Spot welds are common in metalworking and manufacturing. They join pieces of metal together.
Finding these welds can be tricky but important for quality checks and repairs. Spot welds are often small and hard to see. Knowing where to find them ensures the strength and safety of the metal structure. This guide will help you find spot welds effectively.
Whether you are a professional or a DIY enthusiast, mastering this skill is valuable. You will learn practical tips and techniques to locate spot welds quickly. This knowledge can save time and improve your work’s quality. Ready to get started? Let’s dive into the best ways to find spot welds.
Introduction To Spot Welds
Spot welds are the unsung heroes of many industries. From car factories to home appliances, these small but mighty welds hold things together. But what exactly are they, and why are they so important? Let’s dive into the world of spot welds and discover their secrets.
What Are Spot Welds?
Spot welds are tiny welds that join two pieces of metal. Imagine two metal sheets. Now, think about pressing them together and applying a lot of heat in a small spot. This is what creates a spot weld. The heat melts the metal, and when it cools down, the two pieces are fused together in that spot. It’s like giving the metal sheets a very strong glue dot.
Importance In Manufacturing
Why are spot welds so important? Well, they are everywhere. In the automotive industry, for example, cars have thousands of spot welds holding them together. This makes the car body strong and safe. In home appliances like refrigerators and washing machines, spot welds ensure the parts stay together and work correctly.
Here are a few reasons why spot welds are essential:
- Strength: Spot welds provide strong joints without using bolts or screws.
- Speed: They are quick to make, which speeds up manufacturing.
- Cost-effective: Spot welding is less expensive than other types of welding.
- Automation: Machines can easily make spot welds, which reduces labor costs.
Spot welds are like the quiet workers in a factory. You may not see them, but they do an important job. They hold everything together, ensuring the final product is reliable and strong.
Common Methods For Finding Spot Welds
Finding spot welds is essential for many industries, especially in automotive and metalworking. Identifying these welds helps with quality control, repair, and maintenance. There are several common methods to locate spot welds. These methods are easy to use and require minimal tools.
Visual Inspection
Visual inspection is the simplest way to find spot welds. Look for small, round marks on the metal surface. These marks are usually slightly raised or indented. Spot welds often appear in a regular pattern. Use a flashlight to see better in low-light conditions. The welds may have discoloration or heat-affected zones around them.
Tactile Methods
Tactile methods involve using touch to find spot welds. Run your fingers over the metal surface. Feel for small bumps or indentations. These are often the weld spots. Wearing gloves can help protect your hands. Use a smooth cloth to glide over the surface. This can help you feel the welds better.
Advanced Techniques
Spot welds can be challenging to find with traditional methods. Advanced techniques offer more precision and efficiency. These methods use modern technology to detect hidden welds. Let’s explore two popular advanced techniques: Ultrasonic Testing and Thermography.
Ultrasonic Testing
Ultrasonic Testing uses high-frequency sound waves. These waves penetrate the materials and reflect back. The reflections show the locations of spot welds. This method is non-destructive. It does not damage the material. Ultrasonic Testing is accurate and reliable. It is widely used in the automotive and aerospace industries.
Thermography
Thermography uses infrared cameras. These cameras detect heat patterns on the surface. Spot welds create unique heat signatures. Thermography captures these signatures. It is a fast and efficient method. This technique is also non-destructive. It helps in quality control and inspection. Thermography is useful in various industries.

Credit: www.collisionblast.com
Using X-ray Inspection
When it comes to identifying spot welds, using X-Ray Inspection is one of the most effective methods. This advanced technique allows you to see beneath the surface, providing a detailed view of the welds. But how exactly does this work, and is it the right choice for you? Let’s dive into the benefits and limitations of using X-Ray Inspection for finding spot welds.
Benefits Of X-ray Inspection
X-Ray Inspection offers several advantages that make it a popular choice for spot weld detection.
- High Accuracy: X-Ray Inspection can detect even the smallest of welds with pinpoint precision. This means fewer errors and higher quality checks.
- Non-Destructive: One of the biggest perks is that it’s non-destructive. You don’t have to take apart your workpiece to check the welds.
- Detailed Imaging: X-rays provide detailed images of the internal structure. This helps in assessing the weld quality and identifying any defects.
- Versatility: This method is versatile and can be used on a wide range of materials, from metals to plastics.
Limitations To Consider
While X-Ray Inspection is highly effective, it does come with its own set of limitations.
Limitation | Explanation |
---|---|
Cost | X-Ray machines and the process itself can be expensive. |
Safety | Handling X-rays requires strict safety protocols to protect operators from radiation. |
Technical Expertise | Requires skilled technicians to operate the machines and interpret the results. |
So, there you have it! X-Ray Inspection can be a powerful tool for finding spot welds, but it’s essential to weigh the benefits against the limitations. Whether you decide to use it or explore other methods, knowing your options is the first step toward making an informed decision.
