If you’re into car repairs or restoration, you’ve probably wondered if flux core welding is suitable for car sheet metal. I get it—it’s a common question, especially for beginners or hobbyists who don’t have access to expensive equipment. The short answer is yes, you can weld car sheet metal with a flux core welder, but it’s not without its challenges.

As someone who’s tried various welding techniques on thin sheet metal, I can tell you that flux core welding is both convenient and effective when used correctly. However, it requires patience, practice, and a few adjustments to get it right. In this guide, I’ll share everything you need to know about using flux core welding for car sheet metal.
What is Flux Core Welding?
Before we dive into specifics, let’s quickly go over what flux core welding is. Flux core welding, or FCAW (Flux Core Arc Welding), uses a special wire that contains a flux material inside. This flux eliminates the need for an external shielding gas, making it ideal for outdoor welding or in windy conditions.
While flux core welding is great for thicker materials and structural projects, welding thin materials like car sheet metal can be tricky. The key lies in understanding its pros and cons for this specific application.
Why Use Flux Core Welding for Car Sheet Metal?
Ease of Use
Flux core welding is beginner-friendly. You don’t need to worry about setting up a shielding gas system, which makes it more accessible for DIY enthusiasts.
Portability
Since it doesn’t require a gas tank, flux core welders are portable. This is especially useful if you’re working in a garage or driveway.
Cost-Effective
Flux core wire is relatively affordable, and the overall setup cost is lower than other welding methods like TIG or MIG with gas.
Challenges of Welding Car Sheet Metal with Flux Core
Thin Metal Burn-Through
One of the biggest challenges is the risk of burning through the thin car sheet metal. Flux core welding generates a lot of heat, which isn’t ideal for delicate materials.
Spatter and Cleanup
Flux core welding tends to produce more spatter compared to MIG or TIG welding. This means you’ll spend extra time cleaning up the welds afterward.
Less Precision
If you’re looking for smooth, precise welds (like those required for car bodywork), flux core may not be your best bet. With the right technique, you can achieve acceptable results.
How to Weld Car Sheet Metal with Flux Core
Choose the Right Equipment
Start by ensuring your flux core welder is capable of handling thin materials. Look for a welder with adjustable amperage and wire feed speed settings.
Use Thin Flux Core Wire
For car sheet metal, use a smaller diameter wire, such as 0.030 inches or even 0.025 inches. Thinner wire generates less heat and reduces the risk of burn-through.
Set the Correct Parameters
Adjust the voltage, amperage, and wire feed speed to match the thickness of the metal. Lower settings are crucial for thin sheet metal to avoid excessive heat.
Practice Spot Welding
Instead of running continuous beads, use spot welds to minimize heat buildup. Tack weld along the joint, spacing the welds a few inches apart, and then connect them with short bursts.
Keep the Weld Area Cool
Overheating can warp or damage the metal. Pause frequently to allow the metal to cool down, or use a damp cloth to speed up the cooling process.
Work in Clean Conditions
Ensure the sheet metal is free of rust, dirt, and paint before welding. Clean surfaces promote better weld adhesion and reduce contamination.
Tips for Better Results
Master the Technique
Take time to practice on scrap sheet metal before working on your car. Focus on controlling the heat and perfecting your hand movement.
Use Backing Material
If you’re worried about burn-through, place a backing material, like a copper plate, behind the sheet metal. This helps dissipate heat and prevents holes from forming.
Pay Attention to Fit-Up
Make sure the metal pieces fit snugly together before welding. Poor fit-up can lead to gaps that are difficult to fill with flux core welding.
Grind Down the Welds
After welding, use a grinder to smooth out the welds. This not only improves the appearance but also helps with finishing tasks like painting or sealing.
Is Flux Core Welding the Best Option for Car Sheet Metal?
While flux core welding can get the job done, it’s not the ideal method for car sheet metal. Other techniques, like MIG welding with gas or TIG welding, offer better control and cleaner welds. I you’re on a budget or working in outdoor conditions, flux core welding is a viable alternative.
Safety Tips for Welding Car Sheet Metal
- Wear Protective Gear: Always wear gloves, a welding helmet, and flame-resistant clothing.
- Work in a Well-Ventilated Area: Flux core welding produces fumes, so make sure your workspace has proper ventilation.
- Secure Your Workpiece: Use clamps to hold the sheet metal in place while welding.
- Avoid Overheating: Pay close attention to the heat settings to avoid damaging the thin metal.
Conclusion
So, can you weld car sheet metal with flux core? Absolutely—but it’s not without its challenges. With the right setup, technique, and a little patience, you can achieve decent results.
While it may not be the go-to method for professional bodywork, flux core welding is a cost-effective and accessible option for hobbyists or those working in less-than-ideal conditions.
The key is to practice, understand your equipment, and take the time to prepare your materials properly. If you’re up for the challenge, give it a try—you might be surprised at what you can accomplish.
FAQs
Can I use 0.035-inch wire for welding car sheet metal with flux core?
While it’s possible, 0.035-inch wire generates more heat and increases the risk of burn-through. A thinner wire, like 0.030 inches, is better suited for car sheet metal.
Why does my weld keep burning through the metal?
Burn-through usually happens when the heat settings are too high or if you’re moving too slowly. Lower the voltage and speed up your welding technique to minimize heat buildup.
Is flux core welding strong enough for car repairs?
Yes, flux core welding creates strong welds, but it may not be as clean or precise as other methods like MIG or TIG welding. It’s best for small repairs or non-structural components.
How do I reduce spatter when using flux core welding?
To reduce spatter, ensure your wire feed speed and voltage settings are balanced. Clean the metal surface thoroughly before welding and consider using anti-spatter spray.
What’s the best alternative to flux core welding for car sheet metal?
MIG welding with shielding gas is a better option for car sheet metal. It provides cleaner welds and more control, especially for thin materials.
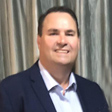
Endow Russel the owner chief editor of giftendow.com . I am a mechanical engineer and assign to an local firm with much experience in welding and industrial equipment.