Welding doesn’t technically “dry” because it involves melting and fusing metals. Instead, it cools and solidifies.
This process can take from a few seconds to several minutes. Understanding how long welding takes to cool is crucial for any project. The time depends on various factors like the type of welding, the thickness of the material, and the surrounding temperature.
Knowing these details helps in planning and ensures safety. Proper cooling time prevents issues like cracks and weak joints. In this guide, we’ll explore the factors affecting welding cooling times. This information will help you better manage your welding projects and achieve strong, reliable welds. Let’s dive in and understand the cooling process of welding.
Drying Time Factors
Welding is a skillful craft that joins materials together, usually metals or thermoplastics. But how long does it take for welding to dry? The answer isn’t straightforward. Several factors influence the drying time. Let’s explore them in detail.
Material Type
The type of material being welded plays a crucial role in how long the weld takes to dry. Different materials have different properties that affect drying time. For example:
- Steel: This is the most common material used in welding. Depending on the thickness and the specific type of steel, drying times can vary.
- Aluminum: Aluminum welding generally dries faster than steel due to its different thermal properties.
- Cast Iron: This material can be tricky. Cast iron may take longer to dry because it retains heat longer.
Each material has its own quirks. Ever tried welding aluminum and wondered why it dries so quickly? It’s because of its high thermal conductivity!
Welding Technique
The welding technique used also impacts the drying time. Here are some common techniques and their effects:
- MIG Welding: Metal Inert Gas (MIG) welding is fast and efficient. It generally leads to quicker drying times.
- TIG Welding: Tungsten Inert Gas (TIG) welding, on the other hand, is more precise but slower. This can result in a longer drying period.
- Stick Welding: Also known as Shielded Metal Arc Welding (SMAW), this technique can vary widely in drying times based on the electrode used and the thickness of the material.
Choosing the right technique can make a big difference. Ever been in a rush and opted for MIG welding to save time? You’re not alone!
Understanding these drying time factors can help you plan your welding projects more effectively. Whether you’re a seasoned welder or just starting, knowing what to expect can save you time and frustration.
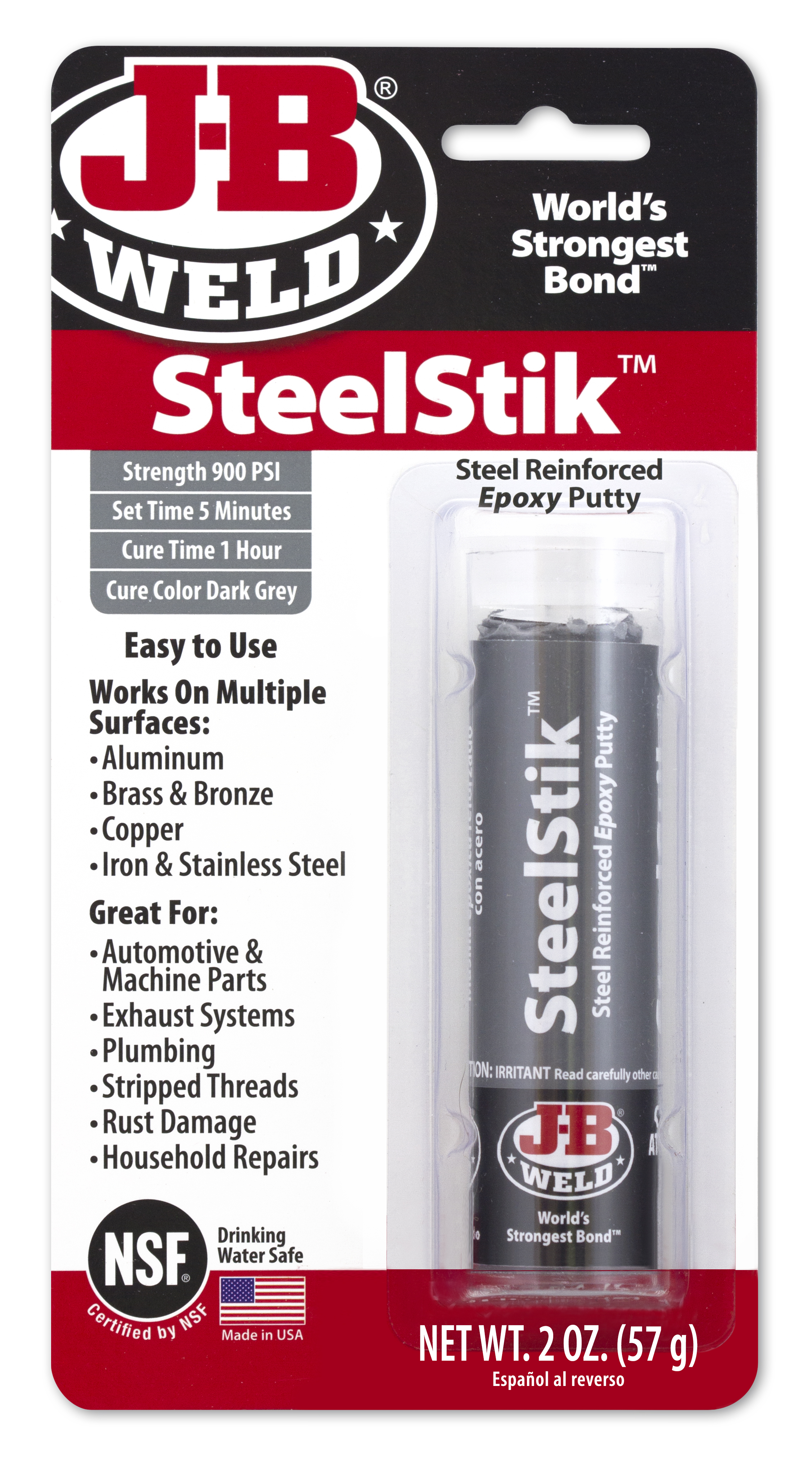
Credit: www.jbweld.com
Environmental Conditions
Understanding how environmental conditions affect welding dry times is crucial. Different factors like temperature and humidity can impact the drying process. Let’s dive into these in detail.
Temperature Impact
Temperature plays a significant role in welding dry times. Higher temperatures speed up the drying process. This is because heat causes the water in the welding material to evaporate faster. On the other hand, colder temperatures slow down drying. This is due to the reduced evaporation rate in cooler conditions. For optimal drying, maintain a steady and warm environment.
