Welding and fabrication are essential skills in many industries. They help create strong, durable structures.
This blog post will explore the best welding and fabrication techniques, tools, and tips. Whether you’re a beginner or a pro, you’ll find valuable insights here. Welding and fabrication are vital for constructing and repairing metal structures. These processes require precision, skill, and the right equipment.
Understanding the best practices can improve your results and efficiency. This guide will cover top techniques, innovative tools, and expert tips. You’ll learn about different welding methods, materials used, and safety measures. So, whether you’re working on a DIY project or a professional task, this information will help you achieve better outcomes. Stay tuned as we delve into the world of welding and fabrication.
Introduction To Welding And Fabrication
Welding and fabrication are the backbone of many industries, from construction to automotive. These processes involve joining materials, usually metals, to create structures, machines, or parts. Whether you are building a skyscraper or fixing a car, welding and fabrication are essential skills that ensure everything stays together. But what makes them so important, and where are they used? Let’s dive in!
Importance Of Quality
When it comes to welding and fabrication, quality is king. Imagine a bridge with poor welding; it could lead to a disaster. Quality welding ensures that the joints are strong and durable, which is crucial for safety and longevity. Skilled welders use various techniques to achieve the best results, ensuring that every weld is up to standard.
Here are some reasons why quality is paramount:
- Safety: High-quality welding prevents accidents and failures.
- Durability: Well-fabricated structures last longer and require less maintenance.
- Efficiency: Good welding practices reduce the need for repairs, saving time and money.
Quality in welding is like having a solid foundation for a house. Without it, everything else can fall apart.
Industry Applications
Welding and fabrication are used in countless industries. From the towering buildings in our cities to the cars we drive, these skills are everywhere. Here are some of the key areas where welding and fabrication play a crucial role:
Industry | Application |
---|---|
Construction | Building structures, bridges, and infrastructure |
Automotive | Manufacturing and repairing vehicles |
Aerospace | Creating aircraft parts and components |
Manufacturing | Producing machinery and equipment |
These industries rely on skilled welders to ensure that their products are safe, durable, and efficient. Without welding and fabrication, many of the things we take for granted would not be possible.
So next time you see a skyscraper or drive your car, remember the welders and fabricators who made it all possible. They might not wear capes, but they are heroes in their own right!
Credit: www.facebook.com
Types Of Welding Techniques
When it comes to welding and fabrication, there are various techniques to achieve strong and durable joints. Each method has its own unique advantages and is suitable for different applications. Whether you’re a hobbyist or a professional, understanding the basics of these techniques can help you choose the right one for your project. Let’s dive into the most popular types of welding techniques.
Arc Welding
Arc welding is one of the most common techniques used in the industry. It involves using an electric arc to melt the metals at the welding point. The heat generated by the arc melts the metal, which then solidifies to create a joint. It’s great for heavy metals and is often used in construction and industrial applications.
- Uses an electric arc
- Great for heavy metals
- Common in construction and industrial applications
Mig Welding
MIG (Metal Inert Gas) welding is another popular technique. It uses a wire feeding gun that continuously feeds the wire and uses an inert gas to shield the weld pool from contamination. MIG welding is fast and produces clean welds. It’s ideal for both thin and thick materials, making it versatile for various projects.
- Uses a wire feeding gun
- Produces clean welds
- Ideal for thin and thick materials
Tig Welding
TIG (Tungsten Inert Gas) welding, also known as GTAW (Gas Tungsten Arc Welding), is known for its precision. It uses a non-consumable tungsten electrode to produce the weld. TIG welding is excellent for thin materials and provides high-quality, clean welds. It’s often used in aerospace and automotive industries where precision is crucial.
- Uses a non-consumable tungsten electrode
- Great for thin materials
- High-quality, clean welds
Spot Welding
Spot welding is a resistance welding technique. It involves using heat generated from electrical resistance to weld two or more metal sheets together. This method is commonly used in the automotive industry for welding sheet metal. It’s quick and efficient, making it perfect for mass production.
- Uses heat from electrical resistance
- Common in the automotive industry
- Quick and efficient for mass production
Choosing the right welding technique can make all the difference in the quality and durability of your project. Whether you need the precision of TIG welding or the speed of MIG welding, understanding these techniques will help you make an informed decision. Happy welding!
Essential Welding Equipment
When it comes to welding and fabrication, having the right equipment is paramount. Whether you’re a seasoned professional or a beginner, understanding the essential tools you need can make your work more efficient and safe. In this blog post, we’ll break down the key pieces of equipment that every welder should have in their arsenal. From welding machines to safety gear and accessories, let’s dive into what you need to get started and keep going strong.
