Finding the right welding helmet is crucial for safety and productivity. This guide will help you choose the best welding helmet for visibility, covering everything from lens technology to comfort features. We’ll explore different types, key features, and factors to consider, ensuring you make an informed decision.
Let’s start with the basics.
A welding helmet’s primary function is to protect your eyes and face from intense light and harmful UV radiation produced during welding. But just as important as protection is visibility. Poor visibility can lead to mistakes, fatigue, and even accidents. This section dives deep into what constitutes good visibility in a welding helmet.
Lens Technology and Shade Numbers
The heart of any welding helmet is its lens. Different lens technologies offer varying degrees of clarity and protection. Auto-darkening lenses (ADLs) are the most popular choice, automatically adjusting their shade to match the welding intensity. These typically range from shade 8 to 13, with higher numbers indicating darker shades for brighter welding arcs. The number you need depends on your welding process; MIG welding usually requires a shade 10-11, while stick welding might need a shade 12-13. I’ve personally found that a shade 10 ADL provides a great balance of clarity and protection for most of my work, offering excellent visibility even in bright conditions.
Passive lenses, on the other hand, are fixed-shade lenses. They don’t automatically darken, meaning you need to select a specific shade beforehand. These are generally more affordable but less convenient.
Viewing Area and Field of Vision
The size of the viewing window significantly impacts visibility. Larger viewing windows offer a wider field of vision, reducing the need to constantly adjust your helmet. Smaller viewing areas restrict your sight and can be tiring during extended welding sessions. I’ve experienced this firsthand – a helmet with a smaller viewing window made precision work significantly more challenging. When choosing a helmet, look for one with the largest viewing area possible within your budget and preferred style.
Consider the shape of the viewing window as well. Some helmets offer a wider, more rectangular viewing area compared to traditional circular lenses, providing a more panoramic view. This feature is particularly beneficial for complex welding projects requiring a broader perspective.
Factors Affecting Welding Helmet Visibility
While the lens itself is paramount, several other factors contribute to the overall visibility of your welding helmet. This section examines these crucial aspects.
Lens Clarity and Optical Quality
Not all lenses are created equal. High-quality lenses offer superior clarity, minimizing distortion and improving the overall viewing experience. Look for lenses made from high-optical-grade materials, which reduce eye strain and enhance precision. Cheap lenses can distort the view, making it difficult to see details. This is critical for complex welds and intricate work. In my experience, spending a bit more on a high-optical-quality lens significantly improves both productivity and the accuracy of my welds.
Consider the clarity of the lens under different light conditions, even outside of welding. A good quality lens will provide a clear view under various ambient lighting circumstances.
Helmet Design and Comfort
An uncomfortable helmet will detract from your concentration, indirectly affecting visibility. A well-designed helmet with proper headgear, balanced weight, and a comfortable fit ensures less shifting or adjustment, resulting in a more focused and less obstructed view. Features like adjustable headbands, padded headgear, and a streamlined design minimize fatigue and distraction, enhancing your overall focus and perception.
The helmet’s weight distribution is also a crucial factor. A helmet that is too heavy can cause neck strain and lead to fatigue, indirectly impairing your ability to maintain a steady and clear view of your work. A lighter-weight helmet ensures that you are comfortable throughout the day, so that your vision remains sharp and clear.
Types of Welding Helmets and Their Visibility
Different welding helmets cater to various needs and preferences. This section explores popular types and their visibility characteristics.
Auto-Darkening Welding Helmets (ADLs)
ADLs are the most popular type, offering convenience and enhanced safety. They automatically adjust the shade of the lens depending on the intensity of the welding arc. This means you don’t have to manually change the shade, making them perfect for quick changes between welding tasks. However, the speed of the darkening and clearing response varies between models. Faster response times translate to better visibility during short arc interruptions. I personally prefer ADLs with a response time under 1/1000th of a second for smooth, uninterrupted viewing during various welding processes.
Moreover, ADLs often feature advanced features like grind mode for improved visibility during grinding tasks. This enhances safety and productivity by eliminating the need to remove the helmet during grinding operations.
Passive Welding Helmets
Passive helmets utilize fixed-shade lenses that don’t darken automatically. They require manual shade adjustments, which can be time-consuming. While less expensive, they can be inconvenient and may not always offer the optimal shade for every welding situation. The primary advantage of passive helmets lies in their simple design and affordability. Their dependability makes them suitable for certain simpler tasks. However, their lack of automatic adjustment impacts visibility and overall productivity when compared to ADLs. Therefore, the suitability of passive helmets greatly depends on individual needs and the complexity of the welding project.
