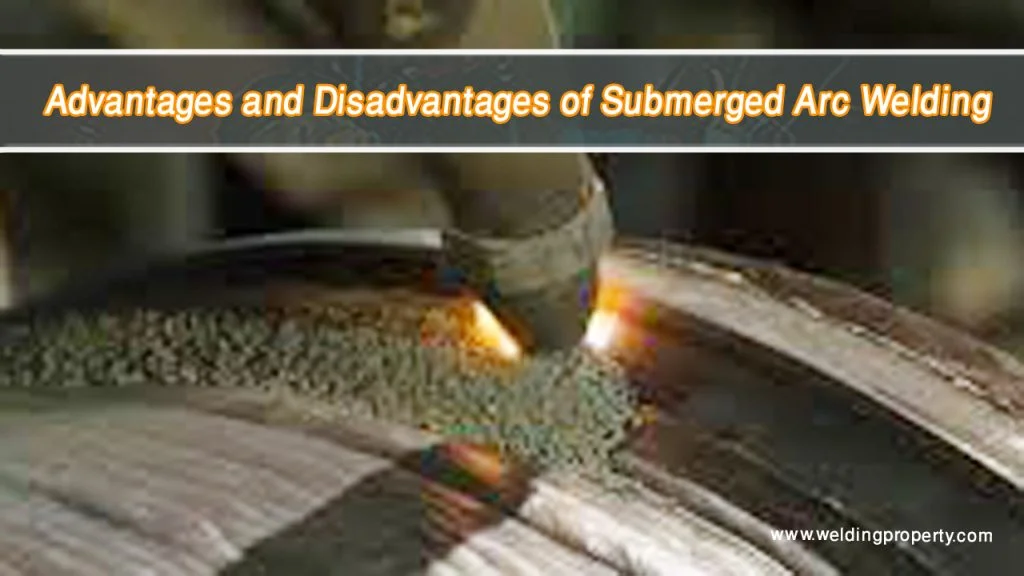
What is Submerged Arc Welding?
Before diving into its pros and cons, let’s start with a quick overview. Submerged Arc Welding is an industrial welding process where a consumable wire electrode creates an arc with the base metal. The arc, weld pool, and molten metal are submerged under a thick blanket of granular flux, which shields the process from atmospheric contamination.
This setup ensures clean, high-quality welds and makes SAW one of the most reliable choices for large-scale fabrication. However, it’s not a one-size-fits-all solution, so let’s explore its advantages and disadvantages in detail.
Advantages of Submerged Arc Welding
High Efficiency and Productivity
One of the standout features of SAW is its speed. Since it uses a continuous wire electrode and operates with automated or semi-automated equipment, the process is highly efficient. This is especially valuable for industries that need to complete large welding jobs quickly, like pipeline construction or shipbuilding.
With high deposition rates, SAW lays down a large volume of filler material in a short time, significantly reducing project timelines.
Superior Weld Quality
The protective flux plays a big role in ensuring the weld is clean and free from defects. It prevents contamination from air, stabilizes the arc, and even improves the mechanical properties of the weld. This results in strong, consistent, and visually appealing welds.
Because of its slag cover, the weld is also smooth, which minimizes the need for post-weld finishing like grinding or sanding.
Reduced Welding Fumes and UV Radiation
Compared to open-arc welding processes like MIG or TIG, SAW is much safer for operators. The submerged arc keeps sparks, fumes, and ultraviolet radiation contained under the flux. This creates a cleaner and safer working environment, reducing exposure to harmful elements.
Deep Penetration for Thick Materials
SAW excels at welding thick materials, such as steel plates and heavy-duty pipes. It produces deep weld penetration, ensuring strong and reliable joints that can withstand high stresses. This makes it the preferred choice for heavy industrial applications.
Minimal Skill Requirement
With automated or semi-automated equipment, SAW reduces the dependency on operator skill. While knowledge and training are still required, the process is relatively simple compared to manual welding techniques.
Cost Efficiency for Large Projects
Although the initial setup for SAW can be costly, it proves cost-effective in the long run for large-scale projects. Its high efficiency, reduced material waste, and minimal need for post-weld cleanup contribute to significant savings.
