When it comes to welding processes, there are plenty of options to choose from, each designed for specific needs and applications. If you’ve come across Submerged Arc Welding (SAW) and are wondering whether it’s the right process for your project, you’re in the right place.
I’ve had my fair share of experience working with SAW, and I can tell you it’s a powerhouse in the welding world. But it’s not a one-size-fits-all solution. Let me walk you through everything you need to know so you can make an informed decision.
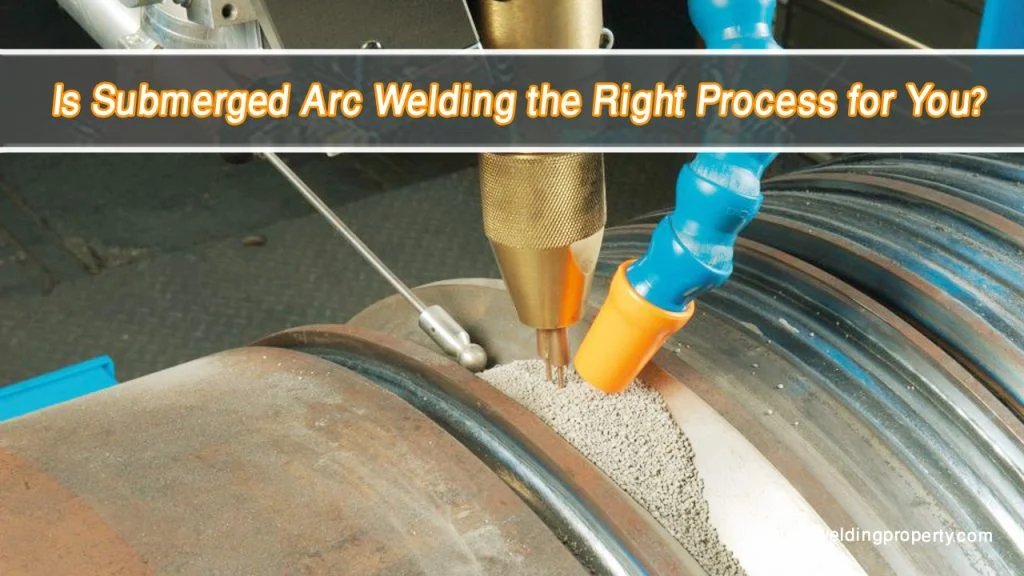
What is Submerged Arc Welding (SAW)?
Submerged Arc Welding is a highly efficient welding process where a consumable electrode and the base material are fused together beneath a layer of granular flux. This protective flux not only shields the weld from atmospheric contamination but also enhances the weld’s properties.
SAW is predominantly used for heavy industrial applications, delivering high-quality welds with exceptional speed. The process is typically automated or semi-automated, making it ideal for large-scale manufacturing.
Why Consider Submerged Arc Welding?
Choosing the right welding process depends on your project’s specific needs. Here’s a breakdown of situations where SAW shines:
- You’re working with thick materials: SAW is excellent for welding heavy steel plates and pipes.
- You need high efficiency: With its high deposition rates, SAW is one of the fastest welding processes.
- You prioritize weld quality: The protective flux ensures clean, defect-free welds.
Still, there are limitations, so let’s dive into the pros and cons to help you decide.
Advantages of Submerged Arc Welding
Exceptional Efficiency
SAW is designed for high productivity. Its continuous electrode feed and automated equipment allow it to complete large welding tasks quickly. This is a game-changer for industries like shipbuilding and pipeline construction, where time is money.
Superior Weld Quality
One of the biggest selling points of SAW is its ability to produce clean, strong, and defect-free welds. The protective flux eliminates impurities and ensures consistent weld quality.
Reduced Environmental Hazards
Unlike open-arc welding processes, SAW contains sparks, fumes, and UV radiation under the flux layer. This makes it safer for operators and reduces environmental contamination.
Cost-Effective for Large Projects
While the initial setup for SAW can be expensive, its high efficiency and minimal waste make it cost-effective for large-scale projects. You’ll save time and resources in the long run.
Versatility in Applications
SAW is widely used in industries such as:
- Oil and gas (pipelines)
- Structural steel fabrication
- Shipbuilding
- Heavy machinery manufacturing
If your project falls into one of these categories, SAW might be the perfect fit.