Welding Machines
A good welding machine is the heart of any welding operation. These machines come in various types, including MIG, TIG, and Stick welders. Each type has its own set of benefits and is suited for different tasks.
- MIG Welders: Ideal for beginners due to their ease of use. They are perfect for welding thin to medium thickness metals.
- TIG Welders: These provide high precision and are great for welding thin materials and intricate work.
- Stick Welders: Known for their durability and ability to work well in outdoor or windy conditions, making them a favorite for heavy-duty tasks.
Choosing the right welding machine depends on the type of work you plan to do. For instance, if you’re planning to work on car bodies or thin metal sheets, a MIG welder would be your go-to tool. On the other hand, for tasks requiring finesse and precision, a TIG welder would be more appropriate.
Safety Gear
Welding is a dangerous job, and safety should always be a top priority. The right safety gear can protect you from burns, eye damage, and other injuries. Here’s a list of essential safety equipment:
- Welding Helmet: Protects your eyes and face from sparks and harmful UV rays. Auto-darkening helmets are highly recommended for their convenience.
- Gloves: Heat-resistant gloves are a must to protect your hands from burns.
- Protective Clothing: Wear flame-resistant jackets and pants to shield your body from sparks and heat.
- Safety Glasses: Even with a helmet, it’s wise to wear safety glasses for extra protection.
- Respirator: To avoid inhaling harmful fumes, a respirator is essential, especially when working in confined spaces.
Remember, safety gear is not optional – it’s a necessity. Take it from me; I once skipped wearing my gloves and regretted it the moment a hot spark landed on my hand. Ouch!
Welding Accessories
Welding accessories might not steal the spotlight, but they are just as crucial for a successful welding project. Here are a few must-have accessories:
Accessory | Purpose |
---|---|
Clamps | Hold your workpieces together securely for accurate welds. |
Wire Brush | Clean the metal surfaces before welding to ensure a good bond. |
Chipping Hammer | Remove slag from welds to see the quality of your weld bead. |
Angle Grinder | Prepare and finish your welds by grinding down excess material. |
These accessories might seem trivial, but trust me, they can make a world of difference. Imagine trying to weld two pieces of metal without clamps – it’s like trying to write with a pen that keeps running out of ink. Frustrating, right?
In conclusion, having the right welding equipment is essential for both safety and efficiency. By investing in quality welding machines, proper safety gear, and handy accessories, you’re setting yourself up for success in every welding project you undertake. So, gear up and get ready to weld like a pro!
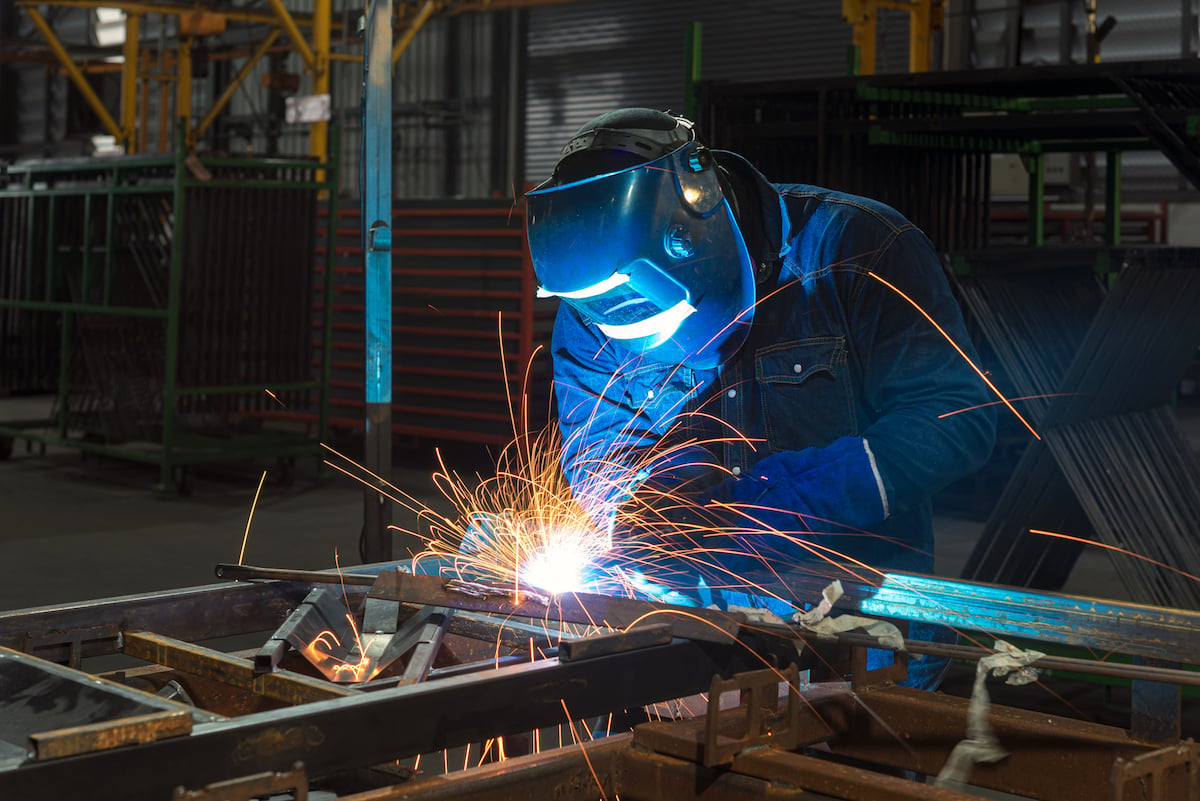
Credit: www.fvmt.com
Preparation For Welding
Welding is an art that requires precision and attention to detail. Proper preparation is the key to achieving high-quality welds. Whether you are a seasoned welder or just starting out, understanding the fundamentals of preparation can make all the difference. Let’s dive into the essential steps you need to take before striking that first arc.
Material Selection
