Laser welding is a widely used technique in many industries. It offers precision, speed, and reliability.
But like any technology, it has its advantages and disadvantages. Laser welding involves using a concentrated laser beam to join materials. It’s known for creating strong, precise welds in metals and plastics. Many industries, from automotive to aerospace, rely on this technology for critical applications.
Understanding the pros and cons of laser welding helps in making informed decisions. It allows you to weigh the benefits against the limitations. This knowledge is crucial whether you are considering adopting this technology or simply want to understand it better. Dive into the details to see how laser welding could impact your projects and operations.
Introduction To Laser Welding
Laser welding offers high precision and speed, making it ideal for many industries. Though efficient, it can be costly and requires technical expertise.
Laser welding is a modern technique used in joining metal parts. It offers precision and speed, making it popular in various industries. This method uses a concentrated laser beam to fuse materials. Its accuracy and efficiency stand out compared to traditional welding methods.What Is Laser Welding?
Laser welding is a process that uses a laser to join metal pieces. The laser beam melts the material, creating a strong bond. It is ideal for small, delicate parts and complex shapes. This method ensures minimal distortion and high-quality welds. It is used in industries like automotive, aerospace, and medical devices.Historical Background
The concept of laser welding emerged in the mid-20th century. Early experiments showed potential, but technology was limited. By the 1960s, advancements in laser technology made practical applications possible. Industries began adopting laser welding for its precision and speed. Today, it continues to evolve with new innovations and techniques. “`
Credit: www.heatsign.com
Advantages Of Laser Welding
Laser welding is a modern technique that uses a laser beam to join materials. It’s like magic for industries, making welding faster, more precise, and versatile. Let’s dive into some of the major advantages that make laser welding a top choice in manufacturing and beyond.
Precision And Accuracy
One of the biggest advantages of laser welding is its incredible precision and accuracy. Imagine trying to sew a delicate piece of fabric with a needle – you need to be precise, right? Laser welding is like that but on a microscopic level. This technique allows for very small and exact welds, which means less material wastage and cleaner results.
- Produces high-quality welds with minimal distortion
- Perfect for delicate and intricate components
For example, in the electronics industry, where components are tiny and delicate, laser welding ensures connections are strong without damaging nearby parts.
Speed And Efficiency
Time is money, and laser welding helps save both. This technique is known for its speed and efficiency. It can join materials quickly, which means less downtime and more productivity. Think of it as a high-speed train compared to a traditional bus – you get to your destination faster.
- Reduces overall production time
- Increases throughput and productivity
In industries where high-volume production is key, like automotive manufacturing, laser welding’s speed can significantly boost output.
Versatility In Materials
Laser welding is like a jack-of-all-trades when it comes to the materials it can handle. From metals to plastics, it works with a wide range of materials. This versatility means that industries don’t need different welding methods for different materials, simplifying the manufacturing process.
Material | Compatibility |
---|---|
Steel | High |
Aluminum | High |
Plastic | Moderate |
Whether it’s joining steel parts in a car or delicate plastic components in medical devices, laser welding adapts to the material, making it a versatile choice.
In summary, laser welding stands out for its precision, speed, and versatility. It’s a modern solution that keeps industries running smoothly and efficiently. Have you ever seen laser welding in action? It’s quite a spectacle!
Enhanced Quality And Strength
Laser welding offers enhanced quality and strength for various applications. This technique minimizes distortion and creates stronger welds, ensuring durable and reliable results.
Minimal Distortion
Laser welding produces minimal distortion in the welded materials. The focused laser beam delivers precise heat. This prevents excessive thermal expansion. Conventional welding methods often cause warping. Laser welding reduces this risk. The materials retain their original shape. This is crucial for delicate or intricate projects.
Stronger Welds
Laser welding results in stronger welds. The concentrated heat source creates deep penetration. This forms a robust bond between the materials. The welds are cleaner. They have fewer impurities and defects. This increases the overall strength. The joints are able to withstand higher stress and pressure. They are more reliable for critical applications.
