Arc welding is a popular method for joining metals. It uses electricity to create heat.
This heat melts the metal, allowing it to fuse together. Arc welding offers a reliable way to join different types of metals. It’s widely used in construction, automotive, and manufacturing industries. Understanding how arc welding works can help you appreciate its applications and advantages.
In this blog post, we will explore the basics of arc welding, including the equipment needed and the process involved. You’ll learn about the different types of arc welding and their specific uses. Whether you’re a beginner or just curious, this guide will provide you with valuable insights into the fascinating world of arc welding.
Introduction To Arc Welding
Arc welding is a popular method for joining metals. It uses an electric arc to create heat. This heat melts the metals, allowing them to fuse together. Arc welding is a vital skill in many industries. It is used in construction, automotive, and manufacturing.
History Of Arc Welding
Arc welding has a rich history. It started in the late 1800s. Nikolai Benardos invented the first method. Later, scientists improved the process. They introduced new techniques and materials. These advancements made arc welding more efficient.
Importance In Modern Manufacturing
Arc welding plays a key role in modern manufacturing. It ensures strong, durable bonds between metal parts. This is crucial for building safe structures. It also helps in producing high-quality products. Many industries rely on arc welding for their operations.
Types Of Arc Welding
Understanding the different types of arc welding is crucial for anyone diving into the world of metalwork. Each type has its own unique set of benefits and is suited for different applications. In this section, we will explore four common types of arc welding: Shielded Metal Arc Welding (SMAW), Gas Metal Arc Welding (GMAW), Flux-Cored Arc Welding (FCAW), and Gas Tungsten Arc Welding (GTAW). Let’s dive in and see what makes each type unique and how they work.
Shielded Metal Arc Welding (smaw)
Shielded Metal Arc Welding, often known as stick welding, is one of the simplest and most common types of welding. It uses an electric current to create an arc between the metal and a consumable electrode covered with a flux. The heat generated by the arc melts the metal and the electrode, forming a weld pool. The flux coating on the electrode melts and creates a shielding gas that protects the weld from contamination.
Pros:
- Portable and versatile.
- Works well outdoors and in windy conditions.
- Can weld dirty or rusty metals.
Cons:
- Requires frequent electrode replacement.
- Produces slag that needs to be chipped off.
- Not as clean as other methods.
Gas Metal Arc Welding (gmaw)
Gas Metal Arc Welding, also known as MIG (Metal Inert Gas) welding, uses a continuous wire feed as an electrode and a shielding gas to protect the weld from contamination. This method is popular for its speed and ease of use, making it a favorite in industrial settings.
Pros:
- Faster welding process.
- Produces clean and high-quality welds.
- Easy to learn and use.
Cons:
- Not suitable for outdoor use due to wind affecting the shielding gas.
- Requires a gas cylinder and additional equipment.
- Higher initial setup cost.
Flux-cored Arc Welding (fcaw)
Flux-Cored Arc Welding is similar to GMAW but uses a special tubular wire filled with flux. This makes it highly versatile and suitable for various applications, including heavy-duty welding. There are two types of FCAW: self-shielded and gas-shielded.
Pros:
- Can be used outdoors and in windy conditions.
- High deposition rate and deeper penetration.
- Suitable for thick materials.
Cons:
- Produces more smoke and fumes.
- Can be more complex to learn.
- Requires additional cleaning due to slag.
Gas Tungsten Arc Welding (gtaw)
Gas Tungsten Arc Welding, also known as TIG (Tungsten Inert Gas) welding, uses a non-consumable tungsten electrode to produce the weld. An inert gas, usually argon, is used to protect the weld area from contamination. This method is known for its precision and is often used in industries where weld quality is critical.
Pros:
- Produces high-quality, clean welds.
- Can weld a variety of metals, including aluminum and stainless steel.
- Allows for greater control over the weld.
Cons:
- Slower process compared to other methods.
- Requires a high level of skill and practice.
- Higher equipment cost.
Essential Equipment
Understanding the essential equipment for arc welding is crucial for beginners. Each piece of equipment plays a vital role in the welding process. Let’s explore the key components you need for successful arc welding.
Welding Machine
The welding machine is the heart of the arc welding process. It generates the electric current needed for welding. There are different types of welding machines. Some are designed for specific welding tasks. Choose the right machine based on your welding needs. Ensure it has the correct voltage and amperage. A good welding machine ensures a stable arc and quality welds.
Electrodes
Electrodes are essential for creating the weld. They conduct the electric current from the welding machine to the metal. There are two main types of electrodes: consumable and non-consumable. Consumable electrodes melt during welding, adding material to the weld. Non-consumable electrodes do not melt. They are used in welding processes like TIG welding. Select the right electrode for your welding task. The choice depends on the type of metal and the welding process.
