If you’ve ever seen industrial-grade welds that are smooth, strong, and nearly flawless, chances are they were made using Submerged Arc Welding (SAW). This welding process is widely used in industries that demand high-quality, efficient, and precise welds on thick materials.
When I first explored SAW, I was amazed by its efficiency and the clean, polished results it produces. Unlike some of the more manual welding processes, SAW operates in a way that feels almost automated, yet still offers incredible control.
If you’re curious about how it works, what it’s used for, or it’s the right choice for your project, let’s break it all down.

Image by reddit
About Submerged Arc Welding
Submerged Arc Welding, often abbreviated as SAW, is a welding process that involves creating an arc between a continuously fed electrode and the base material. The “submerged” part refers to the layer of granular flux that completely covers the arc during the process.
This flux layer does two main things:
- It shields the molten weld from contaminants like oxygen and nitrogen in the air.
- It prevents sparks, spatter, and ultraviolet radiation from escaping, making the process safer and cleaner.
The result is a high-quality weld with minimal defects and almost no need for post-weld cleanup.
How Does Submerged Arc Welding Work?
SAW might sound complicated, but its process is surprisingly straightforward once you understand the components. Here’s how it works:
Electrode: A continuously fed consumable electrode is used. It’s typically made of wire and serves as both the heat source and filler material.
Arc Formation: An electric arc forms between the electrode and the base material, generating intense heat.
Flux Layer: Granular flux is poured over the weld zone, fully covering the arc. This flux melts and forms a protective slag layer over the molten weld pool.
Weld Pool: The heat melts the base material and electrode, forming a weld pool that solidifies into a strong joint.
Since the entire welding zone is submerged under flux, there’s no visible arc, sparks, or smoke. This makes SAW incredibly efficient and clean compared to other welding methods.
Advantages of Submerged Arc Welding
One of the reasons SAW is so popular in heavy industries is its range of advantages. Let’s look at some of the key benefits:
High Efficiency
SAW is known for its high deposition rates, meaning it can lay down a large amount of weld metal in a short period. This makes it perfect for industries where speed and productivity are essential.
Clean Welds
The protective flux layer prevents spatter, slag, and impurities from contaminating the weld. As a result, the welds are smooth and require minimal post-weld cleanup.
Deep Penetration
SAW excels at welding thick materials. It provides deep penetration, creating strong, durable welds that are ideal for structural applications.
Automated Capability
SAW is often paired with mechanized or automated systems, allowing for consistent, high-quality welds. This makes it a favorite for repetitive tasks or long weld seams.
Safe and Quiet Operation
Unlike open-arc welding methods, SAW doesn’t produce visible sparks, smoke, or harmful ultraviolet light. This makes it safer and more comfortable for operators.
Disadvantages of Submerged Arc Welding
Like any process, SAW has its limitations. While it excels in many areas, there are a few challenges to keep in mind:
Limited to Flat or Horizontal Positions
SAW is primarily used for flat or horizontal welding. It’s not suitable for vertical or overhead positions, which can be a limitation for certain projects.
Requires Specialized Equipment
SAW equipment is more complex and expensive than simpler welding setups. It’s not the best choice for small-scale operations or hobbyists.
Restricted to Certain Materials
SAW is most effective on thick steel and stainless steel. It’s not ideal for thin materials, non-ferrous metals, or delicate projects.
Flux Handling and Storage
The granular flux used in SAW needs to be stored and handled carefully to avoid contamination or moisture absorption, which can affect weld quality.
Applications of Submerged Arc Welding
SAW is a workhorse in industries that demand heavy-duty, high-quality welds. Here are some of its most common applications:
Shipbuilding
SAW is extensively used in shipbuilding due to its ability to create long, strong welds with deep penetration. It’s perfect for joining large steel plates used in hulls and decks.
Pipe and Pressure Vessel Manufacturing
When it comes to pipelines and pressure vessels, weld integrity is critical. SAW ensures leak-proof, durable welds, making it a trusted choice for these applications.
Structural Welding
SAW is often used in the construction of bridges, buildings, and industrial structures. Its ability to handle thick materials and create strong joints makes it ideal for these heavy-duty tasks.
Automotive and Heavy Equipment
In the automotive and heavy equipment industries, SAW is used for fabricating components like chassis, frames, and axles. Its efficiency and precision make it a valuable tool for large-scale production.
Tank and Storage Construction
Large tanks and storage vessels for chemicals, fuel, or water often rely on SAW for their construction. The process ensures seamless, reliable welds that can withstand pressure and environmental factors.
Submerged Arc Welding vs Other Welding Processes
Wondering how SAW compares to other methods? Here’s a quick comparison:
Process | Best For | Advantages | Limitations |
---|---|---|---|
Submerged Arc Welding | Thick materials, heavy-duty welds | Clean welds, high efficiency | Limited to flat positions |
MIG Welding | Thin to medium materials | Versatility, speed | Requires shielding gas |
TIG Welding | Precision, aesthetics | High-quality welds | Slow and expensive |
Stick Welding | Outdoor and repair work | Portable, affordable | Slower, more cleanup needed |
SAW stands out for its efficiency and ability to handle thick materials, making it ideal for industrial applications. However, it’s not as versatile as MIG or TIG welding when it comes to positions or materials.
Why Choose Submerged Arc Welding?
If you’re working on large-scale industrial projects that require fast, strong, and reliable welds, SAW is an excellent choice. It’s perfect for tasks like joining thick steel plates or creating long, seamless welds.
That said, it’s not the best option for small-scale or delicate work. The equipment cost and setup complexity mean it’s better suited for professional environments rather than DIY projects.
FAQs
Can SAW be used for aluminum?
No, Submerged Arc Welding is not suitable for aluminum. It’s primarily used for steel and stainless steel.
What industries commonly use SAW?
SAW is popular in shipbuilding, pipeline welding, structural construction, and heavy equipment manufacturing.
Is SAW suitable for vertical welding?
No, SAW is primarily used in flat and horizontal positions due to its process requirements.
What is the role of flux in SAW?
The flux shields the weld from contaminants, stabilizes the arc, and forms a protective slag over the weld.
Can SAW be automated?
Yes, SAW is often paired with automated systems for consistent, high-quality results in repetitive tasks.
Conclusion
Submerged Arc Welding (SAW) is a powerhouse in the welding world, offering unparalleled efficiency, strength, and precision. From shipbuilding to structural construction, it’s a reliable choice for industries that demand high-quality welds on thick materials.
In my experience, SAW is one of those processes that feels almost magical in its ability to create smooth, flawless welds with minimal effort. However, it’s essential to weigh its benefits against its limitations to see if it’s the right fit for your project.
If you’re an industry professional or simply curious about advanced welding techniques, SAW is a fascinating process that deserves attention. If your work involves large-scale, heavy-duty tasks, you’ll quickly see why it’s a favorite among welders worldwide.
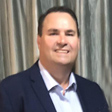
Endow Russel the owner chief editor of giftendow.com . I am a mechanical engineer and assign to an local firm with much experience in welding and industrial equipment.