Welding underwater is a fascinating and complex process. It involves joining metal pieces beneath the water’s surface.
Underwater welding is crucial for various marine projects. This skill is vital for repairing ships, fixing pipelines, and maintaining offshore oil rigs. Divers use specialized equipment to weld in such challenging environments. The process requires expertise and precision due to the added difficulty of working underwater.
Safety is also a significant concern, as the underwater setting presents unique hazards. Understanding how underwater welding works can help appreciate the skill and technology involved. This blog post will explore the techniques, equipment, and safety measures in underwater welding. Dive in to learn about this intriguing and essential field.
Introduction To Underwater Welding
Diving underwater, welders use special equipment to join metals in submerged environments. Electrical currents and unique electrodes enable this process.
Underwater welding is a unique and essential skill in many industries. It involves joining metal parts while submerged in water. This technique is vital for maintaining offshore structures, ships, and pipelines. Underwater welders work in challenging environments. They must be skilled in both diving and welding. Special equipment is used to perform these tasks safely and efficiently. The welds must be strong and durable to withstand underwater conditions.Importance Of Underwater Welding
Underwater welding plays a crucial role in many sectors. It is essential for the maintenance of oil rigs and offshore wind farms. Ships and submarines often need repairs that require underwater welding. Pipelines that transport oil and gas also depend on this technique. Without underwater welding, many underwater structures would deteriorate. This could lead to costly repairs and environmental hazards. Skilled underwater welders ensure the safety and longevity of these structures.Challenges Faced
Underwater welding comes with many challenges. Visibility underwater is often poor. Welders must rely on touch and experience. The water pressure at deep levels can be intense. This adds extra stress to the welder’s body. Temperature variations also impact the welding process. Cold water can cause materials to behave differently. Safety is a major concern. Welders must be aware of the risks, including electric shock and decompression sickness. Proper training and equipment are essential to manage these risks. “`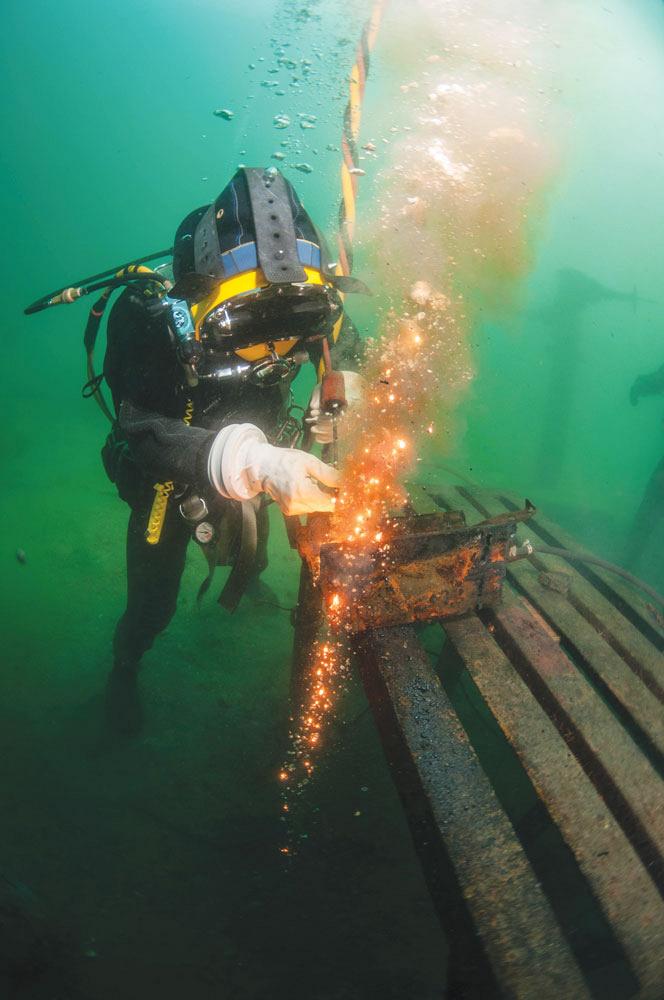
Credit: www.canadianmetalworking.com
Types Of Underwater Welding
Underwater welding might sound like something out of a science fiction movie, but it’s a real and fascinating profession. There are two main types of underwater welding: Wet Welding and Dry Welding. Each method has its own unique process and set of challenges. Let’s dive into the details!