Protective Gear
Welding involves high temperatures and bright light. Protective gear is necessary for safety. A welding helmet protects your eyes and face from sparks and UV rays. Welding gloves guard your hands from burns and heat. Wear a welding jacket to shield your body from sparks. Safety boots protect your feet from falling objects and hot metal. Always use protective gear to stay safe while welding.
Basic Techniques
Understanding the basic techniques of arc welding is crucial for beginners. It helps create stronger welds and ensures safety. Let’s dive into the core steps involved in this process.
Setting Up The Workspace
Start by preparing a clean, well-ventilated area. Remove any flammable materials. Use a sturdy workbench to hold your materials. Ensure you have proper lighting. This helps you see the weld clearly.
Wear protective gear like gloves, a welding helmet, and a long-sleeved jacket. This keeps you safe from sparks and UV radiation. Check your welding machine’s connections. Make sure all cables are securely attached. Set the machine to the correct settings based on the material you are welding.
Striking An Arc
To begin welding, strike an arc. Gently tap the electrode on the material. Lift it slightly to create a spark. This starts the arc. Maintain a short distance between the electrode and the material. This keeps the arc stable and hot.
If the arc goes out, try striking again. Practice makes perfect. Keep a steady hand. Avoid shaking or sudden movements. Consistency helps produce clean welds.
Maintaining Arc Stability
Maintaining a stable arc is key. Hold the electrode at a consistent angle. Usually around 15 degrees. Move it steadily along the weld path. Keep a constant speed. This ensures even heating and a smooth weld.
Watch the weld pool closely. Adjust your speed if needed. If the pool gets too big, move faster. If it gets too small, slow down. A stable arc creates a strong, clean weld. Always monitor your progress. Make adjustments as necessary. This ensures the best results.
Advanced Techniques
Mastering arc welding requires more than basic skills. Advanced techniques elevate the quality and precision of your work. These methods help welders tackle complex projects with ease and efficiency. Let’s explore some key advanced techniques in arc welding.
Weaving Patterns
Weaving patterns in arc welding improve weld quality. They provide better control over the weld pool. Common patterns include zigzag, circular, and triangular. Zigzag patterns help in filling wide gaps. Circular patterns work best for thin metals. Triangular patterns offer strong welds for thicker materials.
Vertical And Overhead Welding
Vertical and overhead welding are challenging positions. These techniques require steady hands and precise control. In vertical welding, move the electrode upward or downward. For upward, keep the angle between 5 to 15 degrees. In downward, use a faster travel speed.
Overhead welding needs patience and practice. Ensure a short arc length. This prevents molten metal from dripping. Use a weaving motion for better control. Maintain a consistent speed for a uniform weld.
Backhand And Forehand Techniques
Backhand and forehand techniques refer to the direction of welding. In the backhand technique, the electrode points away from the weld. This method offers deeper penetration. It’s ideal for thick materials.
In the forehand technique, the electrode points towards the weld. This method creates a wider and shallower weld. It works well for thin materials. Use the right technique based on the material thickness. This ensures strong and clean welds.

Credit: www.youtube.com
Common Challenges
Arc welding is a fascinating process that joins metals using electricity. But as intriguing as it sounds, it’s not without its hurdles. Welding can be tricky, especially for beginners. Here, we’ll dive into some of the most common challenges welders face and how to overcome them. Whether you’re a novice or have some experience, this guide will help you get smoother welds.
Dealing With Spatter
Spatter occurs when small molten metal drops fly off during welding. This can make your work look messy and can be a nuisance to clean up. So, how do you deal with spatter?
- Adjust Your Settings: Incorrect voltage or amperage can cause excessive spatter. Make sure your machine settings are correct for the material and thickness you’re welding.
- Use Anti-Spatter Spray: This is a quick fix. Spray it on your workpiece before welding to make cleaning up easier.
- Maintain Your Equipment: Dirty or worn-out nozzles and contact tips can increase spatter. Regular maintenance is key.
Preventing Cracks
Cracks in your welds can weaken the joint, making it less reliable. Here are some tips to prevent cracks:
- Preheat Your Metal: Especially for thicker materials, preheating can reduce the risk of cracks.
- Use the Right Filler Material: Choosing a filler that matches your base metal can help prevent cracking.
- Control Your Cooling Rate: Let your welds cool down slowly to avoid stress that can cause cracks.
Managing Heat Input
Too much heat can warp your metal, while too little can result in weak welds. Managing heat input is crucial for a good weld. Here’s how:
- Adjust Travel Speed: Moving too slowly can cause overheating. Find a steady, moderate pace.
- Use Proper Technique: Techniques like weaving or stringer beads can help manage heat distribution.
- Monitor Your Weld Pool: Keep an eye on the size of your weld pool. A too large pool indicates too much heat.
