Replacing a welding liner might seem like a daunting task at first, but trust me, it’s simpler than you think. I remember the first time I had to do it myself; I was nervous about damaging the welder or not getting it right. However, once I understood the process, it became second nature.
I’ll walk you through everything you need to know about welding liner replacement. From understanding why it’s important to step-by-step instructions, this article has you covered. If you’re a beginner or an experienced welder, these tips will help you achieve a smooth replacement and get back to your welding projects in no time.

Image by weldclass
Why Is Welding Liner Replacement Important?
The welding liner is a crucial component in your MIG welding gun. It guides the welding wire from the feeder to the contact tip. Over time, liners can become dirty, kinked, or worn out, leading to wire feed issues, poor weld quality, and frustrating downtime.
Replacing the liner at the right time can save you from these problems and keep your welder performing at its best. It’s all about maintaining a smooth path for the wire, ensuring consistent feed, and achieving clean, strong welds.
Signs That Your Welding Liner Needs Replacement
Knowing when to replace your welding liner is key to avoiding unnecessary disruptions. Here are some common signs to look out for:
Inconsistent Wire Feed
If the wire feed stutters or jams, it could mean the liner is blocked or damaged.
Poor Weld Quality
A worn-out liner can cause irregular wire feeding, leading to spatter, weak welds, or uneven bead formation.
Difficulty Feeding Wire
If the wire feels stiff or hard to push through manually, the liner might be kinked or clogged.
Increased Friction or Resistance
As the liner wears down, it creates more resistance for the wire, affecting feed consistency.
If you notice any of these issues, it’s time to replace your welding liner.
Tools You’ll Need for Welding Liner Replacement
Before starting, gather the tools and materials you’ll need. Here’s what I always have on hand:
- Replacement welding liner (specific to your welder model)
- Wire cutters or pliers
- Adjustable wrench or screwdriver
- Cleaning brush or compressed air
- Protective gloves
Having everything ready will make the process smoother and save you time.
Step-by-Step Instructions for Welding Liner Replacement
Replacing a welding liner is a straightforward process. Follow these steps to ensure success:
Power Down and Disconnect the Welder
Safety first! Always turn off your welder and unplug it from the power source before starting. This eliminates the risk of accidental shocks or damage.
Remove the Welding Gun from the Feeder
Detach the welding gun from the wire feeder. Unscrew or release the gun connection, depending on your welder’s design.
Take Out the Wire Spool
Carefully remove the wire spool to prevent tangles. Cut the wire near the feeder and release any tension from the rollers.
Detach the Contact Tip and Nozzle
Remove the nozzle and contact tip from the gun. This will give you clear access to the liner and make it easier to install the new one.
Remove the Old Liner
Locate the set screw or retaining mechanism holding the liner in place. Loosen it, then pull the liner out from the back of the gun. Go slowly to avoid damaging any internal components.
Clean the Gun Assembly
Before installing the new liner, take the time to clean the gun assembly. Use a brush or compressed air to remove dirt, debris, or buildup inside the tube. This step ensures optimal performance.
Insert the New Liner
Feed the new liner into the gun assembly from the back. Guide it gently until it reaches the contact tip end. Trim any excess length using wire cutters, leaving a small overhang.
Secure the Liner
Reattach the set screw or retaining mechanism to hold the liner in place. Make sure it’s tight enough to keep the liner secure but not overly tight.
Reinstall the Contact Tip and Nozzle
Attach the contact tip and nozzle back onto the welding gun. Ensure they are snug and properly aligned.
Load the Wire Spool and Test
Reload the wire spool and feed the wire through the new liner. Check for smooth and consistent feeding. Adjust the tension if necessary.
Tips for a Successful Welding Liner Replacement
Over the years, I’ve picked up a few tips that can make the process even easier:
Choose the Right Liner Size: Using the correct liner size for your wire diameter is critical for smooth feeding.
Keep Spare Liners Handy: Having an extra liner on hand can save you time if one fails unexpectedly.
Inspect During Replacement: While replacing the liner, check other components like the rollers and contact tip for wear or damage.
Use High-Quality Liners: Investing in quality liners can reduce wear and extend the time between replacements.
Common Mistakes to Avoid
Replacing a welding liner isn’t complicated, but there are a few pitfalls to watch out for:
- Skipping the Cleaning Step: Installing a new liner in a dirty gun can lead to immediate problems.
- Using Excessive Force: Forcing the liner into place can damage the gun or the liner itself.
- Incorrect Trimming: Cutting the liner too short or leaving it too long can disrupt the wire feed.
Taking your time and following the steps carefully will help you avoid these issues.
Maintaining Your Welding Liner for Longevity
Once you’ve replaced your welding liner, proper maintenance can help extend its lifespan. Here’s what I recommend:
- Clean Regularly: After each use, clean the welding gun to remove debris and residue.
- Avoid Sharp Bends: Keep the gun cable straight to prevent kinks in the liner.
- Inspect Before Use: Check the liner and other components for wear or damage before starting a project.
- Store Properly: When not in use, store your welding equipment in a clean, dry place.
Why Proper Liner Replacement Matters
A well-maintained liner isn’t just about convenience; it’s essential for achieving high-quality welds. By replacing your liner as needed, you’ll ensure consistent wire feeding, minimize downtime, and avoid costly repairs.
I’ve found that taking the time to replace a liner properly pays off in smoother welding sessions and better results. It’s a small effort that makes a big difference.
Conclusion
Welding liner replacement might sound intimidating at first, but it’s a simple process once you know what to do. By following the steps in this guide, you’ll be able to replace your liner quickly and effectively, ensuring your welder performs at its best.
Remember, regular maintenance and timely replacements are the keys to avoiding wire feed issues and achieving clean, strong welds. Take care of your welding equipment, and it will take care of you.
If you’re ever in doubt, don’t hesitate to refer back to this guide or consult a professional for help. Happy welding!
FAQs
How often should I replace my welding liner?
It depends on usage, but typically every 6–12 months or when you notice wire feed issues.
Can I clean my welding liner instead of replacing it?
You can clean it to remove minor debris, but a worn or kinked liner should be replaced.
What happens if I use the wrong liner size?
Using the wrong size can cause feeding problems, poor weld quality, and equipment damage.
Do I need special tools to replace a welding liner?
No, basic tools like pliers, a wrench, and a wire cutter are usually sufficient.
Why does my liner wear out so quickly?
Frequent kinks, improper storage, or using low-quality liners can shorten their lifespan.
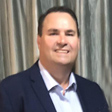
Endow Russel the owner chief editor of giftendow.com . I am a mechanical engineer and assign to an local firm with much experience in welding and industrial equipment.