Calculating welding leg length is crucial for strong welds. This task might seem challenging, but it’s straightforward with the right approach.
Understanding the welding leg length is essential for ensuring the integrity of your welds. The leg length directly affects the strength and durability of the welded joint. Whether you’re a beginner or an experienced welder, knowing how to measure this accurately can make a significant difference in your projects.
In this guide, we’ll walk you through the steps to calculate welding leg length efficiently. This will help you achieve better results in your welding tasks, ensuring safety and quality in your work. Let’s dive in and simplify the process for you.
Introduction To Welding Leg Length
Welding is a skill that demands precision. One of the key aspects to master is understanding and calculating the welding leg length. But what exactly is welding leg length, and why is it so important? Let’s dive in!
Importance In Welding
The welding leg length is crucial because it directly affects the strength and quality of the weld. Think of it as the backbone of your weld joint. Without the correct leg length, the weld might not hold up under stress, leading to potential failures. In simpler terms, getting this measurement right ensures your welds are strong and reliable.
Here are a few reasons why welding leg length is important:
- Ensures Structural Integrity: Correct leg length makes sure the weld can support the intended load.
- Avoids Over-Welding: Prevents wasting materials and time.
- Quality Control: Helps maintain consistency in weld quality.
Common Challenges
Calculating the welding leg length can be tricky, especially for beginners. Here are some common challenges you might face:
- Measurement Accuracy: Getting precise measurements can be tough, especially with different joint configurations.
- Understanding Standards: Different projects might have varying standards and requirements for weld sizes.
- Visual Estimation: Relying on sight alone can lead to errors; using proper tools is crucial.
But don’t worry! With practice and the right tools, you can overcome these challenges. Just remember, even the pros had to start somewhere.
So, are you ready to master welding leg length? Keep reading, and we’ll guide you through the process step by step!
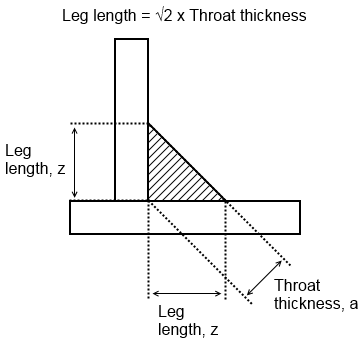
Credit: www.colliewelding.com
Basic Welding Terminology
Understanding basic welding terminology is crucial. It helps ensure precise calculations and strong welds. Knowing the right terms makes the welding process easier and safer. This section will cover key terms used in welding. Let’s start with weld types and key measurements.
Weld Types
There are different weld types you need to know. Each has its own application and characteristics. Here are some common weld types:
- Fillet Weld: Joins two surfaces at a right angle.
- Butt Weld: Joins two pieces end-to-end.
- Lap Weld: Overlaps two pieces for a strong bond.
- Corner Weld: Joins pieces at the corners.
- Edge Weld: Joins the edges of two pieces.
Knowing these weld types helps choose the right one for your project.
Key Measurements
Several key measurements ensure weld quality. These include throat thickness, leg length, and weld size. Let’s look at leg length in detail.
Leg Length: The distance from the root to the toe of the weld. It is vital for strength and stability. Accurate leg length ensures a strong weld. Use a welding gauge for precise measurements.
Understanding these measurements is vital for successful welding. It ensures safety and durability in your projects.
Tools And Equipment Needed
Calculating welding leg length can seem like a daunting task, but with the right tools and a bit of practice, you’ll have it down in no time. Whether you’re a seasoned welder or just starting out, having the proper equipment is crucial to getting accurate measurements. Let’s dive into the essential tools and gear you’ll need to measure welding leg length effectively.
Measuring Tools
First things first, you need the right measuring tools. Without these, it’s like trying to bake a cake without a recipe – possible, but not ideal.
- Fillet Weld Gauge: This handy tool helps you measure the leg length and throat thickness of your weld. It’s a must-have for any welder.
- Tape Measure: A good old tape measure is indispensable. Ensure it’s sturdy and long enough for your projects.
- Caliper: For those times when you need precision, a caliper will help you get the exact measurements you need.
- Ruler: Sometimes the simplest tools are the best. A ruler can help you double-check your measurements.
