Welding comes in different forms. The main types are manual, automatic, and semi-automatic.
Understanding these welding processes is crucial for anyone in the industry. Each method has its unique features, benefits, and applications. Manual welding involves a human welder controlling the process. Automatic welding uses machines without human intervention. Semi-automatic welding combines both human and machine efforts.
Choosing the right type can affect your project’s quality and efficiency. In this post, we will explore these welding processes. We will compare their differences to help you make an informed decision. Whether you are a beginner or an expert, this guide will be useful. Dive in to learn more about these welding techniques.
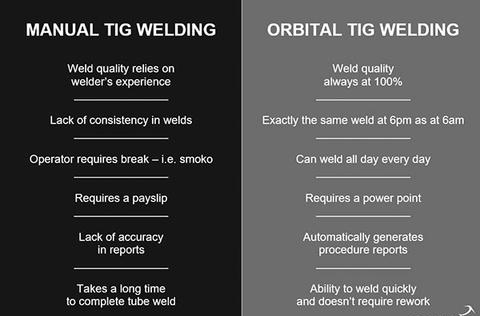
Credit: www.zzkehui.com
Introduction To Welding Processes
Welding is a fundamental process in many industries. It involves joining metals by melting and fusing them. There are various welding processes, each with its own techniques and applications. Understanding these processes is essential for choosing the right method for your project.
Importance Of Welding
Welding is crucial in construction and manufacturing. It ensures the strength and durability of structures. Welded joints are often stronger than the base materials. This reliability makes welding indispensable in many fields. From skyscrapers to ships, welding is everywhere.
Types Of Welding Processes
There are three main types of welding processes: manual, automatic, and semi-automatic. Each process has unique characteristics and benefits. Manual welding requires a skilled welder to control the process. It’s versatile but demands precision and expertise.
Automatic welding uses machines to perform the weld. This method is efficient and produces consistent results. It’s ideal for high-volume production and repetitive tasks. Semi-automatic welding combines manual and automatic techniques. The welder controls some aspects while machines handle others. This balance offers flexibility and efficiency.
Choosing the right welding process depends on your project needs. Consider factors like material type, production volume, and required precision. Each welding process has its own advantages and applications.
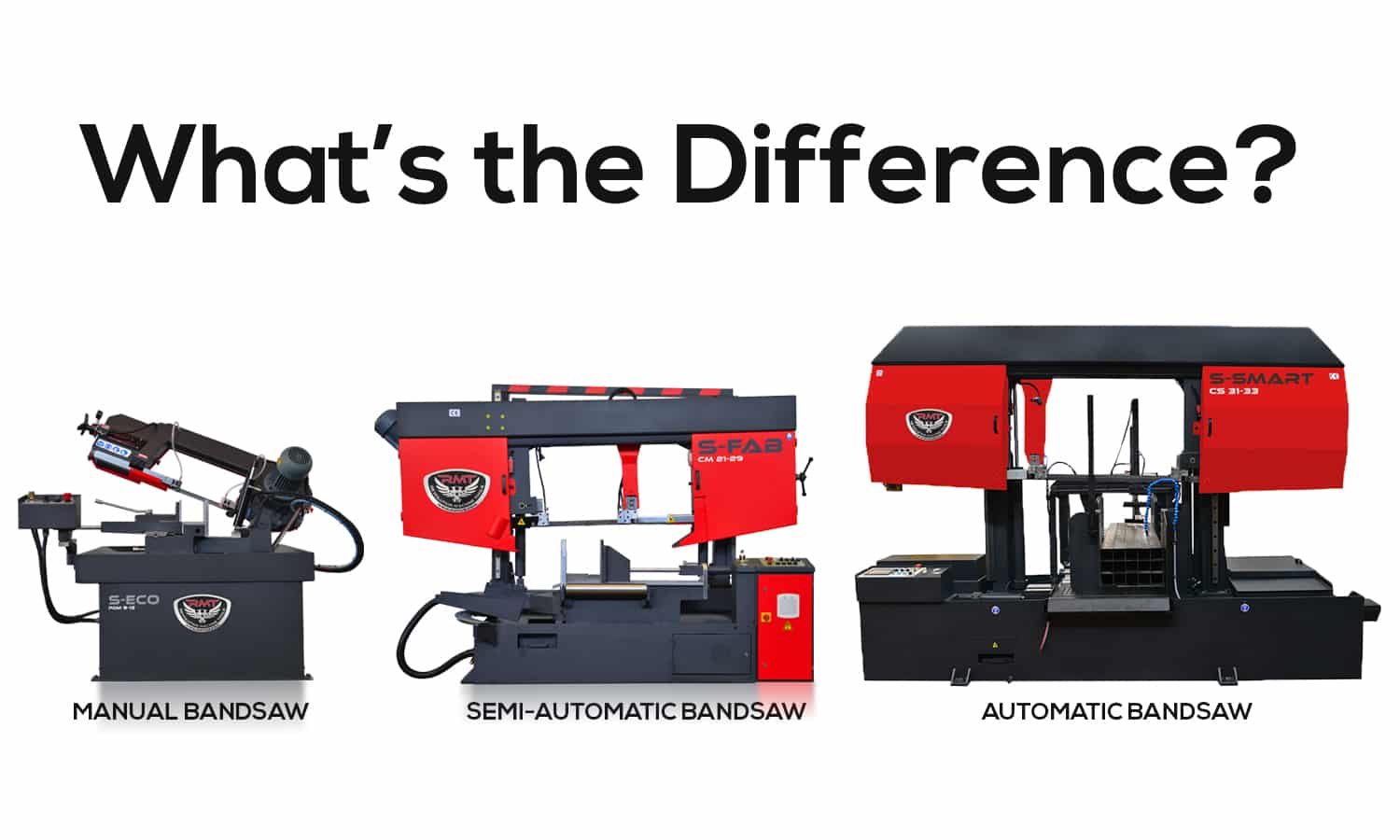
Credit: www.rmtus.com
Manual Welding Process
Welding is an essential skill in many industries. From building skyscrapers to fixing machinery, welding joins metal parts together. One of the oldest methods is the manual welding process. But what makes it unique? Let’s dive in and explore.
Definition