Humidity Levels
Humidity levels also influence welding dry times. High humidity means more moisture in the air. This extra moisture slows down the drying process. Low humidity creates a drier environment. This speeds up the drying time. To achieve the best results, keep the humidity level controlled. Aim for a balanced environment.
Welding Processes
Welding is an essential skill in many industries, from construction to automotive repairs. But not all welding processes are created equal. Each type has its own unique characteristics, and the drying time can vary. Let’s dive into two popular methods: MIG and TIG welding.
Mig Welding
MIG stands for Metal Inert Gas. This method is a favorite because it’s easy to learn. Even beginners can get the hang of it quickly. But how long does it take to dry?
- Speed: MIG welding is fast. The weld cools down quickly, often within a few minutes.
- Materials: It works well on thicker materials, which helps speed up the process.
- Environment: If you are working outside, the wind can affect drying time. A gusty day might make the weld cool faster.
In most cases, you can handle or move the welded piece in about 15 to 20 minutes. Just be sure to check the specifics of your materials and conditions.
Tig Welding
TIG, or Tungsten Inert Gas welding, is a bit more sophisticated. It’s great for detailed work and offers high precision. But, it comes with its own set of quirks.
- Precision: TIG welding is slower because it focuses on precision. This means a longer drying time.
- Materials: Ideal for thinner materials and metals like aluminum and stainless steel.
- Skill Level: Requires more skill, which can also affect the drying time.
So, how long does it take to dry? It can take around 30 to 40 minutes. Patience is key here. Rushing can ruin a good weld.
Both MIG and TIG welding have their own pros and cons. The drying time can vary based on several factors, but with a bit of practice, you’ll get a feel for the right timing. Happy welding!
Material Thickness
One key factor that affects how long welding takes to dry is the thickness of the material. Whether you’re working with thin sheets or thick slabs, the drying time can vary greatly. Let’s dive into the specifics of welding different material thicknesses.
Thin Materials
When dealing with thin materials, such as sheet metal or light gauge steel, the drying time is usually shorter. This is because thin materials cool down quickly. Imagine welding a soda can versus a heavy-duty steel beam. The can cools in seconds, right?
- Quick Cooling: Thin materials lose heat fast, so the welding dries faster.
- Less Heat Required: You don’t need as much heat to weld thin materials, which speeds up the process.
- Delicate Handling: Be careful, as thin materials can warp easily if overheated.
Personally, I once welded a thin aluminum sheet for a friend’s DIY project. It took just a few minutes to cool and dry, saving us loads of time!
