Welding, brazing, and soldering all join metals. But, they are different processes.
Knowing these differences is vital for choosing the right method for your project. Each technique has its unique applications and benefits. Welding fuses metals using high heat, creating strong bonds. Brazing uses a filler metal with moderate heat, ideal for joining different metals.
Soldering works at lower temperatures with a soft metal filler, perfect for delicate tasks. Understanding these methods will help you decide which one suits your needs. Let’s explore these processes, their advantages, and when to use each one.

Credit: www.differencebetween.net
Introduction To Joining Techniques
Have you ever wondered how metals are joined together? Whether creating a sturdy bridge, a sleek car, or even a simple tool, joining techniques are essential. Welding, brazing, and soldering are three common methods used to join metals. Each technique has its unique process and purpose. Let’s dive into the fascinating world of joining metals!
Purpose Of Joining Metals
The primary goal of joining metals is to create a strong bond between them. This bond ensures that the assembled structure can withstand various forces and stresses. Here’s a quick overview:
- Welding: This technique melts the base metals to form a strong joint. It’s like merging two pieces into one.
- Brazing: Brazing uses a filler metal with a lower melting point than the base metals. The filler metal flows into the joint, bonding the pieces without melting them.
- Soldering: Soldering is similar to brazing but uses even lower temperatures. It’s often used for delicate tasks like electronics.
Each method serves a specific purpose, depending on the strength required and the type of metals being joined. Imagine building a skyscraper with soldering—sounds ridiculous, right? That’s why choosing the right technique is crucial!
Importance In Various Industries
Joining techniques are vital across many industries. Here’s a table highlighting their importance:
Industry | Common Technique | Application |
---|---|---|
Construction | Welding | Bridges, buildings, pipelines |
Automotive | Welding & Brazing | Car frames, exhaust systems |
Electronics | Soldering | PCBs, wiring |
Aerospace | Brazing | Airplane parts, satellites |
These techniques aren’t just for large industries. Even hobbyists and DIY enthusiasts rely on them. Ever repaired a broken gadget? You’ve likely used soldering. Built a sturdy fence? Welding might have been your go-to.
In summary, welding, brazing, and soldering are the unsung heroes in the world of metalwork. They keep structures intact, machines running, and our everyday lives ticking smoothly. So, next time you see a towering skyscraper or a sleek car, you’ll know a bit about the magic behind their creation!
Basics Of Welding
If you’ve ever wondered how metal structures stay together, you’ve probably thought about welding. Welding is essential in construction, manufacturing, and even art. It’s a process that joins metals by melting parts together and then cooling them, creating a strong bond. Let’s dive into the basics, starting with the definition of welding and exploring some common methods.
Definition Of Welding
Welding is the process of joining two or more pieces of metal by applying heat, pressure, or both. The goal is to create a strong joint that can withstand stress and strain. Think of it like glue, but for metal. The difference is, instead of using adhesive, welding melts the metal itself to fuse the pieces together. This ensures a very strong bond that is often as durable as the material itself.
Common Welding Methods
There are several methods to weld metals, each with its unique benefits and applications. Let’s look at some of the most common methods you might encounter:
- MIG Welding (Metal Inert Gas): This is one of the easiest welding methods to learn. It uses a wire feeding gun that feeds wire at an adjustable speed and sprays gas around to protect against contaminants. It’s great for beginners and is often used in automotive repairs and small projects.
- TIG Welding (Tungsten Inert Gas): TIG welding uses a non-consumable tungsten electrode to produce the weld. This method requires more skill and is slower than MIG welding but offers greater control and precision. It’s ideal for thin materials and is often used in aerospace and bicycle manufacturing.
- Stick Welding (Shielded Metal Arc Welding – SMAW): This is one of the oldest and most versatile welding methods. It uses a consumable electrode coated in flux to lay the weld. It’s great for outdoor work and in windy conditions because it doesn’t require an external gas source.
- Flux-Cored Arc Welding (FCAW): Similar to MIG welding, but uses a special tubular wire filled with flux. This method is used in construction projects due to its speed and ability to weld thicker materials.
Each welding method has its pros and cons, and the best choice often depends on the specific needs of the project. Whether it’s the ease of use with MIG, the precision of TIG, the versatility of stick, or the speed of flux-cored welding, understanding these basics can help you choose the right technique for your needs.
