Calculating welding time is crucial for planning and cost estimation. It ensures efficiency and helps in resource management.
Welding projects often demand precision and careful time allocation. Knowing how long a welding job will take can make a huge difference. It impacts project deadlines, labor costs, and overall productivity. Whether you’re a beginner or a seasoned welder, understanding the factors that influence welding time is essential.
From the type of weld to the material thickness, various elements play a role. This guide will walk you through the steps to calculate welding time accurately. You’ll learn to consider each variable and use simple formulas to estimate the duration of your welding tasks. Ready to dive in? Let’s explore the process of calculating welding time.
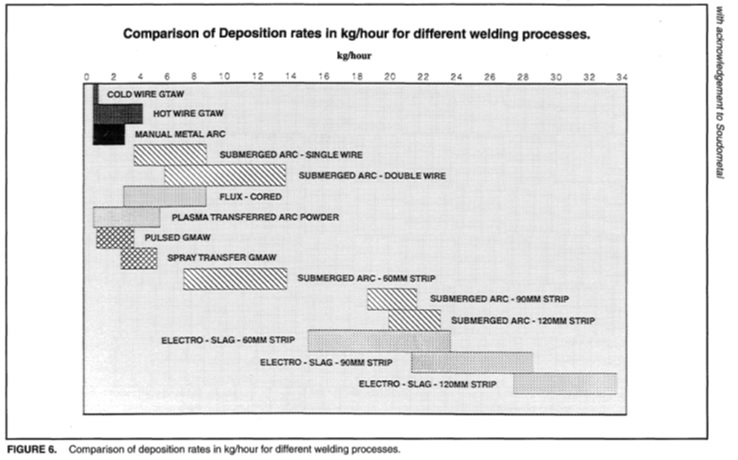
Credit: www.welderdestiny.com
Factors Influencing Welding Time
Welding is a skilled craft that requires precise calculation and understanding of various elements. When calculating welding time, several factors come into play. These factors can significantly affect the overall time required to complete a welding project. Let’s delve into some of these key factors.
Material Type
The type of material being welded plays a crucial role in determining welding time. Some materials are easier to weld than others. For instance, aluminum and stainless steel have different welding characteristics. Aluminum, being a softer metal, tends to require less welding time compared to stainless steel, which is known for its durability and strength.
Moreover, different materials react differently to heat. Metals like copper and brass conduct heat rapidly, which can impact the welding time. On the other hand, metals like titanium require specific welding techniques and can be more time-consuming.
Thickness Of The Material
The thickness of the material is another significant factor. Thicker materials generally take more time to weld because they require more heat and multiple passes to ensure a strong weld. In contrast, thinner materials can be welded more quickly but require careful handling to avoid burn-through.
Here’s a quick comparison:
Material Thickness | Welding Time |
---|---|
Thin (1-3mm) | Shorter Time |
Medium (4-6mm) | Moderate Time |
Thick (7mm+) | Longer Time |
Welding Position
Believe it or not, the position in which you weld can make a big difference. Welding in a flat position is generally faster and easier compared to vertical or overhead positions. Gravity is on your side when welding flat, making it easier to control the molten metal.
When welding in more challenging positions, like vertical or overhead, it can be more time-consuming. The welder needs to be more precise and cautious to ensure a strong and clean weld.
Type Of Welding Process
Lastly, the type of welding process used can significantly influence the welding time. Different welding processes, such as MIG (Metal Inert Gas), TIG (Tungsten Inert Gas), and Stick Welding, have varying speeds and complexities.
- MIG Welding: Generally faster and suitable for thicker materials.
- TIG Welding: Provides high-quality welds but is slower and requires more skill.
- Stick Welding: Versatile but can be slower and less precise than MIG and TIG.
Choosing the right welding process depends on the specific requirements of the project. Each process has its own set of advantages and disadvantages, which can impact the total welding time.
In conclusion, calculating welding time is not a one-size-fits-all approach. By considering these factors—material type, thickness, welding position, and type of welding process—you can better estimate the time needed for your welding project. Happy welding!
Welding Time Calculation Basics
Calculating welding time helps in planning and cost estimation. It involves understanding the welding speed, estimating weld length, and distinguishing between arc time and non-arc time. Let’s break down these basics.