Thick Materials
On the flip side, thick materials like heavy-duty steel or large metal parts take longer to dry. Think of it as baking a cake. A thin pancake cooks quickly, but a thick cake needs more time in the oven.
Factor | Impact on Drying Time |
---|---|
Heat Retention | Thick materials retain heat longer, slowing the drying process. |
Heat Input | More heat is required for thick materials, extending the cooling period. |
Material Type | Different metals have varying heat conduction properties, affecting drying time. |
For example, when I worked on a large steel frame for a garage door, the welds took a good hour to fully dry. Patience is key with thick materials!
In conclusion, the thickness of the material plays a significant role in determining how long welding takes to dry. Thin materials cool quickly, while thick ones require more time. Remember, every project is unique, so always take material thickness into account.
Post-welding Treatments
Post-welding treatments are essential for ensuring a strong and durable weld. These treatments help to manage the cooling process, prepare the surface, and enhance the overall quality of the weld. Understanding the right methods can make a significant difference in the final outcome.
Cooling Methods
Cooling the weld properly is crucial. It prevents cracks and distortions. Slow cooling is often recommended. This method helps avoid internal stresses. Some welders use blankets or sand. This helps control the cooling rate. Faster cooling might be needed for certain metals. Air or water can be used in these cases.
Surface Preparation
Preparing the welded surface is the next step. It ensures a clean and smooth finish. Start by removing slag and spatter. A wire brush or grinder works well for this. Sanding the area can also help. It smooths out any rough edges. Clean the surface with a solvent. This removes any oils or residues.
Expert Tips
Welding is a critical skill in various industries. Knowing how long it takes for welding to dry ensures strong and durable joints. Here are some expert tips to help achieve the best results.
Best Practices
Always ensure the welding area is clean and dry. Contaminants can weaken the weld. Use appropriate welding techniques for each material. Different metals require different approaches. Maintain a steady hand and consistent speed. This ensures a uniform weld.
Use the right amount of heat. Too much or too little can compromise the weld. Allow the weld to cool naturally. Rapid cooling can cause cracks. Follow manufacturer guidelines for drying times. These are tested and proven.
Common Mistakes
One common mistake is rushing the process. Patience is key. Another is not cleaning the surface properly. Dirt and oil can ruin the weld. Using incorrect techniques for the material is also common. Learn the proper method for each type.
Applying too much heat is a frequent error. It can warp the metal. Not allowing enough drying time is another mistake. This can lead to weak joints. Avoid rapid cooling methods. These can cause cracks and other issues.
Drying Time Estimation
Welding projects require careful attention to drying times. The time it takes for welding to dry impacts the strength and durability of the final product. Understanding the drying time can help ensure the quality of your welds.
General Guidelines
Welding drying times vary. They depend on the type of weld and the materials used. Commonly, welds dry within 24 hours. Yet, some might need up to 48 hours. Checking the manufacturer’s instructions is essential. This can give precise drying times for specific welding materials.
Environmental factors affect drying times too. Humidity and temperature play a big role. In cooler or more humid settings, expect longer drying periods. Conversely, dry and warm conditions can speed up the process.
Specific Examples
Consider MIG welding on mild steel. It usually dries within 24 hours. But, if the environment is cold, it might take longer. Similarly, TIG welding on aluminum can dry faster. It often dries within 12 to 24 hours under optimal conditions.
Stick welding on stainless steel can be different. It tends to need around 48 hours to dry. This is due to the nature of the material and the welding process itself.
Each welding type and material combination will have its own drying time. Always refer to guidelines specific to your project. This ensures the best results and safety.