Wet Welding
Wet welding is exactly what it sounds like: welding that takes place in the water. This method is often used because it’s quick and cost-effective. Here’s how it works:
- A special waterproof electrode is used.
- The welder wears a diving suit and uses a standard welding rod.
- The electric arc created can work even underwater, melting the metal and welding it together.
Sounds simple, right? Well, there’s a catch. Wet welding can be tricky because the water cools the weld too fast, which can cause cracks. Plus, it’s not the safest job around. But don’t worry, the professionals are well-trained and follow strict safety procedures. Think of them as underwater superheroes!
Dry Welding
Dry welding, on the other hand, involves creating a dry environment around the welding site. This is done using a special chamber called a habitat. Here’s a quick breakdown:
- The habitat is placed over the area to be welded.
- Water is pumped out, creating a dry space.
- The welder then enters the habitat and welds as they would on land.
It sounds like building a tiny room underwater, doesn’t it? And that’s exactly what it is. This method is safer and produces higher-quality welds, but it’s also more expensive and time-consuming. Imagine trying to build a house inside a swimming pool – it’s no easy feat!
Both wet and dry welding are amazing feats of engineering. They require skill, precision, and a bit of bravery. Next time you see a bridge or an oil rig, remember the underwater welders who keep these structures safe and sound. They might just be the unsung heroes of the deep blue sea!
Equipment Used In Underwater Welding
Underwater welding is a fascinating yet complex process that requires a unique set of equipment. This specialized gear ensures the safety and effectiveness of the welders working beneath the waves. To understand how welding underwater works, let’s dive into the essential equipment used in this remarkable practice.
Diving Gear
Diving gear is crucial for underwater welders. Without it, they wouldn’t be able to breathe, see, or move comfortably underwater. Here are the main components of diving gear used in underwater welding:
- Diving Suit: Provides thermal insulation and protection from the underwater environment. It keeps the welder warm and shields them from sharp objects and marine life.
- Diving Helmet: Ensures a continuous supply of air and protects the welder’s head. It also allows for clear communication with the surface team.
- Air Supply: Can be provided via tanks or through an umbilical cord connected to the surface. A steady air supply is vital for the welder’s survival.
- Weight Belt: Helps to counteract buoyancy and keep the welder stable underwater. It ensures they stay grounded while working.
- Fins: Aid in movement through the water. They help the welder navigate to the work site efficiently.
Welding Tools
Underwater welding requires specific tools designed to function in wet conditions. These tools must be robust and reliable to ensure quality welds. Here are some of the essential welding tools:
- Underwater Welding Machine: This machine generates the electrical current needed for welding. It is specially designed to operate safely underwater.
- Electrodes: These are consumable rods that create the weld. Underwater electrodes are coated to prevent water damage and ensure a stable arc.
- Welding Stinger: A device that holds the electrode. It must be waterproof and insulated to protect the welder from electric shock.
- Cutting Torch: Used to cut through metal. Underwater cutting torches use a combination of gas and electricity to create a flame capable of cutting through metal even underwater.
- Inspection Tools: Tools like cameras and ultrasound devices are used to inspect the welds. They ensure the welds are strong and meet safety standards.
With the right equipment, underwater welding can be done safely and effectively. This specialized gear not only protects the welder but also ensures the quality of the work being performed beneath the sea. Whether it’s repairing a ship hull or maintaining an offshore oil rig, the right tools make all the difference.
Safety Precautions
Welding underwater is a fascinating and complex process. However, it comes with its unique set of challenges and risks. Ensuring safety is critical when performing such tasks. Let’s dive into the essential safety precautions that welders need to follow to stay safe underwater.
Personal Safety Measures
Diving into the depths to weld is no child’s play. It demands rigorous personal safety measures. Picture this: you’re deep underwater, working with electrical equipment. Sounds risky, right? Here’s how professionals stay safe:
- Proper Training: Underwater welders undergo extensive training. They learn both diving and welding techniques. This combo makes them adept at handling any situation.
- Diving Suit: A high-quality diving suit is a must. It protects the welder from the cold, marine life, and potential hazards.
- Helmet and Breathing Apparatus: Safety begins with the basics. A sturdy helmet and a reliable breathing apparatus ensure the diver can breathe easily and stay protected.
- Communication Systems: Constant communication with the surface team is vital. Advanced intercom systems allow welders to stay in touch, ensuring they can call for help if needed.
