Working on vehicles equipped with electronic control units (ECUs) requires a delicate balance of expertise, precision, and caution. Welding on such vehicles is a common necessity in automotive repair, restoration, or customization.
It comes with inherent risks to the vehicle’s sensitive electronics and safety systems. As someone who has been hands-on in the automotive and welding industry, I can confidently say that following best practices is crucial to protect both the vehicle and your equipment.
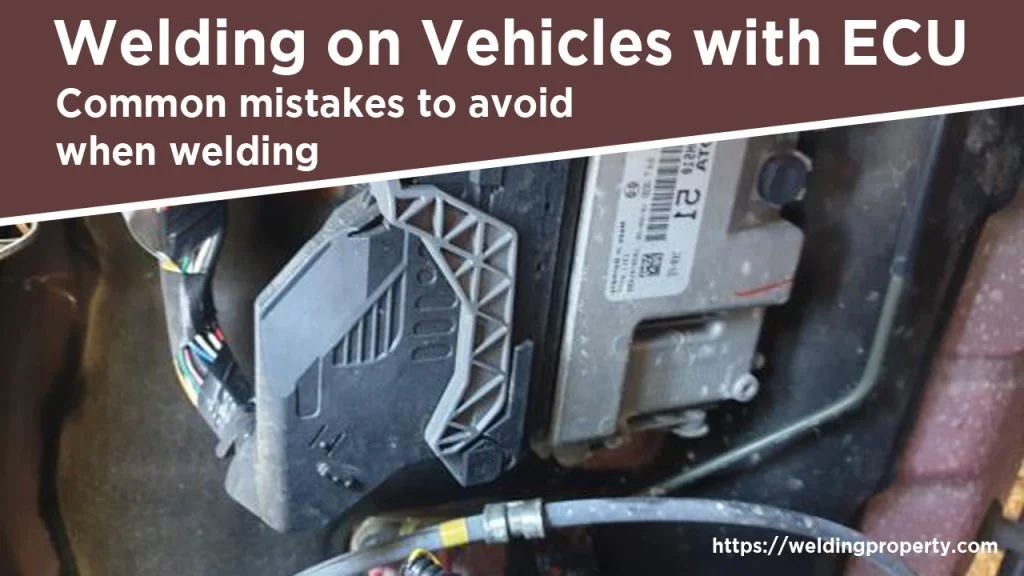
Let’s dive into some practical, tried-and-tested tips and strategies that ensure safe and efficient welding on vehicles with ECUs.
Role of an ECU in Modern Vehicles
An ECU acts like the brain of a modern vehicle. It controls key systems such as engine performance, transmission, airbags, and even advanced features like parking sensors. Damage to the ECU during welding can lead to costly repairs or safety issues.
The first step to safe welding is understanding that these systems are highly sensitive to electrical surges and electromagnetic interference (EMI), both of which are common during welding.
Preparing the Vehicle for Welding
Before starting any welding task, proper preparation is non-negotiable. Preparation minimizes risks and ensures you’re set up for success.
Disconnect the Battery
Always disconnect the vehicle’s battery before welding. This isolates the ECU and reduces the risk of an electrical surge damaging the electronics.
- Start by removing the negative terminal first.
- If possible, disconnect both terminals for added safety.
Remove or Shield the ECU
If feasible, remove the ECU from the vehicle before welding. In cases where removal isn’t practical, use a specialized welding surge protector or shielding device to protect the unit from voltage spikes.
Inspect Wiring and Connections
Check for exposed wires or loose connections near the welding area. Use protective sleeves or heat-resistant tape to shield these components.
Choosing the Right Welding Technique
Not all welding methods are equally suited for work on vehicles with ECUs. Selecting the right technique minimizes the risk of interference and damage.
MIG Welding
MIG welding is a popular choice for automotive work because it offers precision and control. It’s effective for thinner materials like car panels and ensures minimal heat distortion.
TIG Welding
For projects requiring finer detail or involving aluminum and stainless steel, TIG welding is ideal. While it’s slower, the precision it provides is worth the extra time.
Spot Welding
Spot welding is commonly used in body shops for joining sheet metal. It focuses heat on a small area, reducing the chances of damage to nearby components.