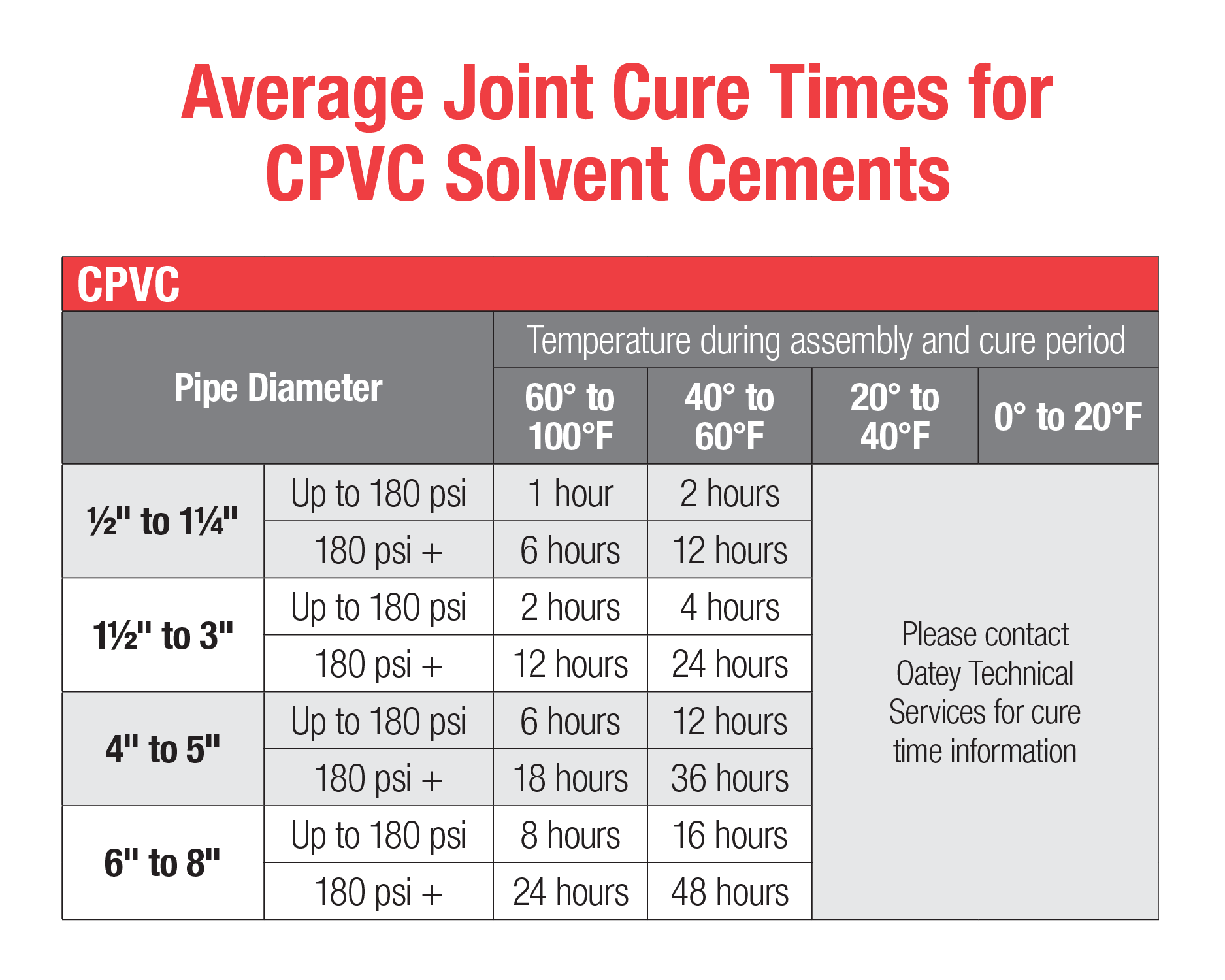
Credit: www.oatey.com
Advanced Techniques
Welding requires precision and patience. Advanced techniques can significantly reduce drying times. These methods ensure strong and lasting welds. This section explores two key techniques: Accelerated Drying and Quality Control.
Accelerated Drying
Accelerated drying can speed up welding projects. One common method is using heat. Applying controlled heat helps welds dry faster. Infrared heaters are often used for this purpose. They provide consistent and even heat distribution. Another method is using fans. High-powered fans can reduce drying time significantly. Proper ventilation is crucial to avoid trapping moisture. Quick drying prevents rust and other issues.
Quality Control
Quality control ensures welds meet standards. Inspect welds carefully after drying. Look for cracks or weak spots. Use non-destructive testing methods. Ultrasonic testing is effective for this purpose. This method detects internal flaws without damaging the weld. Visual inspections are also important. Inspectors should have proper training. Regular training updates help maintain high standards. Quality control helps in achieving reliable and durable welds.