Limitations of Submerged Arc Welding
Even with all its benefits, SAW isn’t perfect. Here are some drawbacks you should consider:
Limited to Flat or Horizontal Positions
SAW works best in flat or horizontal positions. The flux and molten weld pool rely on gravity, making it unsuitable for vertical or overhead welding.
Not Ideal for Thin Materials
SAW generates significant heat and is primarily used for thick materials. Using it on thinner metals can lead to warping or burn-through.
High Initial Investment
The equipment and setup required for SAW can be costly. Smaller workshops may find it difficult to justify the expense unless they have a high volume of suitable projects.
Flux Handling and Maintenance
The granular flux needs careful handling and storage to prevent contamination. Additionally, a flux recovery system is required, adding complexity to the process.
Restricted Metal Types
SAW is best suited for ferrous metals like steel. It doesn’t work well with non-ferrous metals such as aluminum, which limits its versatility in certain industries.
Comparing SAW to Other Welding Processes
Here’s a quick comparison to see how SAW stacks up against other popular welding methods:
Process | Advantages | Disadvantages |
---|---|---|
SAW | High efficiency, superior weld quality, low fumes | Limited positions, high setup costs |
MIG Welding | Easy to learn, versatile, works on thin metals | Higher fumes, less suitable for thick metals |
TIG Welding | Precision, excellent for thin materials | Slow process, requires high skill level |
Stick Welding | Portable, works in any position | Slower, more post-weld cleanup needed |
This table shows that while SAW is unbeatable for large-scale, flat-position welding of thick materials, other processes may be better suited for small-scale or intricate work.
Key Factors to Consider
If you’re still on the fence about whether SAW is right for you, here are some key factors to weigh:
Material Type
SAW works best with ferrous metals like carbon steel and stainless steel. If your project involves aluminum or other non-ferrous metals, you’ll need a different welding process.
Project Size
For large-scale projects, SAW is a clear winner. Its high deposition rates and efficiency make it perfect for long welds and thick materials. However, for smaller, one-off projects, the setup time and cost might not be worth it.
Position of the Weld
Because SAW is limited to flat and horizontal positions, it’s not suitable for applications that require vertical or overhead welding.
Budget
If you’re working with a tight budget, consider whether the initial investment in SAW equipment is justified. For large projects, the efficiency and cost savings will offset the upfront costs, but smaller operations might find it prohibitive.
Is SAW the Right Choice for You?
Let’s answer the big question. SAW is the right choice if:
- You’re working on a large-scale project with thick ferrous materials.
- The welds will be performed in a flat or horizontal position.
- High-quality, defect-free welds are critical to your project.
- You have the resources to invest in SAW equipment.
If your project involves thinner metals, non-ferrous materials, or out-of-position welding, you’ll need to explore other options like MIG, TIG, or stick welding.
FAQs
What types of metals can Submerged Arc Welding work with?
SAW is primarily used for ferrous metals like carbon steel and stainless steel. It’s not suitable for non-ferrous metals such as aluminum.
Can SAW be used in outdoor environments?
While SAW is most effective in controlled environments like workshops, it can be used outdoors with the proper setup, though moisture can affect the flux.
Is SAW cost-effective for small projects?
Not usually. SAW’s high efficiency shines in large-scale projects, but the initial setup costs can be too high for smaller jobs.
What industries commonly use SAW?
SAW is widely used in industries such as shipbuilding, pipeline construction, structural steel fabrication, and heavy equipment manufacturing.
How does SAW ensure weld quality?
The protective flux shields the weld from atmospheric contamination, ensuring a clean, defect-free weld with superior mechanical properties.
Conclusion
Submerged Arc Welding is a fantastic process for the right projects. Its speed, efficiency, and ability to produce high-quality welds make it a favorite in industries like shipbuilding, pipeline construction, and heavy machinery manufacturing.
That said, it’s not the best choice for every situation. Its limitations with thin materials, out-of-position welding, and non-ferrous metals mean you need to carefully assess your project requirements before committing to SAW.
If your project involves heavy-duty work where precision, strength, and efficiency are critical, SAW could be the ideal solution. However, for smaller-scale or more intricate work, exploring other welding techniques might be the better route. Whatever you choose, understanding the process will help you achieve the best possible results.
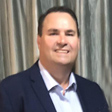
Endow Russel the owner chief editor of giftendow.com . I am a mechanical engineer and assign to an local firm with much experience in welding and industrial equipment.