Manual welding, often known as stick welding or SMAW (Shielded Metal Arc Welding), is a process where the welder manually controls the entire welding operation. They hold a welding rod and guide it along the joint, creating a weld by melting the metal at the joint and the rod.
Advantages
- Cost-Effective: Manual welding equipment is generally cheaper and simpler than automatic systems.
- Versatility: Suitable for various positions and environments, including outdoor settings.
- Portability: The equipment is usually portable, making it easy to transport to different job sites.
- Skilled Craftsmanship: A skilled welder can produce high-quality welds with precise control.
Disadvantages
- Labor-Intensive: Requires continuous attention and effort from the welder, which can be physically demanding.
- Speed: Generally slower compared to automatic welding processes, leading to longer project times.
- Skill Dependency: The quality of the weld heavily depends on the welder’s skill, which can vary greatly.
- Safety Risks: Higher risk of injury due to the manual handling of equipment and exposure to intense light and heat.
In conclusion, while manual welding has its challenges, it also offers unique benefits. Its cost-effectiveness and portability make it a valuable method for many welding tasks. However, the need for skilled labor and the slower process are factors to consider. Whether you choose manual welding or another method depends on the specific needs of your project.
Automatic Welding Process
The automatic welding process involves using machines to perform welding tasks. This method requires minimal human intervention. It is ideal for large-scale production and ensures consistent quality. Automatic welding is popular in industries like automotive and aerospace. Let’s explore this process in detail.
Definition
Automatic welding uses programmed machines to join materials. The machine handles the welding task without direct human control. Operators set the parameters and monitor the process. This method ensures precision and consistency.
Advantages
Automatic welding offers several benefits. First, it increases production speed. Machines can work continuously without breaks. Second, it ensures uniform welds. This reduces the chance of errors. Third, it lowers labor costs. Fewer operators are needed to oversee the process. Fourth, it enhances safety. Workers are less exposed to harmful fumes and heat.
Disadvantages
There are some drawbacks to automatic welding. Initial setup costs are high. Buying and installing machines can be expensive. Also, maintenance is required. Machines need regular servicing to function correctly. Another downside is the lack of flexibility. Adjusting the process for different tasks can be challenging. Finally, skilled operators are still needed. They must know how to program and monitor the machines.
