Underwater welding is a specialized skill in the welding industry. It involves welding at high pressures underwater.
This unique job offers many opportunities but comes with its challenges. Underwater welders repair ships, oil rigs, and underwater structures. The work can be rewarding, both financially and in terms of job satisfaction. But it also requires rigorous training and poses significant risks.
Understanding the pros and cons helps in making an informed decision about this career path. In this blog, we will explore the benefits and drawbacks of underwater welding. This will help you decide if this challenging and exciting career is right for you. Let’s dive into the details and see what underwater welding entails.
Introduction To Underwater Welding
Welcome to the fascinating world of underwater welding! This unique profession combines the skills of welding with the challenges of working underwater. It’s a job that demands courage, expertise, and a love for the ocean. In this post, we will explore the pros and cons of underwater welding. But first, let’s dive into an introduction to what underwater welding is all about.
What Is Underwater Welding?
Underwater welding, also known as hyperbaric welding, is the process of welding at elevated pressures, usually underwater. It is a critical task in the marine industry, especially for repairing ships, oil rigs, and pipelines. Welders use specialized equipment and techniques to perform their duties underwater. Imagine being a welder who not only works with metal but also battles the elements of the deep sea!
There are two main types of underwater welding:
- Wet Welding: This is done directly in the water. The welder uses a waterproof electrode, and the work is performed in a wet environment. It’s like welding while scuba diving!
- Dry Welding: This type is performed in a dry chamber created around the structure to be welded. The chamber is pressurized and free from water, making it similar to welding on land.
History And Evolution
Underwater welding has a rich history that dates back to the early 20th century. The first known instance of underwater welding took place in the 1930s. It was a time when the marine industry was expanding, and the need for underwater repairs was growing.
Let’s take a look at the key milestones in the evolution of underwater welding:
- 1930s: The first underwater welding attempts were made. It was a groundbreaking achievement, albeit with many challenges.
- 1940s: World War II increased the demand for underwater welding as the navy needed to repair ships and submarines quickly.
- 1960s: Technological advancements led to the development of better equipment and techniques, making underwater welding more efficient and safer.
- 1980s: The oil and gas industry boom created a surge in underwater welding for pipeline and rig maintenance.
- Present Day: Continuous improvements in technology and safety measures have made underwater welding a sophisticated and highly skilled profession.
Today, underwater welding is a crucial part of marine construction and repair. It’s an essential skill that keeps our modern world running smoothly.
So, are you ready to explore the pros and cons of this captivating career? Let’s dive deeper in our next sections!

Credit: www.researchgate.net
Types Of Underwater Welding
Underwater welding is a specialized skill with unique challenges. There are two main types: wet welding and dry welding. Each type has its own benefits and drawbacks. Understanding these can help in choosing the right method for a given project.
Wet Welding
Wet welding involves welding directly in the water. The welder uses special electrodes that work underwater. This method is faster and less expensive. There’s no need for a dry environment. Wet welding is often used for quick repairs on ships and offshore structures. It is very practical for shallow water projects. But, it has its cons. The welds can be less durable. Water can cause defects in the welds. Safety is a major concern. The welder is exposed to the water and the risks that come with it.
Dry Welding
Dry welding, also known as hyperbaric welding, occurs in a dry chamber. This chamber is placed around the welding site. It keeps water out and maintains a dry environment. This method produces high-quality welds. The dry environment reduces the risk of weld defects. It is safer for the welder. They are not directly exposed to water. But, dry welding is more expensive. Setting up the chamber takes time and effort. It is typically used for critical structures where weld quality is crucial. This includes pipelines and deep-sea repairs.
Benefits Of Underwater Welding
Underwater welding is a fascinating field, combining the skills of welding and diving. Imagine working beneath the waves, with marine life as your audience. But, it’s not just about the novelty. Underwater welding offers some solid benefits that make it an attractive career choice. Let’s dive into some of these benefits.
High Demand And Job Opportunities
One of the biggest perks of underwater welding is the high demand for skilled professionals. Industries like offshore oil and gas, shipbuilding, and marine construction are always on the lookout for talented welders who can work underwater. This means job security and a steady stream of opportunities.
