If you’re diving into the world of welding, you might have come across the term “Flux Cored Arc Welding” or FCAW. It’s one of the most popular welding methods out there, known for its versatility and efficiency. I’ve personally used FCAW in various projects, and I can tell you—it’s a game-changer when it comes to tackling challenging welding tasks.

Image by codinter
But what exactly is flux cored arc welding? How does it work, and where is it most useful? In this guide, I’ll walk you through everything you need to know about FCAW, from its working principles to its benefits and common applications. If you’re a seasoned welder or just starting, this information will help you decide if FCAW is the right technique for your project.
Flux Cored Arc Welding
Flux Cored Arc Welding (FCAW) is a type of welding process that uses a tubular wire filled with flux as the electrode. This wire is fed through a welding gun, where it creates an arc between the electrode and the workpiece. The heat generated by this arc melts the metal and allows for a strong, durable weld.
The flux inside the wire is the secret ingredient—it produces a shielding gas that protects the weld from contaminants like oxygen and nitrogen in the air. This eliminates the need for an external shielding gas in certain conditions, making FCAW a highly flexible welding option.
Types of Flux Cored Arc Welding
There are two main types of FCAW, and each serves a specific purpose depending on the project requirements:
Self-Shielded Flux Cored Arc Welding (FCAW-S)
In this method, the flux within the wire generates its own shielding gas. This eliminates the need for an external gas supply, making it ideal for outdoor or windy environments where shielding gas might be blown away.
Gas-Shielded Flux Cored Arc Welding (FCAW-G)
This method uses an external shielding gas, like carbon dioxide or a CO2-argon mix, in addition to the flux in the wire. It provides cleaner, more precise welds, making it perfect for indoor projects or jobs requiring high-quality welds.
How Does Flux Cored Arc Welding Work?
Flux cored arc welding might sound complex, but the process is pretty straightforward once you break it down:
Set Up Your Equipment
You’ll need a welding machine, a wire feeder, and the appropriate flux-cored wire. For FCAW-G, you’ll also need a tank of shielding gas.
Feed the Wire
The wire is fed continuously through the welding gun, maintaining a consistent arc.
Strike the Arc
When you pull the trigger, the arc ignites between the wire and the workpiece, melting both the wire and the base metal.
Shield the Weld Pool
The flux inside the wire or the external shielding gas protects the weld pool from contamination.
Complete the Weld
As the weld cools, it solidifies into a strong bond. The flux also produces slag, which covers the weld and must be removed afterward.
Advantages of Flux Cored Arc Welding
FCAW has several benefits that make it a go-to option for many welders:
High Productivity
FCAW offers faster welding speeds and higher deposition rates compared to some other methods. This makes it ideal for large-scale projects or industrial applications.
Versatility
Whether you’re working indoors or outdoors, FCAW has you covered. Self-shielded FCAW is perfect for outdoor environments, while gas-shielded FCAW excels indoors.
Strong Penetration
FCAW provides excellent penetration, allowing you to weld thicker materials effectively.
Ease of Use
The continuous wire feed makes FCAW easier to handle, especially for beginners. It’s also forgiving of slightly dirty or rusty surfaces.
Cost-Effectiveness
Since self-shielded FCAW doesn’t require external gas, it can save you money on equipment and gas refills.
Applications of Flux Cored Arc Welding
Flux cored arc welding is widely used across various industries, thanks to its versatility and efficiency. Here are some common applications:
Construction
FCAW is a favorite in construction for tasks like structural welding and repairing heavy equipment. Its strong penetration and ability to handle thick materials make it ideal for these jobs.
Shipbuilding
The maritime industry relies on FCAW for its speed and durability. It’s often used to weld ship hulls, decks, and other large structures.
Automotive Repairs
FCAW is frequently used for car repairs, especially when working with thicker metals like frames or exhaust systems.
Pipeline Welding
FCAW-S is particularly useful in pipeline welding, as it performs well in outdoor and windy conditions.
General Fabrication
From creating metal furniture to crafting custom components, FCAW is a go-to for general fabrication tasks.
Challenges of Flux Cored Arc Welding
While FCAW has many advantages, it’s not without its challenges:
Slag Removal
The flux produces slag that needs to be chipped away after welding, adding an extra step to the process.
Spatter
FCAW can produce more spatter than some other methods, which may require additional cleanup.
Cost of Wire
Flux-cored wire is typically more expensive than solid wire used in MIG welding.
Limited Thin Material Use
FCAW is not the best option for welding very thin materials, as it can lead to burn-through.
Tips for Successful Flux Cored Arc Welding
If you’re planning to use FCAW, here are some tips to ensure success:
Choose the Right Wire: Match the wire type to your project needs (self-shielded or gas-shielded).
Adjust Your Settings: Fine-tune the voltage, wire speed, and travel angle for optimal results.
Prepare the Surface: While FCAW can handle slightly dirty surfaces, cleaning the material will improve weld quality.
Practice Your Technique: Maintaining a steady travel speed and angle will help you create clean, consistent welds.
Use Proper Ventilation: If you’re working indoors, ensure good ventilation to remove fumes produced during welding.
Conclusion
Flux Cored Arc Welding is a versatile and efficient method that’s perfect for a wide range of applications. Whether you’re working on a large construction project or tackling automotive repairs, FCAW offers the flexibility and strength you need.
After using this technique for years, I’ve come to appreciate its ability to perform well in challenging conditions, from outdoor welding in the wind to heavy-duty tasks requiring strong penetration. While it has its challenges, like slag removal and spatter, the benefits far outweigh the drawbacks.
If you’re considering adding FCAW to your skillset, start by practicing on various materials and experimenting with different wire types. With time and practice, you’ll see why so many welders rely on this method for their projects.
FAQs
What is the difference between FCAW-S and FCAW-G?
FCAW-S is self-shielded and doesn’t require external gas, while FCAW-G uses an external shielding gas for cleaner welds.
Is FCAW good for beginners?
Yes, FCAW is beginner-friendly, thanks to its continuous wire feed and forgiving nature.
Can I use FCAW outdoors?
Absolutely! Self-shielded FCAW is perfect for outdoor welding as it doesn’t rely on external shielding gas.
What materials can I weld with FCAW?
FCAW is suitable for a variety of materials, including mild steel, stainless steel, and some alloys.
Does FCAW produce slag?
Yes, FCAW produces slag, which must be removed after welding to ensure a clean finish.
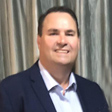
Endow Russel the owner chief editor of giftendow.com . I am a mechanical engineer and assign to an local firm with much experience in welding and industrial equipment.