Remember, welding is not just about melting metal. It’s about creating something strong and durable. So, next time you see a skyscraper, a bridge, or even a bicycle, you’ll know a bit about the magic that holds it all together.
Basics Of Brazing
When it comes to joining metals, there are various techniques available. One such method is brazing, which is often confused with welding and soldering. However, brazing has its own unique characteristics and applications. Let’s delve into the basics of brazing to understand what sets it apart from other metal joining techniques.
Definition Of Brazing
Brazing is a process used to join two or more metal pieces by melting a filler metal into the joint. The filler metal has a lower melting point than the workpieces, so the workpieces themselves do not melt. This technique creates a strong bond between the metals. It’s like using a glue stick but for metals! The process is typically performed at temperatures above 450°C (840°F), which is much higher than soldering but lower than welding.
Common Brazing Techniques
There are several techniques used in brazing, each with its own unique approach. Here are some of the most common:
- Torch Brazing: This method uses a gas flame to heat the filler metal and the workpieces. It’s great for small jobs and repairs.
- Furnace Brazing: In this technique, the components are heated in a furnace. It’s ideal for large production runs and complex assemblies.
- Induction Brazing: This method uses electromagnetic fields to heat the metals. It’s precise and efficient, making it suitable for high-volume production.
- Dip Brazing: The parts are dipped into a molten bath of filler metal. It’s commonly used for aluminum and other metals with low melting points.
Choosing the right brazing technique depends on the materials involved, the desired strength of the joint, and the specific application. For example, if you’re fixing a bicycle frame, torch brazing might be your go-to. But if you’re manufacturing aerospace components, furnace brazing could be the best choice.
So, next time you encounter a metal joining project, consider brazing. It might just be the perfect fit for your needs!
Basics Of Soldering
Soldering, a process that often slips under the radar, is a fundamental technique in the world of metalworking and electronics. If you’ve ever repaired a broken wire or assembled a circuit board, you’ve likely encountered soldering. But what makes it tick? Let’s dive into the basics of soldering to uncover its secrets.
Definition Of Soldering
Soldering is a method used to join two or more metal components together by melting a filler metal, known as solder, into the joint. The key here is that the base metals are not melted; only the solder is. This makes soldering distinct from welding, where the base metals are melted.
Imagine it like this: think of soldering as using glue to stick two pieces of paper together. The glue (solder) melts and solidifies to create a bond, but the paper (base metals) remains unchanged. Sounds simple, right?
Common Soldering Methods
There are several methods of soldering, each with its own unique applications and benefits. Here are a few of the most common:
- Hand Soldering: This is the most basic method, often used for small electronic components. A soldering iron, which is a handheld tool, heats the solder and directs it to the joint.
- Wave Soldering: Used in mass production, wave soldering involves passing a circuit board over a wave of molten solder. This method is efficient but requires precise control.
- Reflow Soldering: This method is commonly used for surface-mount technology (SMT). Components are placed on a board with solder paste, and then the whole assembly is heated in an oven to melt the solder.
- Resistance Soldering: In this method, an electrical current is passed through the components to generate heat and melt the solder. This is ideal for delicate or precise work.
Each method has its place in the soldering world, from DIY projects to large-scale manufacturing. Choosing the right method depends on the specific needs of your project.
So, whether you’re a hobbyist tinkering with gadgets or a professional assembling complex circuits, mastering the basics of soldering can unlock a world of possibilities. And hey, it’s not rocket science – just a bit of melted metal magic!
Key Differences Between Welding, Brazing, And Soldering
When it comes to joining metals, three popular methods come to mind: welding, brazing, and soldering. While they may seem similar on the surface, each technique has unique characteristics that make it suitable for different applications. Understanding these differences can help you choose the right method for your project. Let’s dive into the key differences between welding, brazing, and soldering.
Temperature Requirements
One of the main distinctions between welding, brazing, and soldering lies in the temperatures required for each process. Here’s a quick comparison:
Process | Temperature Range |
---|---|
Welding | Above 1,500°F (800°C) |
Brazing | Between 840°F (450°C) and 1,500°F (800°C) |
Soldering | Below 840°F (450°C) |
Welding demands high temperatures because it melts the base metals, fusing them together. Brazing, on the other hand, uses a filler metal that melts at a lower temperature than the base metals, which remain solid. Soldering operates at even lower temperatures, utilizing a filler metal to bond the components without melting the base metals.