Understanding Welding Speed
Welding speed is how fast the weld progresses. This speed affects the total welding time. It is usually measured in inches per minute (IPM) or millimeters per minute (mm/min). Knowing the welding speed is essential for accurate time calculation.
Weld Length Estimation
Estimate the total length of the weld to be made. This estimation includes all welds in the project. Measuring the distance that needs welding provides a clear picture. This length helps in determining the time needed for welding.
Arc Time Vs. Non-arc Time
Arc time is the actual time spent welding. Non-arc time includes setup, repositioning, and breaks. Both times affect the total welding duration. Understanding the difference helps in more precise time calculation.
Manual Welding Time Calculation
Calculating welding time manually can be quite straightforward. It involves understanding the variables and using the correct formulas. This method is useful for welders who need to estimate job times quickly. Let’s delve into the steps and formulas required for manual welding time calculation.
Steps For Manual Calculation
First, measure the length of the weld. This is the total distance to be welded. Next, determine the welding speed. This is how fast you can weld per unit of time. Then, calculate the time by dividing the weld length by the welding speed. Finally, account for any additional time needed for preparation and finishing tasks.
Common Formulas Used
The basic formula for welding time is:
Welding Time = Length of Weld / Welding Speed
Another formula includes additional factors:
Total Time = Welding Time + Preparation Time + Finishing Time
These formulas help ensure accurate time estimates.
Example Calculations
Let’s say you have a 10-meter weld. If your welding speed is 0.5 meters per minute, the welding time would be:
Welding Time = 10 meters / 0.5 meters per minute = 20 minutes
If preparation and finishing take an extra 10 minutes, the total time would be:
Total Time = 20 minutes + 10 minutes = 30 minutes
By following these steps and using these formulas, you can accurately estimate welding time.

Credit: www.youtube.com
Automated Welding Time Calculation
Have you ever felt like calculating welding time is more complicated than it should be? We’ve all been there. Fortunately, automated welding time calculation can help. With the right tools, you can save time and improve accuracy. Let’s explore how automation can transform your welding process.
Benefits Of Automation
Automating welding time calculations offers several benefits. First, it reduces human error. No more second-guessing your math! Second, it saves time. What used to take hours can now be done in minutes. Third, it provides consistency. Every calculation follows the same process, ensuring uniform results.
- Accuracy: Automated tools minimize errors, ensuring precise calculations.
- Efficiency: Save valuable time and effort, letting the software do the heavy lifting.
- Consistency: Get reliable results every time, with no variations.
Popular Welding Time Calculators
There are several welding time calculators available that can make your life easier. Some of the popular ones include:
- WeldCost: This tool offers detailed cost and time calculations for various welding processes.
- ProWeld: Known for its user-friendly interface, ProWeld is perfect for beginners.
- WeldCalc: A comprehensive tool that caters to both small and large welding projects.
Each of these tools has unique features, so be sure to choose one that fits your specific needs.
How To Use Welding Software
Using welding software may seem daunting at first, but it’s easier than you think. Here’s a simple guide to get you started:
Step | Action |
---|---|
1 | Download and install the software from a trusted source. |
2 | Open the software and select the type of welding process. |
3 | Enter the material details, such as type and thickness. |
4 | Input the welding parameters, like speed and voltage. |
5 | Click ‘Calculate’ to get the welding time. |
And there you have it! With these steps, you can easily calculate welding time and get back to what you do best – welding.
Expert Tips For Accurate Calculation
Calculating welding time accurately can save you money, materials, and effort. It’s an essential skill for anyone working with metal. Let’s explore some expert tips to help you get it right every time.
Choosing The Right Equipment
Picking the right welding equipment is crucial. Using the wrong tool for the job can lead to errors and wasted time. Here’s a quick guide:
- MIG Welders: Great for thin to medium-thickness metals.
- TIG Welders: Ideal for precise work on thin metals.
- Stick Welders: Best for heavy-duty tasks and thicker metals.
Remember, each type of welder has its own settings and capabilities. Choosing the right one can make your calculations more precise.