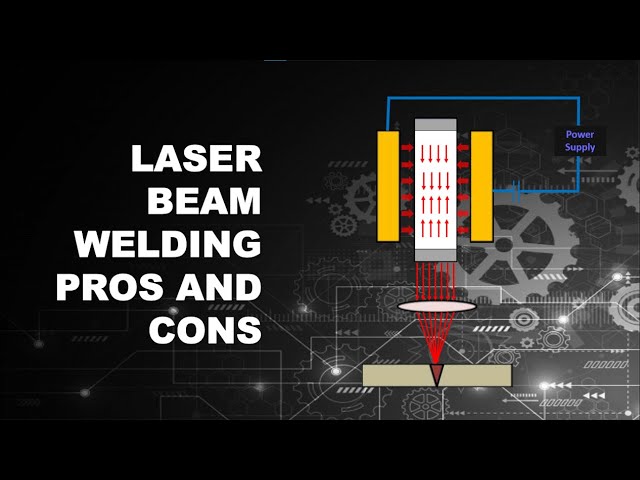
Credit: m.youtube.com
Cost Considerations
Cost considerations play a crucial role in deciding whether to use laser welding. This advanced technique offers many advantages but comes with specific financial aspects. Understanding these can help make an informed decision.
Initial Investment
The initial investment in laser welding equipment is quite high. The machines and necessary components are expensive. This makes laser welding suitable for businesses with a significant budget. Smaller companies might find this cost prohibitive. However, the precision and efficiency of laser welding can justify the investment.
Maintenance Costs
Maintenance costs for laser welding equipment are also notable. Regular servicing and part replacements can add up. Proper maintenance ensures the longevity and optimal performance of the machines. It helps avoid unexpected breakdowns and costly repairs. Businesses must budget for these ongoing expenses. Neglecting maintenance can lead to more significant issues and higher costs in the long run.
Technological Requirements
When it comes to laser welding, understanding the technological requirements is crucial. This high-precision process offers numerous benefits, but it does come with its set of challenges. In this section, we will dive into the necessary equipment and the skills required to master laser welding.
Equipment Needed
Let’s start by discussing the essential equipment for laser welding. The main piece of equipment is, of course, the laser welding machine. This machine uses a concentrated beam of light to fuse materials together. It’s not just any light, though; it’s a laser, which stands for Light Amplification by Stimulated Emission of Radiation. Fancy, right?
You’ll also need a power source to keep your laser running. Most laser welders use a continuous power supply to maintain a steady beam. Additionally, you might need a cooling system to prevent overheating. Trust me, you don’t want your equipment to fry in the middle of a project!
Other handy tools include:
- Protective Gear: Safety first! Always wear goggles and gloves.
- Welding Table: A stable surface to work on.
- Clamps and Fixtures: To hold your materials in place.
Skill And Training
Now, let’s talk about the skill and training needed for laser welding. It’s not as simple as pushing a button and watching the magic happen. Nope, there’s a bit more to it.
Firstly, you need to understand how the laser interacts with different materials. Metals, plastics, and ceramics each have unique properties. Knowing these can help you adjust the laser settings for optimal results. This might sound complicated, but with a bit of practice, it becomes second nature.
Training is also essential. Many vocational schools and technical institutes offer courses in laser welding. These programs usually cover:
- Basic welding principles
- Laser safety protocols
- Hands-on practice with various materials
And let’s not forget the importance of continuous learning. Technology is always evolving, and staying updated with the latest advancements can give you an edge. Plus, it’s fun to learn new tricks, don’t you think?
So, while laser welding does require specific equipment and training, the investment is well worth it. With the right tools and knowledge, you can achieve precise, high-quality welds that are sure to impress.
Limitations And Drawbacks
Laser welding offers numerous advantages. Yet, it is not without its limitations and drawbacks. These aspects must be considered to make an informed decision about its use. Understanding the challenges can help in assessing its suitability for specific applications.
