Welding cast iron is tricky. It needs the right process for success.
Cast iron is common in many industries. It’s strong but brittle. Finding the best welding process is crucial. The wrong method can cause cracks or weak joints. This can lead to costly repairs or failures. In this blog post, we’ll explore the best welding processes for cast iron.
Understanding these techniques helps you choose the right one. This ensures your work is durable and reliable. Whether you’re a beginner or an expert, this guide will provide useful insights. Let’s dive into the world of cast iron welding and find the best process for your needs.

Credit: www.cruxweld.com
Introduction To Cast Iron Welding
Welding cast iron can be tricky. This metal has unique properties. Understanding these helps achieve better results. This guide will explore the best welding process for cast iron. Let’s dive into the basics and importance of proper techniques.
Importance Of Proper Techniques
Using the correct techniques in cast iron welding is crucial. Proper methods ensure strong welds. They also prevent cracks and other defects. Cast iron has high carbon content. This makes it brittle and sensitive to heat. Incorrect techniques can lead to weak joints.
Good techniques enhance durability. They also improve the overall quality of the weld. This is especially important in repair work. Proper welding can restore the original strength of the cast iron piece. It also ensures the longevity of the repair.
Common Challenges
Welding cast iron presents several challenges. The high carbon content can cause cracking. This happens if the metal cools too quickly. Managing heat is critical to avoid this issue. Preheating the metal can help control the cooling rate.
Porosity is another common problem. This occurs when gas gets trapped in the weld. It weakens the weld and can cause failure. Using the right filler material can minimize porosity. Special care is needed to select the right filler for cast iron.
Another challenge is contamination. Cast iron often contains impurities. These can interfere with the welding process. Cleaning the surface thoroughly is essential. Removing oils, rust, and other contaminants improves weld quality.
Types Of Cast Iron
When it comes to welding cast iron, understanding the different types of cast iron is crucial. Each type has unique properties that affect how it responds to welding. Let’s dive into the most common types: Gray Cast Iron, Ductile Cast Iron, and White Cast Iron.
Gray Cast Iron
Gray cast iron is the most common type of cast iron. It gets its name from the gray color of the fracture surface. This type is known for its excellent machinability and good thermal conductivity. It’s used in many applications, like engine blocks and pipes.
Fun fact: The graphite flakes in gray cast iron make it easy to machine but tricky to weld. Why? These flakes can create weak points that might crack under stress.
Ductile Cast Iron
Ductile cast iron, also known as nodular cast iron, is a bit different. Instead of graphite flakes, it has graphite nodules. These nodules give it better flexibility and toughness compared to gray cast iron. It’s commonly used in automotive parts and gears.
Imagine trying to bend a twig versus a rubber band. Ductile iron is like the rubber band—it can handle more strain without breaking. This makes it more weld-friendly than gray cast iron.
White Cast Iron
White cast iron is the hardest type but also the most brittle. It has a white, shiny fracture surface due to the absence of graphite. It’s often used in wear-resistant surfaces like grinding balls and mill linings.
Here’s a little analogy: If gray cast iron is like a pencil, white cast iron is like a piece of chalk. It’s very hard but can easily snap if mishandled. This brittleness makes welding white cast iron quite challenging.
To sum up, knowing the type of cast iron you are dealing with is the first step in choosing the best welding process. Each type has its own set of challenges and advantages, and understanding these can make the welding process smoother and more successful.
Choosing The Right Welding Process
Choosing the right welding process for cast iron is crucial. It ensures the strength and durability of your welds. Different methods can affect the results. Here’s a look at some of the best options.
Arc Welding
Arc welding is one of the most common methods for cast iron. It uses an electric arc to melt the metal. This creates a strong bond. It’s suitable for repairing cracks or joining pieces. Preheating the cast iron is essential. It prevents cracking during cooling.
Gas Welding
Gas welding, or oxy-acetylene welding, is another effective method. This process uses a flame to heat the cast iron. It’s ideal for smaller repairs. It allows for better control over the heat. This reduces the risk of damage. Proper flux is needed to clean the metal surface. This ensures a strong weld.
