Flux core welding is one of the most versatile and beginner-friendly welding processes out there. If you’re using a Lincoln flux core welder, getting the right settings is key to producing strong, clean welds. I remember when I first started with flux core welding—there were so many adjustments to make, and it felt overwhelming. But once I figured out the right settings for different materials and thicknesses, everything started to come together.

If you’re struggling with burn-through, spatter, or weak welds, chances are your settings need fine-tuning. This guide will walk you through everything you need to know about Lincoln flux core welding settings so you can dial in your machine like a pro.
Understanding Flux Core Welding and Its Benefits
Flux core welding (FCAW) is a wire-feed welding process that doesn’t require an external shielding gas. Instead, the flux inside the wire melts and creates a protective gas shield around the weld. This makes it perfect for outdoor welding, dirty metals, and thick materials.
Some of the biggest advantages of flux core welding are:
- Great for windy conditions – No need for gas shielding.
- Penetrates thick metals well – Ideal for heavy-duty work.
- Fast and efficient – Higher deposition rates than MIG.
- Works on rusty or painted metal – Less prep required.
Lincoln Electric makes some of the best flux core welders, but choosing the right settings for wire speed, voltage, and material thickness is what truly makes a difference.
Lincoln Flux Core Welding Settings Chart
Before diving into the details, here’s a quick reference chart for Lincoln flux core welding settings based on wire size and metal thickness.
Wire Size | Material Thickness | Voltage (V) | Wire Speed (IPM) | Polarity |
---|---|---|---|---|
.030″ | 18-20 gauge (thin) | 14-16 | 50-120 | DCEN (Electrode Negative) |
.030″ | 1/8″ – 3/16″ | 16-18 | 90-200 | DCEN |
.035″ | 1/8″ – 1/4″ | 16-20 | 90-250 | DCEN |
.045″ | 1/4″ and thicker | 18-22 | 130-300 | DCEP (Electrode Positive) |
Now, let’s break down each of these settings so you can understand how to adjust them for your specific project.
Choosing the Right Wire Size
One of the first things you need to do is select the right wire size for your material thickness.
- .030″ Wire – Best for thin metals (18-gauge to 3/16″). It provides good control and minimal spatter.
- .035″ Wire – The most commonly used size for general welding. It works well on 1/8″ to 1/4″ thick steel.
- .045″ Wire – Great for heavy-duty welding on thick steel (1/4″ and up). Requires higher voltage.
For most home and auto repairs, .030″ or .035″ wire is ideal. If you’re working with thicker metals, you might need to switch to .045″ wire with higher power settings.
Setting the Right Voltage
Voltage controls the arc length and affects the overall heat of the weld. Too much voltage will cause burn-through, while too little can lead to poor penetration and weak welds.
- Lower voltage (14-16V) – Used for thin sheet metal and small projects.
- Medium voltage (16-18V) – Ideal for general-purpose welding on 1/8″ to 3/16″ thick steel.
- Higher voltage (18-22V) – Needed for thicker materials (1/4″ and up) to ensure deep penetration.
If you’re unsure, start with a lower voltage and gradually increase it until you get a smooth, strong weld.
Adjusting Wire Speed
Wire speed controls how fast the welding wire feeds through the gun. Setting it correctly is crucial for smooth welds with minimal spatter.
- Too slow – Causes an unstable arc, weak penetration, and inconsistent welds.
- Too fast – Leads to excessive spatter, poor fusion, and an erratic arc.
A good rule of thumb is to start with the recommended speed for your wire size and metal thickness (see the chart above) and adjust slightly as needed.
Polarity Settings for Lincoln Flux Core Welding
One of the most common mistakes beginners make is using the wrong polarity for flux core welding. Unlike MIG welding, which uses DCEP (Electrode Positive), most flux core wires require DCEN (Electrode Negative).
- DCEN (Electrode Negative) – This is the correct polarity for most flux core wires like Lincoln NR-211-MP. It produces deeper penetration and less spatter.
- DCEP (Electrode Positive) – Used for gas-shielded flux core wires. If your Lincoln welder has a polarity switch, make sure to set it to DCEN unless using gas-shielded wire.
Fine-Tuning Your Lincoln Welder for Better Results
Even with the correct settings, you may still need some fine adjustments to improve your weld quality. Here are a few things to keep in mind:
- Clean the metal – Even though flux core welding works on rusty or painted surfaces, cleaning the area with a wire brush or grinder improves weld quality.
- Keep a short stick-out – Hold the tip of the wire about 1/2 inch from the metal for better control.
- Use a drag technique – Pull the torch instead of pushing to maintain a stable arc.
- Check for spatter buildup – If you see excessive spatter, adjust the wire speed or voltage slightly.
- Listen to the arc – A good weld sounds like a steady sizzle, not popping or crackling.
Common Issues and Fixes in Flux Core Welding
Sometimes, even with the right settings, you’ll run into weld defects. Here’s how to fix them:
Issue | Cause | Solution |
---|---|---|
Excess spatter | Too high wire speed | Reduce wire speed |
Burn-through | Voltage too high | Lower voltage, move faster |
Weak welds | Low penetration | Increase voltage, adjust wire speed |
Porosity (holes) | Moisture in flux or metal | Keep metal dry, check wire quality |
Conclusion
Getting the right settings on your Lincoln flux core welder is key to producing strong, clean, and professional-quality welds. By understanding wire size, voltage, wire speed, and polarity, you can fine-tune your machine to match any project.
If you’re just starting out, begin with .030″ wire on 1/8″ thick steel, set your voltage around 16-18V, and adjust wire speed based on the weld puddle. Over time, you’ll develop a feel for what settings work best for different materials and situations.
Flux core welding is a great skill to master, and once you dial in the right settings, it becomes an incredibly efficient and reliable process. Grab your Lincoln welder, experiment with these settings, and start laying down some solid welds!
FAQs
What polarity should I use for Lincoln flux core welding?
Most flux core wires require DCEN (Electrode Negative). Check your wire type before switching polarity.
Why am I getting too much spatter in my welds?
Excessive spatter can be caused by high wire speed, incorrect voltage, or improper torch angle. Try adjusting your settings for a smoother arc.
What is the best flux core wire for a Lincoln welder?
For general welding, Lincoln NR-211-MP is an excellent choice. It works well on mild steel and provides smooth welds.
Can I use gas with my Lincoln flux core welder?
Most flux core wires are self-shielded, meaning they don’t need gas. However, some gas-shielded flux core wires require CO2 or a mix of argon and CO2.
How do I prevent burn-through on thin metal?
Use lower voltage, slower wire speed, and a back-and-forth weaving motion to distribute heat evenly.
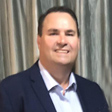
Endow Russel the owner chief editor of giftendow.com . I am a mechanical engineer and assign to an local firm with much experience in welding and industrial equipment.