Material Suitability
Another key factor to consider is the type of materials each method is best suited for. Let’s break it down:
- Welding: Ideal for thick, similar metals, such as steel and aluminum. It provides a strong, permanent bond and is commonly used in construction and automotive industries.
- Brazing: Suitable for joining dissimilar metals and thin-walled components, like copper, brass, and stainless steel. It’s often used in plumbing, HVAC, and electronics.
- Soldering: Perfect for delicate and electrical components, such as circuit boards. It works well with metals like copper, silver, and gold, making it a staple in electronics and jewelry making.
Choosing the right method depends on the materials you’re working with and the strength of the bond required. Welding offers the strongest bond but requires high temperatures and similar metals. Brazing provides a strong bond for different metals and is great for fine work. Soldering is perfect for small, delicate tasks where precision is key.
In conclusion, understanding the key differences between welding, brazing, and soldering can help you make an informed decision for your next project. Whether you’re building a skyscraper, fixing a leaky pipe, or assembling a tiny electronic gadget, there’s a method that’s just right for you.
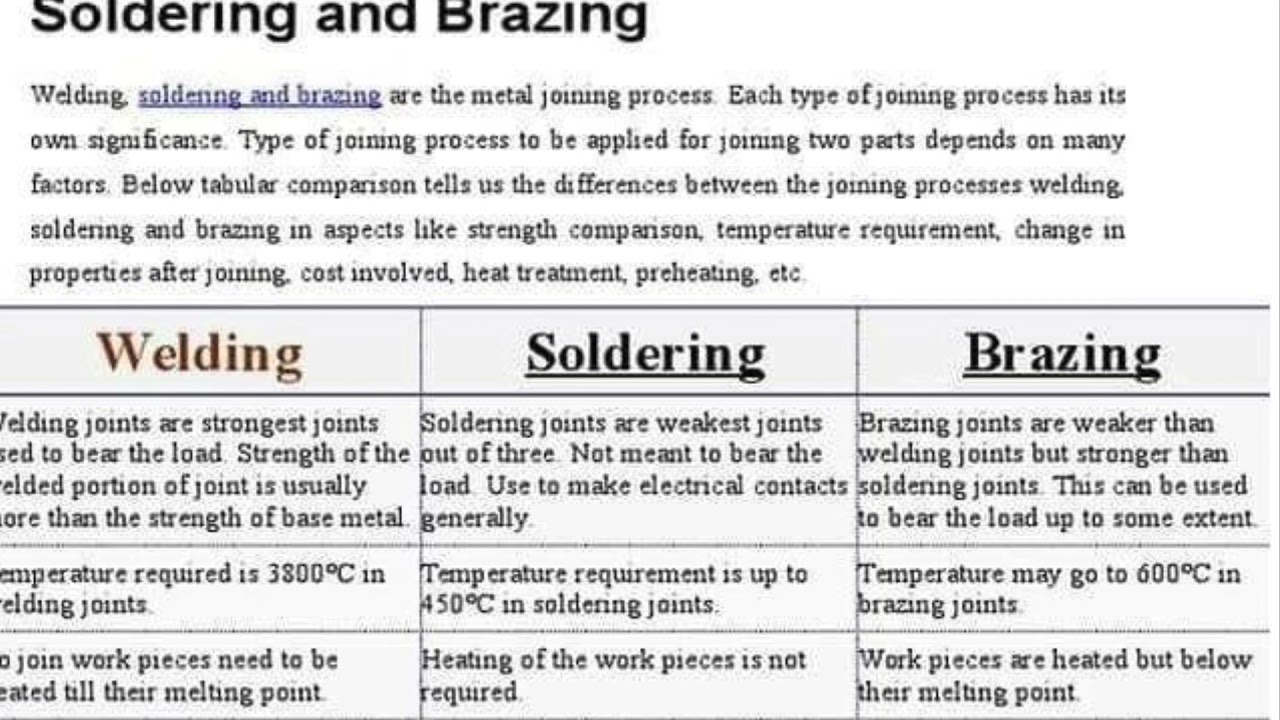
Credit: www.youtube.com
Strength And Durability
When it comes to joining metals, strength and durability are key. Whether you are building a bridge, fixing a pipe, or creating jewelry, understanding how welding, brazing, and soldering differ in strength can help you choose the right method. Let’s dive into the details.