Mig Welding
MIG welding is also a good choice for cast iron. It uses a wire feed and a shielding gas. This method is fast and efficient. It’s ideal for larger projects. Preheating and slow cooling are necessary. These steps prevent cracking. It’s easier for beginners to learn. It provides consistent results.
Preparation Techniques
Preparing cast iron for welding is like setting the stage for a perfect performance. If you get the preparations right, the welding process becomes much smoother and more successful. Let’s dive into two essential preparation techniques: cleaning the surface and preheating the material.
Cleaning The Surface
Cleanliness is next to godliness, especially in welding. The first step in preparing cast iron is to clean the surface thoroughly. Here’s why it’s crucial:
- Remove impurities: Dirt, grease, and old paint can contaminate the weld, leading to weak joints.
- Prevent porosity: Contaminants can cause porosity, making the weld porous and brittle.
So, how do you clean the surface effectively? Follow these steps:
- Degrease: Use a degreaser or soapy water to remove oil and grease. Wipe the surface clean with a cloth.
- Grind or sand: Use a grinder or sandpaper to remove rust, old paint, and other residues. Aim for a shiny, bare metal surface.
- Brush: Finish off with a wire brush to get rid of any leftover particles.
Remember, a clean surface is key to a strong, reliable weld. It’s like cooking in a clean kitchen – you can’t expect a great meal if your pots and pans are dirty!
Preheating The Material
Preheating is another vital step in preparing cast iron for welding. But why bother with preheating? Well, here are a few reasons:
- Reduce thermal shock: Cast iron is prone to cracking due to its brittleness. Preheating helps reduce the risk of thermal shock when welding.
- Improve weld quality: Preheating ensures a more uniform temperature, leading to a stronger weld.
Here’s how you can preheat cast iron:
- Check the temperature: Aim for a preheating temperature between 500°F and 1200°F (260°C and 650°C). Use a temperature stick or infrared thermometer to monitor the heat.
- Heat evenly: Use a torch or an oven to heat the entire piece evenly. Uneven heating can cause stress and cracks.
- Maintain temperature: Keep the material at the desired temperature throughout the welding process to prevent cooling too quickly.
Think of preheating like warming up before a workout. It prepares the material, making it more flexible and less likely to get injured (or in this case, cracked).
By following these preparation techniques, you set yourself up for a successful welding experience with cast iron. So, roll up your sleeves and get ready to create some strong, sturdy welds!
Welding Procedures
Welding cast iron can be tricky because it is prone to cracking. Following the right procedures is crucial. This guide will help you weld cast iron effectively.
Step-by-step Guide
First, clean the cast iron surface thoroughly. Remove all dirt, grease, and paint. Use a wire brush or grinder for this task.
Next, preheat the cast iron. Heat it slowly to around 500°F to 1200°F. This reduces the risk of cracking.
Then, choose the right welding rod. Nickel-based rods are the best for cast iron.
Start welding with short beads. Avoid long welds to reduce stress on the metal.
Peen the welds after each pass. This helps in reducing stress and cracking.
Finally, cool down the cast iron slowly. Wrap it in an insulating blanket. This step is crucial to prevent cracks.
Avoiding Common Mistakes
Do not weld cast iron without preheating. It will crack easily.
Do not use the wrong welding rod. Nickel-based rods are the best choice.
Do not weld too quickly. Short welds are better than long ones.
Do not skip peening the welds. This step helps in reducing stress.
Do not cool down cast iron too fast. Rapid cooling will cause cracks.
Post-welding Practices
Post-welding practices are crucial for ensuring the integrity of the weld on cast iron. These practices help to reduce stress, prevent cracks, and ensure the welded area is sound. Proper cooling and thorough inspection are key steps in this process.
Cooling Techniques
Cooling must be controlled. Rapid cooling can cause cracks in cast iron. Use slow and uniform cooling methods. Cover the welded part with insulating material. This helps to retain the heat. Sand, ashes, or dry lime work well. These materials slow down the cooling process.
An oven can also be used for cooling. Set it to a low temperature. Reduce the temperature gradually. This prevents thermal shock. Always monitor the cooling process. This ensures it is slow and even.
