If you’ve ever found yourself standing in front of your welding setup, wondering whether to use flux core or stick welding, you’re not alone. Both methods are widely used, versatile, and deliver excellent results when applied correctly. But they each have their strengths and weaknesses, and choosing the right one can save you time, money, and a lot of frustration.
Having explored both methods over the years, I’ve learned when to reach for my stick welder and when flux core gets the job done better. This guide will help you understand the key differences, advantages, and applications for both techniques so you can confidently tackle your next welding project.

What Is Flux Core Welding?
Flux core welding, officially known as flux-cored arc welding (FCAW), uses a hollow wire filled with flux as the electrode. As the wire melts during welding, the flux inside creates a shielding gas that protects the weld pool from contamination.
There are two main types of flux core welding:
- Self-Shielded Flux Core: No external shielding gas is required because the flux inside the wire provides all the protection.
- Gas-Shielded Flux Core: Requires an external shielding gas for cleaner and more precise welds.
Flux core is popular for its high welding speed, strong welds, and ability to perform well in outdoor or windy conditions.
What Is Stick Welding?
Stick welding, also called shielded metal arc welding (SMAW), is one of the oldest and simplest welding methods. It uses a consumable electrode, or “stick,” coated with flux. As the electrode melts, the flux coating releases gas and slag to protect the weld from contaminants.
Stick welding is known for its ruggedness, making it a favorite for fieldwork and heavy-duty applications. It’s a great choice for welding thicker materials and working in less-than-ideal conditions.
Differences Between Flux Core and Stick Welding
Ease of Use
Flux core welding is often considered easier for beginners. The wire feed system provides consistent material flow, making it more forgiving of uneven techniques. Stick welding, while straightforward, requires better control of the electrode and arc to avoid sticking or poor weld quality.
Portability
Both methods are portable, but stick welding has an edge here. Since stick welding doesn’t require a wire feeder or shielding gas (in most cases), it’s perfect for remote locations or jobs that demand minimal equipment.
Material Thickness
- Flux Core: Excels with thin to medium-thickness materials. Gas-shielded flux core welding can even handle precision work on thinner metals.
- Stick Welding: Better for thicker materials due to its strong arc and deep penetration.
Welding Speed
Flux core welding is faster, especially for repetitive tasks or when working on long welds. Stick welding takes more time due to the need to change electrodes frequently and clean off slag.
Outdoor Performance
- Flux Core: Self-shielded flux core welding performs exceptionally well outdoors, even in windy conditions.
- Stick Welding: Also reliable outdoors but may struggle more with wind disrupting the flux protection.
Weld Quality
- Flux Core: Provides cleaner welds with less slag when using gas-shielded wire.
- Stick Welding: Produces good welds but often requires more post-weld cleanup to remove slag.
Advantages of Flux Core Welding
High Productivity
Flux core welding has a faster deposition rate, meaning you can lay down more material in less time. This is ideal for industrial and large-scale projects.
Versatility in Environments
Self-shielded flux core wires make it easy to weld outdoors or in windy conditions without worrying about shielding gas getting blown away.
Ease of Learning
Beginners can pick up flux core welding quickly due to the consistent feed of the wire and simplified technique compared to stick welding.
Advantages of Stick Welding
Cost-Effectiveness
Stick welding equipment is often more affordable and requires fewer accessories, making it a budget-friendly option.
Wide Material Compatibility
From thick steel to cast iron, stick welding can handle a variety of materials. It’s particularly suited for heavy-duty applications.
Simple Setup
With no need for shielding gas or wire feeders, stick welding has a straightforward setup that’s perfect for quick jobs or remote locations.
When to Use Flux Core Welding
You should consider flux core welding if:
- You need to work on thin to medium-thickness materials.
- Speed is a priority.
- You’re working outdoors but still need high-quality welds.
- You’re a beginner looking for an accessible starting point in welding.
When to Use Stick Welding
Stick welding is a better choice when:
- You’re working with thick materials.
- The job site is remote or lacks access to shielding gas supplies.
- You need a rugged, portable welding solution.
- Cost is a concern, and you’re looking for a simple, reliable method.
Tips for Better Welding Results
Flux Core Welding Tips
- Choose the right type of flux-cored wire for your project.
- Adjust your machine settings for the thickness of the material.
- Maintain a steady travel angle, typically a drag technique.
- Be prepared for spatter, especially with self-shielded wire.
Stick Welding Tips
- Match the electrode type to the material you’re welding.
- Strike and maintain a consistent arc to avoid sticking.
- Clean your workpiece thoroughly for better results.
- Take breaks to allow your machine and materials to cool if overheating occurs.
Which Method Is Right for You?
Choosing between flux core and stick welding depends on your project requirements, budget, and skill level.
- Go with Flux Core if you need speed, versatility, and ease of use, especially for projects that involve thinner materials or outdoor work.
- Stick Welding is ideal if you’re tackling heavy-duty jobs, working with thicker metals, or need a low-cost, portable solution.
Conclusion
Both flux core and stick welding have their place in the world of fabrication and repair. As someone who’s used both extensively, I can confidently say that neither is inherently better than the other. It all comes down to what your project demands.
Flux core welding shines with its speed, ease of use, and ability to deliver clean welds in challenging environments. Stick welding, on the other hand, is the rugged workhorse that can tackle tough jobs with minimal equipment.
Understanding the strengths and limitations of each method will help you make an informed decision and achieve the best possible results. Whichever you choose, take your time to master the technique, and you’ll be well on your way to becoming a skilled welder.
FAQs
Which is better, flux core or stick welding?
It depends on the project. Flux core is better for speed and outdoor work with thinner materials, while stick welding is great for heavy-duty, thick materials.
Can I use flux core welding for structural projects?
Yes, especially with gas-shielded flux core wire. It offers strong penetration and reliable welds for structural applications.
Is stick welding harder to learn than flux core welding?
Yes, stick welding typically requires more practice to master due to the need for precise electrode control.
What are the main drawbacks of flux core welding?
Flux core welding can produce more spatter, and self-shielded wire isn’t ideal for thinner metals.
Can stick welding be used outdoors?
Absolutely! Stick welding performs well outdoors and doesn’t rely on shielding gas, making it a reliable choice for fieldwork.
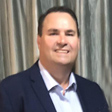
Endow Russel the owner chief editor of giftendow.com . I am a mechanical engineer and assign to an local firm with much experience in welding and industrial equipment.