Welding is both an art and a science. It feels amazing when you create that perfect, strong weld, but let’s be honest—things don’t always go smoothly. I’ve been there myself, staring at a weld that didn’t turn out the way I wanted, wondering what went wrong.
If you’ve experienced problems like cracks, porosity, or weak welds, don’t worry—you’re not alone. These issues are common, but the good news is that they’re also fixable. I’ll walk you through the most common welding problems and how to address them effectively. Let’s troubleshoot together!
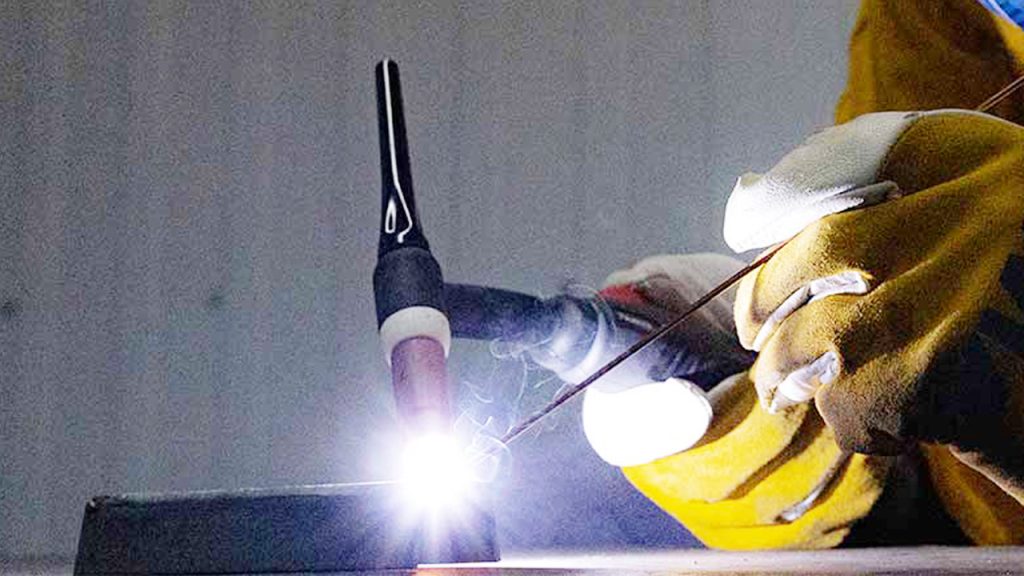
Image by welding.com.au
Why Understanding Welding Issues Is Important
Before jumping into specific problems, it’s worth noting why understanding and fixing welding issues matters. Poor welds can compromise the strength and durability of your work, which might lead to costly repairs or even safety hazards. Knowing how to identify and solve these problems ensures that your welds are not only visually appealing but also structurally sound.
Porosity: What It Is and How to Fix It
What Is Porosity?
Porosity refers to tiny holes or gas pockets that get trapped in the weld. These bubbles weaken the weld and make it look less professional.
Common Causes of Porosity
- Contaminated materials (oil, dirt, or rust)
- Incorrect shielding gas or gas flow
- Welding in windy conditions
- Excessive heat or moisture
Fixing Porosity
Here’s how I’ve tackled porosity in my projects:
Clean Your Materials: Always clean the metal surfaces thoroughly before starting. Use a wire brush or grinder to remove dirt, rust, and oil.
Check Your Gas Flow: Make sure you’re using the correct shielding gas and that the flow rate is appropriate. For MIG welding, a flow rate of 20–25 cubic feet per hour usually works well.
Protect Against Wind: Shield your workspace from wind, or use a windscreen to ensure consistent gas coverage.
Dry Your Materials: If moisture is present, heat the materials slightly before welding to drive off water.
Cracks: Causes and Solutions
What Are Cracks?
Cracks in welding occur when the weld becomes brittle and fractures. These are serious issues, especially in structural welds.
Types of Cracks
- Hot Cracks: Appear while the weld is cooling.
- Cold Cracks: Develop after the weld has cooled completely.
Common Causes of Cracks
- Rapid cooling of the weld
- Incorrect welding technique
- Using incompatible filler material
- Poor joint preparation
Fixing Cracks
Preheat Your Metal: For materials prone to cracking, like high-carbon steel, preheating reduces rapid cooling and stress.
Use Proper Filler Materials: Match your filler rod or electrode to the base metal to prevent incompatibility.
Control Cooling: Allow the weld to cool slowly by covering it with a blanket or sand.
Check Joint Design: Make sure the joint is properly prepared and not under excessive stress.