Grounding Best Practices
Proper grounding is the cornerstone of safe vehicle welding. A poor ground connection can cause stray currents that harm the ECU or other electronics.
- Attach the ground clamp as close to the welding area as possible.
- Ensure the grounding surface is clean, free of paint, rust, or grease.
- Never ground through sensitive components, such as the ECU or wiring harness.
Using Surge Protection Devices
Surge protectors designed for automotive welding are a worthwhile investment. These devices are installed between the vehicle’s electrical system and welding equipment, acting as a shield against voltage spikes.
Benefits of Surge Protection
- Prevents electrical surges from damaging the ECU.
- Provides peace of mind when welding near sensitive electronics.
Look for products specifically made for welding applications to ensure compatibility and reliability.
Controlling Heat and Spatter
Heat and spatter are inevitable during welding, but they can wreak havoc on a vehicle’s sensitive parts.
Use Heat-Resistant Materials
Cover nearby components, such as wiring, fuel lines, and the ECU, with heat-resistant blankets or shields.
Manage Heat Input
Avoid excessive heat buildup by using short welding cycles and allowing cooling periods between passes. This reduces the risk of warping or damaging nearby parts.
Post-Welding Inspection
Once the welding is complete, inspect the vehicle thoroughly before reconnecting the battery or powering up the ECU.
Check for Damage
Inspect all electronics, wiring, and surrounding components for any signs of damage caused during welding.
Reconnect the Battery Safely
Reconnect the positive terminal first, followed by the negative. Start the vehicle and monitor for error codes or unusual behavior in the electrical systems.
Comparison of Welding Methods for Vehicles with ECUs
Welding Method | Advantages | Precautions |
---|---|---|
MIG Welding | Precision, suitable for thin materials | Avoid excessive heat near sensitive components. |
TIG Welding | Ideal for detailed work | Requires more skill; slower process. |
Spot Welding | Minimal heat distortion | Ensure proper grounding and control spatter. |
Common Mistakes to Avoid
Even with preparation, certain missteps can compromise the safety of the ECU. Here are some mistakes I’ve seen and learned to avoid:
- Skipping the Battery Disconnect: This leaves the ECU vulnerable to voltage spikes.
- Poor Grounding: A weak or distant ground connection can lead to stray currents.
- Rushing the Job: Skipping protective measures to save time can lead to costly damage.
- Neglecting Inspection: Overlooking a post-welding check can result in undetected issues.
Experience with Vehicle Welding
When I first started welding on vehicles, I underestimated the complexity of working around ECUs. I forgot to properly ground the welding machine, which caused a minor surge that tripped several sensors. Fortunately, I caught it during the inspection phase, but it was a wake-up call. That experience taught me the importance of thorough preparation and attention to detail.
Conclusion
Welding on vehicles with ECUs isn’t just about skill with the torch—it’s about understanding the intricacies of modern automotive systems and taking proactive measures to protect them. By following these safety tips and best practices, you can confidently weld on vehicles without compromising their electronics.
Remember, preparation, technique, and post-welding checks are your best friends in this process. It’s not just about doing the job right; it’s about doing it safely and responsibly.
FAQs
Can I weld on a vehicle without disconnecting the battery?
It’s strongly advised to disconnect the battery to avoid voltage surges that can damage the ECU and other electronics.
What happens if I damage the ECU during welding?
ECU damage can lead to malfunctioning systems, costly repairs, or even safety risks. Always take precautions to avoid this.
Is TIG welding safe for vehicles with ECUs?
Yes, TIG welding is safe as long as proper grounding and shielding techniques are used.
Do I need a surge protector for every welding job?
While not mandatory, a surge protector is a smart investment for added safety when working on vehicles with sensitive electronics.
What should I inspect after welding?
Check the ECU, wiring, sensors, and surrounding components for damage or signs of overheating.
Welding on modern vehicles requires more than technical skill—it demands respect for the sensitive systems that make these machines tick. With the right precautions, you can handle any automotive welding task with confidence.
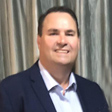
Endow Russel the owner chief editor of giftendow.com . I am a mechanical engineer and assign to an local firm with much experience in welding and industrial equipment.