Calculating welding thickness is crucial for strong and safe welds. Accurate measurements ensure durability and prevent failures.
Understanding how to calculate welding thickness can seem complex. But it’s essential for quality welding projects. By learning the right techniques, you can achieve precise measurements. This not only enhances the strength of the weld but also ensures safety. In this guide, we’ll break down the process into simple steps.
We’ll cover the basic principles and tools you need. Whether you’re a beginner or experienced, this information will help you. Let’s dive in and simplify the calculation of welding thickness.
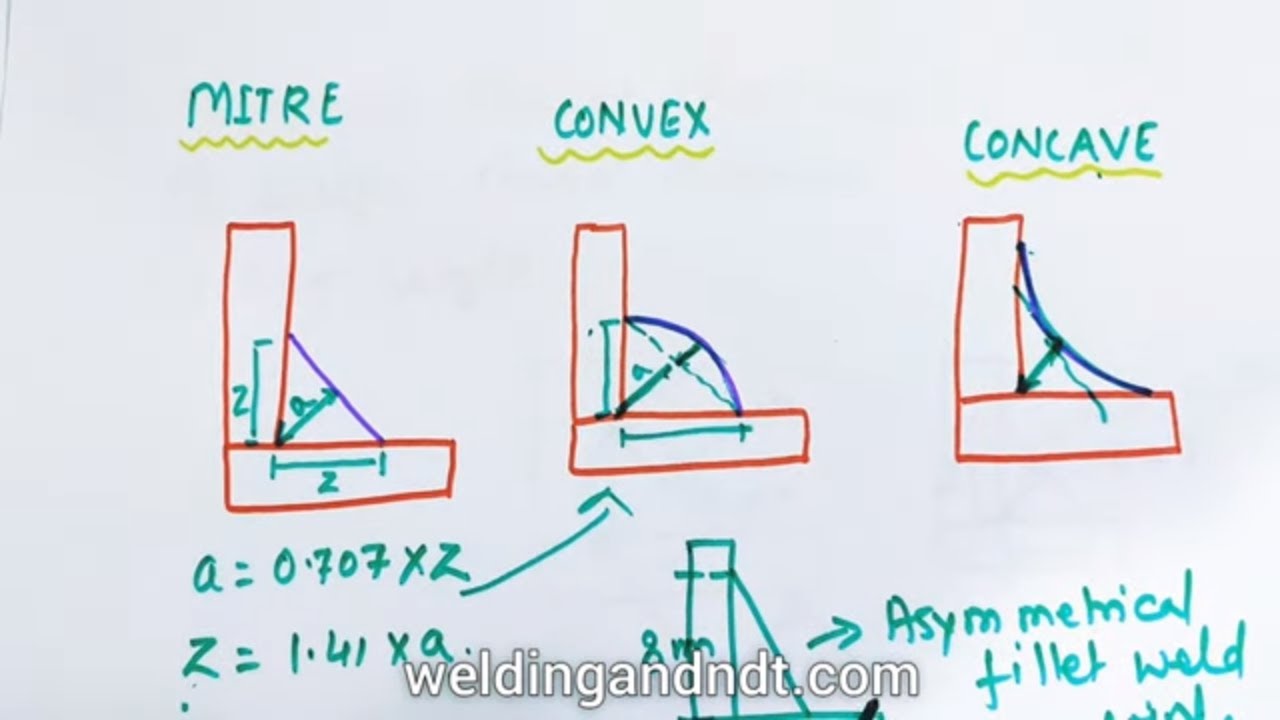
Credit: www.youtube.com
Introduction To Welding Thickness
Understanding welding thickness is crucial in welding. It ensures strong and durable welds. Welding thickness refers to the thickness of the material being welded. This can affect the welding process and the final product.
Importance In Welding
The thickness of the material impacts the welding technique used. Thicker materials need more heat and longer welding times. Incorrect thickness measurements can lead to weak welds or material damage. The right welding thickness ensures the weld’s strength and longevity. It also helps in selecting the right welding equipment and settings.
Common Applications
Welding thickness is important in many industries. In construction, it ensures the stability of structures. In automotive, it affects vehicle safety and performance. Shipbuilding uses precise welding thickness for durable ships. Even in art, welding thickness helps in creating strong sculptures. Each application needs accurate welding thickness for the best results.
Factors Affecting Welding Thickness
Calculating welding thickness involves various factors. These factors determine the quality and durability of the weld. Understanding these factors can help achieve the desired welding results. Let’s dive into two main factors: material type and joint design.
