Welding sheet metal requires precision and the right technique. Different processes suit different needs.
Understanding the best welding process for sheet metal can save time and money. Whether you’re a hobbyist or a professional, choosing the right method is essential. Sheet metal is thin and can warp or burn easily. This makes the welding process more challenging.
You need a method that provides control and accuracy. In this blog, we will explore various welding processes suitable for sheet metal. From MIG to TIG, each technique has unique advantages. We will discuss these methods to help you make an informed decision. Stay tuned to learn which welding process suits your project best.
Mig Welding
When it comes to welding sheet metal, MIG welding often stands out as a top choice. Known for its simplicity and efficiency, MIG welding is a go-to for both beginners and seasoned welders. But what makes it so special? Let’s dive into the details of MIG welding to understand its advantages, disadvantages, and best applications.
Advantages
MIG welding, or Metal Inert Gas welding, offers several benefits that make it a preferred method for working with sheet metal:
- Ease of Use: MIG welding is user-friendly. Even beginners can quickly get the hang of it.
- Speed: It’s a fast process, which saves time on projects.
- Versatility: This method works well on various metals, including aluminum, stainless steel, and mild steel.
- Cleaner Welds: MIG welding produces fewer splatters compared to other methods, which means less cleanup.
Disadvantages
However, like any technique, MIG welding has its downsides:
- Cost: The initial setup can be expensive due to the need for a MIG welder and gas supply.
- Portability: MIG welding equipment is less portable, making it cumbersome for on-site jobs.
- Material Thickness: This method is not ideal for very thick metals, limiting its use to thinner sheets.
Best Applications
So, where does MIG welding shine the brightest? Here are a few scenarios where it truly excels:
- Automotive Repairs: Perfect for fixing car bodies and frames.
- Manufacturing: Ideal for producing metal furniture, appliances, and other industrial products.
- DIY Projects: Great for home repairs and creative metalwork projects.
In summary, MIG welding is a reliable and efficient method for welding sheet metal. It offers ease of use, speed, and versatility, making it suitable for a range of applications. While it has some drawbacks, such as cost and portability, the benefits often outweigh the cons, especially for those looking to achieve clean and precise welds.

Credit: www.zintilon.com
Tig Welding
If you’re new to welding, you might be wondering which process is best for sheet metal. One of the top contenders is TIG welding. TIG stands for Tungsten Inert Gas, and it’s a favorite among welders for its precision and versatility. Let’s dive into the details, shall we?
Advantages
TIG welding has some notable advantages that make it a popular choice for working with sheet metal. Here are a few:
- Precision: TIG welding offers excellent control, making it ideal for thin materials.
- Clean Welds: The process produces high-quality, clean welds without spatter or slag.
- Versatility: It can be used on a variety of metals, including aluminum, stainless steel, and mild steel.
- Control: Welders can easily control the heat input, reducing the risk of warping the sheet metal.
Disadvantages
Of course, TIG welding isn’t perfect. Here are some of the downsides:
- Slow Process: It can be slower compared to other welding methods, which may not be ideal for high-volume projects.
- Skill Level: It requires a higher level of skill and practice to master, which can be a barrier for beginners.
- Equipment Cost: The equipment needed for TIG welding can be more expensive than other welding types.
Best Applications
So, when should you use TIG welding? Here are some of the best applications:
- Automotive Work: TIG welding is great for car body repairs and custom builds because of its precision.
- Artistic Projects: If you’re working on sculptures or metal art, the clean, precise welds are a huge advantage.
- Aerospace: The aerospace industry often uses TIG welding due to the high-quality welds it produces.
- Thin Sheet Metal: It’s particularly well-suited for thin sheets where control and precision are crucial.
There you have it! TIG welding is a fantastic option for sheet metal, especially if you need precision and clean welds. While it does come with some challenges, the benefits often outweigh the drawbacks. Have you tried TIG welding before? Share your experiences and tips in the comments below!
Spot Welding
When it comes to joining sheet metal, spot welding is a popular method. It uses heat from an electric current to join two pieces of metal together. Let’s dive into the specifics of spot welding, including its advantages, disadvantages, and best applications.
Advantages
Spot welding has several benefits, making it a go-to option for many. Here are some of its key advantages:
- Speed: Spot welding is fast. It can join metals in a matter of seconds.
- Efficiency: This method uses less energy compared to other welding techniques.
- Cost-Effective: It is cheaper because it requires less material and labor.