Choosing the right material is crucial for a successful weld. Different metals have unique properties and require specific techniques. Here are some things to consider:
- Type of Metal: Are you working with steel, aluminum, or perhaps titanium? Each metal behaves differently when welded.
- Thickness: Thicker materials may need more heat, while thinner ones require a delicate touch.
- Compatibility: Ensure that the filler material matches the base metal to avoid weak joints.
For example, when I first started welding, I used the wrong filler for a stainless steel project. The result? A brittle joint that broke under pressure. Lesson learned: always double-check your materials!
Surface Cleaning
Imagine trying to paint a dirty wall. The paint won’t stick well, right? The same goes for welding. Surface cleaning is essential for a strong bond. Here’s how to do it:
- Remove Rust and Dirt: Use a wire brush or grinder to clean the metal surface. Rust and dirt can create weak spots.
- Degrease: Wipe the area with a degreasing agent to remove oils and grease. This ensures a clean surface for welding.
- Dry Thoroughly: Make sure the surface is completely dry before you start welding. Moisture can lead to porosity in the weld.
Trust me, taking a few extra minutes to clean the surface can save hours of rework later. I’ve been there, done that!
Joint Design
The way you prepare your joints affects the strength and appearance of the weld. Here are some common joint designs and tips for each:
Joint Type | Description | Best Practice |
---|---|---|
Butt Joint | Two pieces of metal placed edge to edge. | Ensure edges are aligned and tack-welded before full welding. |
Lap Joint | One piece overlaps another. | Overlap should be consistent, and edges should be clamped tightly. |
Corner Joint | Two pieces meet at a right angle. | Use a proper jig to maintain the angle and prevent movement. |
I remember my first lap joint project; I didn’t clamp the pieces tightly, and they shifted during welding. It was a mess! Proper joint design and preparation prevent such mishaps.
In conclusion, preparation for welding is like laying the foundation for a building. Get it right, and everything else falls into place. Take the time to select the right material, clean the surfaces, and design your joints properly. Your future self will thank you!
Advanced Fabrication Methods
Advanced fabrication methods have transformed modern welding and fabrication industries. They bring precision, efficiency, and quality to projects. Cutting-edge technologies like CNC machining, laser cutting, and robotic welding are leading the way. These methods enhance productivity and ensure superior results.
Cnc Machining
CNC machining stands for Computer Numerical Control machining. It involves using computers to control machine tools. This process ensures high precision and consistency. CNC machines can handle complex shapes and intricate designs. They work efficiently with various materials like metal, plastic, and wood. This method reduces human error and speeds up production time.
Laser Cutting
Laser cutting uses a high-powered laser beam to cut materials. It offers unmatched accuracy and clean edges. This method is suitable for metals, plastics, and even wood. Laser cutting is fast and precise. It minimizes waste and maximizes material usage. This technique is ideal for detailed and complex designs.