Material Type
The type of material affects welding thickness. Different materials have different properties. For example, steel and aluminum require different welding techniques. Steel is strong but needs more heat. Aluminum is softer and melts quickly. Knowing the material helps in setting the correct thickness. This ensures a strong and durable weld.
Joint Design
Joint design is another crucial factor. The way materials join affects the weld thickness. Common joint types include butt joints, lap joints, and T-joints. Butt joints need precise thickness for proper fusion. Lap joints may require more thickness for extra strength. T-joints usually need thicker welds to bear stress. Proper joint design ensures a secure and lasting weld.
Measuring Tools And Equipment
Measuring welding thickness accurately is crucial for ensuring the integrity and quality of welds. Different tools and equipment help achieve precise measurements. This section explores some of the key measuring tools used in welding thickness calculation.
Calipers
Calipers are versatile measuring instruments that come in various types. They can measure the internal and external dimensions of a welded joint. Digital calipers provide precise readings and are easy to use. They are suitable for measuring thin and thick welds alike.
To use calipers, place the jaws on the weld. Make sure to align them properly. Read the measurement displayed on the digital screen or the scale. This method is simple and effective for quick checks.
Ultrasonic Thickness Gauges
Ultrasonic thickness gauges are advanced tools for measuring weld thickness. They use sound waves to gauge the thickness of materials. This non-destructive method ensures the weld’s structural integrity remains intact.
These gauges work by sending ultrasonic pulses through the weld. The device then measures the time taken for the pulses to bounce back. The gauge displays the thickness reading based on this time.
Ultrasonic thickness gauges are highly accurate. They can measure thickness through coatings and rust. This makes them ideal for industrial applications where precision is key.
Calculating Welding Thickness
Calculating welding thickness is essential for a strong, durable weld. It helps ensure the structural integrity of the welded piece. Knowing the correct welding thickness can prevent costly mistakes and rework.
Basic Formulae
Welding thickness calculation starts with some basic formulae. The thickness (T) of the weld is generally determined by the thickness of the thinner material being joined. A common formula is:
T = 0.7 x Thickness of the Thinner Material
This formula assumes a fillet weld. Different weld types may use other formulae. Always refer to welding standards for specific requirements.
Practical Examples
Let’s look at a practical example. If you are welding two pieces, one 6mm and the other 8mm:
In this case, the welding thickness should be 4.2mm. This ensures a proper weld without over-penetration.
Another example involves welding two plates, each 10mm thick. The calculation would be:
This ensures that the weld is robust and meets the required standards.
Techniques For Accurate Measurement
When it comes to welding, ensuring the right thickness is crucial for the strength and durability of your welds. Accurately measuring the thickness can be a bit tricky, but using the right techniques will make it easier. In this section, we’ll explore some effective methods for measuring welding thickness. Let’s dive in!
Visual Inspection
Visual inspection is one of the simplest and most straightforward methods for measuring welding thickness. By just looking at the weld, you can get a good estimate of its thickness. Of course, this method relies heavily on your experience and trained eye.
- Surface Finish: Check the surface finish of the weld. A smooth, consistent bead usually indicates a uniform thickness.
- Bead Width: Measure the width of the bead. A wider bead often means a thicker weld.
- Overlapping Layers: Look for overlapping layers which might suggest multiple passes and increased thickness.
While visual inspection is quick and easy, it’s not the most precise method. However, it’s a good starting point before moving on to more accurate techniques.
Non-destructive Testing
Non-destructive testing (NDT) methods are excellent for accurately measuring welding thickness without damaging the weld. These techniques are more precise and reliable than visual inspection.
- Ultrasonic Testing (UT): This method uses high-frequency sound waves to measure the thickness. The sound waves travel through the weld and reflect back, giving you an accurate thickness measurement.
- Radiographic Testing (RT): X-rays or gamma rays are used to create an image of the weld. By examining the image, you can determine the thickness and identify any internal flaws.
- Magnetic Particle Testing (MT): This method involves applying a magnetic field to the weld and then sprinkling magnetic particles on it. The particles will gather around any irregularities, helping you gauge thickness and detect defects.
Although NDT methods are more complex and require specialized equipment, they provide the most accurate and detailed measurements. This makes them invaluable for critical welding applications.
In conclusion, choosing the right technique for measuring welding thickness depends on your specific needs and resources. Whether you rely on a keen eye or sophisticated technology, ensuring accurate measurements is key to creating strong and reliable welds. So, what’s your go-to method for measuring welding thickness? Share your thoughts in the comments below!