High Initial Costs
The initial investment in laser welding equipment is substantial. This can be a significant barrier for small businesses. The machinery, setup, and maintenance costs are high. It’s an advanced technology that requires specialized training. Skilled operators are essential for optimal performance. Training can add to the overall expense. These factors can deter potential users.
Material Limitations
Not all materials are suitable for laser welding. It works best with specific metals. For example, aluminum and copper can pose challenges. These materials reflect the laser beam, causing inefficiencies. Additionally, the thickness of the material matters. Thick materials can be difficult to weld effectively. This limits the range of applications for laser welding.
Industry Applications
Laser welding offers precision and speed, making it ideal for industries requiring high-quality joints. Drawbacks include high initial costs and sensitivity to material and thickness variations.
Laser welding is a versatile technology. It caters to various industries due to its precision and efficiency. Let’s explore some key industry applications of laser welding.Automotive Industry
Laser welding is prevalent in the automotive industry. It helps in manufacturing car bodies and engines. The technology ensures strong, precise welds. It is ideal for high-volume production. This results in consistent, high-quality automotive parts. Laser welding also reduces material waste.Aerospace Industry
The aerospace industry benefits greatly from laser welding. It provides high-strength, lightweight joints. This is crucial for aircraft and spacecraft components. Laser welding ensures minimal thermal distortion. Precision is critical in aerospace, and laser welding delivers it. The technology is also used for repairing turbine blades.Medical Device Manufacturing
Laser welding plays a key role in medical device manufacturing. It is used for producing surgical instruments and implants. The process ensures high levels of cleanliness and precision. Laser welding is ideal for small, intricate devices. It also minimizes the risk of contamination. This makes it suitable for medical applications. “`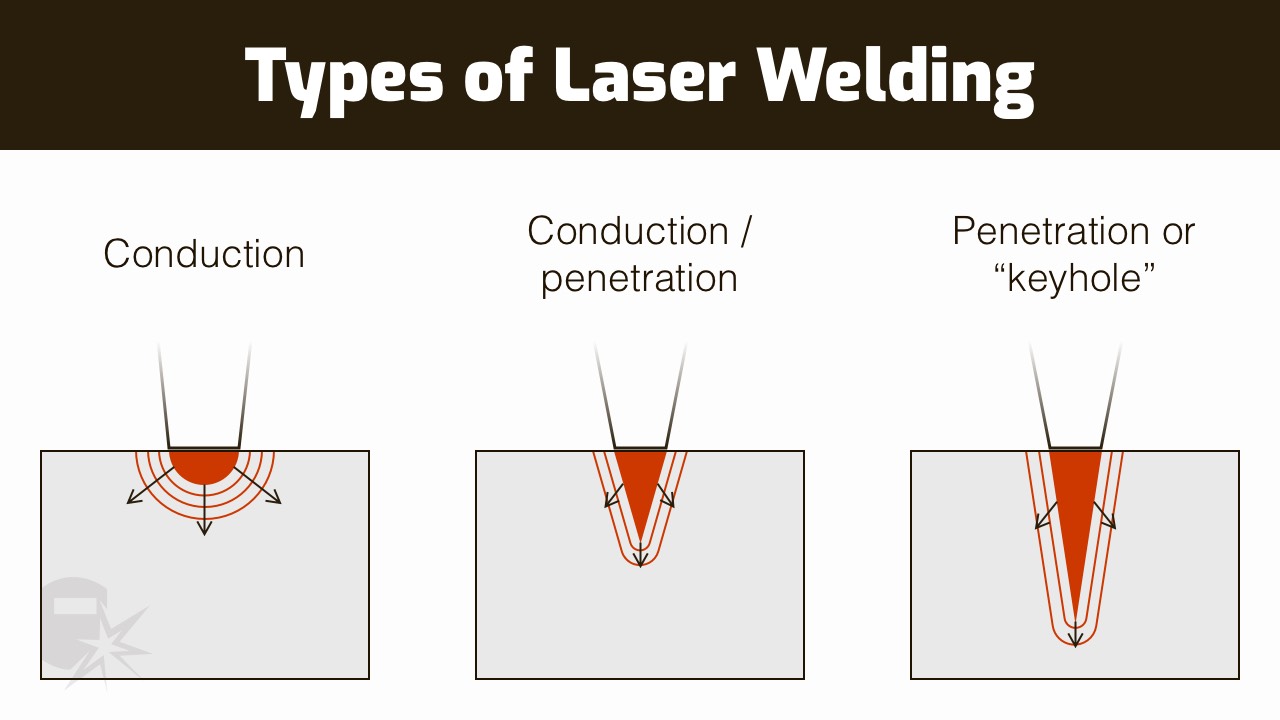
Credit: weldguru.com
Future Of Laser Welding
The future of laser welding is exciting and full of potential. As technology advances, the applications and benefits of laser welding continue to grow. From automobiles to electronics, laser welding is transforming industries worldwide. But what lies ahead? Let’s dive into the upcoming trends and developments in this fascinating field.
