When I first started working with metal projects, one issue kept popping up: galvanic corrosion. It seemed like no matter how careful I was, certain connections between metals would eventually start to degrade. Over time, I realized this was due to a chemical reaction that occurs when two dissimilar metals come into contact with each other in the presence of moisture or an electrolyte.
If you’re dealing with metal connections—whether it’s for plumbing, construction, or electronics—you’ve probably come across this problem too.
There are several effective ways to prevent galvanic corrosion and extend the life of your materials. In this guide, I’ll share what I’ve learned about this process and the best ways to stop it in its tracks.

Image by strongtie
What Is Galvanic Corrosion?
Before diving into prevention methods, it’s important to understand what galvanic corrosion is. It occurs when two different types of metal are electrically connected in the presence of an electrolyte, such as water or moisture. One of the metals (the anode) will start to corrode, while the other (the cathode) remains protected.
This reaction happens because different metals have varying tendencies to give up electrons. The more “active” metal (the anode) sacrifices itself to protect the less active one.
Why Is Galvanic Corrosion a Problem?
The main issue with galvanic corrosion is that it weakens the affected metal over time. This can lead to structural failures, leaks, or costly repairs. Whether you’re working on a plumbing system, a metal roof, or a marine vessel, ignoring galvanic corrosion can compromise the safety and durability of your project.
Common Areas Where Galvanic Corrosion Occurs
From my experience, galvanic corrosion tends to show up in a few key areas:
- Plumbing: When copper and galvanized pipes are connected without proper insulation.
- Construction: Metal roofing, screws, and fasteners that combine different metals.
- Marine Environments: Boats and docks, where exposure to saltwater accelerates the process.
- Electronics: Circuits and devices with mixed-metal components.
Recognizing these hotspots is the first step to preventing corrosion.
How to Prevent Galvanic Corrosion
Thankfully, there are several tried-and-true methods to prevent galvanic corrosion. Here’s what I’ve found works best:
Choose Compatible Metals
The simplest way to avoid galvanic corrosion is to use metals that are similar in their electrochemical properties. Metals closer together on the galvanic series chart are less likely to cause a reaction. For example, aluminum and zinc are more compatible with each other than aluminum and copper.
When planning a project, take time to select materials that won’t react negatively with one another.
Use a Barrier or Insulator
If you need to connect dissimilar metals, adding a physical barrier can prevent them from coming into direct contact. Some effective options include:
- Dielectric Unions: Commonly used in plumbing to separate copper and galvanized pipes.
- Plastic or Rubber Gaskets: Provide insulation between metal parts.
- Paint or Coatings: Applying a protective layer can shield the metals from direct exposure.
Apply Protective Coatings
Coatings act as a shield between the metal and the environment, reducing the chance of corrosion. There are several types of coatings to consider:
- Zinc Coating (Galvanization): Protects steel by making it the sacrificial anode.
- Epoxy or Powder Coatings: Provide a durable, non-conductive layer.
- Anodizing: Enhances the natural oxide layer on metals like aluminum for extra protection.
I’ve used these coatings on outdoor projects, and they’ve significantly improved durability.
Control the Environment
Sometimes, the key to preventing galvanic corrosion lies in managing the surrounding environment. By reducing exposure to moisture and electrolytes, you can slow down the reaction.
- Seal Connections: Use sealants to keep water out of joints.
- Improve Drainage: Prevent standing water near metal components.
- Control Humidity: In indoor spaces, dehumidifiers can help reduce moisture levels.
Use Sacrificial Anodes
This method involves deliberately adding a more reactive metal to “sacrifice” itself and protect the main material. Sacrificial anodes are commonly used in:
- Boats: Zinc anodes protect hulls and propellers in saltwater.
- Water Heaters: Magnesium or aluminum anodes prevent tank corrosion.
Replacing the anode periodically ensures continued protection.
Select Appropriate Fasteners
In construction, the fasteners you use can make or break your project’s longevity. Avoid using screws or bolts made from a different metal than the components they’re connecting. For example, use stainless steel screws with stainless steel panels.
If mixing metals is unavoidable, use washers or bushings as insulators.
Inspect and Maintain Regularly
No prevention method is completely foolproof, so regular inspections are crucial. Look for early signs of corrosion, such as discoloration, rust, or pitting. Catching the problem early can save you from major repairs later
Practical Examples of Preventing Galvanic Corrosion
To give you a better idea, here are a few scenarios where I’ve applied these methods:
- Plumbing: When connecting copper and galvanized pipes, I always use a dielectric union. This small step has saved me countless headaches.
- Outdoor Structures: For a metal patio roof, I used the same type of screws and washers as the panels to prevent corrosion around the fasteners.
- Boat Maintenance: Installing sacrificial zinc anodes on the hull kept my boat safe from saltwater corrosion during a summer trip.
Benefits of Preventing Galvanic Corrosion
Taking the time to prevent galvanic corrosion pays off in many ways:
- Cost Savings: Avoid expensive repairs or replacements.
- Longevity: Extend the lifespan of your materials and projects.
- Safety: Reduce the risk of structural failures.
- Aesthetics: Prevent unsightly rust or discoloration.
From my experience, these benefits far outweigh the small upfront effort required.
Conclusion
Preventing galvanic corrosion might seem like a small detail, but it can make a big difference in the durability and safety of your projects. If you’re working on plumbing, construction, or marine applications, the key is understanding how different metals interact and taking steps to minimize their contact.
By choosing compatible materials, adding barriers, and staying on top of maintenance, you can keep your connections strong and corrosion-free for years to come. Trust me—your future self will thank you for the effort!
FAQs
What is galvanic corrosion, and why does it happen?
Galvanic corrosion occurs when two different metals are electrically connected in the presence of an electrolyte, causing one metal to corrode.
Can galvanic corrosion be completely avoided?
While it’s difficult to eliminate all risks, proper prevention methods like using dielectric unions or protective coatings can minimize the chances of corrosion.
Is galvanic corrosion common in plumbing systems?
Yes, especially when copper and galvanized steel pipes are connected without insulation. Using a dielectric union can solve this problem.
How do sacrificial anodes work?
Sacrificial anodes are made from more reactive metals, like zinc, which corrode instead of the main material they’re protecting.
Can regular paint prevent galvanic corrosion?
Paint can act as a barrier, but for the best results, use specialized coatings like epoxy or powder coatings.
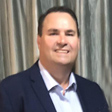
Endow Russel the owner chief editor of giftendow.com . I am a mechanical engineer and assign to an local firm with much experience in welding and industrial equipment.