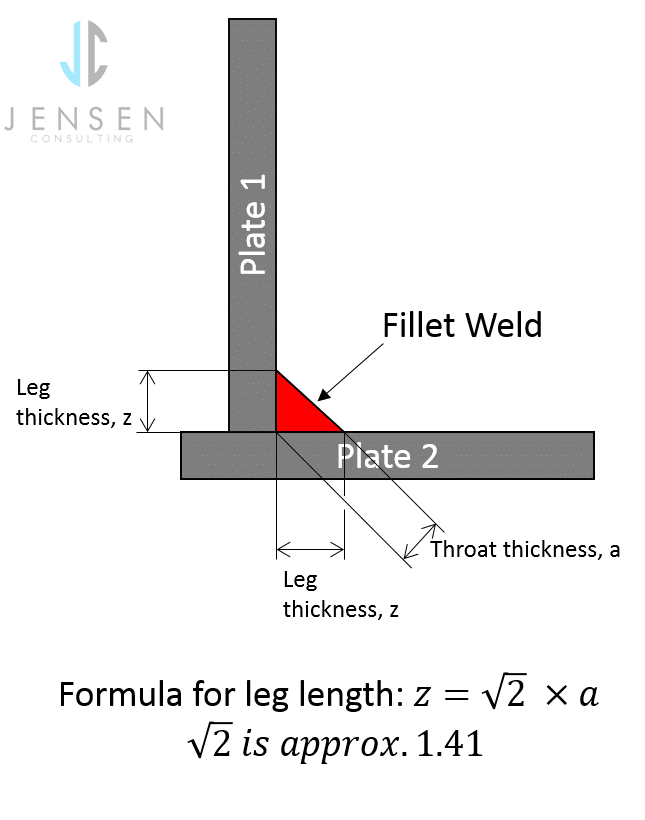
Credit: restoric.co.uk
Common Challenges And Solutions
Calculating welding thickness can be tricky. There are many challenges you might face, but don’t worry! We have some solutions to help you out. Let’s dive into two common challenges and how to overcome them.
Dealing With Irregular Surfaces
Irregular surfaces can be a real headache when welding. Imagine trying to weld on a bumpy or uneven surface. It’s like trying to walk on a tightrope with roller skates! Here are some tips to make it easier:
- Surface Preparation: Make sure the surface is clean and smooth. Remove any dirt, rust, or old paint. A clean surface helps the weld stick better.
- Use Fillers: If the surface is too uneven, use fillers to level it out. This gives you a more even surface to work on.
- Adjust Welding Parameters: Sometimes, you need to adjust the heat or the speed of your welding. This helps you get a better weld, even on tricky surfaces.
Remember, patience is key. Take your time to prepare the surface and adjust your settings. It’ll make a big difference in the end.
Ensuring Consistency
Consistency in welding is essential. Think of it like baking a cake. You need the right ingredients and the right method to get a perfect cake every time. Here’s how you can ensure consistency:
- Maintain Equipment: Regularly check and maintain your welding equipment. Clean the nozzles, check the gas flow, and make sure everything is in good working order.
- Follow Procedures: Stick to the welding procedures. Use the right techniques and follow the guidelines for the materials you are working with.
- Practice: Like any skill, practice makes perfect. The more you weld, the better you get at maintaining consistency.
Consistency might seem hard at first, but with practice and attention to detail, you’ll get there. Keep tweaking your approach until you find what works best for you.
By tackling these common challenges head-on, you can improve your welding skills and ensure accurate thickness calculations. Happy welding!
Expert Tips For Precision
Calculating welding thickness is a critical skill for welders. Precision in this task ensures the strength and durability of the weld, which is essential for safety and quality. Below, we share expert tips that can help you achieve precise measurements, making your welding projects more reliable and professional.
Pre-measurement Preparation
Before you even think about measuring, make sure everything is in place. A clean workspace is not just a tidy one; it’s vital for accurate readings. Dust, debris, or oil can throw off measurements, making your hard work unreliable.
- Clean the Surface: Use a clean, dry cloth to wipe the area where you will measure.
- Check for Defects: Inspect the weld for any visible defects like cracks or bubbles.
- Gather Your Tools: Ensure you have all the necessary instruments within reach.
Think about it: Would you trust a chef who cooks in a dirty kitchen? The same principle applies here. Clean and prep your workspace for the best results.
Calibration Of Instruments
Even the best tools need a little TLC to function at their best. Calibration ensures that your instruments are providing accurate readings. This step is crucial and, fortunately, straightforward.
- Read the Manual: Every instrument is different, so start by reading the instructions.
- Use Calibration Blocks: These blocks have known measurements, allowing you to adjust your tools accordingly.