Welding is as much an art as it is a science. While these challenges can be daunting, with practice and the right approach, you can overcome them. Remember, even the best welders started somewhere. Keep experimenting, learning, and perfecting your craft!
Safety Precautions
Arc welding is a powerful technique. Safety must be a top priority. This ensures protection from potential hazards. Follow these precautions to stay safe.
Personal Protective Equipment
Wearing the right gear is crucial. Use a welding helmet to protect your eyes and face. Gloves shield your hands from heat and sparks. Wear a long-sleeve shirt and pants. This covers your skin from burns. Steel-toed boots provide foot protection. They guard against heavy objects falling.
Ventilation And Fume Control
Welding produces harmful fumes. Ensure good ventilation in the workspace. Use exhaust fans to remove toxic gases. Consider a fume extractor for better control. A respirator mask can also help. It filters out dangerous particles.
Fire Safety
Welding sparks can start fires. Keep flammable materials away from the work area. Have a fire extinguisher nearby. Inspect your surroundings for fire hazards. Always stay alert and prepared. Safety first.
Applications Of Arc Welding
Arc welding is a versatile and powerful technique that is used in many industries. Whether building towering skyscrapers or crafting the latest automobiles, this method is highly valued for its efficiency and strength. Let’s dive into how arc welding is applied in various sectors.
Construction Industry
In the construction industry, arc welding is a cornerstone. Picture a gigantic skyscraper; its steel framework holds everything together, and arc welding plays a pivotal role in ensuring those joints are solid and reliable. The process is used to fuse beams, columns, and reinforcement bars, creating the skeleton of buildings. This robust technique withstands immense weight and stress, ensuring the safety and durability of structures.
Moreover, arc welding is employed in the construction of bridges, roads, and tunnels. It helps create strong connections that can handle the stress of heavy traffic and environmental factors. For instance, when building a bridge, welders join large steel sections together seamlessly, ensuring they can support tons of weight and resist natural forces like wind and water.
Automotive Industry
Have you ever wondered how your car is put together? Arc welding is a key player in the automotive industry. From the chassis to the exhaust system, this method is used to join various metal components. The precision of arc welding ensures that every part fits perfectly, providing the strength needed to withstand daily wear and tear.
Arc welding is also crucial in manufacturing heavy-duty vehicles like trucks and buses. These vehicles need to be strong and reliable, and arc welding helps achieve that by creating durable joints. Additionally, the technique is used in repairing vehicles, making it easier to replace damaged parts and extend the life of the vehicle.
Shipbuilding
Shipbuilding is another industry where arc welding shines. Imagine a massive ship cruising through the ocean; its hull must be incredibly strong to withstand the harsh marine environment. Arc welding is employed to join thick steel plates, ensuring the vessel’s structural integrity. This process helps create ships that are not only strong but also watertight, preventing leaks and ensuring safety at sea.
Furthermore, arc welding is used in building various parts of the ship, from the deck to the engine room. The technique ensures that all parts are securely connected, providing the strength needed to navigate rough waters. In ship repair, arc welding is invaluable for fixing damaged sections, allowing ships to return to service quickly and efficiently.
In conclusion, arc welding is a critical technique across multiple industries. Its applications range from constructing skyscrapers to building reliable vehicles and ships. The strength and precision it provides make it an indispensable tool in modern manufacturing and construction.
Future Of Arc Welding
The future of arc welding holds great promise. As technology advances, new methods and tools are emerging. These changes are making the process more efficient and sustainable. Let’s explore the technological advances, sustainability considerations, and industry trends shaping the future of arc welding.
Technological Advances
Robotics and automation are transforming arc welding. Machines can now perform tasks with high precision. This reduces errors and increases productivity. Welders are using advanced software to control welding parameters. This ensures consistency and quality in every weld. Augmented reality (AR) is also making its way into training. Trainees can practice welding in a virtual environment. This reduces material waste and enhances learning.
Sustainability Considerations
Reducing environmental impact is a key focus. New welding techniques use less energy. This helps lower carbon footprints. There is a shift towards eco-friendly materials. These materials produce fewer emissions. Recycling and reusing metal scraps are becoming common practices. This minimizes waste and conserves resources. Sustainable practices in arc welding not only help the planet but also reduce costs.
Industry Trends
The demand for skilled welders is growing. As industries expand, the need for quality welding increases. There is a trend towards continuous learning. Welders are updating their skills to keep up with new technologies. Safety is a top priority. Enhanced protective gear and safety protocols are being implemented. This ensures a safer working environment. Certification programs are gaining importance. They validate a welder’s skills and knowledge.