Regular Maintenance And Calibration
Think of your welding equipment as a car. It needs regular check-ups to keep running smoothly. Here are some maintenance tips:
- Check Connections: Make sure all cables and hoses are secure.
- Clean Regularly: Dust and debris can affect performance.
- Calibrate: Ensure your settings are accurate. Use a calibration tool if necessary.
Regular maintenance not only prolongs the life of your equipment but also ensures that your welding time calculations are on point.
Best Practices For Consistency
Consistency is key in welding. It helps you achieve the same results every time. Here are some best practices:
- Practice: The more you weld, the better you’ll get at estimating time.
- Record Keeping: Keep a log of your welding times for different projects. This can be a valuable reference.
- Standard Procedures: Develop and follow standard procedures for different types of welding jobs.
By following these tips, you’ll ensure that your welding times are consistent and accurate, making your projects more efficient and successful.
Common Challenges And Solutions
Calculating welding time is essential for project planning and cost estimation. Several challenges can affect the accuracy of these calculations. Below, we explore common issues and offer practical solutions.
Dealing With Material Variability
Different materials require different welding times. Some metals heat up faster. Others may need more passes or special techniques. A standard approach won’t work for every material.
Solution: Always check the material specifications. Consult welding guides for accurate time estimates. Test weld a small piece first. Adjust your calculations based on the test.
Managing Environmental Factors
Environmental conditions can impact welding time. Wind, humidity, and temperature play a role. They can affect weld quality and speed.
Solution: Set up a controlled environment. Use wind shields or tents if working outdoors. Adjust your welding speed based on the weather. Always monitor the conditions closely.
Addressing Human Error
Human error is a big factor in welding time calculations. Mistakes in technique can slow down the process. Fatigue and inexperience also contribute.
Solution: Provide proper training. Make sure welders have enough rest. Use checklists to minimize errors. Regularly review and improve welding techniques.
Advanced Techniques
In the evolving world of welding, advanced techniques are pivotal for precision and efficiency. Calculating welding time accurately can save costs and improve productivity. Let’s explore some advanced techniques that can enhance your welding process.
Using Welding Simulations
Welding simulations allow for detailed planning and analysis. These tools enable you to visualize the weld before actual work starts. You can adjust parameters and see the impact on welding time. This method reduces trial and error. It ensures optimal settings from the beginning. Welding simulations also help in training new welders. They can practice virtually, gaining skills without wasting materials.
Incorporating Ai And Machine Learning
AI and machine learning enhance welding accuracy and efficiency. These technologies analyze patterns and data from past welds. They predict the best settings for new projects. AI algorithms adjust parameters in real-time. This minimizes human error and reduces welding time. Machine learning models can also forecast potential issues. This proactive approach keeps the welding process smooth and efficient.
Predictive Maintenance Approaches
Predictive maintenance tools monitor equipment health continuously. They alert you about potential failures before they happen. This prevents unexpected downtimes and maintains consistent welding quality. By knowing the status of your tools, you can plan maintenance without disrupting work. This approach helps in maintaining productivity. Predictive maintenance also extends the lifespan of your welding equipment.
Credit: calculator.academy
Frequently Asked Questions
How To Calculate The Welding Time?
To calculate welding time, measure the weld length. Divide by the welding speed. Consider preparation and finishing time. Use the formula: Welding Time = Weld Length / Welding Speed.
What Is The Formula For Welding Calculation?
The formula for welding calculation is: Heat Input (J/mm) = (Voltage x Current x 60) / (Travel Speed x 1000). This determines the energy used per unit length.
How To Calculate The Welding Speed?
To calculate welding speed, divide the length of the weld by the time taken to complete it. Measure the length in inches or millimeters and time in minutes. Ensure consistent units for accurate results.
How Is Weld Length Calculated?
Weld length is calculated by measuring the total length of the weld seam. This includes any additional welds for joints. Use a measuring tape or ruler for accuracy.
Conclusion
Calculating welding time involves several steps. First, measure the weld length. Then, consider the welding speed. Don’t forget to account for preparation and breaks. By understanding these factors, you can estimate welding time accurately. This helps in planning your projects better.
Remember, practice makes perfect. Keep refining your calculations. Soon, you will be more confident in your estimates. Happy welding!