It’s important to note that the visibility offered by passive helmets greatly depends on the quality of the lens and the selected shade. Choosing an appropriate shade is paramount to ensuring sufficient protection without compromising visibility.
Choosing the Right Shade for Optimal Visibility
Selecting the appropriate shade number is paramount for both eye protection and optimal visibility. This section clarifies the importance of shade selection.
Shade Number and Welding Process
Different welding processes require different shade numbers. For instance, MIG welding typically requires a shade 10-11, while stick welding may necessitate a shade 12-13. Choosing an incorrect shade can compromise either your eye safety or your visibility. Too dark a shade will obscure your view, leading to inaccuracy and fatigue. Too light a shade exposes your eyes to excessive UV radiation, jeopardizing your eye health. To determine the appropriate shade, consult the safety guidelines for your specific welding process and equipment.
The selection of the right shade number can impact productivity and accuracy. A well-chosen shade ensures you can focus on your welding task without straining your eyes or sacrificing safety. Experimenting with slightly different shade numbers can help you find the ideal level of visibility and eye protection for your work environment and welding style.
Factors Affecting Shade Selection
Besides the welding process, other factors influence shade selection. Ambient lighting conditions, the intensity of the arc, and personal preferences play significant roles. Brighter environments may require a darker shade to maintain proper protection, while dimmer settings might allow for a lighter shade. I found that a darker shade is preferable for outdoor welding to counteract the bright sunlight, while a lighter shade is adequate for indoor welding where ambient lighting is controlled.
Individual eyesight and personal preference also play a role. Some welders may find a slightly darker shade more comfortable than others, and this should be considered when selecting the best shade for your needs. It’s essential to find a balance between safety and visibility, so experimenting and determining your own optimum shade is essential.
Advanced Features Enhancing Visibility
Modern welding helmets incorporate advanced features that further boost visibility. This section explores these features.
External Grinding Mode
Many ADLs feature an external grinding mode. This mode adjusts the lens to a lighter shade, ideal for grinding or other tasks where you need greater visibility. This is particularly important for safety; removing and putting on a helmet during grinding operations is a safety hazard. The grinding mode increases safety by allowing the welder to maintain eye protection during these operations without compromising visibility.
The functionality of the external grinding mode greatly enhances workflow efficiency by eliminating the need to switch helmets or adjust shade settings. This seamless transition is critical for efficient and productive welding processes.
Improved Lens Coatings
Modern lenses incorporate advanced coatings that further enhance visibility. These coatings reduce glare and reflections, improving clarity. Additionally, some coatings offer anti-fog capabilities, preventing condensation from obscuring your view in humid environments. These coatings are essential for ensuring both enhanced visibility and reduced maintenance. Anti-fog coatings, in particular, are critical for maintaining productivity in less-than-ideal conditions, such as those in which humidity or temperature changes might compromise visibility.
The investment in high-quality lenses with advanced coatings ensures clear and consistent vision during all phases of the welding process, making it easier to maintain concentration and perform welds precisely.
Budget Considerations and Value for Money
Welding helmets range in price, and this section discusses how budget impacts visibility.
Balancing Cost and Features
While expensive helmets often boast superior features, a budget-friendly option can still offer acceptable visibility. The key is to prioritize the features most critical for your needs and welding style. For occasional welders, a basic ADL with a decent-sized viewing window might suffice. However, for professional welders who spend many hours welding daily, a high-end helmet with advanced features like increased viewing area, faster response times, and improved lens clarity may justify the higher cost.
It’s important to evaluate your personal needs and budget, balancing features with affordability. Consider the frequency of welding tasks and the required precision before selecting a model. Don’t overspend on unnecessary features if you rarely use them, but also prioritize key features that significantly improve your visibility and safety.
Finding the Best Value
Finding the best value for your money involves researching different models, comparing features, and reading reviews from other welders. Focus on critical features such as lens clarity, viewing area, shade adjustment speed, and comfort features. Read reviews to see what other welders have experienced with particular models, as this can provide insights into durability, ease of use, and long-term performance.
Websites and forums dedicated to welding often offer in-depth reviews and comparisons. These resources can assist you in narrowing your options based on your welding applications and budget considerations. Always prioritize both safety and value when selecting your next welding helmet.
Maintenance and Care for Optimal Visibility
Regular maintenance is crucial for preserving your welding helmet’s visibility and lifespan.