Technological Advancements
Laser welding technology is moving forward at a rapid pace. New innovations are making the process more efficient and accessible. Here are a few technological advancements that are shaping the future:
- Fiber Lasers: Fiber lasers are becoming more popular due to their precision and high power. They offer better performance and reliability compared to traditional lasers.
- Automation: Automation in laser welding is making the process faster and more accurate. Robots can perform complex welds with consistent quality, reducing the need for manual labor.
- Real-Time Monitoring: New systems allow for real-time monitoring of the welding process. This means defects can be detected and corrected immediately, ensuring higher quality welds.
With these advancements, the future of laser welding looks bright. We can expect more precise, efficient, and cost-effective welding solutions on the horizon.
Potential Market Growth
The market for laser welding is also expanding. As more industries recognize the benefits, the demand for laser welding technology is increasing. Let’s look at some areas where we can expect significant growth:
- Automotive Industry: The automotive industry is a major player in the laser welding market. With the rise of electric vehicles, the need for precise and strong welds is crucial. Laser welding provides the perfect solution.
- Electronics Manufacturing: As electronics become smaller and more complex, traditional welding methods are often inadequate. Laser welding offers the precision needed for these intricate components.
- Medical Devices: The medical field is also seeing increased use of laser welding. From surgical instruments to implants, the ability to create strong, precise welds is essential.
With these sectors driving demand, the laser welding market is poised for substantial growth. This means more opportunities for innovation and development in the coming years.
In summary, the future of laser welding is full of promise. Technological advancements and market growth are paving the way for new applications and improvements. Whether you’re in the automotive, electronics, or medical industry, laser welding is set to play a crucial role in the future of manufacturing.
Frequently Asked Questions
What Are The Disadvantages Of Laser Welding Machine?
Laser welding machines can be expensive. They require skilled operators. Maintenance costs are high. Not suitable for all materials. Limited joint accessibility.
How Long Do Laser Welders Last?
Laser welders typically last between 10 to 15 years. Proper maintenance can extend their lifespan. Quality and usage frequency also impact longevity.
What Are The Failures Of Laser Welding?
Laser welding failures include cracks, porosity, incomplete fusion, and spatter. Poor joint fit-up and improper parameters can cause defects.
What Is The Greatest Hazard To A Welder While Laser Welding?
The greatest hazard to a welder while laser welding is eye injury from intense laser light exposure. Proper eye protection is essential to prevent damage.
Conclusion
Laser welding has its pros and cons. It offers precision and speed. But, it can be expensive and complex. Ideal for high-tech industries. Not always the best choice for all projects. Consider your needs and budget. Weigh the benefits and drawbacks.
Then, make an informed decision. Laser welding might be perfect for your next project. Or not. Evaluate carefully. Choose wisely.