Flux core welding is a versatile and efficient welding method. It’s popular for its ease and effectiveness in various settings.
Whether you’re a beginner or an experienced welder, knowing the best tips for flux core welding can improve your results. This guide will help you understand key techniques and practices. From equipment setup to weld quality, these tips cover essential aspects of flux core welding.
Good practices ensure strong, clean welds and enhance safety. By following these tips, you can tackle any welding project with confidence. Let’s explore these valuable insights and make your welding experience smoother and more successful.
Introduction To Flux Core Welding
Flux core welding offers strong joints and is great for outdoor use. Clean the metal surface well. Adjust the wire feed speed to avoid splatter.
Flux core welding is a popular method among welders. It combines efficiency with versatility. Many professionals and hobbyists choose this technique. It works well in different environments, including outdoors. Flux core welding uses a special wire. This wire has a flux coating inside. The flux helps create a shield around the weld. This shield protects the weld from contaminants. It is similar to MIG welding, but the flux makes it unique.Basics Of Flux Core Welding
Flux core welding is simple to learn. It uses an electrode wire that feeds through the welding gun. The wire melts and creates the weld joint. The flux inside the wire provides protection. This reduces the need for an external shielding gas. This method is suitable for thick materials. It can handle rusty or dirty surfaces. The equipment is portable. This makes it ideal for fieldwork. Beginners can start with basic settings. More experienced welders can fine-tune for better results.Applications And Benefits
Flux core welding has many applications. It is used in construction, shipbuilding, and repair work. It is also common in heavy equipment manufacturing. It works well for outdoor projects. The flux provides protection against wind and drafts. The benefits are numerous. It has high deposition rates. This means faster welding. It is efficient and cost-effective. The process is forgiving on less clean surfaces. This reduces preparation time. It produces strong and durable welds. Flux core welding is versatile. It can be used in various positions. This includes flat, vertical, and overhead. It is a reliable method. Many industries trust it for critical projects. The equipment is user-friendly. It is easy to set up and operate. Beginners can learn quickly. Professionals can achieve high-quality results. Flux core welding is a valuable skill. It offers many advantages for different applications. “`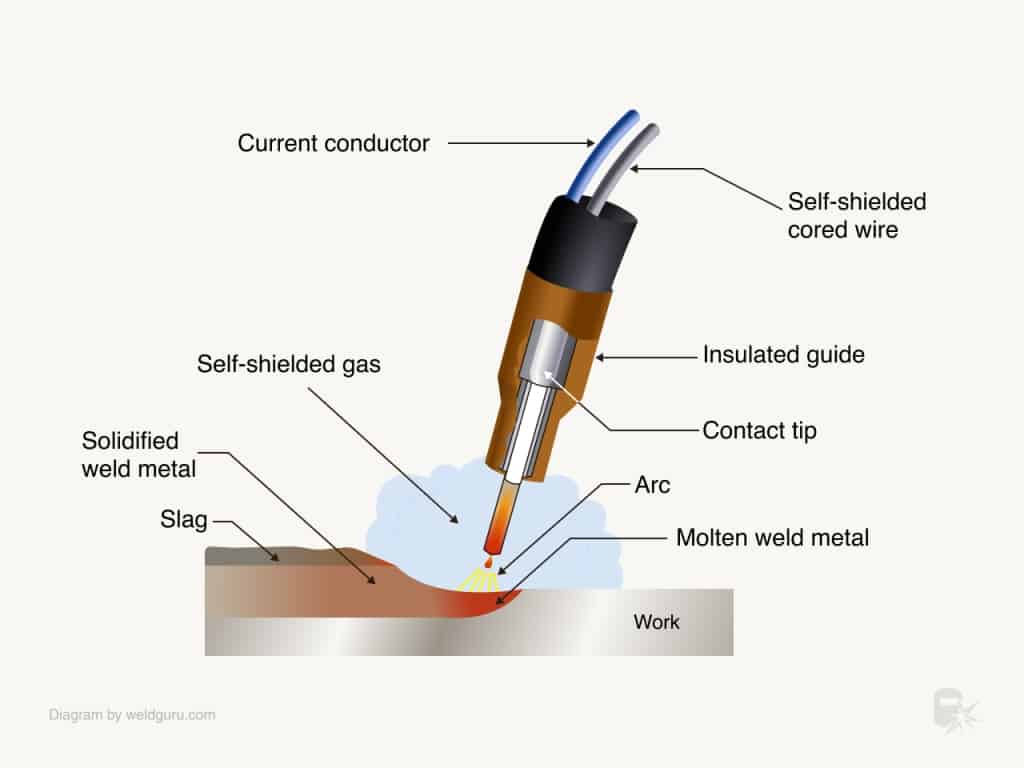
Credit: weldguru.com
Essential Equipment
Essential equipment is key for successful flux core welding. Having the right tools makes the job easier and safer. Let’s explore the necessary gear for effective welding.