Robotic Welding
Robotic welding uses robotic arms to perform welding tasks. It ensures consistent and high-quality welds. This method is perfect for repetitive and high-volume projects. Robotic welding enhances safety by reducing human exposure to hazardous environments. It also increases production speed and efficiency.
Credit: www.facebook.com
Quality Control In Welding
Quality control in welding ensures the strength and durability of welds. It involves various techniques to inspect welds, identify defects, and implement preventive measures. This process is crucial in maintaining the integrity of structures and products.
Inspection Techniques
Inspection techniques are essential in assessing weld quality. Visual inspection is the most basic method. Inspectors look for surface flaws, such as cracks or porosity. Ultrasonic testing uses sound waves to detect internal defects. Radiographic testing involves X-rays to examine the weld’s internal structure. Magnetic particle testing reveals surface and subsurface defects in ferromagnetic materials.
Common Defects
Weld defects can compromise safety and performance. Cracks are serious defects that can lead to failure. Porosity occurs when gas bubbles get trapped in the weld. Incomplete fusion happens when the weld metal does not properly bond with the base metal. Slag inclusions are non-metallic particles trapped in the weld. Undercutting is when the base metal is eroded, weakening the weld.
Preventive Measures
Preventive measures help avoid weld defects. Proper training ensures welders understand techniques and standards. Using clean materials prevents contamination. Preheating the metal can reduce the risk of cracking. Maintaining the correct welding parameters, like temperature and speed, is crucial. Regular equipment maintenance ensures consistent performance. Following these measures can significantly improve weld quality.
Safety Practices In Welding
Welding and fabrication involve risks. Safety practices are essential to protect workers. Following proper safety protocols reduces the risk of accidents and injuries.
Personal Protective Equipment
Welders must wear appropriate personal protective equipment (PPE). This includes a welding helmet, gloves, and flame-resistant clothing. The helmet protects eyes and face from sparks and UV light. Gloves shield hands from heat and sharp objects. Flame-resistant clothing prevents burns and reduces fire risks.
Ventilation And Fume Control
Welding produces harmful fumes and gases. Proper ventilation is crucial to maintain air quality. Use exhaust systems to remove fumes from the workspace. Fume extractors capture harmful particles at the source. Always ensure the work area is well-ventilated to protect respiratory health.
Fire Safety
Welding involves high temperatures and sparks. This increases fire risks. Keep flammable materials away from the welding area. Always have fire extinguishers nearby. Inspect the work area for fire hazards before starting. Train workers to handle fire emergencies. Follow these steps to prevent fires and ensure a safe work environment.
Future Trends In Welding And Fabrication
The welding and fabrication industry is evolving rapidly. New technologies and methods are transforming traditional practices. Future trends in this field promise increased efficiency and sustainability.
Automation And Robotics
Automation and robotics are changing welding and fabrication. Robots now perform complex welding tasks with precision. This reduces human error and increases productivity. Automated systems handle repetitive tasks, allowing skilled workers to focus on more intricate work. The industry is moving towards fully automated production lines.
Sustainable Practices
Sustainability is becoming crucial in welding and fabrication. Companies are adopting eco-friendly methods. They use energy-efficient machines to reduce carbon footprints. Waste management practices are improving. Recycling materials is now a standard practice. These steps help protect the environment and save costs.
Innovative Materials
Innovative materials are making welding and fabrication more efficient. Lightweight composites and advanced alloys are gaining popularity. These materials offer strength and durability while being easy to work with. They also improve product performance and lifespan. The industry is continuously exploring new materials to meet evolving needs.
Frequently Asked Questions
What Is The Highest Quality Welding?
TIG welding is considered the highest quality welding. It offers precision, strength, and a clean finish. This method is ideal for thin materials and critical welds, providing excellent control and minimal distortion.
What Is The Best Company To Weld For?
The best company to weld for varies based on personal preferences and location. Lincoln Electric, Miller Electric, and ESAB are top choices.
Which Welding Brand Is The Best?
Miller, Lincoln Electric, and ESAB are top welding brands. They offer reliable, high-quality equipment favored by professionals.
What Is The Highest Paying Welding?
Underwater welding is the highest paying welding job. It involves working in challenging conditions and requires specialized skills. Salaries can exceed $100,000 annually.
Conclusion
Choosing the best welding and fabrication service is essential. Quality work ensures durability and safety. Skilled professionals provide reliable results. Invest in experienced welders for your projects. Ensure they use modern equipment. Check their previous work. Good reviews matter. Reliable services save time and money.
So, make a wise decision. Your projects deserve the best care. Welding and fabrication done right adds value. Trust skilled hands for top-notch results.