Inspection And Testing
Inspection follows the cooling process. Look for visible cracks or defects. Use a magnifying glass if needed. Dye penetrant testing is useful. Apply a liquid dye to the surface. The dye will seep into any cracks. Use a developer to make cracks visible.
Ultrasonic testing is another method. It helps to detect internal defects. This method uses sound waves. Sound waves reflect off internal flaws. This helps to find hidden defects. Ensure all tests are thorough. This ensures the weld is strong and reliable.
Expert Tips For Success
When it comes to welding cast iron, there’s a fine art to getting it just right. Cast iron is a tricky material, prone to cracking if not handled with care. But don’t worry! With some expert tips, you’ll be well on your way to mastering the craft. Let’s dive into some key insights that will help you succeed in your welding projects.
Maintaining Equipment
First things first, your welding equipment needs to be in tip-top shape. Think of it like maintaining a car. Would you drive a car with flat tires? Of course not! The same logic applies here.
- Regular Inspections: Check your welding machine regularly. Look for signs of wear and tear. Replace any damaged parts immediately.
- Cleanliness: Keep your equipment clean. Dirt and grime can affect the performance. A clean machine is a happy machine!
- Proper Storage: Store your equipment in a dry, safe place. Moisture can cause rust, which is a welder’s worst enemy.
By maintaining your equipment, you ensure a smooth welding process. It’s the small things that make a big difference.
Safety Precautions
Safety first! Welding can be dangerous if you’re not careful. But don’t let that scare you. With the right precautions, you can stay safe and sound.
- Protective Gear: Always wear the right gear. This includes a welding helmet, gloves, and long sleeves. Your skin will thank you!
- Ventilation: Weld in a well-ventilated area. Fumes from welding can be harmful. Fresh air is your friend.
- Fire Safety: Keep a fire extinguisher nearby. Sparks can fly, and it’s better to be safe than sorry.
These simple steps can prevent accidents and keep you welding happily ever after. Remember, a safe welder is a successful welder.
So, there you have it! By maintaining your equipment and following safety precautions, you’re setting yourself up for success. Now, go forth and weld with confidence. Happy welding!
By maintaining your equipment and following safety precautions, you are setting yourself up for success in welding cast iron. Now, go forth and weld with confidence. Happy welding!

Credit: www.reliance-foundry.com
Case Studies And Applications
Cast iron welding is a specialized process with many real-world applications. Understanding these applications through case studies can provide valuable insights. This section explores several examples and the lessons learned from them.
Real-world Examples
One notable example is the repair of antique machinery. A vintage steam engine had a cracked cylinder head. Experts used the oxy-acetylene welding process. This method ensured a strong bond. The engine was restored to full functionality.
Another case involved a large industrial pump. The pump’s housing had a significant crack. The repair team chose the arc welding process. This choice was due to its efficiency. The pump was back in operation within 24 hours.
Lessons Learned
These real-world examples offer several lessons. First, choosing the right welding process is crucial. Each method has its strengths and weaknesses. Understanding these can save time and resources.
Second, preparation is key. Pre-heating the cast iron before welding can prevent further damage. Post-weld cooling should be gradual. This ensures the weld’s integrity and longevity.
Lastly, skilled welders make a difference. Experienced professionals can adapt methods to specific needs. Their expertise ensures high-quality repairs.