It’s always better to measure twice and weld once. Trust me, it saves a lot of headache down the line!
Safety Gear
Safety first, folks! Before you even think about picking up those measuring tools, make sure you’re geared up. Welding can be dangerous if you’re not properly protected.
- Welding Helmet: Protect your eyes and face from sparks and harmful rays. A good helmet is your best friend in the workshop.
- Gloves: Your hands are your livelihood. Keep them safe with a pair of heavy-duty welding gloves.
- Protective Clothing: Long sleeves and pants made from flame-resistant material will keep your skin protected.
- Boots: Sturdy, closed-toe boots are a must. They protect your feet from falling objects and hot materials.
Remember, it’s better to be safe than sorry. I once knew a guy who skipped the gloves – let’s just say he learned his lesson the hard way. Don’t be that guy.
By having the right tools and safety gear, you’re setting yourself up for success. Now, you’re ready to measure that welding leg length with confidence. Happy welding!
Step-by-step Calculation Process
Calculating welding leg length might sound like a task reserved for engineers, but with a step-by-step process, anyone can master it. Whether you’re a seasoned welder or just getting started, understanding the basics can ensure your welds are both strong and reliable. Let’s break it down into simple, digestible steps.
Initial Measurements
Before diving into calculations, it’s important to gather some key measurements. This ensures accuracy and saves you from potential headaches later on.
- Measure the Weld Throat: The throat is the shortest distance from the weld root to the weld face.
- Weld Leg Lengths: These are the distances from the weld root to the toe of the weld on each side.
Got your measurements? Great! Now, let’s move on to the fun part—doing the math.
Mathematical Formulas
Don’t worry, you won’t need a degree in mathematics to follow along. We’ll keep it straightforward.
- Calculate the Throat: Use the formula
Throat = Leg Length 0.707
. This formula applies to a 45-degree fillet weld, a common type. - Verify with Leg Length: If your leg lengths are different, use the larger one for more accurate results.
For example, if your measured leg length is 10mm, the throat will be:
Measurement | Value |
---|---|
Leg Length | 10mm |
Throat Calculation | 10mm 0.707 = 7.07mm |
See? It’s not rocket science. Just a bit of multiplication and you’re good to go.
In summary, calculating welding leg length involves a few easy steps: measure accurately, apply the formula, and double-check your work. With practice, you’ll be performing these calculations in your sleep. So, grab your measuring tools and start welding with confidence!
Common Mistakes To Avoid
Calculating the welding leg length correctly is crucial for the strength and reliability of welded joints. However, there are common mistakes that people often make during this process. Understanding these pitfalls can save you time, money, and a whole lot of frustration. Let’s dive into some of the most frequent errors and how to avoid them.
Measurement Errors
One of the most common mistakes when calculating welding leg length is measurement errors. These can occur for several reasons, such as using the wrong tools or not calibrating your instruments properly.
- Inaccurate Tools: Make sure you are using a quality measuring device. Cheap tools can give you false readings.
- Incorrect Calibration: Regularly calibrate your tools to ensure they provide accurate measurements.
- Human Error: Double-check your measurements. Even the most experienced welders can make mistakes.
Imagine trying to bake a cake without measuring your ingredients correctly. You’d end up with something that resembles a science experiment gone wrong rather than a tasty dessert. The same goes for welding; precise measurements are crucial.
Incorrect Calculations
Another area where people frequently go wrong is in the actual calculations. Even if your measurements are spot-on, a small error in your math can lead to big problems.
- Misunderstanding Formulas: Ensure you understand the formulas you are using. If the formula looks like Greek to you, take a moment to learn it.
- Skipping Steps: Don’t rush through the process. Skipping steps can lead to inaccurate results.
- Relying Solely on Memory: Always write down your calculations. Memory can be unreliable, especially under pressure.
It’s like trying to solve a puzzle with a piece missing. You won’t get the full picture, and the end result will be flawed. Double-check your work to ensure accuracy.
By avoiding these common mistakes, you’ll be well on your way to mastering the calculation of welding leg lengths. Remember, even the best welders started with the basics, and learning from these errors will make you a better professional in the long run.