Environmental Considerations
Welding underwater isn’t just about personal safety. The environment plays a crucial role too. Ever wondered how the surroundings affect the process? Here’s a breakdown:
Factor | Consideration |
---|---|
Water Pressure | Water pressure increases with depth. Welders need to be cautious, as high pressure can affect both equipment and human bodies. |
Temperature | Cold water can be challenging. Proper insulation and thermal protection are essential to keep the welder safe and efficient. |
Visibility | Murky waters can obscure vision. Good lighting and clear water are crucial for precise welding. |
Marine Life | Encountering fish or other sea creatures is common. Understanding and respecting marine life ensures the safety of both the welder and the creatures. |
In conclusion, welding underwater is a skill that blends expertise with strict safety measures. By prioritizing personal safety and understanding environmental factors, underwater welders can perform their tasks effectively and securely. Next time you think about underwater welding, remember the intricate dance of safety and skill involved!
Techniques For Effective Underwater Welding
Underwater welding is a fascinating and challenging skill. It requires special techniques to ensure safety and effectiveness. Let’s dive into some key methods that make underwater welding work seamlessly. We will discuss the importance of selecting the right electrode and controlling the arc stability. These techniques are crucial for achieving strong, reliable welds underwater.
Proper Electrode Selection
Choosing the right electrode for underwater welding is like picking the perfect tool for a job. It makes all the difference. The electrode must be designed to handle the wet environment and provide a stable arc. Here are some key points to consider:
- Waterproof Coating: Ensure the electrode has a waterproof coating. This prevents water from getting into the weld, which can cause defects.
- Material Compatibility: Match the electrode material with the metal being welded. For instance, use a steel electrode for steel work.
- Size and Type: Use electrodes that are the right size and type for the welding task. Thicker electrodes might be needed for deeper, stronger welds.
Think of the electrode as your underwater partner. Choose wisely, and it will help you create strong bonds even in the depths.
Controlling Arc Stability
Maintaining a stable arc underwater is a bit like walking a tightrope – it requires balance and precision. Here are some tips to keep the arc stable:
- Consistent Distance: Keep a consistent distance between the electrode and the workpiece. This helps maintain a steady arc.
- Steady Hand: Use a steady hand to avoid fluctuations in the arc. Movement can disrupt the weld quality.
- Proper Equipment: Use equipment designed for underwater welding. It ensures better control over the arc.
Controlling the arc is like steering a ship – steady hands and the right tools keep you on course. These techniques will help ensure your welds are solid and durable.
By focusing on proper electrode selection and controlling arc stability, you can achieve effective and reliable results in underwater welding. Remember, precision and the right tools are your best allies in this challenging environment.

Credit: yeswelder.com
Common Applications
Underwater welding might sound like something straight out of a sci-fi movie, but it’s a crucial skill in many industries. From fixing pipelines to building massive marine structures, underwater welders are often the unsung heroes keeping things in shape. Let’s dive into some common applications of underwater welding.
Marine Construction
When you think of marine construction, you might picture grand bridges, sturdy docks, and offshore oil rigs. All these structures need a lot of work and maintenance, much of which happens underwater. Underwater welders play a vital role here.
Imagine a team working on a bridge. The support pillars that go deep into the water need to be strong and secure. If there’s any damage or rusting, the pillars might weaken. That’s where underwater welders come in. They dive down, often in challenging conditions, to weld and repair any damage. This ensures the bridge remains safe for everyone using it.
Offshore oil rigs are another example. These massive structures are out in the middle of the ocean, facing harsh weather and constant waves. Underwater welders are essential for keeping these rigs stable and operational. They handle everything from regular maintenance to emergency repairs, ensuring the oil keeps flowing.
Pipeline Repairs
Underwater pipelines are like the veins of our modern world, transporting vital resources like oil and gas. But, just like any other pipe, they can get damaged or start to leak. That’s when underwater welders step in to save the day.
Picture this: A pipeline on the ocean floor has developed a leak. The precious oil or gas starts escaping, which could be disastrous for the environment and very costly. Underwater welders gear up and dive down to fix the problem. They use special techniques to weld the pipeline, even while it’s submerged in water.
These repairs are not just about patching a hole. Sometimes, entire sections of the pipeline need to be replaced. Underwater welders cut out the damaged part and weld in a new section, ensuring the pipeline can continue to function smoothly.