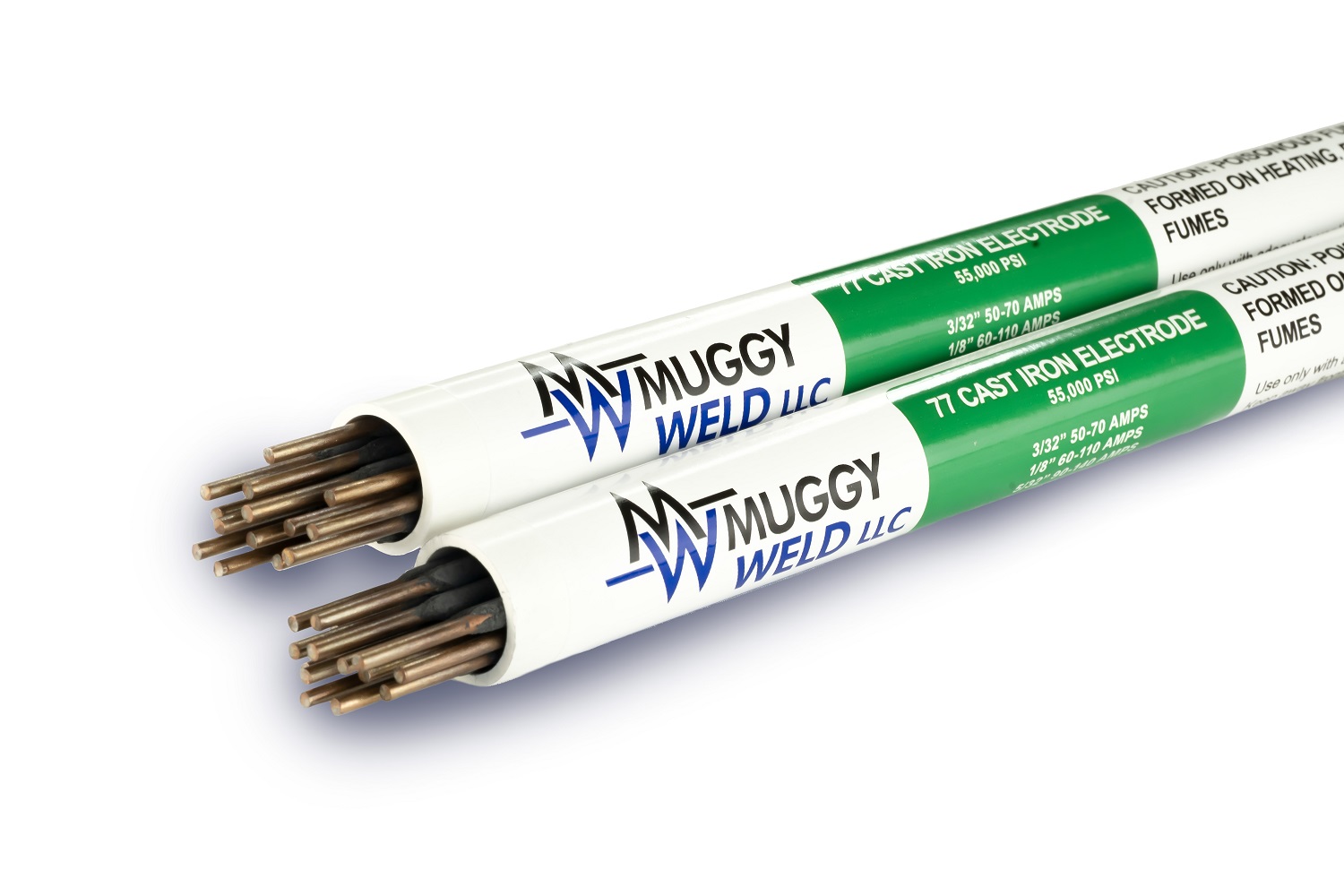
Credit: www.muggyweld.com
Frequently Asked Questions
What Is The Best Process To Weld Cast Iron?
The best process to weld cast iron involves preheating the metal. Use nickel-based electrodes and weld slowly to avoid cracks. Allow the cast iron to cool gradually to prevent stress.
Which Welding Is Suitable For Cast Iron?
MIG welding and stick welding are suitable for cast iron. Use nickel-based electrodes for best results. Preheating helps prevent cracks.
What Is The Welder Setting For Cast Iron?
Set the welder to low amperage for cast iron. Use nickel-based electrodes. Preheat the metal to 500°F. Ensure slow cooling.
How To Weld Cast Iron Without It Cracking?
Preheat cast iron before welding to 500-1200°F. Use nickel or stainless steel electrodes. Weld slowly and in small sections. Allow it to cool gradually. Avoid rapid cooling to prevent cracking.
Conclusion
Choosing the best welding process for cast iron is crucial. Different methods suit different needs. Stick welding is great for small repairs. MIG welding works well for larger projects. TIG welding offers precision. Always consider the specific requirements of your project.
Proper preparation and technique ensure success. Cast iron welding can be challenging but rewarding. With the right approach, your results will be strong and reliable. Practice and patience are key. Happy welding!