Credit: www.weldingandndt.com
Tips For Precision
Calculating welding leg length accurately is crucial for the strength and safety of your welds. Precision is key, and a few tips can make this task easier. Whether you’re a seasoned welder or just starting, these tips will help you achieve the best results.
Double-checking Measurements
One of the simplest yet most effective ways to ensure precision is to double-check your measurements. It’s easy to make a mistake, especially when you’re focused on other aspects of the welding process. Here’s how you can do it:
- Use a reliable ruler or tape measure: Ensure your measuring tool is accurate and in good condition.
- Check multiple times: Measure twice, or even three times, before making any cuts or welds. This can prevent costly mistakes.
- Compare with a buddy: If you’re working with a partner, have them check your measurements. A second set of eyes can catch errors you might miss.
Think of double-checking as your safety net. It’s a small step that can save you a lot of trouble down the road. Remember, measure twice, cut once!
Using Advanced Tools
In today’s world, technology can be a welder’s best friend. Advanced tools not only make the job easier but also enhance precision. Here are some tools you might find helpful:
- Digital Calipers: These provide highly accurate measurements and are easy to read. Unlike traditional calipers, digital ones reduce the chance of human error.
- Laser Measuring Tools: These are great for long distances and hard-to-reach areas. They offer pinpoint accuracy and can save you a lot of time.
- Angle Finders: These tools help you measure the exact angle of your weld, ensuring it meets the required specifications.
Using advanced tools doesn’t mean you’re taking shortcuts. It means you’re leveraging technology to work smarter, not harder. Plus, who doesn’t like playing with fancy gadgets?
Remember, precision in welding is not just about the final product. It’s about the process, the tools, and the attention to detail. By double-checking your measurements and using advanced tools, you’re setting yourself up for success. So, next time you’re preparing for a weld, keep these tips in mind and watch your accuracy soar!
Real-world Applications
Understanding how to calculate welding leg length is not just a technical skill; it’s a gateway to numerous practical applications in everyday life. Whether you are working in a large industrial setting or creating a beautiful piece of metal art, knowing the right welding techniques and measurements can make all the difference.
Industrial Uses
In the industrial world, precision and safety are paramount. Calculating welding leg length correctly ensures that structures are strong and durable. This is critical in industries like construction, automotive, and shipbuilding. Imagine the skyscrapers of New York or the ships that sail the ocean – they all rely on precise welding for their structural integrity.
- Construction: Welding is used to join beams and other structural elements. Accurate measurements ensure the stability and safety of buildings.
- Automotive: In car manufacturing, welding leg length affects the strength and durability of the vehicle. This is especially important in crash safety.
- Shipbuilding: Ships must withstand harsh conditions. Proper welding ensures the hull and other parts can handle stress and pressure.
In each of these fields, the calculation of welding leg length is a fundamental step in creating safe and reliable products. This knowledge can save time, reduce costs, and prevent accidents.
Artisan Projects
On the other end of the spectrum, calculating welding leg length plays a vital role in artisan projects. Whether you are crafting a custom piece of furniture or a unique metal sculpture, precision in welding can make your work stand out.
- Furniture Making: When creating metal furniture, accurate welding ensures that pieces fit together perfectly and are sturdy.
- Sculpture: Artists use welding to create intricate designs. Proper measurements ensure that their vision comes to life exactly as planned.
- DIY Projects: For hobbyists, understanding welding leg length can turn a weekend project into a professional-looking piece.
Imagine creating a stunning metal sculpture that becomes the centerpiece of a room. Or a custom metal chair that not only looks good but is also incredibly durable. The secret often lies in the precision of your welds.
So, whether you are an industrial professional or an artisan, understanding how to calculate welding leg length is a skill that can elevate your work. It opens up a world of possibilities and ensures that whatever you create is both beautiful and strong.