Weak Welds: How to Strengthen Them
What Are Weak Welds?
Weak welds lack the strength to hold the materials together. This can happen when the weld doesn’t penetrate deeply enough or when there’s insufficient fusion between the materials.
Common Causes of Weak Welds
- Incorrect amperage settings
- Poor joint preparation
- Inconsistent welding speed
- Using the wrong electrode size
Fixing Weak Welds
Adjust Your Amperage: Ensure you’re using the correct amperage for the material thickness. Too low, and the weld won’t penetrate; too high, and it might burn through.
Improve Joint Preparation: Clean and bevel the edges for better penetration and fusion.
Maintain a Steady Speed: Move the torch at a consistent pace to achieve uniform welds.
Use the Right Electrode: Check the size and type of your electrode for compatibility with your base metal.
Undercutting: Prevention and Repair
What Is Undercutting?
Undercutting happens when the weld metal fails to fill the edges of the joint, leaving a groove or notch.
Common Causes of Undercutting
- Excessive heat
- Incorrect electrode angle
- Fast travel speed
Fixing Undercutting
Lower the Amperage: High heat can cause the base metal to melt excessively. Adjust your settings accordingly.
Hold the Right Angle: Keep the electrode or torch at the correct angle to avoid digging into the metal.
Slow Down: A slower travel speed allows the weld to fill the joint completely.
Spatter: Causes and Cleanup
What Is Spatter?
Spatter refers to small droplets of molten metal that scatter around the weld area. While it doesn’t usually affect weld strength, it looks messy and can be a pain to clean up.
Common Causes of Spatter
- Incorrect voltage or amperage settings
- Using cheap or incompatible consumables
- Dirty or contaminated materials
Fixing Spatter
- Adjust Your Settings: Ensure the voltage and amperage are set correctly for the welding process and material thickness.
- Use High-Quality Consumables: Cheap electrodes or wires often produce more spatter. Invest in better-quality options.
- Clean Your Materials: Dirt and oil can lead to excess spatter, so clean the metal thoroughly before welding.
- Use Anti-Spatter Spray: This prevents spatter from sticking to your work surface.
Incomplete Fusion: How to Get It Right
What Is Incomplete Fusion?
Incomplete fusion occurs when the weld metal doesn’t bond properly with the base material, leaving weak spots.
Common Causes of Incomplete Fusion
- Low heat input
- Poor joint preparation
- Incorrect electrode angle
Fixing Incomplete Fusion
- Increase Heat Input: Ensure the material gets hot enough to achieve proper fusion.
- Prepare the Joint: Clean and bevel the edges to allow for better penetration.
- Check Your Technique: Use a slight weaving motion and maintain the correct electrode angle to improve bonding.
Distortion: Controlling Material Warping
What Is Distortion?
Distortion happens when heat from welding causes the metal to warp or bend.
Common Causes of Distortion
- Excessive heat
- Lack of clamping or supports
- Poor welding sequence
Fixing Distortion
- Use Clamps: Secure the material firmly to minimize movement during welding.
- Reduce Heat Input: Lower the amperage and reduce dwell time to minimize warping.
- Plan Your Welds: Use a staggered welding sequence to distribute heat more evenly.
Conclusion
Welding is a rewarding skill, but it comes with its challenges. From porosity to distortion, every welder encounters issues at some point. The key is to recognize these problems and know how to fix them.
By understanding the causes and solutions to common welding issues, you’ll improve your skills and produce higher-quality work. Remember, every mistake is an opportunity to learn and grow as a welder. So, don’t get discouraged—keep practicing, stay patient, and enjoy the journey.
FAQs
Why does my weld have holes in it?
This is likely caused by porosity, which can result from contaminated materials, incorrect shielding gas, or welding in windy conditions.
How can I prevent cracks in my welds?
Preheat the material, use compatible filler materials, and control cooling to reduce the risk of cracks.
What causes spatter, and how do I clean it up?
Spatter can result from incorrect voltage or dirty materials. You can clean it up with a wire brush or grinder, and prevent it with anti-spatter spray.
How do I fix a weak weld?
Check your amperage settings, prepare the joint properly, and ensure consistent welding speed for a stronger weld.
What’s the best way to prevent distortion?
Use clamps, reduce heat input, and plan your welding sequence to distribute heat evenly and minimize warping.
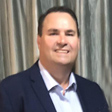
Endow Russel the owner chief editor of giftendow.com . I am a mechanical engineer and assign to an local firm with much experience in welding and industrial equipment.