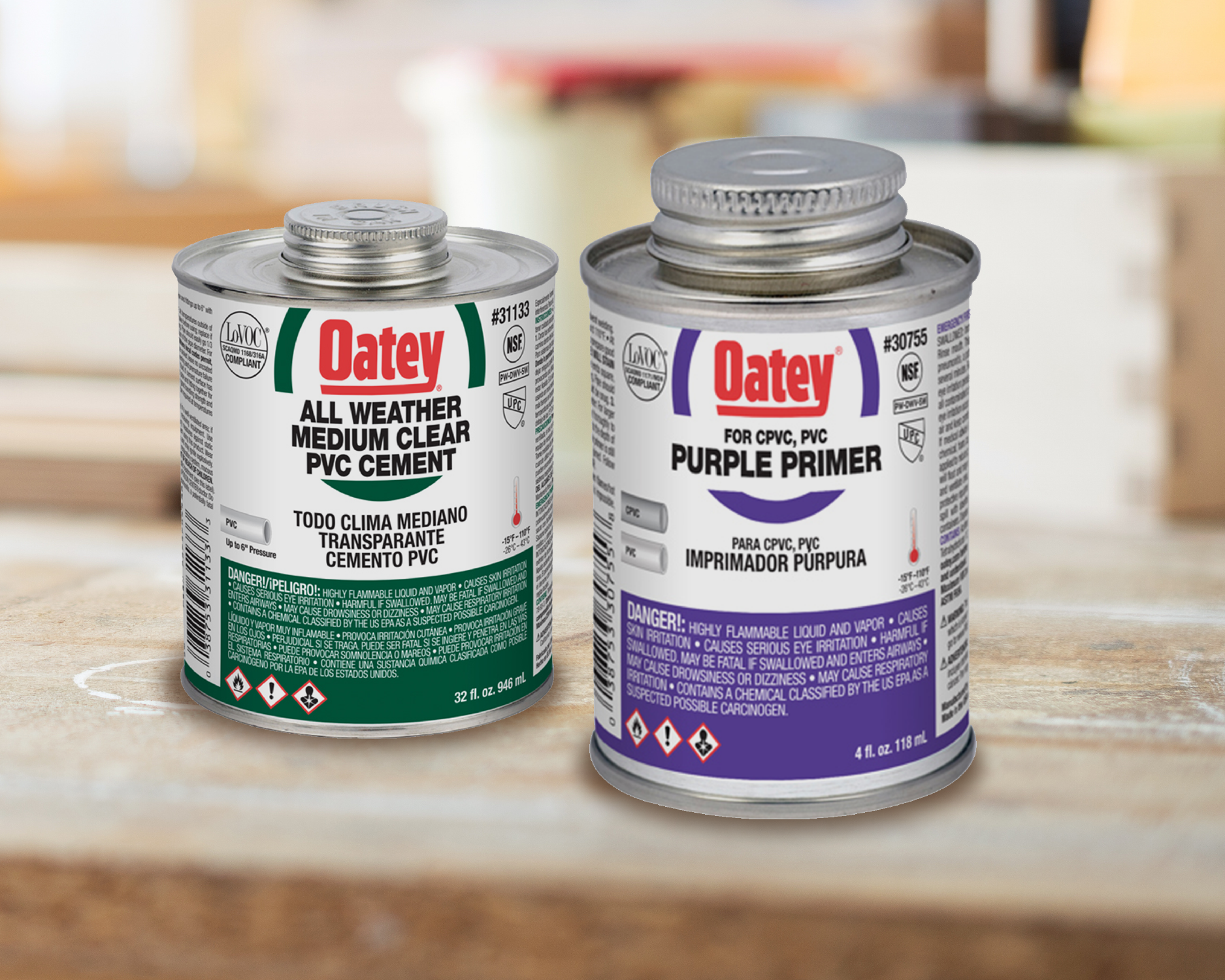
Credit: www.oatey.com
Frequently Asked Questions
How Long Do Welds Take To Harden?
Welds typically harden within 24 hours. The exact time depends on the material, welding method, and environmental conditions.
How Long Does It Take For Weld To Dry?
Welds typically dry within a few minutes to an hour. Factors like temperature and material affect drying time. Always follow manufacturer guidelines.
Is It Safe To Shower After Welding?
Yes, it is safe to shower after welding. Showering helps remove harmful chemicals and particles from your skin. Make sure to clean any cuts or abrasions thoroughly to prevent infections. Always use mild soap and lukewarm water.
How Long To Wait After Welding?
Wait 24 hours after welding for proper cooling and inspection. This ensures strength and prevents cracks or defects.
Conclusion
Welding drying times vary based on type and conditions. Typically, it takes 24 hours. Ensuring proper drying is crucial for strong welds. Factors like temperature and humidity impact drying time. Always follow manufacturer guidelines for best results. Checking the weld before use is essential.
Patience during drying leads to safer, reliable welds. Happy welding!