Semi-automatic Welding Process
Semi-automatic welding is a versatile welding process. It balances control and efficiency. This method combines manual and automatic features. Here, the welder guides the torch while the machine controls the wire feed. This process is popular in various industries for its flexibility and speed.
Definition
Semi-automatic welding involves a welder operating the welding torch. The machine automatically feeds the filler wire. This process offers a mix of manual control and automation. It is suitable for both small and large-scale projects.
Advantages
Semi-automatic welding has several advantages. It allows for higher productivity. The machine controls the wire feed, reducing manual effort. It provides consistent weld quality. This method is also flexible, adapting to different welding positions. It is suitable for various materials and thicknesses.
Disadvantages
There are some disadvantages to semi-automatic welding. It requires skilled operators. Training is needed to handle the equipment properly. The initial setup cost can be high. Equipment maintenance is also necessary. Additionally, it may be less efficient than fully automatic systems for certain tasks.
Manual Vs Automatic Welding
When it comes to welding, there are different methods to choose from. The most common are manual, automatic, and semi-automatic. Each has its own pros and cons. In this section, we’ll dive into the differences between manual and automatic welding. We’ll look at how they compare in terms of control and precision, as well as labor requirements.
Control And Precision
In manual welding, the welder has full control over the process. This means they can adjust the technique as needed to ensure a high-quality weld. Manual welding is like painting with a brush; you can add fine details and make adjustments on the fly. However, it requires a skilled hand to get it right.
Automatic welding, on the other hand, is controlled by machines. These machines are programmed to perform the welding tasks with high precision. Think of it like a printer; it follows a set pattern to produce the same results every time. While this can lead to very consistent welds, it lacks the flexibility of manual welding.
Labor Requirements
Manual welding is labor-intensive. It requires a trained welder to operate the equipment and manage the entire process. This can be time-consuming and costly, but it also means that adjustments can be made quickly if something goes wrong.
Automatic welding reduces the need for skilled labor. Once the machine is set up and programmed, it can run with minimal supervision. This can save on labor costs, but it also means that any issues with the weld might not be noticed until it’s too late.
So, which is better? It really depends on your needs. If you need flexibility and the ability to make adjustments on the fly, manual welding is the way to go. If you need consistency and can afford to invest in the equipment, automatic welding might be a better choice.
Credit: www.scribd.com
Manual Vs Semi-automatic Welding
Understanding the difference between manual and semi-automatic welding can help you choose the right technique for your projects. Both methods have their own advantages and challenges. Below, we explore two key aspects: flexibility and skill level.
Flexibility
Manual welding offers high flexibility. You control every movement, allowing for intricate welds. This makes it ideal for custom and detailed work. You can adapt to various positions and angles easily.
Semi-automatic welding provides less flexibility. The machine controls some parts of the process. This can limit your ability to adjust on the fly. It is more suited for repetitive tasks and standard welds.
Skill Level
Manual welding requires high skill. You need to master hand-eye coordination and precision. This method demands more training and experience. It is often used by seasoned welders.
Semi-automatic welding is easier to learn. The machine assists in maintaining consistency. This reduces the skill barrier for beginners. It allows for quicker training and smoother operations. New welders can achieve good results with less practice.
Automatic Vs Semi-automatic Welding
Understanding the differences between automatic and semi-automatic welding can help you make better decisions. Both processes have their own unique advantages and disadvantages. Let’s take a closer look at these two welding methods.
Efficiency
Automatic welding offers higher efficiency. Machines handle most of the work. This reduces the need for human intervention. As a result, the welding process becomes faster and more consistent.
Semi-automatic welding, on the other hand, requires some manual input. Operators must guide the welding torch. This can slow down the process. It also introduces variability, as human error can affect the weld quality.
Cost Implications
Automatic welding systems can be expensive to set up. The initial investment includes advanced machinery and software. This can be a significant cost for small businesses.
Semi-automatic welding tends to have lower setup costs. Operators need basic equipment and training. This makes it more accessible for smaller operations. However, labor costs can be higher due to the need for skilled workers.