Versatility in Applications
SAW is incredibly versatile. It’s used in a wide range of industries, including:
- Shipbuilding
- Oil and gas pipelines
- Heavy equipment manufacturing
- Bridge construction
- Pressure vessel fabrication
Disadvantages of Submerged Arc Welding
Despite its many benefits, SAW isn’t without its drawbacks. Here are some limitations you should consider:
Limited to Flat or Horizontal Positions
SAW works best in flat or horizontal positions due to the way the granular flux and molten weld pool behave during the process. It’s not suitable for vertical or overhead welding, which can be a major drawback for certain applications.
High Initial Setup Costs
The equipment required for SAW—including the welding machine, flux recovery system, and automated components—can be expensive. This makes it less accessible for smaller workshops or low-budget projects.
Not Suitable for Thin Materials
SAW is designed for welding thick materials. When used on thin materials, it can cause excessive heat input and distortion. For thinner metals, other welding methods like TIG or MIG are more appropriate.
Flux Handling and Storage
The granular flux used in SAW requires careful handling and storage. Any contamination from moisture or foreign particles can compromise weld quality. Operators must also manage flux recovery and recycling systems, which can add complexity to the process.
Limited to Ferrous Metals
SAW is primarily used for ferrous metals like steel and stainless steel. It’s not suitable for non-ferrous metals such as aluminum, which restricts its versatility in certain industries.
Requires Large, Controlled Workspaces
Because of its size and the equipment involved, SAW is best suited for controlled environments like factories or workshops. It’s not ideal for fieldwork or confined spaces, where portability is essential.
Slag Removal and Cleaning
While the slag layer protects the weld during cooling, it must be removed after the welding process. Although this is less labor-intensive compared to stick welding, it still adds an extra step to the workflow.
A Quick Comparison of Advantages and Disadvantages
Advantages | Disadvantages |
---|---|
High efficiency and productivity | Limited to flat/horizontal positions |
Superior weld quality | High initial setup costs |
Reduced welding fumes and UV | Not suitable for thin materials |
Deep penetration for thick metals | Flux handling challenges |
Minimal skill requirement | Limited to ferrous metals |
Cost-effective for large projects | Requires large, controlled spaces |
Versatile in heavy industries | Slag removal needed |
When Should You Use Submerged Arc Welding?
SAW is a great choice if you’re working on a large-scale industrial project that involves thick materials and requires high-quality welds. For instance:
- Pipeline Construction: SAW’s deep penetration and efficiency are perfect for long pipeline joints.
- Shipbuilding: The smooth and strong welds produced by SAW are ideal for constructing ship hulls.
- Heavy Equipment Manufacturing: When durability is a priority, SAW delivers the strength needed for heavy machinery.
If your project involves thin materials, non-ferrous metals, or out-of-position welding, you’ll need to explore other welding techniques.
FAQs
Is Submerged Arc Welding safe for operators?
Yes, SAW is safer than many other welding methods because the flux layer contains fumes, sparks, and UV radiation.
Can SAW be used on aluminum?
No, SAW is primarily used for ferrous metals like steel and stainless steel. It’s not suitable for non-ferrous metals like aluminum.
What is the biggest advantage of SAW?
The biggest advantage of SAW is its efficiency. It produces high-quality welds quickly, making it ideal for large-scale projects.
Why is SAW limited to flat or horizontal welding?
The granular flux and molten weld pool rely on gravity to stay in place, which restricts SAW to flat or horizontal positions.
Does SAW require post-weld cleaning?
Yes, the slag layer formed during the process must be removed after welding to reveal the finished weld.
Conclusion
Submerged Arc Welding is a powerhouse in the world of industrial welding. Its ability to deliver high-quality, efficient welds on thick materials makes it a go-to choice for heavy-duty applications like shipbuilding, pipeline construction, and structural fabrication.
That said, it’s important to weigh its advantages and disadvantages carefully. While SAW shines in controlled environments with large, flat workpieces, its limitations make it less suitable for smaller or more intricate projects.
In my experience, SAW is an exceptional process when used in the right context. If you’re tackling a large-scale project where speed and strength are critical, SAW can save you time, money, and effort while delivering top-notch results.
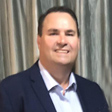
Endow Russel the owner chief editor of giftendow.com . I am a mechanical engineer and assign to an local firm with much experience in welding and industrial equipment.