- Strength: The welds are strong and can withstand significant stress.
- Clean Process: Spot welding does not produce smoke, gas, or fumes, making it cleaner and safer.
Disadvantages
However, spot welding is not without its downsides. Here are some potential drawbacks:
- Limited Thickness: It works best with thin metals. Thick sheets may not weld properly.
- Surface Preparation: The metal surfaces must be clean for an effective weld.
- Accessibility: Only works where the welding electrodes can reach.
- Equipment Cost: The initial investment in spot welding equipment can be high.
Best Applications
Spot welding is ideal for certain types of projects. Here are some of its best applications:
- Automotive Industry: Used extensively in car manufacturing for joining metal parts.
- Electronics: Perfect for welding small metal components in electronic devices.
- Construction: Useful in creating steel frameworks and metal structures.
- Household Appliances: Commonly used in assembling metal parts of appliances like refrigerators and washing machines.
In summary, spot welding is a practical and efficient way to join sheet metal. It has its pros and cons, but for many applications, it remains the top choice. Give it a try for your next sheet metal project, and see how it can make your work easier and faster!
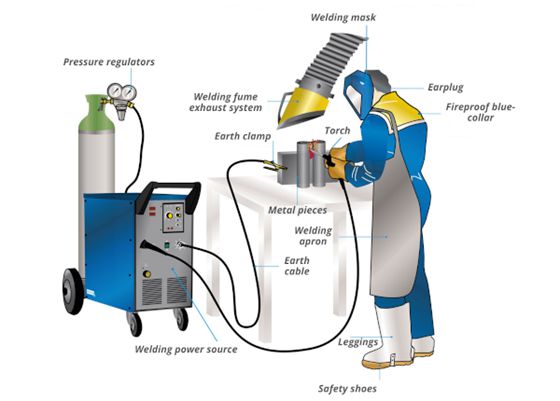
Credit: waykenrm.com
Laser Welding
Laser welding is a precise and efficient method for joining sheet metal. It uses a focused laser beam to melt and fuse metal pieces together. This process offers many benefits for both small and large-scale projects.
Advantages
Laser welding provides high precision. The focused laser beam ensures minimal heat-affected zones. This reduces the risk of warping or distortion in the metal. The process is also very fast. It allows for quick completion of welding tasks, increasing productivity.
Laser welding is also versatile. It can weld various types of metals, including steel, aluminum, and titanium. The welds are strong and clean, requiring little post-weld processing. This saves time and effort in the production process.
Disadvantages
One major drawback of laser welding is the cost. The equipment needed is expensive. This can be a barrier for small businesses or individual welders. The process also requires skilled operators. Proper training is essential to ensure safety and quality.
Laser welding may not be suitable for thicker materials. The process is best for thin sheets, typically less than 6mm thick. This limits its applications in some heavy-duty industries. Maintenance of laser welding equipment can also be costly and complex.
Best Applications
Laser welding is ideal for industries needing precision. The automotive and aerospace sectors often use it for its accuracy and speed. It is also popular in electronics manufacturing. Small, intricate components benefit from the precise control laser welding offers.
Medical device production also uses laser welding. The clean, strong welds are crucial for ensuring the safety and reliability of medical tools. Any industry where high-quality welds are essential can benefit from laser welding.
Plasma Arc Welding
Plasma Arc Welding (PAW) is a process that uses a constricted arc between a tungsten electrode and the workpiece to join metals. It is particularly effective for sheet metal, offering precision and control. But is it the right method for your next project? Let’s dive into the details.
Advantages
Plasma Arc Welding has several advantages that make it a popular choice for sheet metal work:
- Precision: PAW provides excellent control over the arc, making it ideal for intricate and delicate work.
- Speed: It’s a fast process, which can significantly reduce production time.
- Versatility: Suitable for a wide range of metals, from stainless steel to aluminum.
- Clean Welds: Produces high-quality, clean welds with minimal spatter and distortion.
These benefits make PAW a go-to for many professionals working with sheet metal.
Disadvantages
However, every rose has its thorns. Plasma Arc Welding is no exception:
- Cost: The equipment and setup can be quite expensive compared to other welding methods.
- Complexity: Requires skilled operators and precise control, which can be a learning curve for beginners.
- Maintenance: The torch components can wear out quickly and need regular maintenance.
While these drawbacks are notable, they can be managed with proper training and investment.
