If you’re trying to decide between flux core welding and MIG welding for your next project, you’re not alone. Both of these methods are widely used in the welding world, and each has its own strengths and weaknesses. I’ve worked with both techniques extensively, and I can tell you—they’re suited for different scenarios, and choosing the right one can make or break your project.

I’ll break down the main differences between flux core welding and MIG welding, explain how they work, and help you understand when to use each one. By the end, you’ll feel confident in picking the method that’s right for you.
What Is Flux Core Welding?
Flux core welding, also known as flux-cored arc welding (FCAW), uses a tubular wire filled with flux to create the weld. When the wire melts, the flux inside produces a gas that shields the weld pool from contaminants like oxygen and nitrogen.
The biggest advantage of flux core welding is its versatility. You can use it in outdoor environments without needing an external shielding gas, making it ideal for construction, repairs, and heavy-duty projects.
What Is MIG Welding?
MIG welding, or metal inert gas welding, is a process that uses a solid wire electrode and an external shielding gas, typically a mix of argon and CO2. This shielding gas protects the weld from atmospheric contamination, resulting in clean, high-quality welds.
MIG welding is particularly popular for indoor projects and applications requiring precision. It’s user-friendly, which makes it a great choice for beginners and hobbyists.
Differences Between Flux Core Welding and MIG Welding
While both flux core welding and MIG welding involve feeding wire through a gun to create the weld, there are some significant differences between the two methods.
Shielding Mechanism
- Flux Core Welding: Uses flux inside the wire to create shielding gas. No external gas is required.
- MIG Welding: Relies on external shielding gas to protect the weld.
Indoor vs Outdoor Use
- Flux Core Welding: Performs well in windy or outdoor conditions because the flux-generated shielding gas isn’t easily blown away.
- MIG Welding: Best suited for indoor environments, as the external shielding gas can be disrupted by wind.
Material Thickness
- Flux Core Welding: Better for thicker materials due to its deep penetration.
- MIG Welding: Ideal for thinner materials, as it provides precise control and reduces the risk of burn-through.
Weld Appearance
- Flux Core Welding: Can produce more spatter and slag, requiring additional cleanup.
- MIG Welding: Offers cleaner, more aesthetically pleasing welds with minimal post-weld cleanup.
Cost of Equipment and Materials
- Flux Core Welding: Generally more cost-effective since it doesn’t require shielding gas.
- MIG Welding: The need for shielding gas and additional equipment makes it more expensive.
Advantages of Flux Core Welding
Flux core welding comes with its own set of benefits that make it a preferred choice for many projects:
- Portability: No need for shielding gas tanks, making it easier to transport.
- Outdoor Performance: Handles windy conditions with ease.
- High Deposition Rate: Ideal for faster welding and filling large gaps.
- Deep Penetration: Suitable for heavy-duty applications and thicker materials.
Advantages of MIG Welding
MIG welding also has its perks, particularly for projects that require precision and cleanliness:
- Cleaner Welds: Minimal spatter and no slag to remove.
- Ease of Use: Beginner-friendly and less technique-sensitive.
- Versatility: Works well on a variety of materials, including aluminum and stainless steel.
- Better for Thin Materials: Reduces the risk of burn-through on delicate surfaces.
When to Use Flux Core Welding
Flux core welding is best suited for:
- Outdoor Projects: Thanks to its self-shielding properties, it excels in windy environments.
- Heavy-Duty Applications: Perfect for thick materials, structural welding, and industrial repairs.
- Tough Jobsites: Its portability and ruggedness make it ideal for construction and fieldwork.
When to Use MIG Welding
MIG welding is a better choice for:
- Indoor Work: Controlled environments where shielding gas can be used effectively.
- Thin Metals: Great for automotive work, light fabrication, and sheet metal welding.
- Aesthetic Welds: When a clean, professional finish is required.
Choosing Between Flux Core Welding and MIG Welding
If you’re still unsure which method to use, here are a few questions to consider:
Where Will You Be Welding?
- If you’re working outdoors or in windy conditions, go with flux core welding.
- For indoor projects, MIG welding is a solid choice.
What Type of Metal Are You Welding?
- For thick materials, flux core welding offers better penetration.
- For thin materials, MIG welding provides better control.
What’s Your Budget?
- If you’re looking for a cost-effective option, flux core welding may save you money on equipment.
- If you can invest in a full setup, MIG welding offers greater versatility.
Tips for Better Results in Both Methods
No matter which method you choose, here are a few tips to improve your welding results:
- Practice Your Technique: Spend time mastering your travel speed, gun angle, and wire feed settings.
- Use Proper Safety Gear: Always wear a welding helmet, gloves, and protective clothing.
- Prepare Your Surface: Clean your workpiece to remove rust, paint, or oil for better weld quality.
- Check Your Equipment: Regularly inspect your welding machine, gun, and wire for any issues.
Experience with Both Methods
I’ve used both flux core and MIG welding in a variety of projects. I’ve found that flux core welding is unbeatable for outdoor jobs and quick repairs. It’s saved me a ton of hassle when I didn’t have access to shielding gas or when working on thick materials.
On the other hand, MIG welding is my go-to for projects requiring precision and a clean finish. I’ve used it extensively for automotive work and light fabrication, and it never fails to deliver professional results.
Choosing the right method really comes down to the specifics of your project and your working environment.
Conclusion
When it comes to flux core welding vs MIG welding, there’s no one-size-fits-all answer. Both methods have their strengths, and the right choice depends on your project’s requirements.
Flux core welding is perfect for outdoor and heavy-duty applications, while MIG welding shines in indoor environments and projects requiring precision. If you’re just starting out, try experimenting with both methods to see which one suits your style and needs.
Mastering both techniques will give you the flexibility to tackle a wide range of welding tasks with confidence.
FAQs
Can I use flux core welding indoors?
Yes, but ensure good ventilation to deal with the fumes produced during welding.
Is flux core welding easier than MIG welding?
Flux core welding is more forgiving on dirty surfaces, but MIG welding is easier for beginners due to cleaner welds and simpler setup.
Which welding method is better for aluminum?
MIG welding is better for aluminum, as flux core welding is not ideal for this material.
Does flux core welding require shielding gas?
No, self-shielded flux core welding does not require shielding gas.
Can I switch between flux core and MIG welding on the same machine?
Yes, many welding machines support both methods, but you may need to adjust the settings and use the appropriate wire.
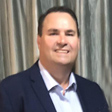
Endow Russel the owner chief editor of giftendow.com . I am a mechanical engineer and assign to an local firm with much experience in welding and industrial equipment.