- Regular Checks: Make it a habit to calibrate your tools regularly, especially if they are used frequently.
It’s like tuning a guitar before a performance. A small adjustment can make a big difference in the quality of your work.
By following these expert tips, you’ll be well on your way to achieving precise welding thickness calculations. Remember, precision not only improves the quality of your welds but also ensures the safety and longevity of your projects.
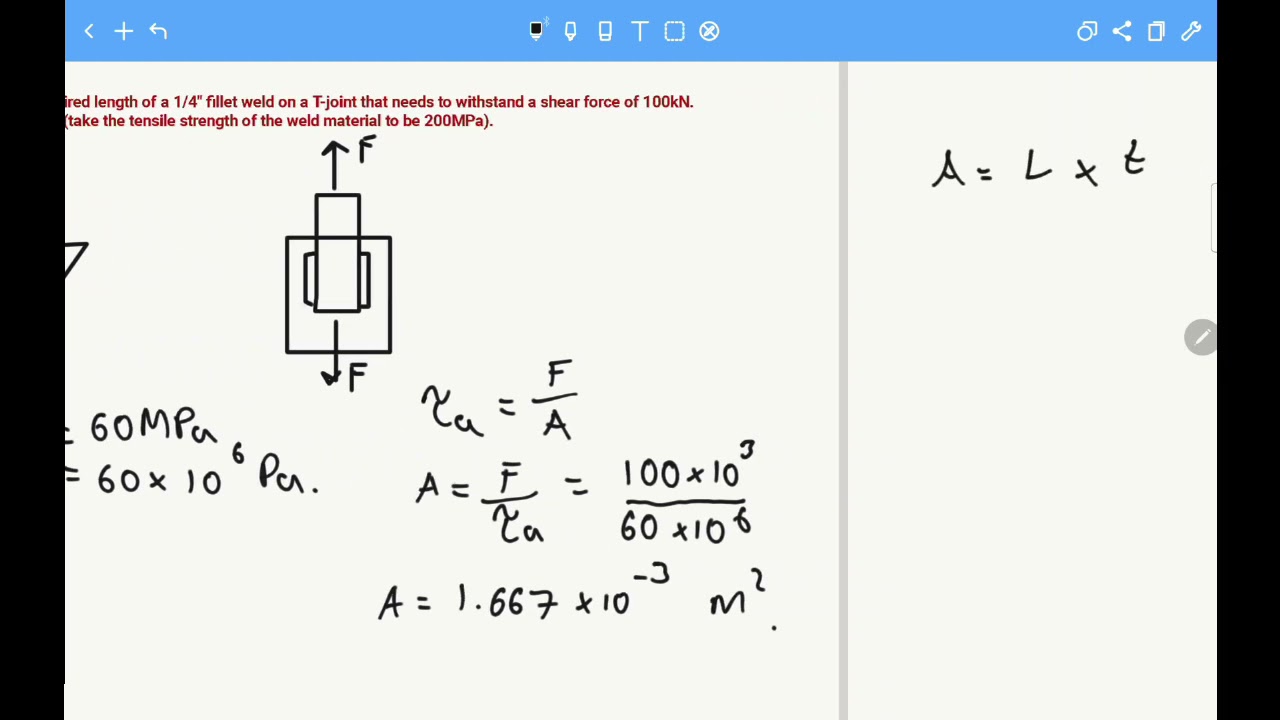
Credit: www.youtube.com
Advanced Techniques And Innovations
In the world of welding, precision is everything. Calculating the thickness of welds is a crucial step in ensuring the strength and durability of a structure. However, with the advancement of technology, the methods of measuring welding thickness have evolved significantly. Let’s delve into some advanced techniques and innovations that have revolutionized this process.
Laser Scanning
Laser scanning is a cutting-edge technique that has transformed the way we measure welding thickness. This method uses laser beams to capture detailed images of the weld surface. The laser scanner emits a beam of light that reflects off the weld, creating a precise 3D model. This 3D model provides accurate measurements of the weld’s dimensions, including its thickness.
Why is this method so effective? Here are a few reasons:
- Accuracy: Laser scanning provides highly accurate measurements, reducing the margin of error.
- Speed: The process is fast, allowing for real-time analysis and adjustments.
- Non-Contact: Since the method is non-contact, it prevents any damage to the weld.
Imagine trying to measure a weld manually with a caliper. It’s time-consuming and prone to human error. But with laser scanning, the process is streamlined and precise. It’s like having a high-tech assistant that ensures your welds are always spot on.