- Offshore Oil and Gas
- Shipbuilding
- Marine Construction
Plus, with the world’s reliance on maritime industries, the demand is only going up. More jobs mean better choices and, often, higher pay. Who doesn’t want that?
Versatility In Applications
Underwater welding isn’t a one-trick pony. Its applications are vast and varied. Whether it’s repairing a ship’s hull, maintaining underwater pipelines, or building underwater structures, the skills of an underwater welder are invaluable.
- Repairing Ship Hulls
- Maintaining Underwater Pipelines
- Building Underwater Structures
This versatility means you can work on a range of projects, keeping your job interesting. No two days are the same when you’re an underwater welder!
Moreover, this versatility makes you a valuable asset. The more skills you have, the more employable you become. It’s like being a Swiss Army knife in the world of welding.
In conclusion, underwater welding offers numerous benefits, from high demand and job security to the excitement of varied applications. If you love the idea of combining welding with diving and are looking for a career that’s both challenging and rewarding, underwater welding might just be for you!
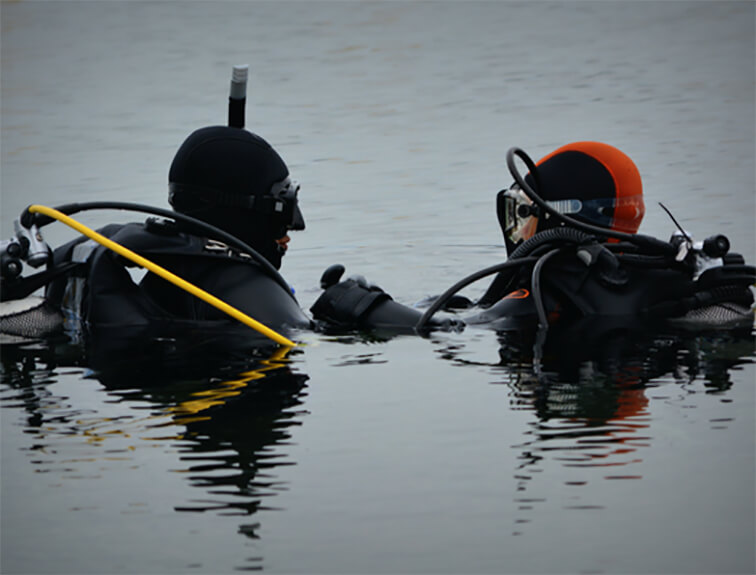
Credit: advanced.edu
Challenges Of Underwater Welding
Underwater welding is a unique and demanding career, often seen as a blend of artistry and engineering. However, while it may seem exciting, it comes with its own set of challenges. In this post, we will dive into some of the most significant hurdles underwater welders face.
Safety Risks
Let’s face it: underwater welding is not for the faint-hearted. Safety risks are a huge concern. Welders work in an environment where one wrong move can mean serious injury or worse. For instance:
- Electric Shock: Water and electricity don’t mix well. Special precautions are necessary to avoid electric shock, which can be deadly.
- Decompression Sickness: Also known as “the bends,” this can occur if a welder ascends too quickly. It’s painful and can be fatal.
- Drowning: Even the best equipment can fail. A sudden loss of air supply can turn a routine job into a race against time.
Welders undergo rigorous training to handle these situations, but the risks are always there, lurking beneath the surface.
Technical Difficulties
Imagine trying to thread a needle while wearing thick gloves. Now, imagine doing it underwater, in murky conditions. That’s what underwater welding can feel like. Here are some technical difficulties welders face:
- Visibility: Often, visibility underwater is poor. Silt, mud, and other particles can make it hard to see what you’re doing.
- Equipment Reliability: The tools used must be highly reliable, but they can still malfunction due to the harsh environment.
- Precision: Welding underwater requires extreme precision. The water pressure can distort the weld, making it difficult to achieve a perfect seal.
These challenges require welders to have not just technical skills, but also incredible patience and a keen problem-solving ability.