Role Of Magnetic Particle Inspection
Finding spot welds can be tricky business. They hide in plain sight, essential but often invisible. This is where Magnetic Particle Inspection (MPI) comes in. It’s like having a detective who can see what the naked eye cannot. MPI helps you find these welds with precision, making your job easier and more efficient.
How It Works
So, how does this magical process work? Think of it like a magnet and iron filings experiment from school. Here’s a simple breakdown:
- A magnetic field is applied to the metal surface.
- Iron particles are sprinkled over the area.
- These particles gather around any defects or discontinuities, including spot welds.
Imagine shaking a blanket to see the hidden treasures underneath. The magnetic field acts like the blanket, and the iron particles reveal what’s hidden. Simple, right?
Applications In Spot Welding
Magnetic Particle Inspection isn’t just a cool science trick. It’s incredibly useful in real-world applications, especially in spot welding. Here’s how:
- Quality Control: Ensures welds are strong and defect-free.
- Safety Checks: Detects weak spots that could lead to failures.
- Maintenance: Regular inspections keep machinery running smoothly.
Think of MPI as the watchdog of the welding world. It keeps everything in check, ensuring that your welds are up to standard and safe. Plus, it’s quick and cost-effective, saving you time and money.
Have you ever tried finding a needle in a haystack? That’s what spotting welds can feel like without the right tools. But with Magnetic Particle Inspection, it’s like having a magnet that pulls that needle right out for you. Handy, isn’t it?
In conclusion, if you’re looking for the best way to find spot welds, give Magnetic Particle Inspection a try. It’s reliable, efficient, and, most importantly, it works. Happy welding!
Implementing Eddy Current Testing
Implementing Eddy Current Testing is an effective way to find spot welds. This non-destructive method offers accurate results without damaging the material. It is ideal for various industries, including automotive and aerospace. The process involves using electromagnetic induction to detect flaws and measure conductivity. Understanding the principles and real-world applications can help optimize its use.
Principles Of Eddy Current
Eddy Current Testing uses electromagnetic fields to inspect materials. A coil carrying an alternating current creates a magnetic field. When this field interacts with a conductive material, it induces eddy currents. These currents flow in circular paths within the material. Disruptions in the flow indicate flaws or changes in material properties.
The equipment includes a probe, an eddy current instrument, and software. The probe sends and receives signals, which the instrument analyzes. Any anomalies appear as changes in the signal. This helps identify spot welds and other defects. Eddy Current Testing is sensitive to small cracks and surface defects. It is also fast and efficient, making it suitable for high-volume inspections.
Case Studies
Several industries have successfully implemented Eddy Current Testing. In the automotive sector, manufacturers use it to inspect spot welds on car bodies. This ensures the welds are strong and reliable, improving vehicle safety.
In the aerospace industry, Eddy Current Testing is used to check aircraft components. Detecting flaws early can prevent potential failures and extend the lifespan of the parts. One notable case involved an airline discovering small cracks in wing panels. Eddy Current Testing identified these cracks before they became critical. This prevented potential accidents and saved the company significant repair costs.
Another case study involved the rail industry. Inspectors used Eddy Current Testing to examine train wheels and tracks. They found subsurface cracks that were invisible to the naked eye. Addressing these issues early helped maintain safety and reduce downtime.
Best Practices For Spot Weld Detection
Spot weld detection can be tricky, but with the right techniques, you can make it much easier. Whether you’re working on car repairs or metal fabrication, finding spot welds accurately is crucial. In this section, we’ll go over some best practices to help you detect spot welds like a pro. Follow these guidelines, and you’ll save time, reduce errors, and ensure safety.
Safety Precautions
Before diving into the detection process, it’s essential to prioritize safety. Here are some key precautions to keep in mind:
- Wear Protective Gear: Always wear gloves, safety goggles, and a face shield. Spot welding can produce sparks and small metal fragments.
- Ensure a Ventilated Area: Work in a well-ventilated area to avoid inhaling fumes. If possible, use an exhaust fan or open windows.
- Disconnect Power: If you’re working on a vehicle or any powered equipment, make sure to disconnect the battery or power source to prevent electrical shocks.
- Secure Your Workspace: Keep your work area clean and organized. Loose tools and clutter can lead to accidents.
Accuracy Improvement Tips
Finding spot welds accurately can sometimes feel like searching for a needle in a haystack. However, these tips can help improve your accuracy:
- Use Proper Lighting: Good lighting is essential. Use a bright, focused light to spot the subtle indentations of spot welds.
- Employ a Weld Cutter: Using a specialized spot weld cutter can make it easier to identify and separate spot welds without damaging the surrounding metal.
- Leverage Inspection Tools: Tools like magnifying glasses or borescopes can help you get a closer look at the welds, especially in hard-to-reach areas.