Best Applications
So, where does Plasma Arc Welding shine the brightest?
- Aerospace Industry: Its precision makes it perfect for the thin, high-strength metals used in aircraft.
- Medical Equipment: The clean, high-quality welds are crucial for sterile environments.
- Automotive Sector: Ideal for intricate parts and components that require strong, reliable welds.
- Electronics: Useful for welding small, detailed parts without causing heat damage.
If your project falls into one of these categories, PAW might just be the perfect fit.
In conclusion, while Plasma Arc Welding has its challenges, its precision, speed, and versatility make it a strong contender for sheet metal welding. Weigh the pros and cons, and consider your specific needs before making a decision. Happy welding!

Credit: www.millerwelds.com
Factors To Consider
Choosing the best welding process for sheet metal involves several factors. Understanding these factors will help in achieving the best results. Each factor plays a crucial role in determining the most suitable welding method.
Material Thickness
The thickness of the material affects the welding process. Thin sheet metals require precise control to avoid burn-through. Thicker metals may need processes that provide deeper penetration. Adjusting the welding method ensures proper fusion without damaging the material.
Joint Design
The design of the joint influences the welding technique. Lap joints, butt joints, and T-joints each have specific needs. The complexity of the joint affects the choice of welding process. Some methods are better for simple joints, while others handle complex designs efficiently.
Production Volume
The volume of production also determines the welding process. High production volumes benefit from automated welding techniques. Manual welding suits low production volumes. Considering production volume ensures efficiency and cost-effectiveness.
Safety Tips
Welding sheet metal can be a rewarding task, but it’s crucial to prioritize safety. Even for seasoned welders, adhering to safety protocols is non-negotiable. Below are some essential tips to keep you safe while welding.
Protective Gear
Wearing the right protective gear is vital. It keeps you safe from sparks, heat, and harmful UV rays. Here’s what you need:
- Welding Helmet: Shields your face and eyes from harmful light and flying debris.
- Gloves: Protect your hands from heat and sharp metal edges.
- Long-Sleeved Jacket: Prevents burns and cuts on your arms.
- Boots: Ensure they are flame-resistant and cover your ankles.
Wearing this gear may feel like suiting up for battle, but it’s worth it. No one wants a trip to the emergency room, right?
Ventilation
Good ventilation isn’t just a nice-to-have; it’s a must. Welding produces fumes that can be harmful if inhaled. Here are some simple steps to ensure proper ventilation:
- Open windows and doors to create a cross breeze.
- Use fans to circulate fresh air into your workspace.
- Consider using a fume extractor if working in a confined space.
Remember, breathing in clean air keeps your lungs happy and healthy. Nobody wants to feel lightheaded while welding, do they?
Fire Hazards
Welding involves high temperatures and sparks, which can easily ignite nearby materials. To prevent fires, keep these tips in mind:
- Clear the Area: Remove any flammable objects from your workspace.
- Keep a Fire Extinguisher Handy: Make sure it’s within arm’s reach, just in case.
- Check for Leaks: If using gas, ensure there are no leaks in your setup.
It’s better to be safe than sorry. A small spark can lead to a big disaster, but with these precautions, you can weld with peace of mind.
Frequently Asked Questions
What Is The Best Method For Welding Sheet Metal?
TIG welding is the best method for welding sheet metal. It provides precision, clean welds, and minimal distortion.
Is Mig Or Tig Welding Better For Sheet Metal?
MIG welding is better for sheet metal due to its speed and ease of use. TIG welding provides cleaner, more precise welds but requires more skill. For most sheet metal applications, MIG welding is more efficient.
Which Welding Is Best For Sheet Metal?
TIG welding is best for sheet metal. It provides precise control and clean welds, especially on thin materials. MIG welding also works well for sheet metal due to its speed and ease of use. Both methods minimize warping and ensure strong joints.
What Is The Most Common Welding Process For Thin Sheet Metals?
The most common welding process for thin sheet metals is Gas Tungsten Arc Welding (GTAW), also known as TIG welding. It provides precise control and clean welds.
Conclusion
Choosing the right welding process for sheet metal is crucial. Each method has its benefits. MIG welding is great for beginners. TIG welding offers precision. Spot welding works well for thin sheets. Consider the type and thickness of your metal.
Also, think about your skill level. Proper equipment and safety measures are essential. Experiment with different methods. Find the one that suits your needs best. Practice makes perfect. Happy welding!