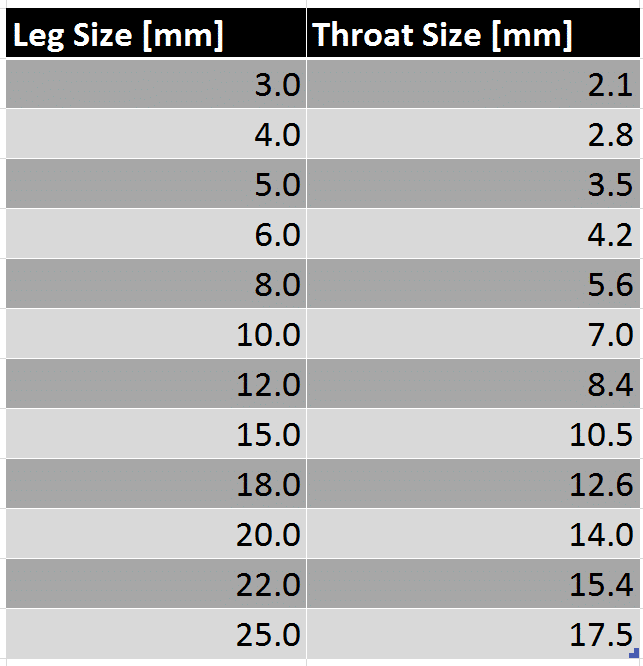
Credit: restoric.co.uk
Advanced Techniques
Advanced techniques in calculating welding leg length offer precision and efficiency. These methods reduce errors and save time. This section covers two leading methods: Computer-Aided Design and Laser Measuring.
Computer-aided Design
Computer-Aided Design (CAD) brings accuracy to welding projects. CAD software creates detailed models of weld joints. These models help calculate the exact welding leg length.
By using CAD, welders can visualize the project before starting. This visualization helps in planning and reduces mistakes. The software also allows for adjustments, ensuring the weld meets specifications.
CAD tools often include built-in calculators. These calculators simplify the process by automatically computing the required leg length. This method is highly efficient and reliable.
Laser Measuring
Laser measuring tools offer another advanced technique. These devices measure distances with high precision. They are especially useful in large or complex welding projects.
Using a laser measuring tool, welders can quickly determine the leg length. The tool projects a laser beam onto the surface, providing an accurate measurement. This reduces the need for manual measuring tools.
Laser measuring tools are easy to use. They require minimal training and increase efficiency. The accuracy of these devices ensures that the welds are consistent and meet the required standards.
Both CAD and laser measuring tools are invaluable in modern welding. They streamline the process and improve the quality of the welds.
Conclusion And Final Thoughts
Calculating welding leg length is crucial for ensuring strong, reliable welds. Understanding the basics and practicing regularly can help you achieve better results.
Recap Of Key Points
We covered several important aspects of welding leg length calculation. Start by understanding the types of welds and their applications. Use proper tools to measure accurately. Remember, the leg length directly affects the strength of the weld.
We also discussed the formula and factors that influence the leg length. Pay attention to the thickness of the materials. Proper technique is essential for achieving the desired results. Accuracy ensures safety and durability.
Encouragement For Practice
Practice is vital in welding. The more you practice, the better you become. Start with simple projects. Gradually move to more complex tasks. Use scrap metal for practice.
Measure your welds. Compare them against the desired leg length. Seek feedback from experienced welders. Learn from mistakes. Every practice session improves your skill. Consistency is key. Keep refining your technique.
Remember, calculating welding leg length is not just about numbers. It’s about understanding the process. It’s about improving your craft. Keep practicing and learning. Your welds will get stronger. Your confidence will grow. Happy welding!
Frequently Asked Questions
How To Calculate Leg Length?
Measure from the top of your hip bone to the floor. Ensure you stand straight with feet together. Use a measuring tape for accuracy.
What Is The Formula For The Length Of Weld?
The formula for the length of weld is: Length of Weld = (Number of Welds) x (Length of Each Weld). This helps calculate total welding length.
What Is The Formula For Throat Thickness And Leg Length?
Throat thickness (t) is calculated as 0. 707 times the leg length (L). The formula is t = 0. 707L.
What Is The Formula For Welding Calculation?
The welding calculation formula is: Heat Input (kJ/mm) = (Voltage x Current x 60) / (Travel Speed x 1000). This calculates the heat input during welding.
Conclusion
Calculating welding leg length is crucial for strong welds. Follow these steps carefully. Measure accurately and double-check your work. Use the right tools and materials. Practice makes perfect in welding. Keep safety in mind at all times. A good weld ensures durability and safety.
Share your welding tips with others. Happy welding!