Welding Strength
Welding is like the heavy lifter in the metal-joining world. It creates the strongest bonds by melting the base metals together. When done right, the welded joint can be as strong as the metal itself. This is why welding is used in construction, car manufacturing, and aerospace industries.
- High Strength: Welded joints are typically very strong and can handle heavy loads.
- Durability: These joints are usually durable and can withstand tough conditions.
Brazing Strength
Brazing is the middle child. It doesn’t melt the base metals but uses a filler metal with a lower melting point. The result is a strong bond, though not as strong as welding. Brazing is often used in plumbing, HVAC systems, and bicycle frames.
- Moderate Strength: Brazed joints are strong but not as strong as welded joints.
- Good Durability: These joints can last long, especially in non-extreme conditions.
Soldering Strength
Soldering is the delicate artist. It uses a filler metal with a low melting point to join metals without heating the base metals much. Soldered joints are not very strong but are perfect for electronics and small metal parts.
- Low Strength: Soldered joints are not very strong and are best for light-duty applications.
- Limited Durability: These joints might not last long under stress or heavy loads.
Choosing between welding, brazing, and soldering depends on your project needs. For high strength and durability, welding is the go-to. For moderate strength with good durability, brazing works well. For delicate and small tasks, soldering is perfect. So, what’s your next project? Choose wisely!
Applications In Industries
When it comes to joining metals, the methods of welding, brazing, and soldering are indispensable in various industries. Each technique has its unique applications, advantages, and limitations. But how do you decide which method to use for your specific industrial needs? Let’s dive into the applications of each method to help you understand where and why they are used.
Welding Applications
Welding is a robust and reliable method of joining metals. It is widely used in industries where strength and durability are paramount. Here are some common applications:
- Construction: Welding is essential in constructing buildings, bridges, and other infrastructures. The method ensures strong joints that can withstand heavy loads and harsh conditions.
- Automotive: Car manufacturing heavily relies on welding for assembling car bodies, frames, and other critical components. Ever wonder how your car stays together on those bumpy roads? Welding is the answer!
- Shipbuilding: In the maritime industry, welding is used to build and repair ships, submarines, and offshore platforms. The strong joints are crucial for the vessel’s integrity at sea.
- Aerospace: Welding in aerospace ensures that aircraft structures are strong and lightweight. Precision and strength are key here, given the extreme conditions encountered in flight.
Brazing Applications
Brazing involves joining metals by melting a filler metal at a lower temperature than the base metals. It is perfect for situations where you need to join dissimilar metals or require a smooth finish. Let’s explore where brazing shines:
- HVAC Systems: Brazing is commonly used in heating, ventilation, and air conditioning systems. The joints need to be leak-proof and durable, handling high pressures and temperatures.
- Electrical Components: Electrical industries use brazing to join wires, terminals, and other components. It provides excellent electrical conductivity and mechanical strength.
- Jewelry Making: The fine craftsmanship in jewelry often requires brazing to join precious metals without affecting their appearance. Ever noticed how intricate those designs are?
- Plumbing: Brazing ensures strong, leak-proof joints in plumbing systems. It’s especially useful for joining copper pipes, which are common in many households.
Soldering Applications
Soldering is a method of joining metals by melting a filler metal at a much lower temperature. It is widely used in electronic and electrical applications where precision and minimal heat are critical. Here’s where soldering is commonly applied:
- Electronics: Soldering is crucial in assembling electronic circuits. It joins tiny components on circuit boards, ensuring good electrical connections. Imagine your phone or computer without soldering – not possible, right?
- Printed Circuit Boards (PCBs): PCB manufacturing relies heavily on soldering to attach components. This ensures reliable performance and durability of electronic devices.
- Home Repairs: Soldering is handy for small home repairs, like fixing broken wires or creating custom electronic projects. It’s a go-to for DIY enthusiasts.
- Art and Craft: Soldering is used in creating stained glass art and other crafts. It allows artists to join pieces of metal with precision and ease.
So, the next time you marvel at a skyscraper, drive your car, or use an electronic gadget, remember the silent heroes – welding, brazing, and soldering – working behind the scenes, ensuring everything stays together!