- Mark Your Findings: Once you locate a spot weld, mark it with a visible marker. This ensures you don’t lose track of it as you move along.
- Practice Patience: Rushing the detection process can lead to mistakes. Take your time to carefully inspect each area for spot welds.
Detecting spot welds doesn’t have to be a daunting task. By following these best practices, you’ll make the process safer and more accurate. Remember, attention to detail and a methodical approach are your best allies in this task.

Credit: www.youtube.com
Future Trends In Spot Weld Detection
Spot weld detection is crucial for ensuring the structural integrity of assembled products, especially in industries like automotive and aerospace. As we step into the future, new trends and technologies are emerging, making spot weld detection more efficient and accurate. Let’s dive into what’s on the horizon for this essential process.
Emerging Technologies
Technology is evolving at a rapid pace, and spot weld detection is no exception. Here are some of the most promising advancements:
- AI and Machine Learning: Artificial Intelligence (AI) and Machine Learning (ML) are transforming spot weld detection. These technologies can analyze vast amounts of data quickly, identifying patterns and anomalies that humans might miss. Imagine a system that learns from each weld, improving its accuracy over time!
- Infrared Imaging: Infrared cameras are being used to detect spot welds by capturing the heat signatures during the welding process. This method is non-invasive and provides real-time feedback, ensuring each weld meets quality standards.
- Ultrasonic Testing: Ultrasonic waves can penetrate materials and provide detailed images of internal structures. This technology helps in identifying even the smallest defects in spot welds, enhancing overall safety and reliability.
Industry Innovations
Industries are continually seeking ways to improve spot weld detection. Here are some exciting innovations making waves:
- Automated Inspection Systems: Automation is revolutionizing spot weld inspection. Robotic arms equipped with sensors and cameras can inspect welds faster and more accurately than human workers. This not only increases productivity but also reduces human error.
- Augmented Reality (AR): AR is being used to train workers and assist in spot weld detection. By overlaying digital information on the real world, workers can see precisely where to place welds and how to inspect them. It’s like having a digital welding coach right in front of you!
- Blockchain for Quality Assurance: Blockchain technology ensures that every weld’s data is securely recorded and traceable. This transparency helps in maintaining quality control and accountability throughout the manufacturing process.
So, what’s the takeaway here? The future of spot weld detection is bright, with emerging technologies and industry innovations leading the way. Whether through AI, infrared imaging, ultrasonic testing, or automated systems, these advancements are set to make weld detection faster, more accurate, and more reliable. Stay tuned, as these trends are just the tip of the iceberg!
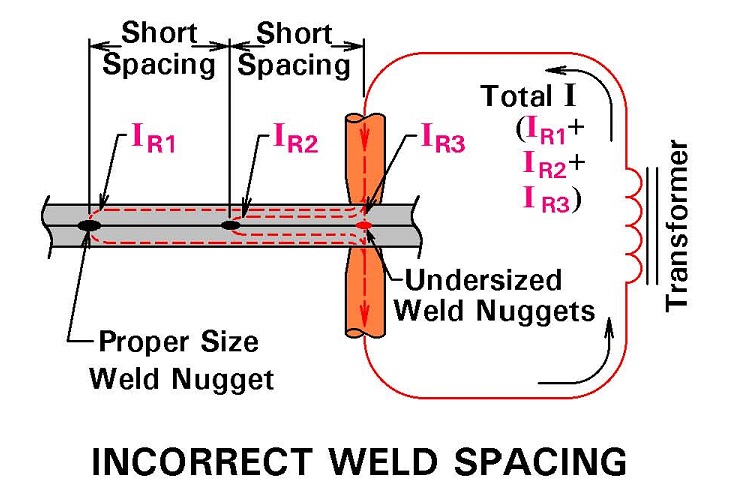
Credit: www.howtoresistanceweld.info
Frequently Asked Questions
How To Identify Spot Welds?
Identify spot welds by looking for small, circular indentations or nuggets on metal surfaces. They often appear in a uniform pattern.
What Is The Best Tool For Spot Welds?
The best tool for spot welds is a quality spot welder. Brands like Miller, Lincoln Electric, and Hobart are highly recommended.
How To Check Spot Welding?
Inspect spot welds visually for uniformity and consistency. Measure weld nugget size with calipers. Perform a peel test to check weld strength. Use ultrasonic testing for internal defects. Conduct a torque test to ensure durability.
Where Can Spot Welding Be Found?
Spot welding is commonly found in automotive manufacturing, electronics, and metal fabrication industries. It joins metal sheets in car bodies, appliances, and various equipment.
Conclusion
Finding spot welds doesn’t have to be difficult. Use the right tools. Inspect carefully. Pay attention to common weld locations. Practice makes it easier. Follow these tips to save time and effort. Your projects will benefit from clean, accurate welds.
Remember, patience and practice lead to success. Keep honing your skills. Happy welding!