Computer-aided Measurement
Another innovative technique in calculating welding thickness is computer-aided measurement. This method leverages advanced software to analyze welding parameters and provide accurate thickness measurements. The software processes data from various sensors and instruments, creating a comprehensive profile of the weld.
Here’s how computer-aided measurement stands out:
- Integration: The software integrates data from different sources, providing a holistic view.
- Precision: It offers precise measurements, ensuring the weld meets the required standards.
- Automation: The process is automated, reducing the need for manual intervention.
Think of it as having a digital toolkit that does all the heavy lifting for you. No more squinting at tiny numbers or second-guessing your measurements. Instead, you get a clear, accurate report that you can rely on. Plus, the software can store and analyze historical data, helping you track and improve your welding processes over time.
Both laser scanning and computer-aided measurement are game-changers in the welding industry. They bring a level of accuracy and efficiency that was previously unimaginable. So, if you’re looking to step up your welding game, these advanced techniques are worth exploring. After all, in welding, as in life, precision is key!
Real-world Applications And Case Studies
Ever wondered how welding thickness is calculated in real-world settings? It’s not just theory; it’s a crucial part of many industries. To make it easy for you, we’ve compiled some industrial examples and success stories. Let’s dive into how this knowledge is applied in everyday scenarios.
Industrial Examples
In industries like construction, manufacturing, and automotive, calculating welding thickness is essential. Here’s a closer look:
- Construction: Buildings and bridges need strong welds. Engineers calculate welding thickness to ensure safety and stability. Imagine a skyscraper; the welds must support tons of weight!
- Manufacturing: Factories producing machinery use precise welding techniques. Incorrect welding thickness can lead to machine failure. Think about the assembly lines – they need to run smoothly without breakdowns.
- Automotive: Cars and trucks rely on strong welds for safety. Welding thickness affects the durability of vehicles. Consider the welds in a car’s chassis; they must withstand vibrations and impacts.
Success Stories
Let’s look at some success stories where proper welding thickness calculation made a big difference:
- Bridge Construction: In 2010, a bridge in a busy city was constructed using calculated welding thickness. This made the bridge not only strong but also long-lasting. The engineers avoided potential disasters by ensuring the welds could handle heavy traffic.
- Factory Machinery: A manufacturing plant reduced downtime by 30% thanks to precise welding calculations. The machinery worked efficiently without unexpected failures, boosting production and saving costs.
- Vehicle Safety: An automotive company improved the crash-test ratings of their cars. By calculating the right welding thickness, they enhanced the safety features, giving buyers more confidence in their vehicles.
These examples show how important welding thickness is in real-world applications. Proper calculations lead to safer, more reliable structures and products. Isn’t it amazing how something so technical can have such a big impact?
Conclusion And Best Practices
Calculating welding thickness is crucial for ensuring structural integrity and safety. Knowing the best practices helps in achieving precise measurements and maintaining quality. This section summarizes key points and explores future trends in welding measurement.
Summary Of Key Points
Understanding material properties is essential for accurate thickness calculations. Always use the correct tools and techniques for measurement. Regular calibration of equipment ensures reliable results. Safety should always be the top priority. Documenting measurements helps in tracking progress and identifying potential issues.
Future Trends In Welding Measurement
Technological advancements continue to improve welding measurement techniques. Automated systems are becoming more popular. These systems reduce human error and increase efficiency. Augmented reality (AR) tools are also emerging. These tools provide real-time data and visual guidance during the welding process. Expect more integration of AI in welding measurements. AI can analyze data faster and provide actionable insights.
Frequently Asked Questions
What Is The Rule For Weld Thickness?
Weld thickness depends on the material type and application. Generally, it should match the thickness of the thinner part being joined.
What Is The Formula For Welding Calculation?
The formula for welding calculation is: Heat Input (kJ/mm) = (Voltage x Current x 60) / (Travel Speed x 1000). Ensure units are consistent.
How Do You Calculate Coating Thickness?
Use a coating thickness gauge to measure coating thickness. Place the gauge on the coated surface for a reading. Ensure the gauge is calibrated for accurate results.
How Do You Calculate Thickness?
Measure thickness using a caliper or micrometer. Place the object between the device’s jaws and read the measurement.
Conclusion
Calculating welding thickness ensures strong and safe welds. Always use proper tools for measurement. Follow industry guidelines closely. This will help maintain quality. Practice regularly to improve your skills. Accurate welding thickness leads to better results. Stay updated with latest techniques.
Seek advice from experienced welders when needed. Welding safely and effectively is crucial. Now, you’re ready to apply your knowledge. Happy welding!