In conclusion, while underwater welding is a fascinating field, it’s not without its challenges. From safety risks to technical difficulties, the job demands a unique blend of skill, bravery, and resilience. So, next time you hear about underwater welding, you’ll know it’s not just about the weld—it’s about overcoming the depths.
Safety Measures
Underwater welding is a high-risk profession. Safety measures are critical to protect welders. Proper safety practices can prevent accidents and save lives. This section covers essential safety measures for underwater welders.
Protective Gear
Underwater welders must wear specialized protective gear. The gear includes a dry suit and helmet. The dry suit keeps the welder dry and warm. Helmets provide breathing support and protect the head. Gloves and boots are also essential. They protect hands and feet from electric shocks.
Welders also use harnesses for safety. Harnesses prevent welders from drifting in strong currents. All gear must be checked regularly. Damaged gear can lead to accidents.
Training And Certification
Proper training is vital for underwater welders. Welders need to complete rigorous training programs. These programs cover welding techniques and safety protocols. Training includes both classroom and practical sessions. Real-life scenarios help welders prepare for actual jobs.
Certification is also crucial. Certified welders meet industry standards. Certification ensures welders have the necessary skills and knowledge. Regular recertification keeps welders up-to-date with new techniques. It also ensures they follow the latest safety practices.
Technological Advances
Underwater welding has come a long way since its inception. Thanks to technological advances, the field has seen tremendous growth. In this section, we’ll dive into some of the exciting innovations that have made underwater welding safer and more efficient.
Innovative Tools
Modern underwater welding relies heavily on new tools that have revolutionized the industry. One of the key innovations is the development of waterproof electrodes. These electrodes are specially designed to work underwater, providing better weld quality and durability.
Another breakthrough is the use of remotely operated vehicles (ROVs). These ROVs can handle tasks that are too dangerous or difficult for humans, such as deep-sea welding. They come equipped with cameras, lights, and robotic arms, making them the perfect assistants for underwater welders.
Improved Techniques
Alongside innovative tools, there have been significant improvements in welding techniques. One such technique is dry welding. In dry welding, a special chamber is created around the weld site, keeping the water out. This allows for better visibility and cleaner welds.
Another technique gaining popularity is hyperbaric welding. This method involves welding at high pressures, which helps in achieving stronger and more reliable welds. It’s particularly useful for repairing underwater pipelines and structures.
Tool/Technique | Advantage |
---|---|
Waterproof Electrodes | Better weld quality |
Remotely Operated Vehicles (ROVs) | Enhanced safety, difficult task handling |
Dry Welding | Clearer visibility, cleaner welds |
Hyperbaric Welding | Stronger welds, suitable for high-pressure environments |
These advances are not just about making life easier for underwater welders; they also play a crucial role in ensuring safety and efficiency. After all, when you’re working in such extreme conditions, every little bit helps.
As technology continues to evolve, we can expect even more exciting developments in the world of underwater welding. Who knows? Maybe one day, welding underwater will be as simple as welding on land!
Career Path In Underwater Welding
Have you ever thought about what it would be like to weld metal while surrounded by water? Sounds thrilling, doesn’t it? Underwater welding is a unique and adventurous career path. But like any job, it has its own set of pros and cons. Before diving into this field, let’s explore what it takes to become an underwater welder.
Required Skills
To excel in underwater welding, you need a mix of technical and physical skills. First and foremost, you must be a certified welder. This means you should know how to join metal parts efficiently and safely. But that’s not all. You also need to be a skilled diver.
Here are some essential skills for underwater welding:
- Welding Proficiency: Master different welding techniques.
- Diving Expertise: Be comfortable and skilled in underwater environments.
- Physical Fitness: Maintain good health and stamina.
- Problem-Solving: Quickly address any issues that arise.
- Attention to Detail: Ensure high-quality welding jobs.
Training Programs
You can’t just grab a welding torch and jump into the ocean. Proper training is crucial. Luckily, there are specialized programs that prepare you for this exciting career. These programs usually combine welding and diving training.