Choosing The Right Process
Choosing the right welding process can be crucial for your project’s success. Each welding process—manual, automatic, and semi-automatic—has unique benefits. Understanding these can help you make an informed decision. Let’s explore the key factors to consider and where each process is commonly used.
Factors To Consider
There are several factors to consider when selecting a welding process. First, think about the project’s size and scope. Manual welding is ideal for small-scale tasks. It allows for greater control and precision. On the other hand, automatic welding is better for large projects. It offers speed and consistency.
Next, consider the skill level of your workforce. Manual welding requires skilled operators. Training can be time-consuming. Automatic welding reduces the need for high skill levels. Semi-automatic welding strikes a balance. It requires some skill but not as much as manual welding.
Finally, think about cost and efficiency. Manual welding can be cost-effective for small projects. Automatic welding, while more expensive, can save time on large projects. Semi-automatic welding offers a middle ground in terms of cost and efficiency.
Industry Applications
Different industries prefer different welding processes. Manual welding is common in the art and craft industries. It allows for detailed, custom work. Semi-automatic welding is often used in the automotive industry. It offers a mix of precision and speed.
Automatic welding is popular in construction and manufacturing. It ensures fast production with consistent quality. Knowing the industry applications can help you choose the right process.
Future Of Welding Technology
Welding has come a long way from the traditional methods our grandparents used. Today, with advancements in technology, welding processes are more efficient, precise, and versatile. The future of welding technology is brimming with innovations that promise to change the landscape of this industry. Let’s dive into what lies ahead for welding technology and how it can revolutionize the way we join metals.
Innovations
The welding industry is experiencing an exciting wave of innovations. Here are some groundbreaking advancements shaping the future:
- Robotic Welding: Imagine robots taking over the welding process, ensuring accuracy and consistency. Robotic welding systems are already being used in industries like automotive manufacturing, where precision is crucial.
- Laser Welding: This cutting-edge technique uses laser beams to fuse materials. It’s incredibly precise and efficient, making it ideal for delicate and complex tasks.
- Augmented Reality (AR) Welding Helmets: AR technology is making its way into welding helmets. These helmets provide real-time data and visual aids, improving the welder’s accuracy and safety.
Trends
The welding industry is not just about innovations; it’s also about trends that set the direction for future developments. Here are some trends to keep an eye on:
- Green Welding: As sustainability becomes a global priority, green welding practices are gaining traction. These methods reduce energy consumption and minimize environmental impact.
- Portable Welding Equipment: Gone are the days when welding equipment was bulky and immovable. The trend is moving towards portable and lightweight welding machines, making it easier for welders to work in various locations.
- Skill Development: With new technologies emerging, there is a growing emphasis on training and upskilling welders. Online courses and virtual simulations are becoming popular ways to learn and master welding techniques.
As we look to the future, it’s clear that welding technology will continue to evolve, bringing new opportunities and challenges. Whether you’re a seasoned welder or just starting in the industry, staying updated with these innovations and trends is essential. So, keep your eyes peeled and your welding torch ready for the exciting times ahead!
Have any thoughts or experiences with the latest welding technologies? Share them in the comments below!
Frequently Asked Questions
What Is The Difference Between Manual, Automatic, And Semi-automatic Welding Processes?
Manual welding requires a human operator to control the process. Automatic welding uses machines without human intervention. Semi-automatic welding involves both human control and machine assistance.
What Is The Difference Between Manual Welding And Automated Welding?
Manual welding relies on a human welder to operate the equipment. Automated welding uses machines and robots for welding tasks. Manual welding offers flexibility, while automated welding provides consistency and speed.
What Is An Example Of A Semi-automatic Welding Process?
An example of a semi-automatic welding process is Gas Metal Arc Welding (GMAW), also known as MIG welding.
What Is The Process Of Manual Welding?
Manual welding involves using a hand-held welding torch. The welder joins metal pieces by melting them with heat. It requires skill and precision. Personal protective equipment is essential for safety.
Conclusion
Choosing the right welding process depends on your specific needs. Manual welding offers great control but requires skill. Automatic welding provides consistency and speed. Semi-automatic welding balances control and efficiency. Each method has its own benefits and challenges. Understanding these differences helps you make an informed decision.
Always consider the project requirements and resources available. This ensures the best results for your welding tasks.