Choosing The Right Welder
Start with selecting a quality flux core welder. Look for a welder with adjustable settings. This flexibility allows for better control over your welds. Ensure the welder has a good duty cycle. A higher duty cycle means longer welding times without overheating.
Portability is another factor. A lightweight welder is easier to move around. Consider one with a built-in handle. This feature adds convenience for transport. Check for compatibility with the power supply. Some welders work on standard household outlets, while others need a higher voltage.
Selecting The Appropriate Wire
Choosing the correct wire is crucial. Flux core welding uses self-shielded wire. This wire does not need external gas. Ensure the wire size matches your welder’s specifications. Thicker materials need larger diameter wires. For thin materials, smaller wires work best.
Pay attention to the wire’s type. Common types include E71T-11 and E71T-GS. E71T-11 is versatile and works well for most projects. E71T-GS is good for thin materials. Store the wire in a dry place. Moisture can cause issues with the weld quality.
Safety Precautions
When it comes to flux core welding, safety is of utmost importance. It’s not just about getting the job done, but doing so without putting yourself or others at risk. Let’s dive into some essential safety precautions to keep in mind. Trust me, taking a few extra steps now can save you from a lot of trouble later.
Personal Protective Equipment
First and foremost, you need to gear up with the right Personal Protective Equipment (PPE). This is non-negotiable.
- Helmet: Always wear a welding helmet with a proper shade lens. It protects your eyes from the bright arc light.
- Gloves: Use heavy-duty welding gloves. They shield your hands from hot metal and sparks.
- Clothing: Opt for flame-resistant clothing. Synthetic fabrics can melt and cause burns.
- Boots: Wear steel-toed boots. They offer protection from falling objects and molten metal.
Once, a friend of mine thought he could skip the gloves for a quick weld. He ended up with a nasty burn. Lesson learned: don’t take shortcuts with PPE.
Safe Working Environment
Creating a Safe Working Environment is just as critical. Here’s how you can ensure it:
- Ventilation: Ensure your workspace is well-ventilated. Welding fumes are toxic, and you don’t want to be breathing them in.
- Fire Safety: Keep a fire extinguisher nearby. Sparks can fly, and it’s better to be safe than sorry.
- Clear Area: Remove any flammable materials from your work area. A clean space is a safe space.
- Electrical Safety: Make sure your equipment is in good condition. Frayed wires and faulty connections are a recipe for disaster.
One time, I nearly tripped over some clutter in my garage while welding. It made me realize the importance of a tidy workspace. You don’t want to learn this the hard way!
By following these safety precautions, you’re not just protecting yourself but also ensuring a smoother and more efficient welding process. Remember, safety first!
Setting Up For Success
Getting started with flux core welding can be a bit daunting, especially if you’re new to it. However, with the right setup, you can achieve great results. In this section, we’ll cover the essentials to set you up for success. So, let’s dive in!
Preparing The Workpiece
Before you even think about striking an arc, you need to prepare your workpiece. Think of it like painting a wall; you wouldn’t just slap paint on without prepping the surface, would you?
- Clean the Metal: Remove any rust, dirt, or oil. A clean surface ensures better weld quality.
- Fit-Up: Make sure your pieces fit together snugly. Gaps can lead to weak welds.
- Clamp It Down: Secure your workpiece to prevent movement during welding.
Remember, a well-prepped workpiece is half the battle won.
Adjusting Machine Settings
Now that your workpiece is ready, it’s time to fine-tune your welding machine. This can make or break your welding experience. Here’s how to get it right:
- Voltage: Set the voltage according to the thickness of the metal. Thicker metals need higher voltage.
- Wire Feed Speed: Adjust the speed so that you get a steady, crackle-free arc.
- Polarity: For flux core welding, use a negative electrode (DCEN) for most applications.
Pro tip: Check the manufacturer’s settings guide on your machine. It’s like having a cheat sheet!