Cleaning and Lens Protection
Keep the lens clean and free of debris. Use a designated lens cleaning solution and a soft, lint-free cloth. Avoid harsh chemicals or abrasive materials that could scratch the lens. Consider using a lens cover to protect the lens when the helmet isn’t in use. Regular cleaning ensures the clarity of your view, maximizing your safety and productivity.
Always use a soft, clean cloth and an appropriate lens cleaner when cleaning the helmet’s lens. Avoid using abrasive cloths or harsh cleaning agents, which might scratch the lens or damage the protective coatings.
Replacing Worn-Out Lenses
Lenses degrade over time, especially with frequent use. If you notice any scratches, discoloration, or decreased clarity, replace the lens immediately. This is a critical safety measure, as compromised lenses can reduce visibility and weaken UV protection. Using a worn-out lens significantly increases the risk of eye damage due to both reduced visibility and weakened protection. Replacing the lens ensures that you maintain optimal eye protection and maintain the best possible visibility.
Always consult your helmet’s manual for instructions on replacing the lens correctly. Improper installation can lead to malfunctions and reduced safety.
Frequently Asked Questions
What is the best welding helmet for visibility for beginners?
For beginners, an auto-darkening helmet with a large viewing area and a comfortable fit is ideal. Look for a helmet with a shade range that covers common welding processes, such as MIG and stick welding. A reputable brand with positive reviews will ensure quality and reliability. Consider a mid-range ADL with a reputable brand to ensure long-term use without overspending.
How do I choose the right shade number for my welding helmet?
The appropriate shade number depends on the welding process and the intensity of the arc. Consult the safety guidelines for your specific welding process to determine the recommended shade. Consider testing different shade numbers to find the one that provides the best balance between eye protection and clarity. Remember, too dark a shade reduces visibility, and too light a shade compromises eye safety.
Can I use a welding helmet with poor visibility?
No, using a welding helmet with poor visibility is extremely dangerous. Compromised visibility increases the risk of accidents and injuries. Replace a worn-out or damaged lens immediately, and consider replacing the entire helmet if the visibility is consistently poor, regardless of cleaning. Maintaining clear vision is critical for safety and precision while welding.
How often should I replace my welding helmet lens?
You should replace your welding helmet lens when you notice scratches, discoloration, or a significant decrease in clarity. Regular inspection is vital. The frequency of replacement depends on usage frequency and conditions, but it’s generally recommended to replace the lens every year or two, even if it appears undamaged. Proactive lens replacement protects your eyesight and ensures optimal welding performance.
What are the benefits of auto-darkening lenses over passive lenses?
Auto-darkening lenses (ADLs) offer superior convenience and safety. They automatically adjust to the welding arc’s intensity, eliminating the need for manual shade adjustments. This results in smoother workflow and improved safety. Passive lenses require manual adjustments, which can be time-consuming and potentially unsafe, depending on the welding application.
How do I clean my welding helmet lens properly?
Clean your welding helmet lens with a dedicated lens cleaning solution and a soft, lint-free cloth. Avoid harsh chemicals or abrasive materials. Gentle wiping motions are essential to avoid scratching. Regular cleaning is crucial for maintaining optimal visibility and lens longevity. Always refer to your helmet’s manual for specific cleaning instructions.
What are the signs of a worn-out welding helmet?
A worn-out helmet may exhibit cracks in the housing, damage to the lens, a malfunctioning auto-darkening system (if applicable), loose or broken straps, or an uncomfortable fit. Any of these signs indicate a potential safety hazard and warrant helmet replacement. A worn-out helmet compromises safety and visibility, increasing the risk of accidents.
Final Thoughts
Choosing the best welding helmet for visibility is a critical decision that directly impacts safety, productivity, and the quality of your welds. This guide has explored various factors to consider, from lens technology and shade numbers to comfort and maintenance. Remember to prioritize features that best suit your needs and budget, ensuring a balance between safety, visibility, and cost-effectiveness. Don’t compromise on safety; invest in a quality helmet that allows you to perform your welding tasks safely and efficiently. By following the guidance outlined in this article, you’ll be well-equipped to select a welding helmet that prioritizes both your safety and optimal visibility. Now, go out there and weld with confidence!
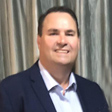
Endow Russel the owner chief editor of giftendow.com . I am a mechanical engineer and assign to an local firm with much experience in welding and industrial equipment.