Here’s a quick overview of what you might expect in a training program:
- Basic Welding Courses: Learn the fundamentals of welding on dry land.
- Diving Certification: Become a certified diver through a recognized program.
- Underwater Welding Techniques: Specialize in techniques specific to underwater environments.
- Safety Training: Understand the safety protocols to prevent accidents.
Training programs often come with hands-on practice. You get to work in simulated underwater conditions before moving on to real-life scenarios. This ensures that you are well-prepared for the challenges you might face on the job.
So, if you’re looking for a career that combines technical skills with a sense of adventure, underwater welding might just be the perfect fit for you. But remember, it’s not all smooth sailing. The right skills and training are essential to succeed in this field.
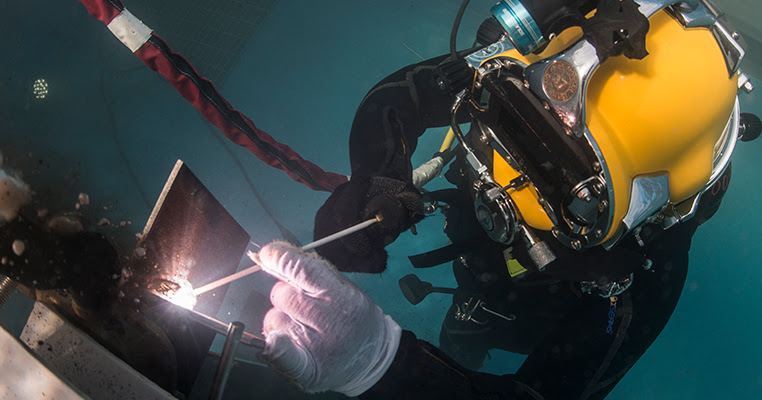
Credit: blog.red-d-arc.com
Future Of Underwater Welding
The future of underwater welding holds promise and challenges. As technology evolves, new trends and sustainability concerns emerge. These factors will shape the underwater welding industry.
Emerging Trends
Technological advancements are driving new trends in underwater welding. Robotics and automation are becoming more common. They increase precision and safety in welding tasks. Divers and welders now use advanced equipment. This equipment helps them work more efficiently and safely underwater.
Virtual reality training is another emerging trend. It helps welders practice in a simulated environment. This reduces the risk of errors and accidents. The use of drones in underwater inspection is also rising. Drones can reach areas that are difficult for humans. They provide detailed visuals of underwater structures.
Sustainability Concerns
Sustainability is a growing concern in underwater welding. The industry needs to address environmental impacts. One concern is the pollution caused by welding materials. These materials can harm marine life. Using eco-friendly materials can help reduce this impact.
Energy consumption is another sustainability issue. Underwater welding requires a lot of energy. Reducing energy use can lower the industry’s carbon footprint. Renewable energy sources, like solar and wind, can be used. This can make underwater welding more sustainable.
Waste management is also important. Proper disposal of waste materials is crucial. This prevents contamination of water bodies. Recycling and reusing materials can further reduce waste. Sustainable practices can ensure the long-term viability of underwater welding.
Frequently Asked Questions
What Are The Pros And Cons Of Underwater Welding?
Underwater welding offers high pay and job demand. It enables repairs in difficult-to-reach underwater locations. Risks include electric shock, decompression sickness, and high-stress environments.
Do Underwater Welders Make 300k?
Underwater welders typically do not make $300k annually. Their average salary ranges from $50k to $100k. High earnings depend on experience and job location.
Do Underwater Welders Live Long?
Underwater welders face higher risks, leading to shorter lifespans. Proper safety measures and training can improve longevity.
What Is The Biggest Risk Of Underwater Welding?
The biggest risk of underwater welding is electric shock. Welders face extreme pressure changes and potential drowning hazards.
Conclusion
Weighing the pros and cons of underwater welding helps make informed decisions. This career offers high pay and adventure. Yet, it also carries risks and challenges. Consider both the benefits and hazards before diving in. Thorough research and training can lead to success.
Underwater welding remains a unique and rewarding field. Make sure it’s the right fit for you.