By carefully preparing your workpiece and adjusting your machine settings, you’re setting yourself up for welding success. Remember, even the best welders started with the basics. Take your time, practice, and soon, you’ll be welding like a pro!
Proper Welding Techniques
Welding can be a bit tricky, but with the right techniques, you can make strong, clean welds every time. Let’s dive into some essential tips on maintaining the proper welding techniques. These tips will help you achieve the best results, whether you’re a beginner or looking to improve your skills.
Maintaining Correct Angle
One of the most important aspects of flux core welding is keeping the right angle. Why is this crucial? Because the angle affects the weld’s penetration and appearance.
Here are some key points to remember:
- Travel Angle: Hold the gun at a 10-15 degree angle from the vertical position. This helps the weld pool move smoothly and evenly.
- Work Angle: Keep the gun perpendicular to the workpiece. This ensures even heat distribution and prevents undercutting.
Think of it like driving a car. Keep your hands steady on the wheel, and you’ll stay on the road!
Controlling Travel Speed
Imagine trying to paint a wall. If you move too fast, you’ll miss spots. If you move too slow, the paint will drip. Welding is similar. Controlling your travel speed is key to a clean weld.
Here’s a simple guide to get it right:
- Consistent Speed: Move at a steady pace. Too fast, and the weld will be thin and weak. Too slow, and you’ll get too much heat and spatter.
- Watch the Puddle: Keep an eye on the molten weld pool. It should be smooth and consistent. If it starts to look uneven, adjust your speed.
- Practice Makes Perfect: Like learning to ride a bike, the more you practice, the better you’ll get. Try different speeds on scrap pieces to find your sweet spot.
By mastering your travel speed, you’ll make strong, neat welds that look professional.
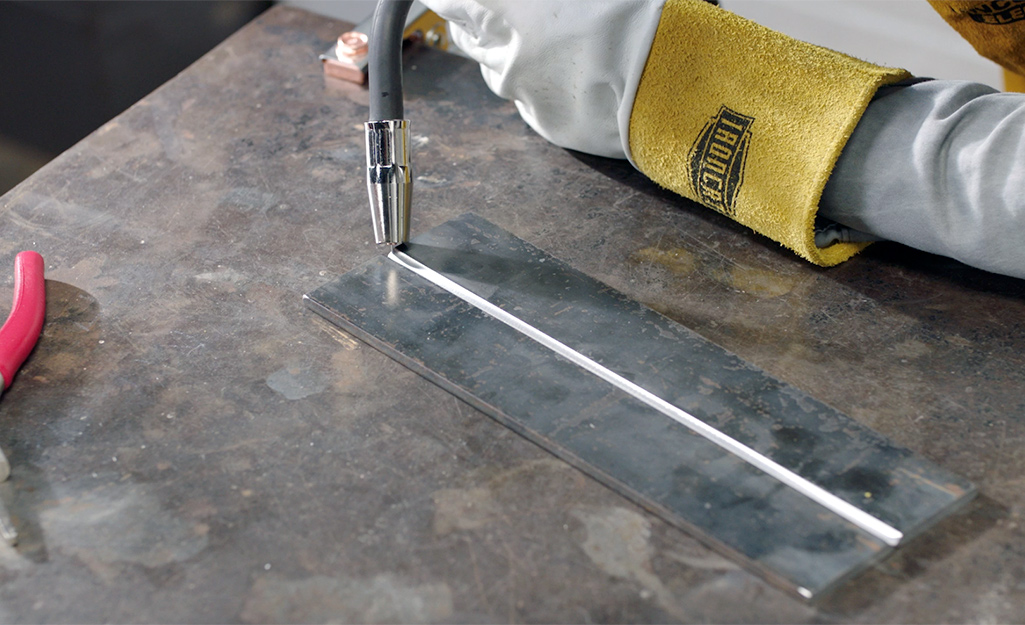
Credit: www.homedepot.com
Dealing With Common Issues
Dealing with common issues in flux core welding can be challenging. Problems like porosity and slag inclusion often arise, affecting the weld quality. Understanding how to prevent these issues is crucial. Here are some tips to help you deal with them effectively.
Preventing Porosity
Porosity occurs due to trapped gas in the weld. This weakens the weld and makes it look bad. To prevent porosity, clean the metal surface well. Remove dirt, rust, and paint before welding. Use the correct wire for the material you’re welding. Ensure proper gas flow if using dual-shield flux core wire. Check for leaks in the gas hose.