Advantages And Disadvantages
Understanding the differences between welding, brazing, and soldering can be a game-changer, especially when you’re diving into the world of metalwork. Each method has its own set of advantages and disadvantages that can make or break your project. Let’s explore these in detail under the following subheadings: Pros and Cons of Welding, Pros and Cons of Brazing, and Pros and Cons of Soldering.
Pros And Cons Of Welding
Advantages:
- Strong Joints: Welding creates some of the strongest joints, making it ideal for structural applications.
- Permanent Bonds: The bonds are permanent, ensuring durability and longevity.
- Versatility: Suitable for a wide range of metals and alloys.
Disadvantages:
- High Heat Required: Welding demands high temperatures, which can distort or damage thinner materials.
- Safety Hazards: It involves risks like burns, electric shock, and exposure to harmful fumes.
- Cost: The equipment and materials can be expensive, and skilled labor is often needed.
Pros And Cons Of Brazing
Advantages:
- Lower Temperature: Brazing operates at lower temperatures, reducing the risk of metal distortion.
- Join Dissimilar Metals: It allows for joining different types of metals.
- Clean Joints: Produces neat and clean joints, often requiring minimal finishing.
Disadvantages:
- Strength: Joints are generally not as strong as welded joints.
- Flux Residue: Flux can leave residue that needs to be cleaned off, adding an extra step.
- Cost of Filler Metals: The filler metals used can be more expensive than those used in welding.
Pros And Cons Of Soldering
Advantages:
- Low Heat: Soldering requires the least amount of heat, making it ideal for delicate tasks.
- Precision: Excellent for small, precise work such as in electronics.
- Simple Equipment: The equipment needed is usually less costly and easier to handle.
Disadvantages:
- Weak Joints: The joints are weaker compared to welding and brazing, making it unsuitable for heavy-duty applications.
- Limited Metal Types: Not all metals can be soldered easily.
- Corrosion: Soldered joints can be prone to corrosion over time.
So, there you have it! Whether you’re a DIY enthusiast or a professional, understanding these pros and cons can help you choose the right method for your project. And remember, every technique has its place, so use them wisely!
Choosing The Right Technique
Choosing the right technique between welding, brazing, and soldering can be challenging. Each method has its unique benefits and limitations. Understanding these differences helps in making an informed decision.
Factors To Consider
Several factors influence the choice of technique. The materials involved play a significant role. Welding is suitable for similar metals. Brazing and soldering work well with different metals.
Temperature requirements also matter. Welding uses very high temperatures. Brazing uses moderate heat. Soldering requires the least heat.
The strength of the joint is another factor. Welding provides the strongest joints. Brazing gives strong but slightly weaker joints. Soldering produces the weakest joints.
Cost Implications
Cost is a crucial factor. Welding often involves higher costs. The equipment and energy needed are more expensive. Brazing costs less than welding. Soldering is the most cost-effective.
Material costs also vary. Welding rods and electrodes can be pricey. Brazing alloys are moderately priced. Soldering materials are generally cheap.
Labor costs should be considered. Welding requires skilled labor. Brazing needs moderate skill. Soldering can be done by less skilled workers.
Credit: www.scribd.com
Frequently Asked Questions
What Is The Difference Between Welding And Brazing And Soldering?
Welding fuses metals using high heat, forming a strong joint. Brazing joins metals using a filler at lower temperatures. Soldering uses a filler metal with even lower heat, ideal for electrical connections.
At What Temperature Does Brazing Take Place?
Brazing takes place at temperatures above 840°F (450°C). The process usually occurs between 1,100°F and 1,500°F (600°C to 800°C).
Why Would You Braze Instead Of Solder?
Brazing creates stronger joints than soldering. It works well for high-temperature applications and different metals. Brazing also offers better corrosion resistance.
Why Choose Brazing Over Welding?
Brazing creates strong joints with less heat, reducing metal distortion. It joins dissimilar metals and is ideal for complex assemblies.
Conclusion
Understanding welding, brazing, and soldering helps in choosing the right method. Welding creates strong joints by melting metals. Brazing joins metals without melting them, using a filler. Soldering works at lower temperatures, ideal for electronics. Each has unique benefits and applications.
Knowing these differences ensures better project outcomes. Consider your material and temperature needs. Then, pick the best technique. Practice and safety are key. Happy joining!