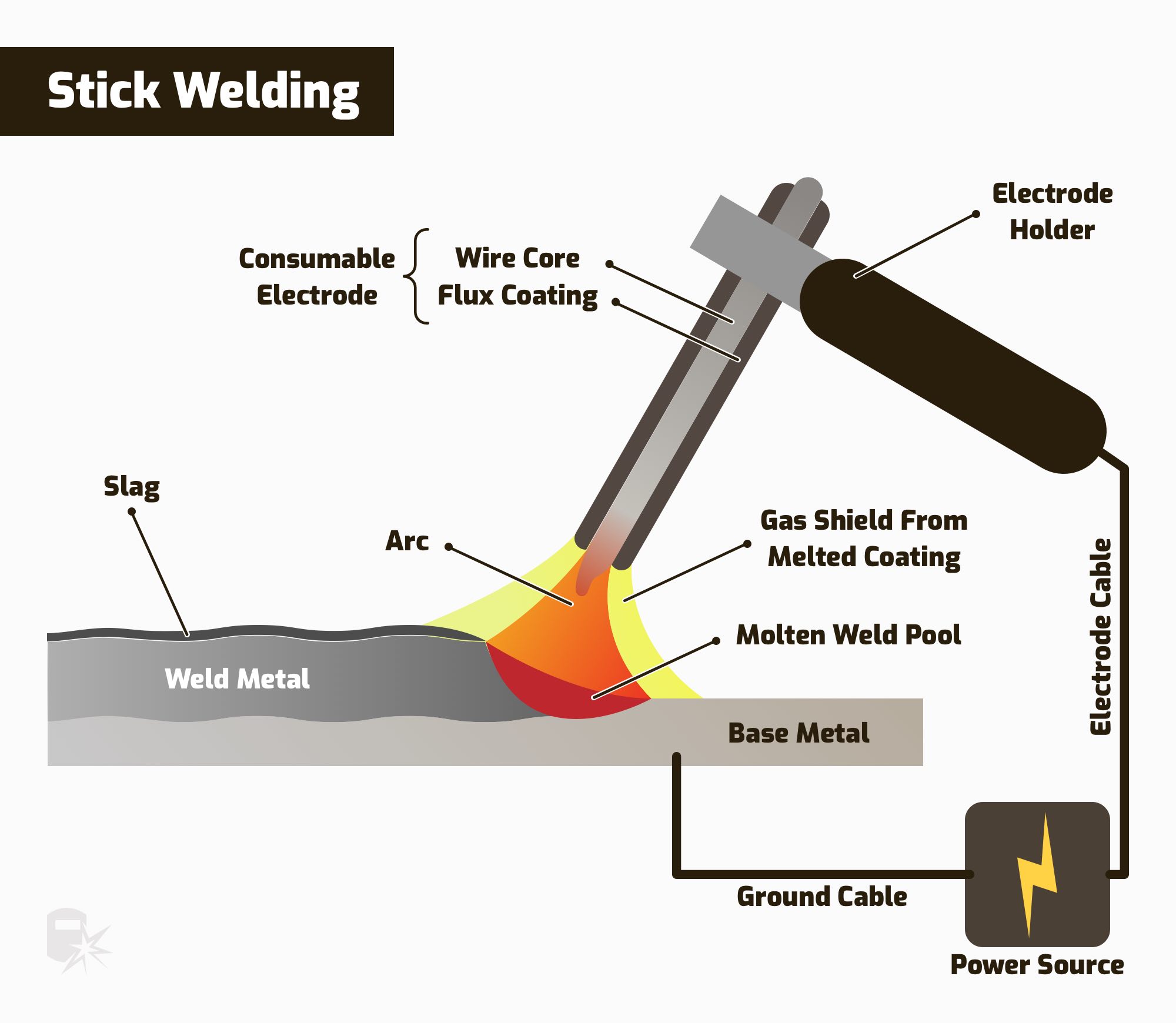
Credit: weldguru.com
Credit: science.howstuffworks.com
Frequently Asked Questions
Is Arc Welding Stronger Than Mig?
Arc welding generally produces stronger welds than MIG welding. It offers deeper penetration and better fusion for thicker materials.
What Are The 4 Basic Steps To Perform Arc Welding?
The 4 basic steps to perform arc welding are: 1. Prepare the metal surfaces. 2. Strike the arc. 3. Maintain the correct arc length. 4. Move the electrode steadily along the joint.
What Is An Arc Welder And How Does It Work?
An arc welder is a device that joins metals using electricity. It creates an electric arc between the electrode and metal. The arc generates intense heat, melting the metals at the welding point. This process fuses the metals together, forming a strong joint.
How Does Welding Work Step By Step?
Welding joins materials using heat and pressure. First, clean the surfaces. Next, align materials. Then, apply heat and filler. Finally, cool the weld.
Conclusion
Understanding how arc welding works can open doors to new opportunities. This technique is essential in many industries. It involves using an electric arc to join metals. Safety is crucial, so always wear protective gear. With practice, you can improve your welding skills.
Remember to maintain your equipment for the best results. Arc welding is both an art and a science. Keep learning and stay curious. Happy welding!