Keep the welding area free of drafts. Wind can blow away the shielding gas. This causes porosity. Maintain the right distance between the nozzle and the workpiece. Too close or too far can lead to porosity. Control your welding speed. Too fast or too slow can trap gas in the weld.
Handling Slag Inclusion
Slag inclusion happens when slag gets trapped in the weld. This weakens the weld and makes it look poor. To avoid this, clean the slag between passes. Use a chipping hammer and wire brush. Ensure the weld area is clean before starting a new pass.
Adjust your welding technique. Maintain the right angle and speed. This helps the slag to float to the surface. Use the correct amperage settings. Too low or too high can cause slag inclusion. Follow the manufacturer’s guidelines for your equipment. Proper setup and maintenance of your welding machine are essential.
Post-welding Procedures
Post-welding procedures are crucial in flux core welding. They ensure the quality and longevity of the weld. These steps help identify any defects and provide a clean, polished finish. Let’s explore essential post-welding procedures for flux core welding.
Cleaning And Inspecting Welds
First, remove slag from the weld. Use a wire brush or chipping hammer. This step is vital to see the weld clearly. After cleaning, inspect the weld for defects. Look for cracks, pores, or weak spots. Any flaw can compromise the weld’s strength. Address issues immediately to avoid future problems.
Applying Finishing Touches
After inspection, apply finishing touches. Smooth any rough edges with a grinder. This step ensures a neat and professional appearance. If necessary, apply a protective coating. This helps prevent rust and corrosion. A well-finished weld not only looks good but also lasts longer.
Advanced Tips And Tricks
Flux core welding can be tricky. But once you’ve got the basics down, it’s time to take your skills to the next level. Whether you’re welding for a hobby or a career, these advanced tips and tricks will help you master even the most challenging tasks. Let’s dive into some expert advice to elevate your flux core welding game!
Mastering Vertical And Overhead Welding
Welding in different positions can be a real pain. But don’t worry, here are some tips to help you nail it:
- Use a Steady Hand: Keep your hand steady and your movements smooth. This helps to prevent any unwanted splatter.
- Control the Heat: Too much heat can cause the weld to drip. Use a lower amperage to control the heat and keep the weld in place.
- Practice Makes Perfect: Practice on scrap metal first. This will help you get a feel for the different angles and positions.
Remember, patience is key. Don’t rush, and take your time to get it right.
Improving Efficiency And Precision
Want to weld faster without losing quality? Here are some tricks to help you improve efficiency and precision:
- Set Up Properly: Organize your workspace before starting. Keep all your tools within reach. This saves time and prevents distractions.
- Use the Right Wire: Make sure you’re using the correct wire for the job. Different wires work better with different metals and thicknesses.
- Maintain Your Equipment: Regular maintenance of your welding machine and tools ensures they perform at their best.
- Watch Your Speed: Welding too fast can cause weak joints, while going too slow can lead to overheating. Find a balance that works for you.
By following these tips, you’ll be able to weld more efficiently and with greater precision.
Flux core welding can be challenging, but with these advanced tips and tricks, you’ll be well on your way to mastering even the toughest welding jobs. Keep practicing, stay patient, and you’ll see improvements in no time!

Credit: www.youtube.com
Frequently Asked Questions
How To Reduce Spatter When Flux Core Welding?
To reduce spatter while flux core welding, use proper voltage and wire feed settings. Maintain a steady hand and correct angle. Keep the nozzle clean and use anti-spatter spray. Ensure the workpiece is free from contaminants.
Do You Push Or Pull When Flux Core Welding?
Push the weld when flux core welding. This technique ensures better penetration and cleaner welds.
Why Are My Flux Core Welds So Bad?
Your flux core welds might be bad due to incorrect settings, poor technique, or contaminated materials. Ensure proper wire speed, voltage, and clean surfaces. Practice consistently to improve your skills.
What Angle Should A Flux Core Welding Gun Be?
Hold the flux core welding gun at a 10-15 degree angle. Ensure the tip points towards the direction of travel.
Conclusion
Applying these flux core welding tips can significantly improve your welding skills. Practice consistently to achieve cleaner, stronger welds. Use the right equipment and maintain it well. Always prioritize safety by wearing proper protective gear. Understand your material and adjust your settings accordingly.
Remember, patience and practice are key. Stay focused and follow these tips to see positive results in your welding projects. Happy welding!