You’re trying to repair a broken clasp on your favorite stainless steel necklace or fix a loose wire in a custom motorcycle exhaust. You’ve soldered copper and brass before, but this time, the solder just balls up and slides off like water on a hot skillet. Sound familiar? I’ve been there too.

Image by klp99mall
Soldering stainless steel wire isn’t like working with other metals—it fights you every step of the way. But after years of trial, error, and a few melted projects, I’ve cracked the code.
Let me walk you through how to solder stainless steel wire so your connections hold strong and look professional.
Why Stainless Steel Is a Soldering Nightmare
Stainless steel contains chromium, which forms a stubborn oxide layer when exposed to air. This layer repels solder like a forcefield. Add stainless steel’s high melting point (2,500°F+), and you’ve got a recipe for frustration.
I learned this the hard way when trying to fix a stainless steel grill grate—my solder joints crumbled faster than a cookie.
Essential Tools and Materials
Here’s what you’ll need (no fancy gear required):
- Soldering Iron or Torch: A 60–100W iron for thin wire; propane torch for thicker gauges.
- Silver-Bearing Solder: Stay away from lead. Use 45%+ silver solder for strength (e.g., Harris Stay-Brite 8).
- High-Activity Flux: Look for “stainless steel” on the label. I prefer Stay-Clean or La-Co flux.
- Abrasive Tools: 220-grit sandpaper, stainless steel brush, or fiberglass pen.
- Cleaning Supplies: Acetone or isopropyl alcohol, lint-free cloth.
Pro Tip: Skip the cheap hardware store flux—it won’t break through chromium oxide.
Step 1: Clean Like Your Solder Depends on It (Because It Does)
Stainless steel’s chromium oxide layer is invisible but deadly to solder. Here’s how to strip it:
- Mechanical Cleaning: Sand the soldering area until it’s shiny. Focus on 1–2 inches of wire.
- Chemical Cleaning: Wipe with acetone or alcohol to remove oils.
- Act Fast: Oxide reforms in minutes. Solder immediately after cleaning.
I once cleaned a wire, got distracted, and had to re-sand it 10 minutes later. Lesson learned: Prep and solder in one go.
Step 2: Flux—Your Secret Weapon
Flux is the bridge between stainless steel and solder. It eats through oxides and keeps the area clean during heating.
- Apply Generously: Coat the joint with flux paste using a brush or toothpick.
- Reapply as Needed: Flux burns off under heat. Add more if the joint dries out.
I keep flux in a syringe for precision. No more globs ruining delicate jewelry repairs.
Step 3: Heat Management—The Key to Success
Stainless steel conducts heat poorly, leading to cold joints or melted insulation. Here’s how to control it:
- Use a Heat Sink: Clip alligator clips or aluminum foil near the joint to absorb excess heat.
- Heat the Metal, Not the Solder: Touch the iron/torch to the wire until it’s hot enough to melt solder on contact (600–800°F).
- Work Quickly: Prolonged heat discolors stainless steel and weakens the joint.
For thick wires, I preheat the area with a torch before switching to the iron for precision.
Step 4: Apply Solder with Precision
- Melt Solder onto the Joint: Let the heated wire draw in the solder—don’t push it with the iron.
- Capillary Action Is Your Friend: Flux pulls solder into tight spaces. Rotate the wire for even coverage.
- Less Is More: A thin, even layer beats a bulky blob.
My Aha Moment: Holding the solder wire against the joint (not the iron) gave me cleaner, stronger bonds.
Step 5: Post-Soldering Cleanup
Leftover flux corrodes stainless steel over time. Here’s how to finish strong:
- Cool Naturally: Don’t quench in water—thermal shock cracks joints.
- Neutralize Flux: Soak in warm water mixed with baking soda (1 tbsp per cup).
- Brush and Buff: Use a stainless steel brush to restore shine.
I ruined a vintage watchband by skipping the baking soda rinse. Don’t be me.
Common Stainless Steel Soldering Problems (and Fixes)
- Solder Won’t Stick: Oxide layer survived. Re-clean and flux.
- Grainy Joints: Contaminated flux or dirty wire. Start fresh.
- Discoloration: Too much heat. Use a lower setting and work faster.
- Solder Balls Up: Wrong flux or insufficient heat. Switch to high-activity flux.
Stainless Steel Soldering Cheat Sheet
Wire Gauge (AWG) | Soldering Iron Wattage | Solder Type | Flux Type |
---|---|---|---|
20–24 | 60W | 45% Silver | Paste flux |
16–18 | 80W | 56% Silver | Liquid flux |
10–14 | Propane torch | 45% Silver + flux core | Heavy-duty paste |
When Soldering Isn’t Enough: Alternatives
For high-stress or high-temperature applications, consider:
- Welding: TIG welding for precision, MIG for speed.
- Crimp Connectors: Ideal for electrical projects.
- Epoxy Adhesives: JB Weld for non-load-bearing fixes.
I repaired a boat railing with epoxy as a temporary fix—it held for a full season.
Final Thoughts
Soldering stainless steel wire is a skill that rewards precision and prep. My first successful project—a custom bike chain—still holds up three years later.
Start with small repairs, master the basics, and soon you’ll tackle any stainless steel challenge. Remember, every stubborn joint is a chance to learn. Keep your flux close, your iron hot, and your patience steady.
FAQs About Soldering Stainless Steel Wire
Can I use regular electrical solder?
No—it won’t bond. Use silver-bearing solder (45%+).
Why does my stainless steel turn rainbow colors?
Overheating. Lower the temperature and work faster.
Can I solder stainless to other metals?
Yes! Use flux and solder compatible with both (e.g., silver solder for copper-stainless joints).
How do I remove old solder from stainless steel?
Heat the joint and wipe with a brass brush. Use solder wick for stubborn bits.
Is soldered stainless steel food-safe?
Only if you use lead-free solder and remove all flux residue.
Can I solder stainless steel with a butane torch?
Yes, but control the flame to avoid overheating thin wires.
Why does my solder crack after cooling?
Thermal stress. Let joints cool slowly—no water quenching!
Can I reuse flux?
Never. Contaminated flux ruins joints.
How strong is a soldered stainless joint?
Properly done, it’s 70–80% as strong as the base metal.
Can I solder stainless steel jewelry?
Yes! Use low-temperature silver solder and a micro torch.
With the right tools and techniques, soldering stainless steel wire becomes second nature. Got a tricky project or success story? Share it below—I’d love to hear how it goes!
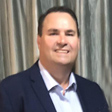
Endow Russel the owner chief editor of giftendow.com . I am a mechanical engineer and assign to an local firm with much experience in welding and industrial equipment.