Without these skilled professionals, our supply of oil and gas could be severely disrupted. Their work keeps the resources flowing and prevents potential environmental disasters.
Training And Certification
Have you ever wondered how underwater welders get their skills? It’s not something you just wake up knowing. Training and certification play a huge role in making sure these professionals can do their job safely and effectively. Let’s dive into what it takes to become an underwater welder.
Essential Skills
Underwater welding is no walk in the park. It requires a unique set of skills. Here are some of the essential abilities you need:
- Swimming and Diving: First, you must be a good swimmer. Diving skills are crucial. You need to be comfortable underwater for long periods.
- Welding Skills: You must know how to weld on land before attempting it underwater. Understanding different welding techniques is essential.
- Problem-Solving: Conditions underwater are unpredictable. You must think on your feet and solve problems quickly.
- Physical Fitness: The job is physically demanding. You need to be in good shape to handle the rigors of underwater work.
- Attention to Detail: Small mistakes can lead to big problems. Precision is key.
Certification Programs
Getting certified is a must. It ensures you have the knowledge and skills to work safely. Here are some common certification programs:
- Commercial Diving Certification: This is the first step. You learn basic and advanced diving techniques. Schools like the Commercial Diving Academy offer these courses.
- Welding Certification: You need to be a certified welder. The American Welding Society (AWS) offers various certifications.
- Underwater Welding Certification: This specialized certification combines diving and welding skills. It’s often provided by commercial diving schools.
Many programs offer hands-on training. This way, you can practice in real-world conditions. It’s like learning to drive; you need to get behind the wheel to truly understand it.
So, are you ready to take the plunge? Becoming an underwater welder is challenging, but the rewards are worth it. With the right training and certification, you’ll be ready to tackle the depths and weld like a pro!

Credit: en.wikipedia.org
Future Of Underwater Welding
The future of underwater welding is bright and promising. Rapid technological advancements and increasing demand in various sectors are driving this field forward. As underwater welding becomes more efficient and safer, new opportunities are emerging for skilled professionals. This section explores the latest technological advancements and career opportunities in underwater welding.
Technological Advancements
New technologies are transforming underwater welding. Robotics play a key role. These machines assist divers and perform complex tasks. This reduces human risk. Advanced welding techniques improve precision and quality. Methods like friction welding and laser welding are becoming more common. These innovations help welders work faster and safer.
Specialized equipment is also evolving. Modern helmets provide better visibility and communication. Divers can see clearly and speak with teams above water. This improves coordination and safety. Additionally, better materials resist corrosion and withstand pressure. These materials make underwater structures more durable.
Career Opportunities
Underwater welding offers many career paths. The oil and gas industry needs skilled welders. These professionals maintain and repair offshore rigs. Construction projects also require underwater welders. Bridges, dams, and underwater tunnels depend on their skills. Shipbuilding is another sector hiring underwater welders. They work on hulls and other submerged parts.
Training programs are expanding. More schools offer courses in underwater welding. Certification programs ensure welders meet industry standards. This increases job prospects. Experienced welders can advance to supervisory roles. They oversee projects and train new divers. The demand for underwater welders is growing. This makes it a viable career choice.
Frequently Asked Questions
How Do Underwater Welders Not Get Shocked?
Underwater welders use specialized equipment and protective gear. They employ direct current (DC) instead of alternating current (AC). This reduces shock risk. Proper training and safety protocols ensure their safety during welding tasks.
How Is Welding Done Underwater?
Underwater welding uses special equipment and techniques. Divers use waterproof electrodes and a constant current. The process creates an electric arc, melting metals to join them.
Do Underwater Welders Make $100 An Hour?
Yes, experienced underwater welders can make $100 an hour. Earnings vary based on skills, location, and job complexity.
How Long Do Underwater Welders Stay Underwater?
Underwater welders typically stay underwater for 30 minutes to 6 hours per dive. Dive duration depends on the job, depth, and safety protocols.
Conclusion
Understanding underwater welding is crucial for many marine projects. This unique process involves specific techniques and equipment to ensure safety. Skilled divers perform these tasks with precision, protecting structures from water damage. Although challenging, underwater welding plays a vital role in maintaining underwater infrastructure.
This essential skill keeps our underwater environments functional and safe. By learning how it works, we appreciate the expertise required.